7 Benefits of Preventive Maintenance for Facilities
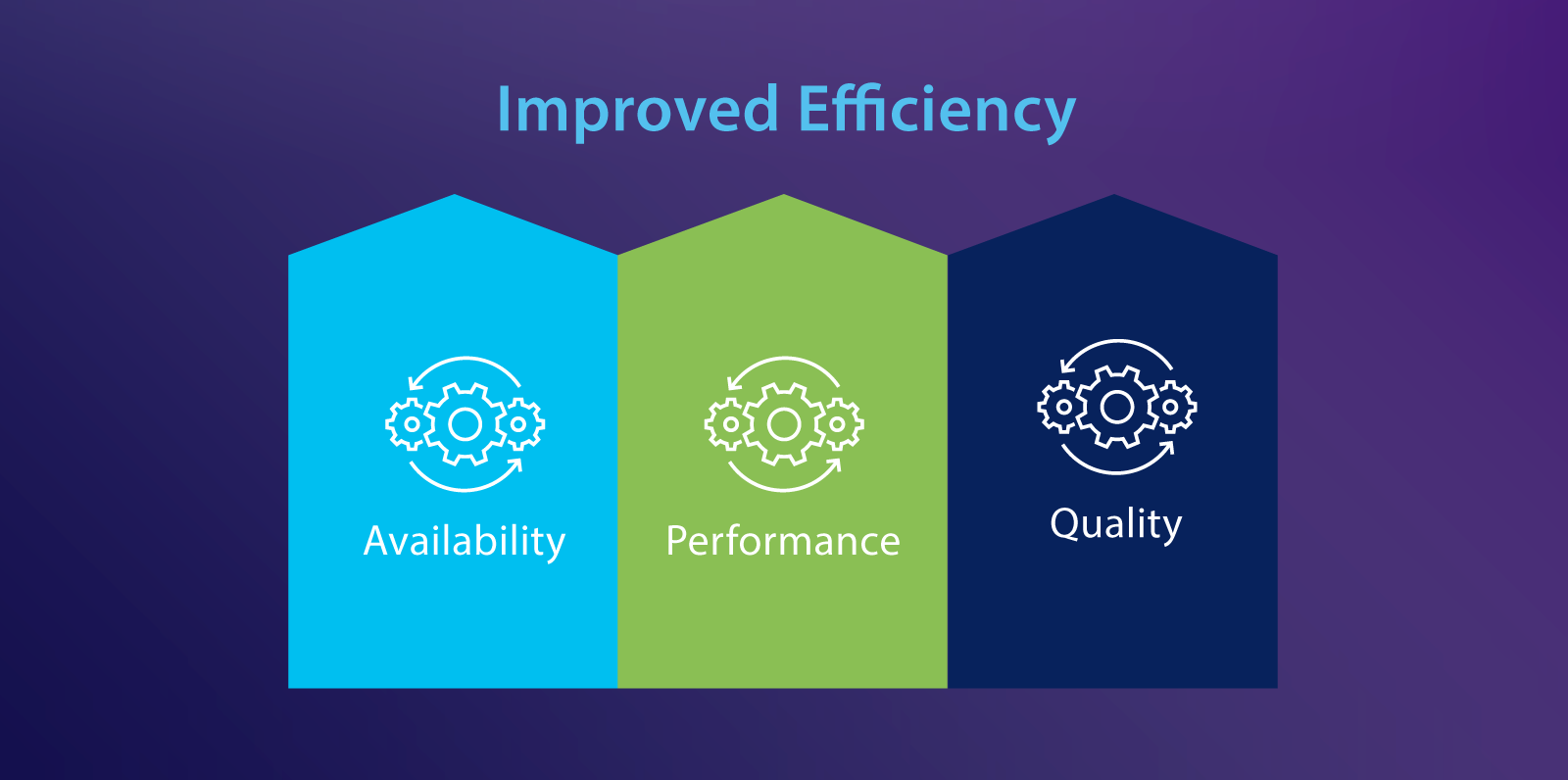
When you only perform reactive maintenance, you set your facility up for downtime and shorten the life of your equipment. Every maintenance task takes time, no matter how minor, which can significantly disrupt operations performed on critical assets.
Proper preventive maintenance management can greatly reduce downtime, maintenance costs, and the time technicians spend on repairs. Those are only a few of the benefits of preventive maintenance. Keep reading to discover more and how you can get started.
What is Preventive Maintenance?
Preventive maintenance is regularly scheduled maintenance or upkeep that extends an asset’s longevity. This is often done through regular inspections and simple repair tasks to enhance an asset’s performance. Part of the point of preventative maintenance tasks is to prevent unplanned downtime from emergency repairs.
Preventive maintenance also includes maintaining accurate records of prior inspections and service reports. The information gives technicians crucial information that helps them determine when they might need to change parts or perform additional maintenance tasks.
Types of Preventive Maintenance
Preventive maintenance is essential to extending equipment life and reducing repair costs. However, there are several types of tasks that each follow a different preventive maintenance schedule.
Time-based
Time-based maintenance (TPM) is planned upkeep that relies on a schedule outlining when to perform maintenance on a piece of equipment. Typically, this schedule is based on metrics that predict how long it will take before the asset has critical maintenance requirements. The idea is to help maintenance workers stay ahead of breakdowns to prevent unscheduled downtime.
Metrics may be internally determined or based on best practices. For example, an HVAC system should undergo routine maintenance at least once a year. This isn’t based on any specific internal data—it is a general best practice. Manufacturer recommendations may also determine the schedule.
Usage-based
Usage-based maintenance (UBM) focuses on how often equipment gets used. UBM planning accounts for average daily use, asset health, and environmental conditions. That information gets pulled together to forecast when a company should plan to inspect or perform maintenance on an asset.
Unlike the time-based model, this schedule is based on the asset’s condition. For instance, critical equipment will need more frequently scheduled maintenance due to its higher usage. This is usually a more cost-effective preventive maintenance plan because it keeps maintenance technicians from performing unnecessary inspections on lesser-used equipment.
Condition-based
Condition-based maintenance (CBM) suggests that preventive maintenance activities should only be performed when the asset indicates tangible signs of deterioration. This doesn’t mean waiting for it to need major repairs—it means taking action only when there are signs of decreased asset performance.
There are pros and cons to this approach. On one hand, you save money on labor costs while maintaining optimal working conditions. On the other hand, unexpected failures can happen even if an asset seems to be in decent condition.
Predictive Maintenance
Predictive maintenance is when machine learning (ML) algorithms and artificial intelligence (AI) predict when equipment will need regular maintenance. Typically, this works by collecting data from IoT (Internet-of-Things) sensors attached to the asset. The data is then sent to a cloud and analyzed to tell your system when to schedule maintenance tasks.
Depending on your needs, you may use predictive maintenance to help you implement TBM, UBM, or CBM.
- If you want to follow TBM: the algorithms would asses data on how long it took before previous equipment breakdowns occurred to predict future needs.
- If you want to follow UBM: the algorithms use data analytics to predict future needs based on how frequently an asset was used until it last needed a repair.
- If you want to follow CBM: the sensor would record data about the asset’s condition, such as vibrations, temperature, and performance.
Planned Maintenance
Planned maintenance refers to a strategy for implementing proactive maintenance tasks that stop unexpected equipment outages before they occur. Preventive maintenance is often part of a company’s planned maintenance strategy, but it is only one part of the whole.
Other aspects of a planned maintenance strategy include your plan of action for emergency repairs, maintenance personnel scheduling, and pinpointing the most efficient, safe, and cost-effective ways to maintain equipment.
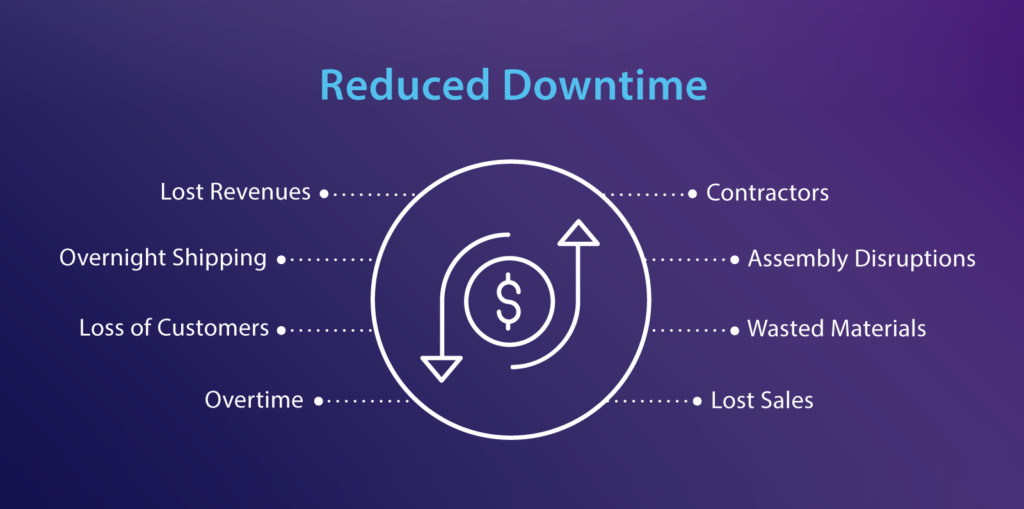
Benefits of Preventive Maintenance
No matter how you perform it, many important benefits of preventive maintenance will surely enhance both working conditions and asset life. Here are 7 of the several benefits of preventive maintenance.
1. Reduced Downtime
Production loss means money lost, and equipment outages or unplanned maintenance are too frequently the cause. You’re trapped in reactive maintenance mode if you can’t predict when an asset might fail. Unplanned downtime can result in missed deadlines and unhappy customers. Preventive maintenance minimizes these issues by giving you a proactive maintenance approach.
2. Lower Costs
One of the most popular benefits of preventive maintenance is that it saves money. When equipment breaks down, you have to repair it as quickly as possible, which means you’ll usually pay more for parts and supplies. You’ll also have to pay more to ship the parts overnight.
Generally speaking, preventative maintenance requires roughly one-third of the resources of reactive maintenance. A carefully scheduled preventive maintenance program can significantly reduce your spend.
3. Increased Equipment Lifespan
Replacing parts, refilling fluids, and performing regular inspections helps ensure equipment works as needed. Preventive maintenance anticipates equipment’s everyday wear and tear, helping you keep assets in optimal working condition for longer. This also helps you save on replacement costs because longer-lived assets are less frequently replaced.
4. Improved Energy Efficiency
Preventive maintenance allows the equipment to run efficiently, which reduces waste. Regular maintenance improves two key metrics:
- Total Effective Equipment Performance (TEEP): which considers equipment performance quality and availability.
- Overall Equipment Effectiveness (OEE): which considers each asset’s overall level of productivity.
These metrics matter to energy efficiency because when equipment works efficiently and without problems, it uses energy in the best possible way. That means all your energy goes towards the production process instead of being wasted.
5. Safer Working Conditions
Workplace safety is a top concern for most businesses. Regular preventive maintenance for equipment can result in a safer working environment for everyone. Routine checks can uncover potential hazards before they cause harm, leading to fewer work-related injuries.
6. Higher Compliance
Preventive maintenance can also help companies manage compliance issues more effectively. Preventive maintenance software often stores compliance requirements in its database and automatically issues work orders when necessary. This can help you avoid fines for violations and save you the worry of manually maintaining compliance.
7. Easier Scheduling and Implementation
When equipment breaks down, maintenance employees must abandon their regularly assigned tasks to fix it quickly. Back office staff also may have to respond to procure parts and issue purchase orders. One breakdown can wreak havoc on your work schedule.
With a predictable preventive maintenance schedule, you can easily avoid that havoc. It reduces downtime, and maintenance teams will know exactly when they need to work on each asset. That will improve efficiency in the workplace for everyone.
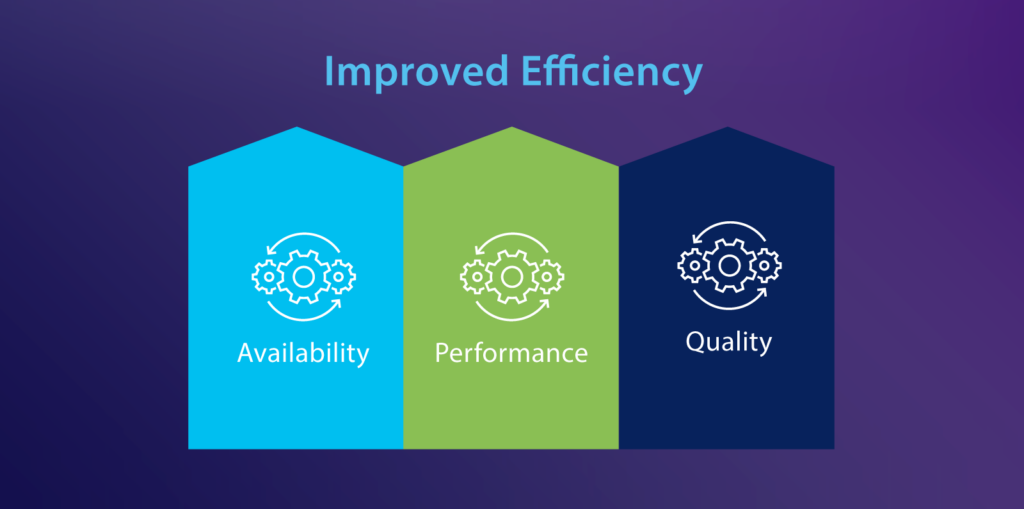
Preventive Maintenance Software for Every Industry
The benefits of preventive maintenance are felt across every industry. No matter where you work, anyone who uses equipment can use preventive maintenance. Still, you need more than just a list of tasks to streamline your preventive maintenance program.
You can make that happen with Service Channel. Our CMMS makes maintenance management a breeze, while our preventive maintenance software tool helps you stay ahead of breakdowns and source service from the best technicians.
Contact us today to book your demo and regain control over your maintenance costs.
Benefits of Preventive Maintenance FAQs
What is the primary goal of preventive maintenance?
The primary goal of preventive maintenance is to prevent equipment downtime before it occurs. This goal has many positive side effects, like cost savings, increased asset lifespans, and easier maintenance management.
Why should you develop a preventive maintenance plan?
Make a regular plan for your preventative maintenance, primarily for your maintenance teams. Preventive maintenance is best done on a regular schedule. Although UBM and CBM aren’t focused on time, you should at least approximately schedule maintenance tasks based on time. It’s much easier for your maintenance teams to work a time-based task into their daily workflows.
What is the main advantage of preventive maintenance?
The main advantage of preventive maintenance tasks is that you can avoid downtime. However, your preventive maintenance program should also focus on continuous improvement. For instance, if you notice that a certain asset is more prone to breakdowns if it overheats, you’ll know to keep it in a cooler area moving forward.
What are the benefits of predictive maintenance?
Predictive maintenance helps you enhance your preventive maintenance plan. That’s because it gathers data-driven insights about your equipment that you can use to inform your preventive maintenance checklist. For example, data from your predictive maintenance software could show that you need to schedule maintenance tasks more frequently than you do currently.
Will preventive maintenance eliminate all breakdowns?
Preventive maintenance can’t stop companies from experiencing equipment failures. However, they can avoid many potential catastrophes through regularly scheduled checks of valuable assets, allowing them to fix minor issues before they balloon into major problems.
What is the difference between preventive and reactive maintenance?
Preventive maintenance focuses on scheduling repairs and servicing assets on a schedule, regardless of if they exhibit problems. Predictive maintenance focuses on checking equipment most likely to end up having issues that affect the company.