What is Scheduled Maintenance?
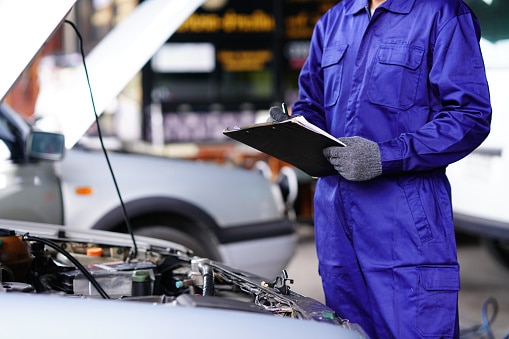
Discover What Scheduled Maintenance is, its types, industries and applications, how to calculate it, and their benefits for organizations and businesses.
Scheduled maintenance refers to any maintenance task assigned to technicians on a regular schedule. This could be reoccurring or a one time task. Scheduled maintenance usually occurs regardless of if the asset is in need of repairs. This is because part of the point of a maintenance schedule is to reduce the amount of repairs and equipment downtime needed.
Scheduled maintenance tasks optimize the amount of time your team spends keeping your equipment running. This lets you allocate your resources more effectively and helps prevent productivity-killing equipment failures.
Types of Scheduled Maintenance
Preventive Maintenance
Preventive maintenance is a type of scheduled maintenance that involves regular inspections regardless of the equipment’s condition. The goal is to proactively prevent equipment failure and unplanned downtime so your team can continue their regular workdays uninterrupted. Inspections follow a predetermined preventative maintenance plan based on your facility’s needs and processes.
Predictive Maintenance
Predictive maintenance is a data-driven approach that involves real-time monitoring and analysis of each asset’s condition. This is done using IoT (internet-of-thing) sensors attached to each piece of equipment. From there, the sensors deliver data to maintenance managers allowing them to plan maintenance tasks in the most efficient way based on which assets will need it most.
Planned Maintenance
Planned maintenance is a strategy that involves scheduling maintenance work in advance based on either regular intervals or other criteria. Examples of other criteria include operator feedback, usage, age, or environmental conditions. Most managers use a combination of both regularly scheduled maintenance and other criteria to determine their planned maintenance schedule.
Corrective Maintenance
Corrective maintenance is what most people have in mind when they think of repairs. It’s a reactive maintenance approach that is done with the goal of correcting an equipment failure or breakdown. While it’s important to schedule tasks to prevent this situation, corrective maintenance often gets priority when it’s required This is especially true if the breakdown hinders your company’s operations.
Condition-Based Maintenance
Condition-based maintenance is when a manager decides to schedule maintenance based on the equipment’s current condition. This is often planned via data-driven predictive maintenance tools. While this is similar to predictive maintenance, it differs in that the necessary work is done the moment the poor condition is detected instead of predicting when deterioration will occur.
Time-Based Maintenance
Time-based maintenance refers to conducting routine maintenance tasks on a predefined schedule. This is done regardless of condition to help ensure the ongoing effectiveness of all needed assets. Preventative maintenance is a form of time-based maintenance, but it is also used in other maintenance strategies. Risk-based maintenance is also typically done on a timed schedule.
Reliability-Centered Maintenance (RCM)
Reliability-Centered Maintenance (RCM) focuses on optimizing maintenance efforts by focusing on the most critical assets for operations, how they could fail, and the most cost-effective ways to prevent or correct these failings. This ensures consistent, optimal operations while also ensuring maximum return on investment on your maintenance costs.
Common Industries and Applications
Manufacturing
Scheduled maintenance is a common practice in most manufacturing plants. This is to help ensure that products are continuously produced with little to no interruption. For instance, a machine’s conveyor belt should be regularly assessed to ensure it keeps running as expected to complete each work order.
Transportation
Scheduled maintenance on vehicles has a lot of benefits for the transportation industry. Vehicles that are rarely in need of repair and more likely to complete more work orders. Additionally, scheduled maintenance can improve vehicle uptime by as much as 25%, which can lead to cost savings of about $2,000 per vehicle per year.
IT and Technologies
Scheduled maintenance for IT systems typically involves both hardware and software. It may include regular virus scans, software updates, or server inspections. This not only ensures that these tools remain operational, it’s also an important part of reducing potential cybersecurity vulnerabilities.
Construction
In construction, scheduled maintenance tasks generally involve keeping heavy machinery functioning correctly. This is both to support higher productivity and to protect worker safety. Malfunctioning construction equipment presents more safety risks, so it’s critical to proactively catch issues in an efficient manner.
Healthcare
Medical devices are the most obvious assets that are in critical need of proactive scheduled maintenance. However, healthcare facilities have also HVAC systems, lighting, and water heaters to keep in optimal condition. These assets play a bigger role in healthcare than one might assume. For instance, a well-maintained HVAC system will improve airflow and lessen the risk of airborne pathogens.
Energy
Maintenance schedules in the energy sector help prevent power outages. In this sense, maintenance planning is important to a lot of people in and out of your business. Most people are reliant on consistent electricity, gas, and water supplies to live comfortably.
How is Scheduled Maintenance Calculated?
In most cases, time-based scheduled maintenance is done based on manufacturer guidelines or compliance requirements. However, unexpected events can delay a scheduled maintenance task. Facility managers can also use the scheduled maintenance critical percent (SCMP) to determine which overdue tasks are most critical.
SMCP (Scheduled Maintenance Critical Percent)
Calculating SMCP is based on how late the task is and how frequently it should be performed. Higher percentage results indicate higher priority tasks.
Here is the formula you can use to calculate SMCP.
SMCP (%) = (Actual Scheduled Maintenance / Total Planned Scheduled Maintenance) x 100
Using this formula accounts for the fact that later tasks are not necessarily the highest priority. For example, a task that’s a couple of days late that should be performed monthly may take priority over a task that’s a week late if it’s only done once every two years.
Scheduled Maintenance Process
An important consideration when you create a new schedule for your maintenance team is that every task will go through three phases. This is also sometimes referred to as the PM cycle (preventative maintenance cycle). Be sure to allocate enough time in your maintenance schedule for your workers to complete all phases effectively.
Preparatory Phase
The process begins with an assessment of the equipment or systems that require maintenance. This may include their current condition, importance to business operations, and deciding what maintenance tasks will be required.
Execution Phase
This phase is when the maintenance team performs their given task. It may involve inspecting, cleaning, lubricating, calibrating, repairing, replacing components, or other services as required.
Post-Maintenance Phase
After all completed tasks, the asset undergoes additional testing to ensure all potential problems have been addressed. At this point, it will also undergo testing to verify that the asset operates as expected.
Benefits of Scheduled Maintenance
Improved Reliability
Regularly inspecting and maintaining assets increases their reliability. A well-maintained asset is much less likely to breakdown during operating hours. Keeping an objective preventative maintenance checklist on hand will also help you ensure that maintenance scheduling supports this goal.
Reduced Downtime
Scheduled maintenance will come with some planned downtime. However, predictable, routine downtime for maintenance will prevent unexpected downtime from occuring while the asset is needed. Specifying planned shutdowns on your maintenance schedule will help workers avoid using this asset during this time and plan needed tasks around it.
Cost Savings
Regular maintenance can decrease an asset’s overall total-cost-of-ownership (TCO) in facilities management. This is because preventing major breakdowns helps you avoid the high costs associated with emergency repairs or equipment replacements.
Extended Equipment Lifespan
Well-maintained equipment simply lasts longer. This gives you more use out of every asset, reduces replacement costs, and improves each asset’s resale value after depreciation.
Choosing the Right Scheduled Maintenance with ServiceChannel
Scheduled maintenance takes work, but it’s worth it. However, you can make your maintenance process much more efficient with your available resources. A preventive maintenance CMMS can help you get there.
That’s where ServiceChannel comes into play. Our CMMS and software tools make maintenance scheduling simple while revealing exactly how you can reduce risks and reduce costs.
Book a demo today and let our team show you how we can help!