Maintenance Management Essentials for Peak Facility Performance
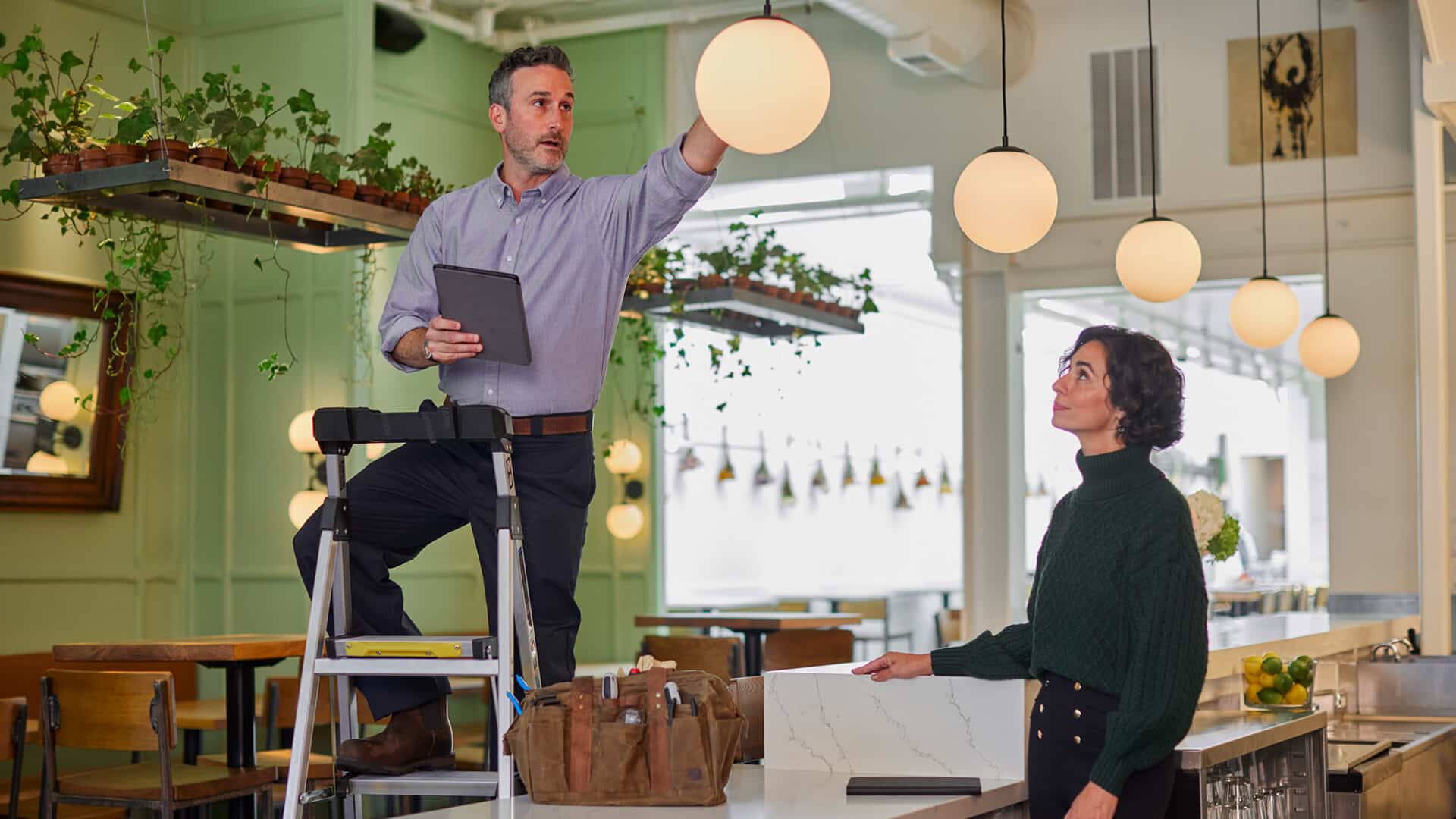
Boost your facility’s performance with this ultimate guide to maintenance management strategies, tips, and best practices for facilities managers.
Maintenance management involves everything that a facility does to keep its assets in peak condition. Therefore, proper maintenance management is key to efficient maintenance operations. Without it, maintenance personnel are left with little direction, and a company’s physical assets may become neglected.
Effective maintenance management helps prolong assets’ lifespans and reduces unplanned downtime and repairs. Facilities managers must schedule regular maintenance to achieve these benefits. However, facilities may choose from varying types of maintenance management strategies.
Understanding The Types of Maintenance Strategies
Maintenance managers may choose several different types of maintenance strategies. The right one depends on what your company’s assets need to uphold operational efficiency.
Preventive Maintenance
Preventive maintenance involves regularly scheduled inspections that prevent equipment failure. This strategy reduces downtime and extends the life of assets. The fewer breakdowns an asset experiences, the less wear it will have.
A few best practices include:
- Setting a maintenance schedule based on both manufacturer recommendations and past performance data
- Training staff on proper equipment use at any time so maintenance tasks are easier
- Monitoring maintenance activities for continuous improvement
Predictive Maintenance
Predictive maintenance uses data analysis tools and techniques to detect early warning signs before failure occurs. The main advantages are that it can prevent unexpected equipment failures and reduce maintenance costs.
Technologies used include:
- IoT sensors
- Thermal imaging
- Predictive analytics
- Artificial intelligence (AI)
Condition-Based Maintenance
Condition-based maintenance involves monitoring the actual condition of the asset to decide what maintenance needs to be done. As a result, maintenance work is only performed when it’s necessary. Therefore, your facility saves money and increases maintenance team availability.
Reliability-Centered Maintenance (RCM)
Reliability-centered maintenance (RCM) focuses on maintaining the reliability of machines by identifying and addressing potential failures before they occur. Key principles include understanding what failures could occur, how they would impact operations, and improving maintenance processes to keep such failures minimal.
To implement RCM, follow these steps.
- Identify which assets are critical to your operations
- Determine how each critical asset might fail
- Evaluate the impact of each potential failure
- Create plans to address each identified potential failure
- Put the maintenance strategies into action and track their effectiveness
Prescriptive Maintenance
Prescriptive maintenance is a strategy that leverages machine learning to provide highly specific maintenance information. By analyzing equipment data, it can predict when maintenance is needed and prescribe the best course of action.
While it’s similar to predictive maintenance, it provides the additional benefit of analyzing and predicting the best maintenance activities, not simply when maintenance is needed.
Selecting and Implementing a Computerized Maintenance Management System (CMMS)
Using software for maintenance management can radically improve how facilities handle this task. Software tools allow organizations to quickly schedule regular maintenance, predict when machines might fail, and keep a detailed history of repairs in one centralized location.
The type of software used for this is called a computerized maintenance management system (CMMS).
What is a CMMS?
A CMMS helps organizations manage their maintenance operations more effectively. It provides a centralized platform for tracking work orders, scheduling repairs, managing inventory, and analyzing maintenance data.
Key Features to Look for in CMMS Software
Work Order Management
Work order management features let you create, track, and manage maintenance tasks efficiently. This can help ensure that all necessary repairs and maintenance are documented and completed on time. This feature aids in maintaining a clear history of maintenance work and improving accountability.
Asset Management
Asset management features within a CMMS help you keep a detailed record of all your assets, including their lifecycle history, maintenance schedules, and key performance metrics.
This feature enables you to maximize the efficiency of your assets by ensuring timely maintenance that reduces downtime.
Maintenance Scheduling
A CMMS needs maintenance scheduling features to help you organize maintenance tasks in advance. This ability is key if you intend to establish a proactive maintenance program outside peak work hours. Doing so ensures that maintenance teams can do what needs to be done without impacting employee productivity.
Inventory Management
Inventory management features in CMMS software enable effective tracking and control of the spare parts, tools, and materials that your maintenance workers need to do their jobs. These insights help ensure that the right parts are available at the right time, reducing your facility’s maintenance delays.
Achieving Operational Excellence in Facilities Management
Choosing your maintenance management strategy and the right CMMS software is one part of the picture. To fully achieve operational excellence, you’ll need to implement best practices that will help you reap more benefits of maintenance management:
- Standardize maintenance procedures to reduce variability, enhance predictability, and ensure consistent quality
- Create clear, documented workflows for each maintenance task
- Offer regular training sessions to ensure that staff members are up-to-date with the latest operational strategies
- Optimize the use of physical assets to better manage inventory and reduce waste
- Regularly review processes and performance metrics to identify areas for enhancement
Technology can help you make these best practices simpler. Connected IoT sensors help your maintenance management team detect emerging issues in real-time, while mobile apps can help maintenance technicians access vital information on the go.
Here are some best practices to review your maintenance management program for areas of improvement:
- Define clear, measurable goals for your maintenance management program. This clarity will help you focus your improvement efforts and evaluate success.
- Collect data related to your current maintenance operations. This could include response times, repair times, costs, and equipment performance. Analyzing this data will help identify areas for improvement.
- Gather input and feedback from maintenance teams, as they can offer valuable insights into real challenges and their potential solutions.
- Prioritize changes that would have the most significant impact on efficiency and effectiveness. Focus on quick wins that can build momentum for further improvements.
- Prepare a detailed plan for implementing changes, including timelines, responsibilities, and resources needed. Communicate this plan clearly to all stakeholders.
- Once changes are implemented, closely monitor their impact. Use key performance indicators (KPIs) to track progress and make adjustments as needed.
Tracking and Improving Facility Management KPIs
KPIs provide a clear picture of asset performance before and after routine maintenance. This helps facilities managers determine how to enhance their maintenance strategy and make decisions about resource allocation. Important facility management KPIs include:
- Equipment Downtime
- Maintenance Costs
- Work Order Completion Rate
- Planned Maintenance Percentage
- Mean Time Between Failures (MTBF)
Strategies for Improving KPIs
Optimize Resource Allocation
Efficiently allocating resources ensures that maintenance is completed more effectively and efficiently. As a result, you will directly improve your work order completion rate. Having all the resources in place in time reduces delays.
Implement Asset Lifecycle Management
Understanding and managing assets’ lifecycles allows for better planning of maintenance, replacements, and upgrades. This strategic focus can prolong your equipment’s useful life and improve your MTBF.
Engage in Supplier and Vendor Management
Developing strong relationships with suppliers and vendors can lead to better support, more favorable terms, and higher-quality materials. This can reduce maintenance costs by helping you secure more cost-effective solutions. It can also reduce production downtime through faster resource procurement.
Adopt Technology and Automation
Technology and automation in maintenance processes can streamline operations and reduce human errors. Computerized maintenance management systems can help better schedule, track, and analyze tasks. These benefits will directly improve your planned maintenance percentage and reduce costs.
Leverage Data Analytics for Decision-Making
Using data analytics to analyze maintenance records and performance data helps identify patterns and trends that can inform decision-making and lead to targeted improvements. These optimize your planned maintenance percentage and cost KPIs by allocating resources to the most critical areas.
Leveraging Data Analytics and Reporting
By systematically examining maintenance records and performance data, facilities can pinpoint areas for improvement and make informed decisions to optimize operations.
Here are some key metrics to analyze.
- Downtime Duration
- Failure Rate
- Mean Time to Repair (MTTR)
- Preventive Maintenance Compliance (PMC)
Several data visualization techniques are employed to effectively communicate the insights drawn from maintenance and performance data. The most common data visualization techniques include:
- Bar charts
- Line charts
- Heat maps
- Pie graphs
Driving Improvements with Insights
Resource Allocation
Insights from data analysis can inform better allocation of maintenance resources. If the data indicates certain equipment types or locations are more prone to failures, additional resources can be directed there to reduce downtime.
Cost Reduction
Studying how costs change over time can help facilities find ways to save money. For instance, a facility manager might notice that certain suppliers or specific parts often lead to failures and need frequent replacement. Knowing this can help them get better deals or find higher-quality parts.
Performance Benchmarking
Comparing data with industry standards can help facilities understand where they stand against competitors and identify areas for improvement.
Effective Spare Parts Inventory Management
Effective spare parts management is key to maintaining the right balance of spare parts. You want enough to prevent operational delays, but overstocking can needlessly tie up capital. Conduct regular checks to ensure the accuracy of inventory records. This helps you identify discrepancies early and proactively adjust inventory levels to match actual needs.
It’s also a good idea to adopt just-in-time (JIT) inventory management practices. The JIT approach minimizes stock levels by encouraging you to only order parts as they are needed. However, precise demand forecasting is required to properly maintain this practice.
Still, all parts ultimately depend on the reliability of your supply chain. Therefore, vendor management best practices are equally as important. Avoid relying on a single supplier and regularly evaluate supplier performance based on criteria like delivery timeliness, quality of goods, and response to issues.
For items with long shelf lives that won’t require a lot of capital, consider bulk purchasing to take advantage of volume discounts. Like grocery shopping, bulk discounts can help reduce inventory costs. You can also use long-term relationships with suppliers to negotiate better prices and payment terms.
Some CMMS solutions include features for managing supplier information, making ordering parts and tracking deliveries easier. Even if your CMMS doesn’t have this feature, any CMMS tool will help reduce the chances of human error by automating updates to ensure you have the most current inventory data.
The Business Case for Maintenance Management Software
A compelling business case does more than just justify the need for new software. It will also show why the tool is worth the investment based on its ability to improve business operations.
Don’t simply consider filling a gap in your business case proposal. Consider how the tool will improve processes that already work well. For example, if your facility has problems tracking costs, you could show how the CMMS software will make the process easier. Alternatively, you could present it as a simpler way to organize maintenance contracts.
A cost-benefit analysis compares the investment’s costs with the benefits it will bring over time. It’s a good idea to perform this analysis for your chosen CMMS before you propose it to upper management. If you can demonstrate the tool’s ROI, stakeholders are more likely to see its value.
To calculate ROI, you need to estimate the total cost of ownership (including purchase price, implementation costs, and ongoing operating expenses) and the anticipated financial gains (like cost savings and increased revenue).
Then, plug your estimated costs into this formula.
ROI = (Total Benefits – Total Costs/Total Costs) x 100
The result will be a percentage. The higher the percentage, the higher the ROI.
Tips For Presenting Your Maintenance Management Software Proposal
- Use clear, concise language to explain the benefits and costs.
- Focus on the benefits and use real data to illustrate these points.
- Use visuals like graphs, charts, or infographics to make your case.
- Be prepared to answer questions about the implementation process, costs, timeline, and how disruptions will be minimized during the transition period.
Integrating Maintenance Management with Other Facility Functions
Integrating maintenance management with other facility functions offers a comprehensive view of operations. This helps maintenance managers streamline processes, reduce operational costs, and enhance asset longevity based on real insights.
Moreover, a holistic approach to facility management can simplify the process of ensuring regulatory compliance standards are met.
For example, integrating a maintenance management software tool with an enterprise resource planning (ERP) system may allow for automated record-keeping. Therefore, when audits happen, maintenance managers can easily show proof of compliance through detailed reports generated by the system.
Here are more examples of systems that could benefit from integration:
Energy Management
Integrating these two systems allows facilities to monitor energy consumption and waste production better. As a result, you can lower your energy costs and contribute to environmental sustainability.
Space Planning
Combining maintenance management with space planning ensures that physical spaces are used efficiently. This integration supports tracking space utilization and the condition of assets within these spaces. This information helps managers make informed decisions about space allocation and maintain operational efficiency.
Capital Project Management
When your maintenance system is integrated with capital project management, it ensures that new projects are aligned with your maintenance strategies. This alignment ensures that new assets move smoothly from the project phase to the operational phase and are properly maintained right from the beginning.
Enterprise Asset Management
Integrating maintenance management with enterprise asset management (EAM) offers a full view of your facility’s assets and their conditions. This full view improves how maintenance activities are planned, scheduled, and carried out.
Implementing a Successful Preventive Maintenance Program
To implement your preventive maintenance program, follow these 6 key steps.
- Establish Goals: Begin by assessing your current maintenance needs. Identify all equipment and systems requiring regular maintenance. Consider how the objectives of maintenance management align with your larger business goals.
- Take an Inventory of Assets: Document all relevant details about your assets to facilitate upcoming maintenance procedures. These should include step-by-step instructions, safety training, and a list of needed materials.
- Prioritize Assets Based on Criticality: Rank assets by the impact of their potential failure on your operations. Make more critical assets a higher maintenance priority.
- Select a Preventive Maintenance Strategy: Choose the maintenance approach that best fits your facility’s and each asset’s care needs. Based on your situation, you may choose different strategies for different assets.
- Create Your Preventive Maintenance Checklist: Create a maintenance schedule that balances the workload with operational demands. Schedule tasks during low-production periods to minimize impact on operations.
- Assign Tasks and Allocate Resources: Ensure adequate resources and provide detailed job plans for maintenance teams. Train your team on the specifics of each procedure, focusing on safety, best practices, and the use of any specialized equipment.
Enhance Your Maintenance Management With ServiceChannel’s CMMS Software
A proactive and data-driven approach to maintenance management is your facility’s key to maintenance success. A good preventive maintenance platform can make that easier to attain.
ServiceChannel provides excellent preventive maintenance software that you can use to accomplish this task. With us, you’ll experience a more productive work environment, all thanks to proper maintenance management.