Integrating Augmented Reality (AR) To Optimize Facilities Management
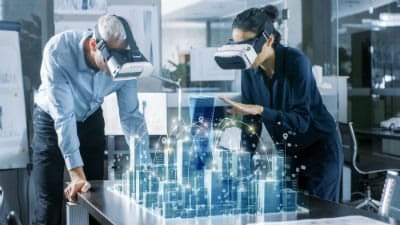
Explore the potential of augmented (AR) and virtual reality (VR) in facilities management. Learn advantages, future trends, and strategies for implementation.
Virtual reality (VR) and augmented reality (AR) are certainly hot topics right now. When most people think of VR and AR, they picture gamers wearing AR headgear. However, VR and AR technologies are more than just for play—they can also be enormously beneficial for work.
Facilities managers are currently integrating virtual and augmented reality technology into maintenance and management processes. This integration is due to their potential to enhance operational efficiency and reduce spending in innovative yet highly effective ways.
Let’s explore using VR and AR for effective facility management.
Understanding Augmented Reality (AR)
Augmented reality (AR) enhances the physical world using sensors, video, audio, graphics, and other technologies. It creates this environment by overlaying digital information onto real images. AR technology actively tracks the user’s movements and adjusts their field of view accordingly. As a result, the user experiences a smooth blend of virtual and real imagery.
AR is particularly useful in facilities management for enhancing maintenance procedures and operational efficiency. For example, you can use AR to train technicians to maintain luxury retail environments.
Simulations allow technicians to practice and develop new skills in a controlled, virtual setting. Then, they can use these practical skills to ensure that high-end retail spaces remain both functional and visually appealing.
Understanding Virtual Reality (VR)
Virtual reality is a computer-generated simulation of 3D environments you can interact with. Typically, users wear headsets equipped with screens and sound systems to immerse themselves in the virtual world. They can move around and interact with objects within the simulation using hand-held controllers or body movements.
Many senior facilities managers use VR to train new employees. VR creates detailed, interactive environments for hands-on training, which is especially useful when on-the-job training is impractical, such as for new security guards.
What’s the Difference Between VR and AR?
The difference between VR and AR is that VR offers an entirely virtual environment, whereas AR combines the digital and physical worlds. In other words, VR creates a fully immersive experience, while AR enhances reality by adding digital elements.
Application of AR in Facilities Management
Utilization for Physical Spaces
Augmented reality technology can create a digital version of a building. Having this virtual twin allows many tasks to be done remotely. For example, a maintenance team could review building conditions without being onsite. This insight can make maintenance processes more efficient.
In some medical facilities, educational facilities, or any other place where it may be important to limit the number of people, AR processes, like the example above, actively reduce the need for close contact and minimize the need to touch shared surfaces.
Maintenance and Operations Management
AR significantly impacts decision-making processes in facility maintenance. It provides real-time information and overlays digital data onto the physical environment. This technology helps maintenance teams quickly pinpoint equipment issues.
Additionally, integrating augmented reality with IoT for maintenance significantly enhances the efficiency of maintenance operations. AR can visually represent the data collected by IoT devices to offer clear instructions and easy-to-understand visual cues for maintenance staff. Having this technology in place can greatly reduce the risk of human error.
Business Continuity
AR’s ability to provide clear, real-time data aids in quick decision-making, which helps reduce business disruptions. It also enables facility managers to instantly collaborate with remote experts to enhance problem-solving efficiency.
Augmented reality can also help managers brainstorm ideas for future business development. By seeing how new technologies could fit into current layouts, they gain a clearer understanding of what must be considered regarding this addition.
For example, a manager could use AR to simulate adding a new piece of machinery to a manufacturing facility. Seeing how it would fit into the existing space would help the manager plan any necessary adjustments or renovations.
Benefits of Augmented Reality in Facilities Management
1. Create Intelligent, 3D Renderings of Facilities with VR
VR makes it possible to create detailed, user-friendly three-dimensional renderings of your facilities. It incorporates building information modeling (BIM) files with VR technology such as Oculus Rift to generate accurate virtual representations.
These 3D renderings allow users to fully immerse themselves in building maps, helping to virtually plan, design, and build facilities or manage equipment and infrastructure. For example, users can utilize VR during construction to map out potential customer flows to ensure buildings are easy to navigate without potential hazards (such as overcrowding).
Additionally, multiple users can view VR facilities maps simultaneously, enabling collaboration and the ability to show rather than tell when presenting FM ideas or real-time reporting.
2. Monitor “Hidden” Equipment and Environments
AR allows people to experience situations without physically being there. This ability can significantly enhance asset monitoring, especially for difficult access, such as pipes and electrical installations buried deep within walls of mechanical and electrical rooms. AR sensors can give you a digitized view of what’s wrong without tearing open walls.
Sensors on or inside assets power AR monitoring capabilities. You gain access to sensor data via technology like QR scanners—some can even provide live audio and video streams—which can then be collected, organized, and analyzed with an FM software platform.
These sensors can also help confirm lifecycle and service information, which can be incredibly useful during maintenance work. By scanning an AR sensor, you can access part numbers and view a digital overlay of how the asset should look and function.
3. Remote Troubleshooting
Similar to AR asset modeling, VR 3D models help visualize equipment systems without physical visual inspections. This capability helps you troubleshoot problems, schedule accurate work orders, and direct contractors remotely, simplifying work and improving safety.
Virtual inspections require significantly fewer resources than physical ones, as you don’t need to knock out drywall or remove ceiling tiles to complete them.
VR makes finding inefficiencies in your systems simple. One quick look gives you a complete picture of the internal structures of your buildings. For instance, if your current setup means HVAC units have to work overtime to regulate the building, VR models make this clear and help you strategize ways to make them more efficient.
With this in-depth visibility into your facilities’ functions, you can also plan preventive maintenance and proactively develop R&M budgets, reducing costs.
4. Efficient Space Planning
Strategic space planning is key to well-organized, customer-friendly facilities. Keep in mind that it is not only important when buildings are first being constructed but also throughout their lives as you replace or add equipment, build new walls, and knock down old ones.
VR models aid in space planning by virtually providing simulations of facility changes before implementation. This gives you unparalleled planning power. You can see what updated facilities will look like, how equipment placement will affect other assets, and if there are better ways to organize your new layout.
5. Track and Manage Assets
Accurate asset management and tracking are vital to reduce downtime in facilities. Downtime lasts much longer if facility managers can’t locate the needed assets to remediate an issue or are unaware of needed repairs. You can use augmented reality to help solve this challenge.
AR can help locate equipment and assess operational efficiencies quickly by enabling staff to scan QR codes or use AR markers to get information about the asset, including its maintenance history or operational status. This way, facility managers can easily keep track of their assets, schedule maintenance tasks, and ensure everything functions correctly.
6. 3D Mapping and Holographic Displays
3D mapping provides a more intuitive way to interact with a facility’s space without any physical processes. For example, 3D mapping can create a digital twin of the facility that allows managers to explore and analyze the space without being physically present. This technology is especially beneficial for planning layout changes and emergency procedure testing.
Holographic displays can create a more engaging way for staff and other stakeholders to visualize data about the facility using virtual demonstrations. This visualization leads to more informed decision-making because it can make complex information easier to understand.
Holographic displays are also becoming an increasingly popular tool in marketing for facilities due to their unique ability to capture audience attention and create memorable experiences.
For instance, incorporating AR-enabled display components in a retail setting can allow customers to see and interact with products in a dynamic and engaging way. This marketing approach strengthens the connection the customer has to the product.
Future AR Trends in Facilities Management
IoT Sensors
IoT devices with cloud computing are frequently used for predictive maintenance. One study even found that IoT-powered predictive maintenance can reduce costs by 20% and extend asset life spans by 30%. Combining IoT with augmented reality takes these advantages further.
AR systems can visualize the data from IoT devices. Then, you can transfer this information to cloud computing platforms. As a result, facility management can access real-time insights from anywhere via the cloud.
Energy Efficiency and Sustainability
AR could transform how energy consumption is monitored and managed. For instance, AR interfaces could pinpoint areas of a building with high energy use or visualize the flow of electric current, heating, cooling, and other systems.
A manager could then use this information to optimize the performance of various assets and make more informed decisions about energy conservation.
Green Buildings
Augmented reality may be instrumental in green building development planning. Developers could virtually ‘see’ into walls to check insulation quality or overlay the building with real-time energy and water usage information. Such insights help ensure the green building meets (or exceeds) sustainability targets.
Smart Cities
AR enhances planning, maintaining, and managing urban environments. AR can provide city planners with a comprehensive view of urban systems, such as utilities and transportation networks.
This transformation could lead to more efficient city management, better resource allocation, and enhanced public services.
Embrace Augmented Reality and Optimize Facilities Management with ServiceChannel
AR adoption in facilities management is one part of the widespread adoption of technology in the industry. Facility managers have been using smart building technology to take tasks off their plates, making work safer, easier, more efficient, and less time-consuming.
AR capabilities in facilities management are still in the early stages. Looking ahead, possible AR applications are limitless. Repair and maintenance work could one day be performed within virtual settings, or entire customer experiences could occur within 3D simulations.
You can learn more about integrating your current facilities management processes with advanced FM technology. Contact ServiceChannel today to request a demo.