Preventive Maintenance Programs: Strategies and Benefits
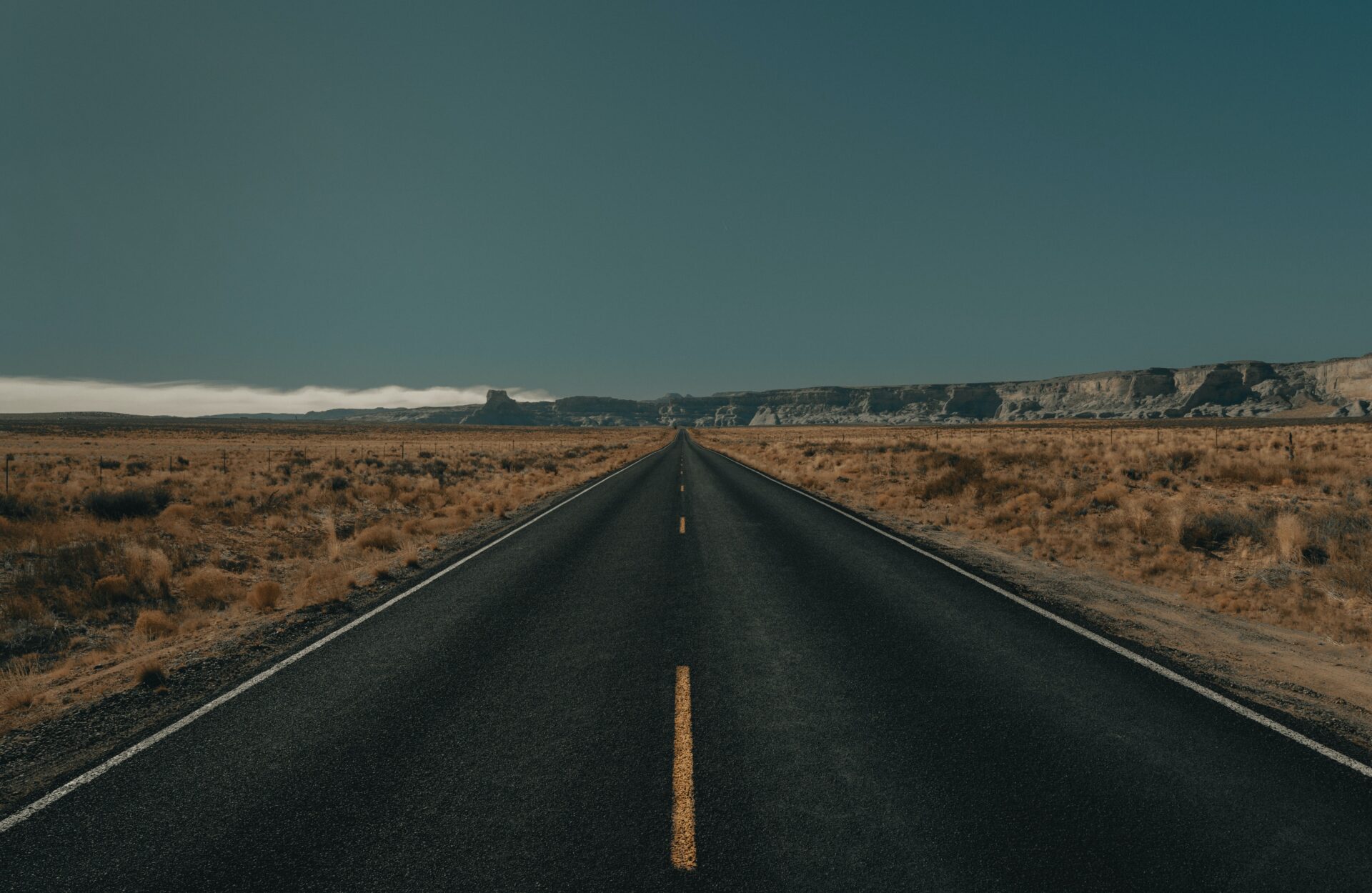
Explore the fundamentals of preventive maintenance (PM) programs, steps to create an effective plan, benefits, and strategies for successful implementation.
Keeping assets in working order can quickly become expensive. As a result, it can be tempting for facilities managers to follow the “If it ain’t broke, don’t fix it” philosophy regarding equipment maintenance. However, waiting until an asset breaks down before investing in repairs can increase your maintenance costs.
Preventive maintenance programs make equipment maintenance less expensive and help business owners get a longer lifespan from asset investments. Therefore, if high maintenance costs are your reason for avoiding proactive maintenance tasks, you may need an effective preventive maintenance program.
What are Preventive Maintenance (PM) Programs?
A preventive maintenance (PM) program establishes a routine for keeping assets in working order by scheduling regular maintenance. Instead of waiting for equipment failures, your maintenance teams check for issues that might cause more significant problems later on a regular schedule.
Examples include:
- Cleaning moving parts
- Checking for any loose bolts or fasteners
- Making sure nothing is trapped within the gears of a machine
Why Build a PM Program?
Equipment breakdowns can lead to costly repairs, the need for new parts, expensive expedited shipping, and the cost of hiring additional technicians.
Additionally, if critical equipment or critical assets fail during busy periods, it can harm your regular operations. Unplanned downtime affects revenue and customer satisfaction. Creating a preventive maintenance schedule can help you avoid unexpected equipment downtime and its potential impact on your operations.
Steps to Create a Preventive Maintenance Program
Facilities managers can struggle to set up preventative maintenance programs. They worry about handling the upfront costs, if they have enough maintenance resources available, and how to decide what assets to cover.
Below are some guidelines for working through these issues as you map out your preventative maintenance program.
1. Establish Goals
Focus your efforts on a select number of assets that incur higher repair costs while offering a significant return on value. To pinpoint which assets these are, start by aligning your plans to implement a preventive maintenance program with your overall business goals. Consider the future direction of your company and identify the most critical assets for achieving these milestones.
You can use this information to create an initial preventive maintenance plan to present to executive leaders who will make the final decisions, demonstrating the clear benefits that will occur when you create a preventive maintenance program. This demonstration will increase the likelihood of decision-makers providing an adequate budget for you to meet your preventive maintenance goals.
2. Take an Inventory of Assets
Review your asset inventory to decide which items to include in your preventative maintenance plan. Capture essential information like:
- How often equipment will need repairing
- The location of all assets
- The condition of each machine
- The cost of performing regular maintenance versus a repair
- What departments are responsible for the upkeep
- Cost of parts that might need repairing
- Maintenance history
Having an asset’s complete history at your fingertips makes it easier to schedule upcoming maintenance tasks.
3. Prioritize Assets Based on Criticality
Perform a criticality analysis of each asset. This process helps you rank the importance of maintaining equipment by assessing the risk associated with failure. Risks include equipment downtime and how that would impact safety, costs, productivity, or potentially a later maintenance operation.
Assets that could have a bigger impact upon failure will be a higher priority for your maintenance technicians, while those deemed non-critical and less expensive are lower on your list.
4. Select a Preventive Maintenance Strategy
It’s important to recognize that there are several different types of preventive maintenance, and not every strategy is suitable for your own preventive maintenance plan. Take the time to compare various strategies to your program’s goals to choose the best one for your preventive maintenance success.
Types of preventive maintenance examples include:
- Time-based preventive maintenance: Involves performing routine maintenance tasks on a regular, predefined preventive maintenance schedule regardless of equipment condition
- Usage-based preventive maintenance: Preventive maintenance tasks are scheduled based on the usage or operational hours of the asset
- Failure-finding maintenance: Maintenance tasks focus on detecting hidden failures or faults in protective devices and backup systems
- Risk-based maintenance: Prioritizes preventive maintenance activities based on the risk assessment of equipment downtime and its impact
- Condition-based maintenance: Maintenance is carried out when equipment condition monitoring indicates a need for preventive maintenance services
- Predictive maintenance: Data analysis tools predict when your team needs to perform preventive maintenance
5. Create Your Preventive Maintenance Checklist
Draw up preventive maintenance checklists that help you track your entire PM lifecycle. Computerized maintenance management system (CMMS) software products make it easier to keep up with workflows within your preventative maintenance program. They help you:
- Draw up the outline of your PM program
- Track all preventive maintenance tasks
- Set notifications and alerts for your maintenance team
- Decide what changes to make based on the analysis of equipment data
- Create a preventive maintenance schedule that fits well with your regular operations
- Receive prompt alerts if reactive maintenance tasks are needed
6. Assign Tasks and Allocate Resources
Review your current pool of available resources for your preventive maintenance program. That makes it easier for managers to assign tasks to each maintenance technician or pinpoint whether they need additional personnel to keep up with your preventive maintenance program goals.
You must also draw up a job plan describing what maintenance teams need to maintain each asset adequately. This plan must include:
- Making pictures, images, maps, and other asset documentation readily available
- Establishing a repair and maintenance history for each piece of machinery or equipment
- Attaching safety instructions for personnel related to all preventive maintenance tasks
- Drawing up instructions on properly inspecting an asset
- Documenting spare parts connected to an asset
Strategies for Implementing a Preventive Maintenance Program
Use Preventive Maintenance Software
Your preventive maintenance needs will change over time. Regularly review your preventive maintenance plan and make any necessary adjustments whenever needed.
Using preventive maintenance software automates the process of updating your preventive maintenance plans. This software identifies when equipment often fails, even with regular maintenance. It then suggests how to change your maintenance schedule to prevent these frequent breakdowns.
Develop Standard Operating Procedures (SOPs)
Create detailed SOPs within your preventive maintenance program for each preventive maintenance task. These procedures should clearly outline the steps, tools, and safety measures required for each task.
SOPs ensure consistency in maintenance activities and help in training new staff. They also serve as a reference point for troubleshooting and improving maintenance procedures.
Train Your Team
Set up formal training that walks your maintenance team through your PM program. Make sure they understand their role in achieving the program’s goals. Training sessions should include reviewing software or other tools that make the program more effective. Have your technicians practice essential maintenance processes to ensure they understand them.
Leverage Historical Data
Analyze past maintenance records to identify trends and patterns in asset failure and repair. This historical data is valuable for refining your preventive maintenance schedule.
Historical records help you predict potential future issues and help you decide the best time for each preventive maintenance task. Use this data to continuously improve your maintenance scheduling strategies in a way that will prevent equipment failures.
Establish Clear KPIs
Set up key performance indicators (KPIs) that reflect the goals of your preventive maintenance program. The metrics help you track your initiative’s effectiveness and let you know if you need to make changes.
Establishing consistency in monitoring the strengths and weaknesses of your preventative maintenance plan builds towards steady progress and increases the chances of a successful preventive maintenance program.
Items you can track through your KPIs include:
- Planned maintenance percentage (PMP): Tracks planned maintenance activities versus overall maintenance tasks
- Preventative maintenance compliance (PMC): Tracks program effectiveness by looking at how many tasks get completed on schedule during a specific period
- Overall equipment effectiveness (OEE): Measures the productivity level of an asset
Benefits of Preventive Maintenance Programs
The benefits of preventive maintenance are magnified when you implement an effective preventive maintenance program. Scheduled maintenance tasks ensure that your preventive maintenance strategy is being put into action by all maintenance personnel.
Longer Asset Reliability and Lifespan
An effective preventive maintenance schedule will help you get more out of each asset. Letting your equipment run to failure causes significant strain on it. Keeping your equipment in good shape by performing proactive maintenance will reduce the amount of wear and tear on each asset, extending its useful life.
Preventive maintenance work will also prevent inconveniences by ensuring all equipment functions at optimal performance levels. For instance, regularly servicing office printers prevents slower-than-expected printing that could cause employees to delay their tasks.
Cost Savings
One of the most common preventive maintenance use cases is using it as part of a cost-savings plan. By scheduling maintenance activities in advance, maintenance professionals can reduce the costs associated with emergency repairs and downtime.
Part of what makes preventive maintenance important is its ability to help maintenance managers allocate budgets and control expenditures effectively.
Lower Risk of Breakdowns
Preventive maintenance involves regular checks on critical equipment, which helps identify potential issues before they escalate into major problems. As a result, preventive maintenance schedules significantly reduce the risk of unplanned downtime.
Furthermore, well-implemented preventive maintenance plans will make corrective maintenance operations run more smoothly when needed. The reason why is that other issues that could compound the problem will likely have already been addressed.
Increased Operational Efficiency
A structured preventive maintenance program helps continuously improve every maintenance task. Maintenance professionals can improve their overall efficiency by regularly assessing and optimizing the preventive maintenance process.
This type of continuous improvement leads to faster, more reliable operations, ensuring that all critical assets consistently perform at their best.
Decreased Unplanned Downtime
One of the key preventive maintenance benefits is the significant decrease in unexpected downtime. When facility managers schedule maintenance effectively, they can plan for downtimes in a way that minimizes disruption to the organization.
Enhanced Safety and Compliance
A preventive maintenance program plays a crucial role in ensuring safety and compliance. Planned maintenance checks help identify and rectify any safety hazards, thereby protecting employees and customers.
Keeping equipment up to code with regulatory standards is also easier with a structured preventive maintenance plan.
Get Your Preventive Maintenance Program Started With ServiceChannel
The key to a successful preventive maintenance program is the right partner. ServiceChannel can provide both preventive and predictive maintenance solutions for your company. We can also help you decide which tools and services best suit your needs so you can further reduce maintenance costs by optimizing your spending.
Learn more about the ServiceChannel platform and how we can help you get ahead and stay ahead with a proactive maintenance strategy. Request a demo today.