How to Create a Predictive Maintenance Strategy for Your Assets
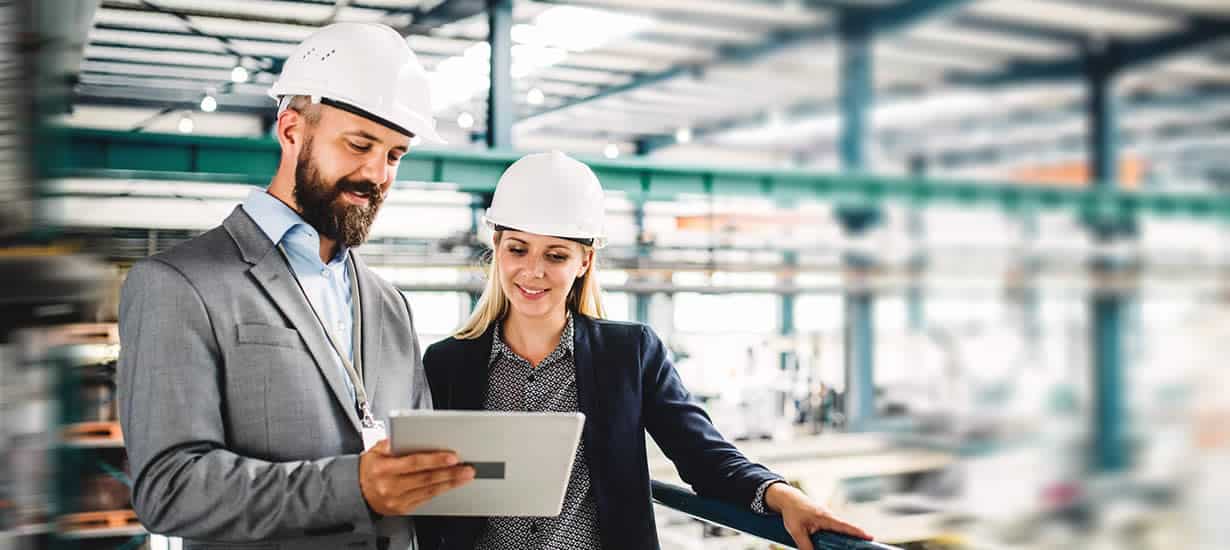
Maintaining your assets is essential to any facilities management strategy, whether you are managing network servers, thermostats, or numerous machines. Without proper maintenance, accidents, unplanned downtime, and broken machinery can result in millions of dollars in losses.
Creating a predictive maintenance strategy with the use of loT, Big Data, and analytics can help prevent major potential financial and litigation disasters while simultaneously improving efficiency, safety, and productivity throughout your facility.
What is Predictive Maintenance ?
Predictive maintenance is the process of utilizing collected analytics generated by Artificial Intelligence (Al) and data science to indicate potential issues or equipment failures that require maintenance and/or immediate attention.
These strategies are useful for monitoring, assessing, and determining viable courses of action for facility equipment, computers, and machinery.
Integrated systems, Al, the cloud, and the Internet of Things (IoT) are all fundamental elements of predictive maintenance, as these each work together in tandem as a seamlessly operated data-collecting machine.
The use of predictive maintenance provides numerous benefits, from saving on labor costs to reducing risk and wear and tear on machinery over time. The advantages of a suitable predictive maintenance solution will vary based on facility needs, capacity, and current equipment and machinery.
Creating a Predictive Maintenance Program
When creating a predictive maintenance program for your facility, you should consider the following steps to ensure a successful and accurate program.
Identify Critical Assets
Implementing a predictive strategy for maintenance first requires facility managers to identify critical assets. Within a facility, critical assets will often include traditional machinery and equipment utilized in day-to-day operations that typically have higher value as well as higher repair or replacement costs. This may include entire ensembles, complete pieces of equipment, and entire floors of working machines.
Comprehensive Asset Database
Once you understand your assets and have identified your critical assets, you need to create a comprehensive asset database that includes your identified assets. Establishing a database allows you to manage and track assets, inventory, as well as specific equipment and/or spare parts necessary for individual facility locations. You can also keep track of both new and outdated equipment, as well as machinery that is accessed on a daily basis.
Ensuring a database is successfully established helps to provide historical data in the event of machine failure or trouble. Collect historical data from hard copies of data, charts, records, and even CMMS.
Establish Fail Models
Creating and establishing fail models is an integral part of any predictive and proactive maintenance strategy. Without a failure model, it can be difficult to detect potential issues or problems that are obvious with machinery or equipment.
You can create failure models by performing FEMA analysis on critical assets that have been established and previously identified in the facility asset database. By analyzing failure modes you will be able to flag any potential errors and troubleshoot matters that will require maintenance. Failure modes also help with creating a more accurate and streamlined predictive algorithm for specific machinery, equipment, or entire facilities.
Establishing and analyzing failure models also provides flags for potential problem areas of specific equipment or models to help facilities managers immediately address and remedy them.
Implement Measurement Tools
If you can measure it, you can manage it. Implementing measurement tools, such as condition-based maintenance (CBM) technology or IOT sensors, ensures that you can manage and identify asset failures and collect data. When you implement the use of sensors and data-tracking solutions, your facilities will be monitored and maintained at all times.
Condition monitoring equipment and sensors provide ongoing streamlined information regarding the overall operations of machinery in any area of a facility and are highly customizable so they can be integrated with various facilities management solutions.
It is important to note that retrofitting older and outdated machinery with updated sensors and condition monitoring equipment is not always easy or straightforward. It is essential to verify that sensors installed on facility machinery or equipment are appropriate, updated, and suitable for the facility itself.
Apply to Pilot Asset
Work together with data scientists to generate and develop new and more precise predictive algorithms that suit your facility’s equipment, machinery, and needs.
Use collected data and information generated by Al and Cloud services to detect what improvements and/or measurements are necessary. Use sensor measurements that have been collected to gain valuable insight into equipment needs, patterns, and the current condition of facility machinery.
Once collected data is analyzed, it is possible to deploy pilot equipment for ongoing tests and validation. Predictive algorithms that have been tested, verified, and validated can then be used throughout numerous machines and pieces of equipment in any sized facility.
In some cases, this process may take anywhere from a few weeks to a few months, depending on the size of the facility as well as the equipment and machinery utilized in pilot equipment tests.
Establish Implementation and Improvement Workflow
Establishing implementation and improvement workflow is possible once the initial analysis of pilot equipment and predictive algorithms are complete.
Once pilot testing is deployed and validated, it is possible to begin implementing a workflow that helps streamline operations of all facility equipment and machinery currently in use.
Getting Started With Predictive Maintenance
Developing a successful maintenance strategy is not always easy, and typically will require buy-ins from multiple stakeholders. Because predictive maintenance strategies are far from simplistic, most facilities and entities are required to have numerous stakeholders and plenty of available capital.
Facilities that are ready for a predictive maintenance strategy are often drawn to a matured facilities management program, although this is not always the most viable solution. For those who are still scaling up their facility but are interested in a predictive and proactive maintenance solution that is more suitable, the ServiceChannel platform can help.
Establishing a predictive and proactive maintenance strategy is essential for any thriving and scaling facility. With a proper predictive maintenance strategy, streamline operations, maximize output, and reduce the risk of machine and equipment failure year-round.