Understanding Maintenance Strategies for Optimal Facility Management
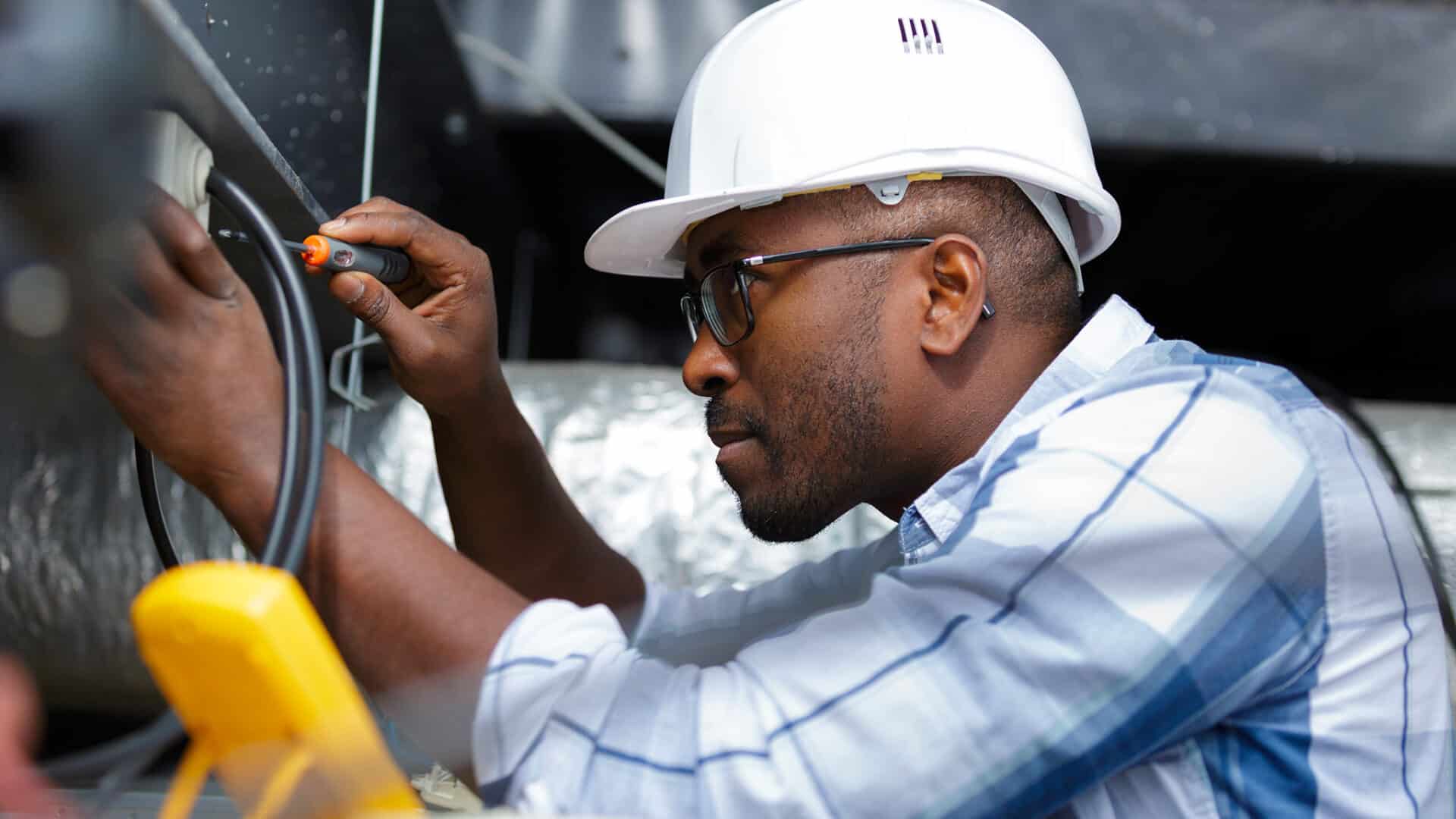
Learn how to optimize maintenance strategies for improved asset reliability, cost efficiency, and overall facility performance.
One of the most important tasks of facilities managers is understanding and implementing appropriate maintenance strategies as part of their maintenance management duties. Maintenance strategies vary based on the importance of assets to safety and production and by the cost impact of performing proactive maintenance over a run-to-failure approach.
Maintenance strategies are the cornerstone of an effective asset management plan. A solid maintenance plan helps to ensure extended equipment lifecycles and a safer operating environment. Choosing the right maintenance strategy for each asset enhances maintenance cost optimization by avoiding unexpected and costly repairs.
The Four Main Maintenance Strategies
Not every type of asset calls for the same maintenance strategy, but each strategy has its place in a maintenance management plan. What may work best for a power washer might not suit a sump pump.
Maintenance strategies fall into four main categories: reactive maintenance or run-to-failure maintenance, preventive maintenance, predictive maintenance, and reliability-centered maintenance. Each has advantages and disadvantages.
Reactive Maintenance
Also called the run-to-failure maintenance strategy or breakdown maintenance strategy, reactive maintenance is a policy of waiting until an asset breaks or malfunctions to address it. One can easily mistake a reactive maintenance strategy as having no strategy, but it is the most cost-effective approach in many circumstances.
Reactive maintenance works best on assets that aren’t vital to operations or won’t cause a safety hazard if they break down.
Pros of a Reactive Maintenance Strategy
One major advantage of reactive maintenance is continuous operation. The cost to replace or repair items that would fit into this maintenance plan is typically much less than the collective maintenance costs of proactive upkeep.
Cons of a Reactive Maintenance Strategy
You often don’t know an asset is failing until it fails. Facility managers must carefully implement a breakdown maintenance strategy for low-impact assets. Enacting such a policy on high-impact equipment could lead to serious issues if a breakdown occurs.
Preventive Maintenance
Preventive maintenance is the practice of scheduling regular maintenance and inspections. This proactive approach enables maintenance teams to catch potential issues before they escalate into a more dramatic problem.
A preventative maintenance program works best when performed according to a set schedule. Set schedules prioritizing more frequent maintenance on assets with the highest impact on production, cost, and safety.
Pros of a Preventive Maintenance Strategy
Preventive maintenance practices enable personnel to repair or replace components before they fail and let facility managers build maintenance time into the production schedule. Managers are also better able to assign specific personnel to future maintenance tasks. A proactive strategy maximizes production time and reduces additional lost time, parts, and labor costs throughout the equipment lifecycle.
Cons of a Preventive Maintenance Strategy
Overscheduling preventive maintenance risks unnecessary waste, which can take valuable time away from maintenance and could have a greater impact on productivity.
Predictive Maintenance
The predictive maintenance strategy incorporates technology to anticipate problems before they’re human-detectable. Advanced sensors, real-time data gathering, and analytics empower condition-based monitoring, which gives the software a narrow view of equipment and parts and a holistic view of an integrated system.
Pros of a Predictive Maintenance Strategy
By interconnecting and communicating with a central system over an Internet of Things (IoT) network, operators can know the status of every piece of equipment and critical component during operation. The system alerts users to anomalous conditions, such as abnormal vibrations or elevated heat levels, enabling a maintenance team to address the situation immediately. This saves the organization substantial dollars in unplanned downtime, extended labor costs, and more expensive repairs.
Cons of a Predictive Maintenance Strategy
The technology and training that an effective predictive maintenance strategy requires usually comes with substantial up-front costs. Additionally, the hardware components involved require their own upkeep, calibration, and monitoring to continue operating properly.
Reliability-Centered Maintenance (RCM)
The modern reliability-centered maintenance strategy uses technology to evaluate and analyze each asset and construct a Failure Modes and Effects Analysis (FMEA) model. The model summarizes the likelihood and the consequences of failure for each asset.
The reliability-centered maintenance method stands on five key principles.
- Prioritize assets
- Identify failure modes and effects
- Maintain functionality
- Construct action plans to address each failure mode
- Continually improve maintenance methods
Pros of a Reliability-Centered Maintenance Strategy
RCM takes an individualized approach, enabling personnel to target specific assets and perform only the necessary maintenance tasks. A more targeted approach reduces downtime by foregoing unnecessary inspection and upkeep.
Cons of a Reliability-Centered Maintenance Strategy
The RCM strategy is highly complex. It functions best when carried out by knowledgeable facility managers and maintenance staff and is best suited for sophisticated assets.
Assessing Your Facility’s Maintenance Needs
By determining which maintenance types work best for which assets, you can build out a holistic maintenance scheme that works optimally for the entire facility structure. These steps can help construct an effective maintenance plan.
Conduct an Assessment
A comprehensive inventory of all assets and equipment simplifies anticipating future expenditures and evaluating current maintenance costs. Locate, identify, and document all repairable assets and equipment. Determine the consumable parts and critical components required to operate and calculate the cost of replacing each item.
Identify Critical Assets
Determine the criticality of each facility asset by evaluating its importance for proper operation. Determine the safety risks assets could pose if they malfunction and rank them accordingly.
High-priority assets primarily describe equipment and items that would halt production or cause a safety hazard if they were to fail, such as a chemical holding tank in a chemical plant.
Medium-priority assets might be items that could slow down production if they fail but wouldn’t cause a safety hazard or bring production to a halt, like a box taper.
Low-priority assets would typically include items of low monetary value that have little to no impact on production or safety, such as breakroom chairs or an overhead speaker.
Evaluate Current Practices
Comparing asset care and upkeep needs with the maintenance they currently receive can help streamline maintenance tasks and scheduling. Conduct a comprehensive assessment of your current maintenance practices. Look for areas where assets might receive more upkeep than necessary and identify situations where equipment needs aren’t met. Look at maintenance checklists and compare them against equipment conditions to determine whether additional tasks should be added to the current workload.
Develop a Maintenance Plan
After completing evaluations and assessments of your assets and their maintenance requirements, the next step is to craft a maintenance plan and schedule that meet those needs. Assign an appropriate maintenance strategy to each asset. Determine individual maintenance tasks for each asset and set a schedule for personnel to perform the specific duties.
Integrating Maintenance Strategies with Facility Management Goals
Maintenance requirements vary widely, and no uniform approach works for all companies and industries. Theoretical understanding and practical application of maintenance strategies can be worlds apart. Facility managers should work with upper management, project managers, equipment operators, and maintenance staff to establish facility management goals for facility and asset maintenance and to monitor the effectiveness of maintenance activities.
Align Strategies
Understanding how each asset fits your facility’s goals is key to integrating maintenance strategies with those objectives. Determine the necessity of each asset in fulfilling your company’s objectives and evaluate maintenance needs for each. Consider how each strategy would impact facility assets and the cost-effectiveness of assigning a maintenance strategy.
Track Effectiveness
Establish key performance indicators (KPIs) to help determine the effectiveness of maintenance strategies that have been implemented. Consider your facility goals when deciding which key maintenance performance indicators best reflect your organization’s objectives. Vital maintenance KPIs often used across most industries include:
- Mean time between failures (MTBF)
- Maintenance backlog
- Overall equipment performance
- Overall equipment downtime
- Individual equipment downtime
- Maintenance cost as a percentage of RAV (replacement asset value) cost
Balance Cost and Reliability
Maintenance cost as a percentage of replacement asset value RAV effectively measures the balance between maintenance costs and reliability. Replacement Asset Value (RAV) is the cost to replace an asset at its present value, including the cost of removing and disposing of the current asset and the expense of moving and installing the new asset.
Maintenance cost percentage (MCP) is a metric that contrasts the annual asset maintenance cost (AMC) against the total asset replacement cost (ARC). The formula is simple: MCP = AMC ÷ ARC. Asset maintenance cost includes the expense of time labor, parts, and lost production time. A lower maintenance cost percentage indicates greater asset reliability.
Leveraging Technology for Effective Maintenance Management
Facility maintenance technologies have advanced significantly over the years, offering facilities managers greater ease and reliability in scheduling and overseeing maintenance activities. A number of key facility management innovations have found a welcome place in commercial and industrial facility environments. Depending on an organization’s maintenance needs, these technologies can work effectively together or independently.
Computerized Maintenance Management Systems (CMMS)
An essential technology solution for enterprise maintenance teams everywhere, CMMS software enables personnel to easily track facility assets, schedule maintenance activities, and track work orders. Often used alongside computer-aided facility management software (CAFM), a CMMS can meet the facility needs of many organizations.
Enterprise Asset Management (EAM) Software
While enterprise asset management software assists with maintenance activities as a CMMS does, the main focus of EAM software is managing and maintaining assets and equipment rather than the facility as a whole. Like CMMS, EAM often possesses work order management and maintenance scheduling capabilities. EAM software also usually incorporates supply chain and inventory management tools to help handle activities such as asset acquisition, equipment decommissioning, and many other asset-specific functions.
Emerging Technologies
Many software and hardware technologies have dramatically improved facility and asset management efforts. Artificial intelligence (AI) and machine learning have enabled maintenance software to learn asset patterns, such as asset condition thresholds. These AI tools enable the software to more accurately predict expected breakdowns and make personnel recommendations. The Internet of Things (IoT) enables equipment to effectively communicate with a central server while sensors feed real-time condition and activity data to the system for analysis.
Technology Solution Best Practices
Utilizing technology to its maximum potential yields the most effective outcomes for facilities. CMMS and EAM software platforms provide a vast array of tools and utilities that can be customized to fit your organization’s specific maintenance and facility management needs.
Take advantage of every capability your technology solutions provide. Establish thresholds and benchmarks and set alerts to inform personnel of undesirable equipment statuses and asset conditions. Automate work order systems to reduce the potential for human error when submitting requests. Use sensors and monitoring systems to gather comprehensive data. The more data points that analytic tools have, the more targeted your approach can be.
Overcoming Common Maintenance Strategy Challenges
Implementing and maintaining a maintenance plan doesn’t come without some obstacles. Over the course of your facility maintenance plan, consider the following common situations that can pose challenges for your maintenance personnel and facility management.
- Resource constraints such as available labor, materials, tools, and budgetary limitations
- The condition of aging assets and infrastructure
- Change management efforts to implement new and adapt current maintenance practices
- Implementation training and continuing education to stay on top of current industry practices
The Future of Maintenance in Facilities Management
Advancements are moving fast in the 21st century. The world is entering the fourth industrial revolution, collectively referred to as Industry 4.0. This revolution revolves around digital technologies and interconnectivity.
Augmented reality (AR) and virtual reality (VR) are at the forefront of the digital revolution. These technologies offer maintenance personnel learning tools that replicate their environment and assets safely, giving them virtual hands-on training.
Predictive analytics and data-driven decision-making practices continue to grow across all industries. They empower companies to anticipate issues and adequately prepare to address complications before they arise.
As industries everywhere move toward a greener, cleaner world, companies continue to explore effective environmental and sustainability practices.
Help Define Your Maintenance Strategy With ServiceChannel
It’s clear that no one maintenance strategy is going to work for every asset and piece of equipment, so integrating each strategy where it works best is the optimal solution. As you conduct your maintenance plan, you’ll inevitably find areas that require adjustment. Continual improvement is all part of a dynamic maintenance program.
Facility management software solutions like ServiceChannel give companies a strong advantage in developing and instituting a maintenance plan. Asset tracking, work order management, and maintenance scheduling tools enable facilities managers to manage maintenance activities efficiently. Look into ServiceChannel today and see how this powerful platform can help you achieve your maintenance goals.