Are Your Facilities Prepared for Extreme Summer Weather?
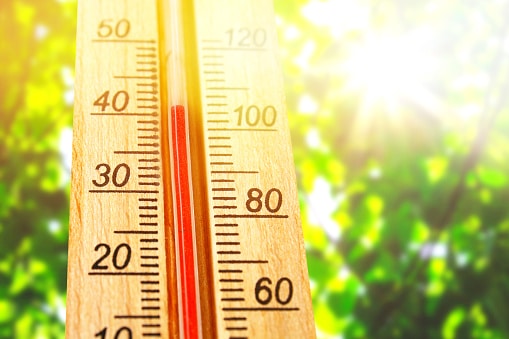
While most would consider winter weather to pose the greatest challenge to facilities managers, the hot summer months can bring their own set of difficulties. Thunderstorms, heavy rains, wildfires, tornadoes, extreme heat, and even hurricanes can put businesses at risk for serious damage – and, if not caught early, this can lead to significant operational downtime. In fact, more than 40% of businesses close their doors after a natural disaster. Of those that do remain open, only 29% continue operating after two years.
Climate change has already proven to be a serious challenge for FM professionals around the world. Weather events are predicted to become steadily more extreme in the coming years. And while we may do our best to implement environmentally-friendly building technologies, we cannot prevent much of what’s to come. However, with proper preparation and best practices in place, facilities managers can at the very least minimize weather-related damage and mitigate devastating losses.
Today’s technology has made building monitoring a much more sophisticated process: The right network of sensors can make the difference between millions of dollars in damage and no damage at all. In this blog, we’ll take a look at a few of these technologies and tactics with which to prepare your facilities for extreme weather conditions. While these steps may not create a weatherproof forcefield around your commercial buildings, they’ll help provide some peace of mind for you and the rest of your team – protecting inventory, revenue, and even lives.
Environmental Monitoring
Environmental monitoring technology involves sensors that detect and record temperature, humidity, air quality, pressure, water levels, and other important environmental factors. Many of today’s “smart buildings” are constructed with this technology already in place.
These sensors may be IoT-based – meaning they collect and store data via connected, Internet-based networks for constant monitoring capabilities. Environmental monitoring sensors can be programmed to detect abnormalities in real-time and alert facility teams of a potential problem. This is especially helpful during the summer months when temperatures and humidity levels are prone to sudden spikes.
Environmental monitoring systems go far beyond your basic smoke alarm: They offer preventive features, using historical data to interpret when a fire or other emergency may be likely (when a gas leak is detected, for instance, or during an extended drought) and can adjust thermostat settings accordingly. In addition, they can rapidly alert the right individuals of the precise location of the problem for easy containment. Since these alerts can be sent directly to facilities managers via their personal devices, a minor, non-threatening alert won’t disrupt business as usual by triggering a building-wide alarm.
Environmental monitoring technology is rapidly becoming the status quo for commercial buildings of all sizes – and it is especially important for businesses whose inventory is perishable, flammable, or hazardous. Hospitals, pharmacies, warehouses, and chemical plants, in particular, must all invest in the latest environmental monitoring technology to prevent devastating community-wide disasters in the event of a weather emergency. For these businesses, even a summer heatwave can have dire consequences.
Preventive Maintenance
Preventive maintenance is a critical component of any strong facilities management program. While it sounds like a simple enough concept, the details involved in preventive asset maintenance – scheduling, performing, and strategizing – adds up to a sizeable workload.
This is especially true when these tasks are carried out manually, without the help of technology and historical data to inform decision-making processes.
HVAC
In the summer months, a failed HVAC unit can bring your business to a complete halt. Let’s say, for instance, you own a grocery store. If that store loses air conditioning for even a single day while outdoor temperatures are soaring, hundreds of dollars of produce and other perishable items may be lost (not to mention your customers).
Most breakdowns are simply a result of aging parts or equipment; with the right technology in place, you’ll be able to keep track of and even predict which assets are likely to require maintenance or replacement before a system fails.
Older HVAC units, for example, need to work harder in the summer: It’s during this time that components tend to degrade and small leaks appear. When the unit works harder to balance out soaring outdoor temperatures, energy consumption increases. The added vibration frequency only leads to a greater chance of failure. However, by strategically measuring temperature, thermostat position, energy consumption, and vibrations, FM professionals can determine as little as two days ahead of time when a unit is going to fail and act accordingly.
It’s also helpful to note that old or underperforming air conditioners are much more costly to run – especially when heat and humidity levels reach their peak in July and August. You need a cool and comfortable building to continue to attract customers, but you also want to mitigate your energy costs. If your cooling system isn’t professionally maintained, you will end up spending far more than expected: A simple duct leak may result in up to a 30 percent energy loss.
Refrigeration
Refrigerant leaks are another common problem that both stores and restaurants may face during the summer months. Corrosion or thermal stress can both increase the likelihood of a leak, especially if fittings have been tightened improperly or your system has been retrofitted with a new type of refrigerant oil.
A failed or leaking refrigerator can lead to spoiled merchandise and even structural damage – so it’s especially important to monitor refrigerant usage and performance when outdoor temperatures heat up. ServiceChannel’s Refrigerant Tracking Manager makes it simple to capture refrigerant information, helping you avoid fines by maintaining EPA compliance and keeping your systems performing optimally during peak season.
With a Service Automation platform, your team can realize savings of up to 18-22 percent on repair and maintenance via advanced work order and compliance management capabilities, as well as increased visibility into asset performance, repair history, and costs. This makes it easy for FMs to decide ahead of time whether that 7-year-old air conditioning system might need servicing ahead of the summer season – and exactly how much to spend on it.
Seasonal Checklist
Smart facilities managers will employ technology and strategic thinking to plan ahead for common summer problems. Create a seasonal maintenance checklist based on historical data, using this information to predict common problems or breakdowns that may have arisen in the past due to hot weather, storms, or heavy rains. Planning can begin as early as March or April, depending on your local climate and weather patterns.
At a minimum, facilities managers should include each of the following items on their summer maintenance checklist:
-
- Thoroughly examine air conditioning units; clean coils, change filters, and check refrigerant levels
- Ensure building thermostats are working properly
- Clean air ducts and check air quality levels to maintain proper ventilation
- Confirm emergency procedures in case of severe weather, electrical outages, or fires
- Check backup generators for leaks, corrosion, or torn gaskets; inspect fuel lines; check coolant levels
- Perform regular maintenance on all safety and alarm systems
Don’t forget to include any additional, industry-specific assets – such as refrigerators or industrial fans – that are relied upon more heavily during the summer season.
Final Thoughts
Typical weather patterns are becoming far less predictable – and as such, facilities managers must continually prepare for the unexpected. This is especially true when the weather heats up for the summer and severe storms increase in frequency. While it’s impossible to entirely prevent a disaster, facilities managers can employ a few key strategies and technologies to mitigate (or even prevent) major losses. Environmental monitoring technology, year-round preventive maintenance, and a seasonal FM checklist are the first steps towards a well-rounded resilience planning program.
Learn how to maximize your facilities management program year-round: Contact us for a free demo.