What is Facilities Maintenance Management?
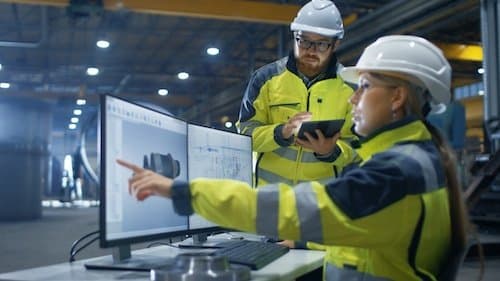
Discover Facilities Maintenance Management: Key Elements, Roles and Responsibilities, Benefits, Challenges, and Best Practices for Efficient Operations.
Facilities maintenance management refers to all of the processes, teams, and protocols involved in preserving assets, ensuring safety, and controlling costs related to equipment maintenance. Facility managers may oversee the facility maintenance system, or a separate facility maintenance management leader may take on the role instead.
Facility maintenance management will help your business stay competitive and contribute to your long-term, sustainable success.
Key Elements of Facilities Maintenance Management
Manufacturing plants, healthcare centers, educational facilities, and retail stores can all benefit from a similar facilities maintenance management system. Here are the key elements of that system that keep assets and facilities in optimal condition:
Preventive Maintenance
Preventive maintenance involves scheduled and routine tasks aimed at preventing equipment or facility failures before they occur. Such tasks include inspections, cleaning, adjustments, and replacements of components. Preventive maintenance management is vital to ensuring these tasks are completed on time. Facility managers assess their assets to ensure their preventive maintenance schedule matches their asset’s needs.
Corrective Maintenance
Corrective or reactive maintenance involves returning a malfunctioning asset to its original state. That includes emergency repairs, clean-ups, or additional non-urgent maintenance tasks on any asset needing correction. It’s important to reduce your need for corrective maintenance and have a streamlined system to ensure that unplanned downtime causes minimal core business disruptions.
Predictive Maintenance
Predictive maintenance leverages data and technology to predict when equipment or systems will likely fail. It uses sensors, data analysis, and machine learning algorithms to forecast maintenance needs. For instance, an Internet of Things (IoT) sensor on a machine can gauge its temperature to indicate overheating.
Facilities Assessment and Inspection
Regularly, your maintenance teams thoroughly evaluate a facility’s condition to identify potential issues, safety hazards, and maintenance needs. This practice is an excellent way to avoid incoming maintenance issues, reducing the likelihood of emergency repairs and minimizing downtime.
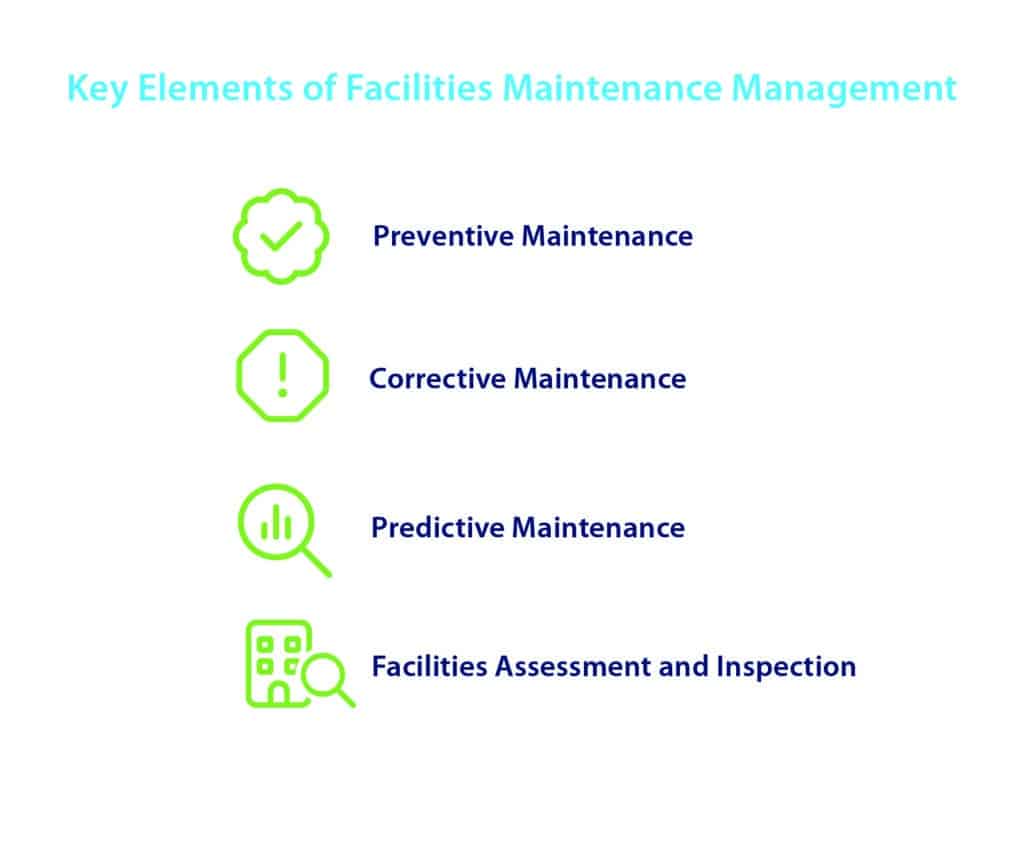
Roles and Responsibilities
Who’s responsible for what in your facilities maintenance system can vary based on your size, industry, and unique business practices. However, here is a general overview of who typically takes on what role in facility maintenance:
- Facility managers: Oversee the entire operation of the facility. They plan, coordinate, and manage all maintenance activities.
- Maintenance technicians: Perform routine maintenance tasks and fix issues like plumbing leaks, electrical faults, or problems with your HVAC units.
- Maintenance engineers: Install, troubleshoot, and repair specific types of equipment using industrial technology. They also diagnose equipment failures and apply specialized training to restore malfunctioning equipment to its original state.
- Safety officers: Ensure that all maintenance activities follow safety standards. They may also conduct regular inspections, building walkthroughs, and training sessions.
- Contractors: External experts hired for specialized tasks that the in-house maintenance team doesn’t handle.
- Service providers: Companies or individuals who offer specific services, such as cleaning, landscaping, or snow removal, if not covered by your internal maintenance team.
Benefits of Facilities Maintenance Management
Proper facilities maintenance management greatly reduces the time and money you spend maintaining your physical assets. Some of these benefits apply to proactive maintenance in general, while others are specific to having a maintenance management strategy.
Cost Reduction
Well-managed proactive maintenance reduces the money you will have to spend on repairs and replacements. Also, reliable equipment wastes less energy, so you’ll pay less on your utility bills. For example, inefficient HVAC units waste energy keeping themselves running instead of heating or cooling your facility.
Enhanced Safety
Scheduled maintenance improves workplace safety and enhances customer or client safety while they’re in your building. Facilities maintenance involves scheduled inspections that can detect potential safety flaws before they cause harm.
In your facilities maintenance management program, it’s also important to check safety equipment, such as fire safety systems (fire extinguishers, smoke alarms, etc.). Performing proactive maintenance on these assets ensures that they are in good working order if they are needed.
Improved Operational Efficiency
When certified facility managers and maintenance workers perform preventive maintenance activities, equipment reliability increases. Increasing equipment reliability means your workforce can count on the assets they need to do their job during working hours. Doing this helps prevent equipment failures from slowing your staff’s productivity.
Your maintenance management system contributes to a more productive environment by detecting new ways to enhance operational tasks. For instance, a routine inspection may reveal new ways of leveraging technology to streamline a particular workflow, even if the asset works fine.
Optimized Workflows
Maintenance managers will also streamline the maintenance tasks themselves. They may do this by scheduling maintenance activities, automating work orders, and allocating resources effectively. Facility managers contribute to this system by guiding maintenance management to plan maintenance schedules and activities around larger facility management goals.
Challenges of Facilities Maintenance Management
Despite its benefits, facilities maintenance management in most large commercial buildings (or residential buildings) can be a demanding task. The following list includes some of the most common challenges that a facility management team may face:
Limited Resources
Limited financial resources can make it challenging to perform necessary maintenance tasks. This limitation may lead to deferred maintenance and increased risks of equipment failures. Look at your maintenance strategy and consider where cost savings are possible. You may defer scheduled maintenance on less critical assets to save costs for more important equipment.
Labor Shortage
Finding and retaining skilled maintenance technicians and engineers can take time and effort. This challenge is especially prominent in niche industries that face a more significant labor shortage. Consider upskilling your current staff so they can perform as many maintenance duties as possible.
Not only will this help address skill gaps, but it will also help you retain employees. Professional development opportunities are a known effective employee retention strategy.
Regulatory Compliance
Adhering to changing building codes, environmental regulations, and safety standards requires continuous monitoring and adaptation. Most facilities management teams are busy with both maintenance management and other facility management tasks — quick pivots can be challenging to implement practically.
For this reason, you may want to designate someone on your team to perform strategic planning tasks in the face of these changes. Choose different people for different regulations, such as safety or environmental. This practice will help reduce the chance of your facility management team missing something.
Data Management
Handling vast amounts of data generated by sensors and maintenance management systems can be overwhelming. CMMS facility management tools can help reduce this burden significantly. Such software applications typically have everything you need to properly analyze data while keeping it all well-organized.
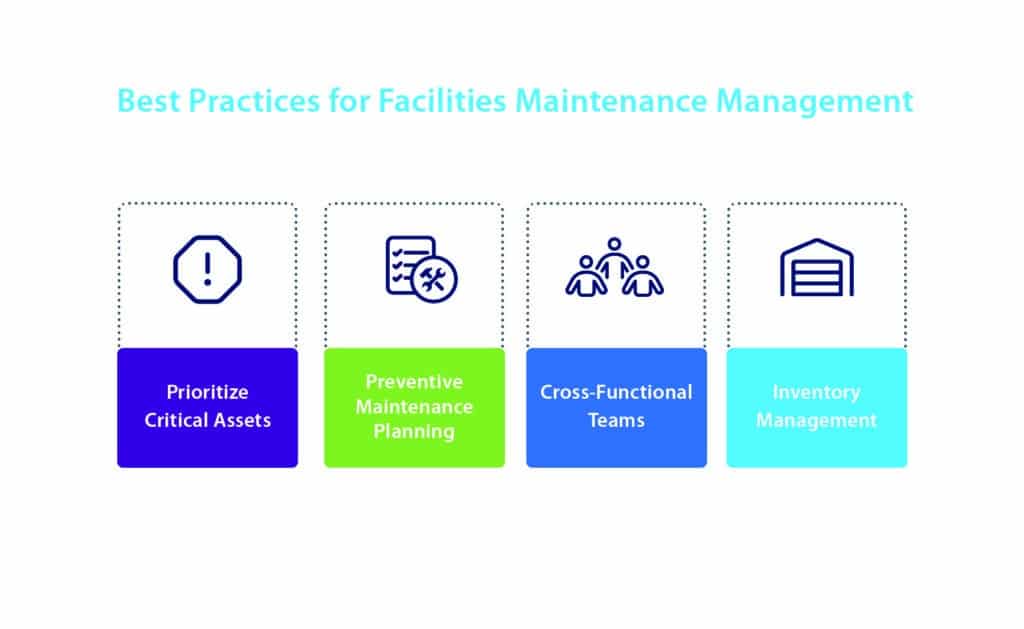
Best Practices for Facilities Maintenance Management
The best way for any facility maintenance management professional to reap many benefits with as few challenges as possible is simply by following best practices. Here are some standard facilities management best practices that are relevant to most industries:
Prioritize Critical Assets
Ensure that your most critical assets take priority. Critical assets refer to any machinery or equipment your employees need to do their jobs. It also refers to any asset that could cause health and safety risks or significant property damage if it were to fail.
Allocate more money and resources for these assets. While paying attention to your non-critical assets, ensure their maintenance is not at the expense of your more critical equipment.
Preventive Maintenance Planning
Create a preventive maintenance schedule that optimizes resource allocation and minimizes planned downtime. Of course, routine maintenance will involve some downtime. Schedule tasks outside of peak working hours to minimize downtime and reduce disruptions.
Remember, your preventive maintenance plan must involve your assets and surrounding infrastructure. Deteriorating building systems may contribute to an asset’s failure. For instance, crumbling walls may affect the wiring inside them. Think of your building, parking lots, and greenspace as assets themselves.
Cross-Functional Teams
Encourage collaboration between facility maintenance professionals and other departments. Share resources and knowledge to make the most of limited labor and budgets. Getting other departments involved in your maintenance management also encourages better care and usage of your assets throughout your facility.
Inventory Management
It’s important for the facility manager and maintenance professionals to proactively avoid stock-out situations. A stock-out may cause delays in needed maintenance since the parts needed to perform the task are unavailable. Use a well-managed inventory system and keep it up to date. Doing so will ensure that every maintenance technician has visibility into what’s available and what’s running low.
Effective Facilities Maintenance Management With ServiceChannel
Your entire process can be much simpler with the right facility management software offered by ServiceChannel, whether dealing with property maintenance, industrial maintenance, or more. This tool can streamline asset management tasks, improve capital assets planning, and enhance energy management across all assets.
Alongside these benefits, ServiceChannel also helps you improve asset performance based on strategically tracked performance benchmarks.
Run your facility proactively, not reactively, with our facility management software. Reach out to ServiceChannel for a free demo.