The Complete Guide to Planned Maintenance
Facilities managers must always look ahead. Being proactive rather than reactive, combined with asset management, is the key to getting and staying ahead. That’s where planned maintenance programs come into play. Anticipating your asset’s needs before they break down is exactly how to ensure optimal productivity and operational efficiency at all times.
What is Planned Maintenance?
Planned maintenance is a part of a proactive maintenance strategy. It involves scheduled maintenance tasks that are performed regardless of an asset’s condition. Each maintenance task is chosen based on historical trends that determine where equipment downtime is at the highest risk. Proactive maintenance focused on these areas drastically reduces your risk of unexpected equipment failures.
Why is Planned Maintenance Important?
Without planned maintenance, you run the risk of unplanned downtime. Unplanned downtime risks lost customers, thousands of dollars in overtime for employees, or a prolonged halt in production. Prolonged unplanned maintenance also takes up your maintenance team’s time, which could be a problem if other maintenance tasks are required.
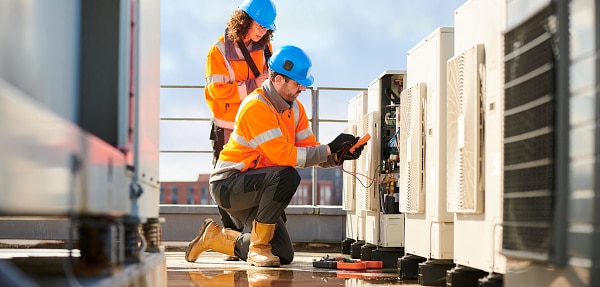
Planned Maintenance vs. Reactive Maintenance
Planned and preventive maintenance both prevent reactive or corrective maintenance. Reactive maintenance activities involve correcting an asset flaw or malfunction so it returns to its functional state. Most facilities managers will need to deal with reactive maintenance at some point. However, implementing a strong planned maintenance program will minimize reactive occurrences. That’s because planned maintenance aims to fine-tune assets before they break down to keep them in optimal condition.
Types of Planned Maintenance Strategies
Preventive Maintenance (PM)
Preventive maintenance (PM) is the process of performing regular maintenance tasks to lessen the risk of equipment breakdowns. This maintenance approach supports business continuity and may be vital to workplace safety depending on the asset. Implement a preventive maintenance strategy if any of your assets are critical and may have significant consequences if they fail (e.g. medical equipment.)
Good preventive maintenance management is required to ensure your facility reaps these benefits. A poorly planned regular preventive maintenance schedule may not catch issues in time.
Predictive Maintenance (PdM)
Predictive maintenance (PdM) involves using sensors or other data collection methods to predict when an asset is near failure. This approach helps you efficiently allocate resources to the assets that need it the most. Therefore, it’s ideal for facilities with critical equipment but small maintenance teams and limited resources.
Condition-Based Maintenance (CBM)
Condition-based maintenance (CBM) is similar to predictive maintenance in the sense that it allocates maintenance tasks based on an asset’s condition. The difference is that PdM predicts future deterioration and prompts maintenance tasks based on this schedule. CBM is performed the moment the deteriorated condition is detected.
CBM is particularly helpful for complex machinery. Complex machinery often has multiple potential failure points that may be difficult to track individually. CBM is based on a comprehensive view of the equipment’s overall health, which can simplify maintenance planning tasks.
Reliability-Centered Maintenance (RCM)
Reliability-centered maintenance (RCM) involves applying a separate, tailored maintenance plan to each individual asset in a facility to maintain productivity efficiently and cost effectively. RCM is a higher-level maintenance strategy that usually involves predictive and preventive maintenance plans. It’s used whenever there are high consequences for equipment failure, such as in airports and power plants.
Total Productive Maintenance (TPM)
Total productive maintenance (TPM) is a method that involves using machines, staff, and processes to keep and enhance production quality and system integrity. In other words, it involves weaving your maintenance strategy into your overall business strategy.
TPM is ideal for manufacturing plants where machine breakdowns can significantly disrupt operations. Training all workers to help with regular maintenance as part of their daily workflows ensures smooth and quality production.
Run-to-Failure (RTF) Maintenance
Run-to-failure maintenance (RTF) is when a facility maintenance team intentionally waits for equipment failure before performing maintenance tasks. This approach should be reserved for low-stakes, low-cost assets that are easy to fix in a short amount of time. An example may be waiting for a bathroom sink to stop running before inspecting its piping.
Risk-Based Maintenance (RBM)
Risk-based maintenance (RBM) involves scheduling maintenance tasks in a way that prioritizes higher-stakes assets. For example, a hospital may prioritize routine maintenance of life-support machines over HVAC systems. This approach is ideal for facilities with a high volume of assets to manage.
When to Use Planned Maintenance
Retail
In retail, HVAC systems, lighting, flooring, cleaning, and other systems are crucial to keeping the customers flowing. Having a rotating schedule in place that addresses all these variables to prevent a disruption in operations is ideal.
Restaurants
Restaurants have a lot of standard operating equipment, such as HVAC systems, grease filters, ovens, refrigerators, and more. There is a lot to keep up with, so cover all bases with a routine maintenance schedule. If an oven breaks down in the middle of the dinner rush hour, orders can’t be filled.
Grocery Stores
Facilities managers at grocery stores deal with a lot of moving parts. Without a planned maintenance system, maintenance activities can fall through the cracks, resulting in breakdowns at inopportune moments. For example, if one of the refrigerators stops working and the food goes out of temp, you now have product loss and reduced inventory.
Facilities
At a minimum, planned maintenance in a facility should include filters based on the type of equipment being used. In fact, almost every industry has maintenance tasks that need addressing. This includes filters for water, paint, air, and grease. The equipment may also have belts that need to be checked for wear and tear.
Compressors, instrument calibration, light fixtures, and pest control will also be on the list. HVAC maintenance is also vital. Regularly clean and check the air and heating unit to make sure it is operating as it should, and air flow is not compromised.
The 8 Steps of Planned Maintenance
It’s easy to get started with your planned maintenance strategy with a simple 8-step process. For additional reading, check out our comprehensive planned maintenance guide.
1. Identify Your Problem and Create a Work Order
The first step to a successful planned maintenance program is to identify the problems your program needs to solve. Gather precise information about each asset and its potential problem details, such as how it could fail and what the consequences of failure may be. This will help you create your work order and decide if this should be a one-time work order or occur on a repeating schedule.
2. Inspect the Facility Worksite and Related Assets
Once the work order has been created, the next step is to inspect the asset and the worksite where the maintenance work will take place. Document the scope of work to be completed, any parts or materials that are required, and the tools the technician will need. At this time, check the worksite for any obstacles that could affect how work is conducted.
3. Create a Maintenance Schedule
Once you’ve planned for your maintenance task, begin scheduling the work to be completed. Determine who will complete the work and when, based on the priority level you assign the task.
4. Assign Tasks and Priority Levels
Once the work has been outlined, it needs to be prioritized. Prioritization can be as simple as low, medium, high, or even a numeric scaling system such as 1-5. When assigning priority, consider the importance of the equipment, the resources available, and the risk of delaying completion.
5. Document Processes and Order Any Necessary Parts
Before the maintenance begins, document the processes and procedures that will be required to successfully complete the work. This includes shutdown procedures, access requirements, and safety procedures. At this time, order any parts necessary to complete the work.
6. Implement Maintenance Procedures
The next step is to perform your required maintenance activities. Important maintenance procedures include:
- Standard Operating Procedures (SOPs): Complete planned maintenance tasks based on your step-by-step process descriptions to ensure you adhere to industry regulations and laws.
- Safety Protocols: Safety precautions should always be involved in your planned maintenance workflow. Failing equipment can present safety hazards. Identify and mitigate them proactively during your planned maintenance process.
- Equipment Inspection: Inspecting equipment is the first step to maintaining equipment. Every maintenance plan must include regular inspections to check for small signs of upcoming failures.
- Testing: Test your asset after you’ve performed your maintenance task but before you complete your planned maintenance routine. This additional step ensures your planned preventive maintenance work accomplishes what you intended it to.
7. Integrate Tools and Automation
Technology can be an asset to your planned maintenance strategy. Here is a brief overview of the components needed to begin incorporating technology into your strategy:
IoT Devices
These devices are usually GPS-chip sensors to track movements and the overall health of the asset. IoT sensors can then send this data to a centralized cloud that facilities managers can read and use to support predictive or condition-based maintenance strategies.
Asset Tracking Software
Asset tracking software is a centralized system that allows your facility to track real-time details about each asset. As a result, it’s an excellent tool for any condition-based maintenance efforts.
Training
Learning a new technology can be challenging. Each person on the team using the technology must be fully trained to understand and troubleshoot at a moment’s notice.
Fine-Tuning
Time is money, but there must be dedicated individuals overseeing the implementation to work out the kinks and ensure the processes are working.
The initial costs of planned maintenance don’t have to be expensive to still reap the benefits. In fact, you can start your strategy with a low lift and still reduce your average repair and maintenance spending by up to 22%.
8. Risk Management and Contingency Planning
Risk Management is important to any operation, planned maintenance is no different. The contingency planning process is part of risk management. Your contingency plan is your plan of action to address risks in your planned maintenance process and their impact if they occur. For example, have a plan in place to address what your maintenance technicians need to do if their work causes an unexpected difference in how the asset functions.
Benefits of Planned Maintenance
Unplanned outages or mechanical breakdowns in the middle of important processes cause reactionary shifts in staffing, costs, and more. Planned maintenance helps ensure your equipment is operating efficiently and optimally while also allowing you to get the most out of your asset’s life cycle.
While maintenance tasks within a planned maintenance setting will look different for every organization, facilities managers who employ a planned maintenance mindset usually have better productivity, reduced costs, and can even boost employee morale.
Here are a few more benefits of planned maintenance.
Reduce Repair Costs
Planned maintenance makes it easier to plan for major repairs and upgrades before they are needed. As a result, facilities managers have time to properly budget for the upcoming maintenance costs. It also gives facilities managers time to source the parts they need for repairs at the best price.
Reduce Time Spent on Maintenance
Planned maintenance helps facility managers pinpoint small problems that require easy repairs before they become large costly ones. Technicians can identify when equipment may be on the verge of failing, providing ample time to replace or recalibrate it before it breaks down.
Reduce Asset Downtime
Equipment must be properly cared for and maintained, or it may break down and fail resulting in increased downtime. Downtimes could last hours, days, or even weeks resulting in unplanned equipment costs, problems finding parts, loss of productivity, and increased labor costs.
With planned maintenance, these problems are resolved before they become an issue. A planned maintenance program gathers data to determine when equipment is due to be serviced or replaced, makes sure parts are available and ready, and the technician is scheduled.
Optimize Your Production Line
Equipment that has been routinely serviced and is in good working order is less likely to break down in the middle of a production day. A breakdown in the middle of the day has a snowball effect on the rest of the organization. Employees may have to wait for the equipment to be fixed and potentially work overtime to get the job done.
The Impact of a Strong Planned Maintenance System
While it can take time to create successful planned maintenance schedules (PMS) and implement them, it is important for facilities managers to consider the positive impact a planned maintenance structure has on the organization.
Having a reduction in asset downtime, maintenance, and repair costs increases efficiency and productivity leading to a strong ROI while improving the culture and safety of your employees.
If your facilities need help creating and managing your planned maintenance program, ServiceChannel is here. Discover how with our powerful preventive maintenance software.
Contact us today.