Keys to a Successful Preventive Maintenance Plan
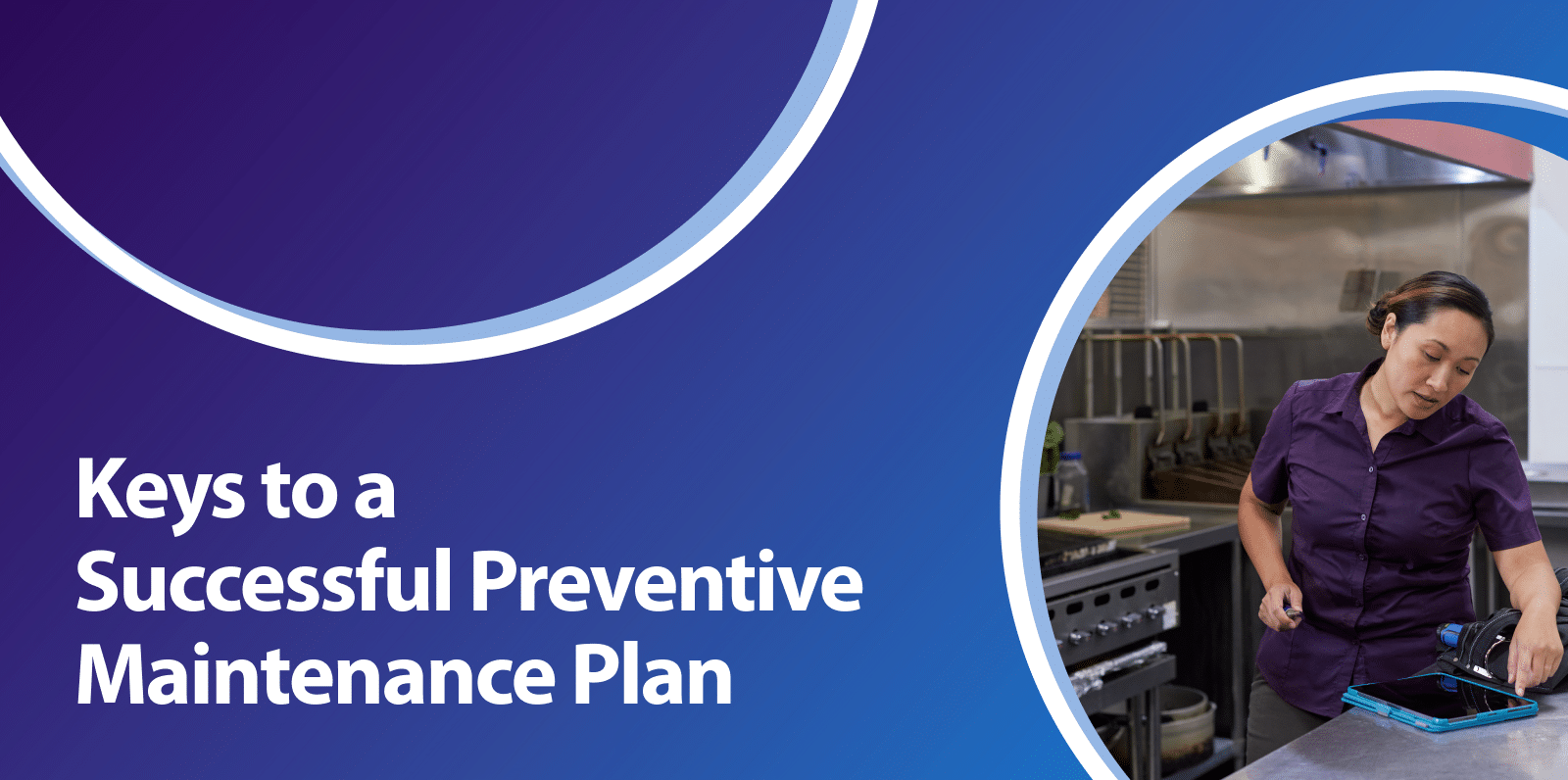
Preventive maintenance, also called preventative maintenance, includes actions performed regularly to lessen the chances of repairs and downtime in the future. The U.S. Navy pioneered the concept of preventive maintenance to improve its vessels’ reliability. A preventive maintenance program can save 12-18% percent over a reactive program.
A successful preventive maintenance program requires careful planning. A preventive maintenance plan includes short-term and long-term maintenance schedules for each piece of equipment. While developing a maintenance plan requires that you allocate time upfront, the program has significant financial benefits. A recent Jones Lang LaSalle study found that one telecommunications company gained a 545% ROI from implementing a preventive maintenance plan.
Why You Need a Preventive Maintenance Plan
Preventive management ensures your organization gets the most from your equipment and serves its customers well. For example, preventive maintenance significantly decreases the possibility that the equipment will break down. Broken equipment disrupts your ability to deliver your product or service to your customers.
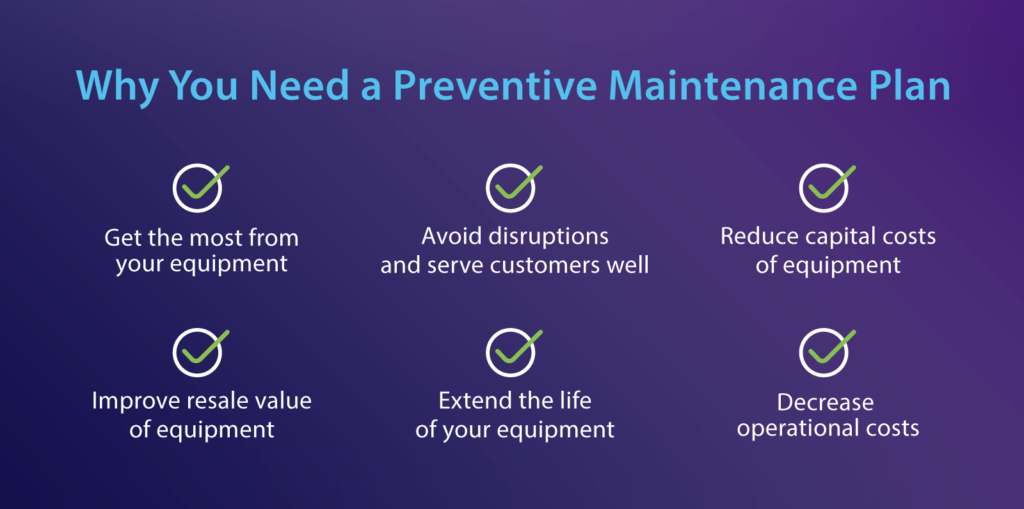
Preventive maintenance also extends the life of your equipment, reducing capital costs over the long term. It also improves the equipment’s resale value and enables it to operate more efficiently, decreasing operational costs.
Keys To Creating a Successful Preventive Maintenance Plan
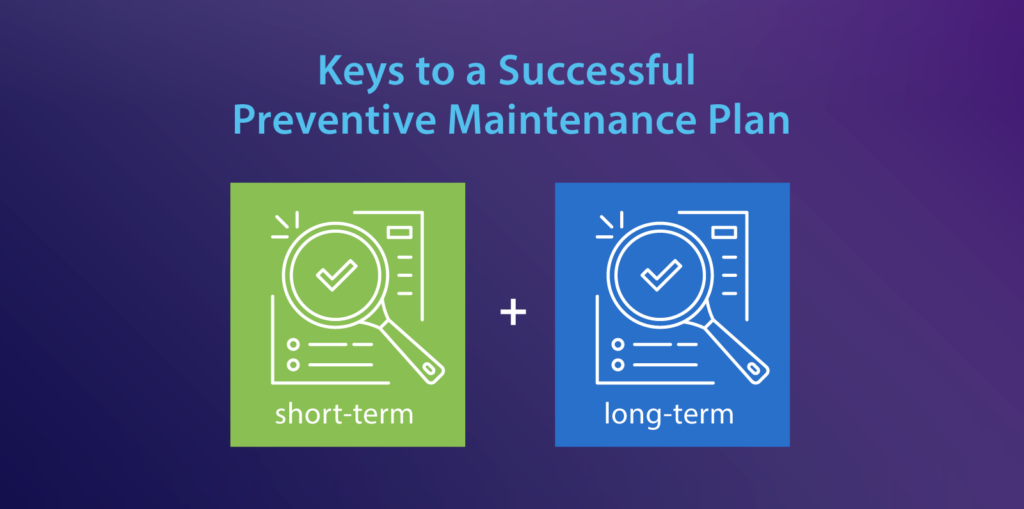
Asset Inventory
The first step in creating a preventive maintenance plan is to go through your facility and inventory the equipment you plan to include in your maintenance plan. Record information about each asset, including:
- Serial number
- Make and model
- QR and barcode
- Specifications and capabilities
- Location
- Category
- Which department is responsible for it?
Asset Prioritization
After conducting an inventory, you’ll want to prioritize which assets to include in your plan. Equipment already nearly worn out or not essential to creating your product or service may not need to be part of the plan.
When deciding what to include in your plan, consider the importance of each asset to productivity and safety. As part of identifying each asset’s significance, develop an asset hierarchy. An asset hierarchy indexes each machine and component and shows how each impacts other devices. This is also the first step in proper asset management.
Also, consider these questions:
- Is the equipment currently operating to the manufacturer’s specifications?
- Does the equipment require routine maintenance?
- How costly are repairs to the equipment?
Preventive Maintenance Schedule
The next step is to develop a schedule. Consulting the manufacturer’s maintenance recommendations is an excellent way to start. Typically, you’ll base your preventive maintenance schedule on either time or usage. For example, you might decide to maintain your fleet either every three months or every 12,000 miles. You’ll also want to schedule both short-term and long-term preventive maintenance.
Once you’ve determined how often to perform a maintenance task, you’ll schedule each task at a time when the equipment is not critical to production. You typically schedule tasks through a work order system.
CMMS Software
While you can schedule tasks and monitor preventive maintenance manually, using Cloud-based Maintenance Management Software – CMMS – makes the process easier. CMMS software streamlines preventive maintenance management in four significant ways.
- It allows facilities managers to create recurring work orders.
- It enables facilities managers to monitor the preventive maintenance process from anywhere.
- It automates invoicing.
- It helps you see trends, providing further hints on how to decrease costs.
Clear Communication
An effective preventive maintenance plan requires clear communication among members of your team. Poor communication can negatively affect your ability to execute your maintenance plan effectively. For example, it can result in delayed maintenance, poor prioritization of tasks, and overlapping work orders.
Goals and KPIs
The next step is to establish goals and key performance indicators. Your goals should be:
- Specific
- Measurable
- Achievable
- Relevant
- Time Bound
Examples of KPIs for measuring the success of your preventive maintenance plan are:
- The number of planned preventive tasks you completed over the period
- The time spent on scheduled vs. unplanned functions during the period
- The average time required to repair a specific piece of equipment
Support
Finally, before launching your plan, you’ll need to ensure that upper management supports it and will allocate money toward it. To gain full support, provide specific information on how the plan will improve the company’s bottom line. For example, select a few pieces of equipment, and determine how much downtime the equipment typically experiences in a year and the cost. Then show how much you’d save if you cut downtime by one-half or two-thirds.
Another way to gain senior management support is to show how developing a long-term maintenance plan fits the company’s overall goals.
Why Preventive Maintenance Plans Fail
Before you implement your plan, you’ll also want to understand why some programs fail so that you can avoid failure. The typical reasons preventive maintenance plans fail are:
- Inadequate training for technicians
- Failure to conduct root cause analysis to determine why equipment breaks down
- Inadequately overseeing the program.
- Lack of transparency
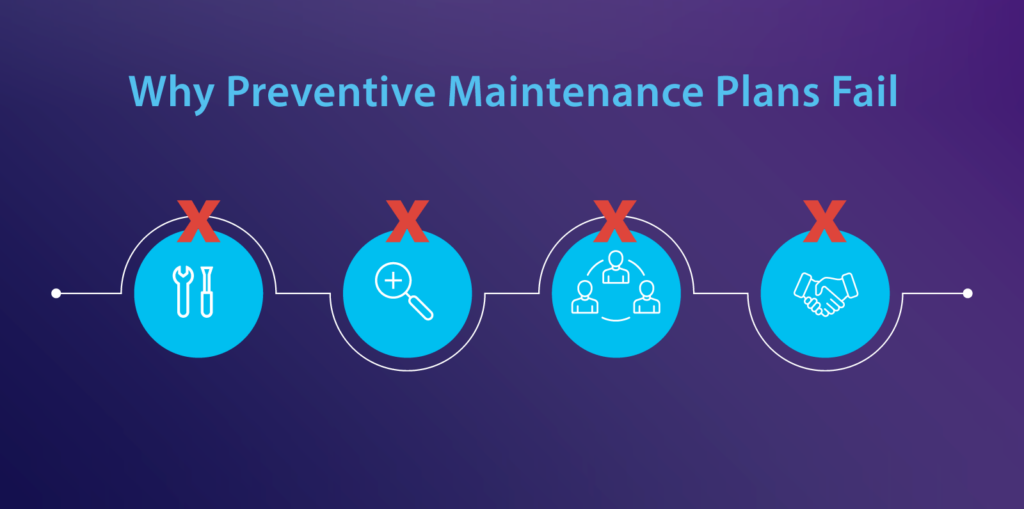
To avoid failure, carefully demonstrate the correct procedure for each technician and debrief frequently. Appoint someone to be accountable for ensuring the plan is executed correctly and for maintaining ongoing communication. CMMS software can help you find the root cause of breakdowns by allowing you to customize root cause analysis procedures to your company’s specific needs. It can also easily assign tasks in the process to team members.
How ServiceChannel Supports Maintenance Teams
Poorly managed maintenance schedules can account for as much as 40% of a company’s operational budget. ServiceChannel helps you proactively manage assets in every location. Our preventive maintenance software:
- Automates work orders using GPS data, photos, and other validation techniques
- Obtain quotes from the best experts
- Conduct site audits within the app
- Track asset health by integrating Internet-connected sensors with the platform
- Keep track of your maintenance
Talk with us today or book a demo to discover how we can help you develop and execute the perfect preventive maintenance plan.