What is Equipment Downtime?
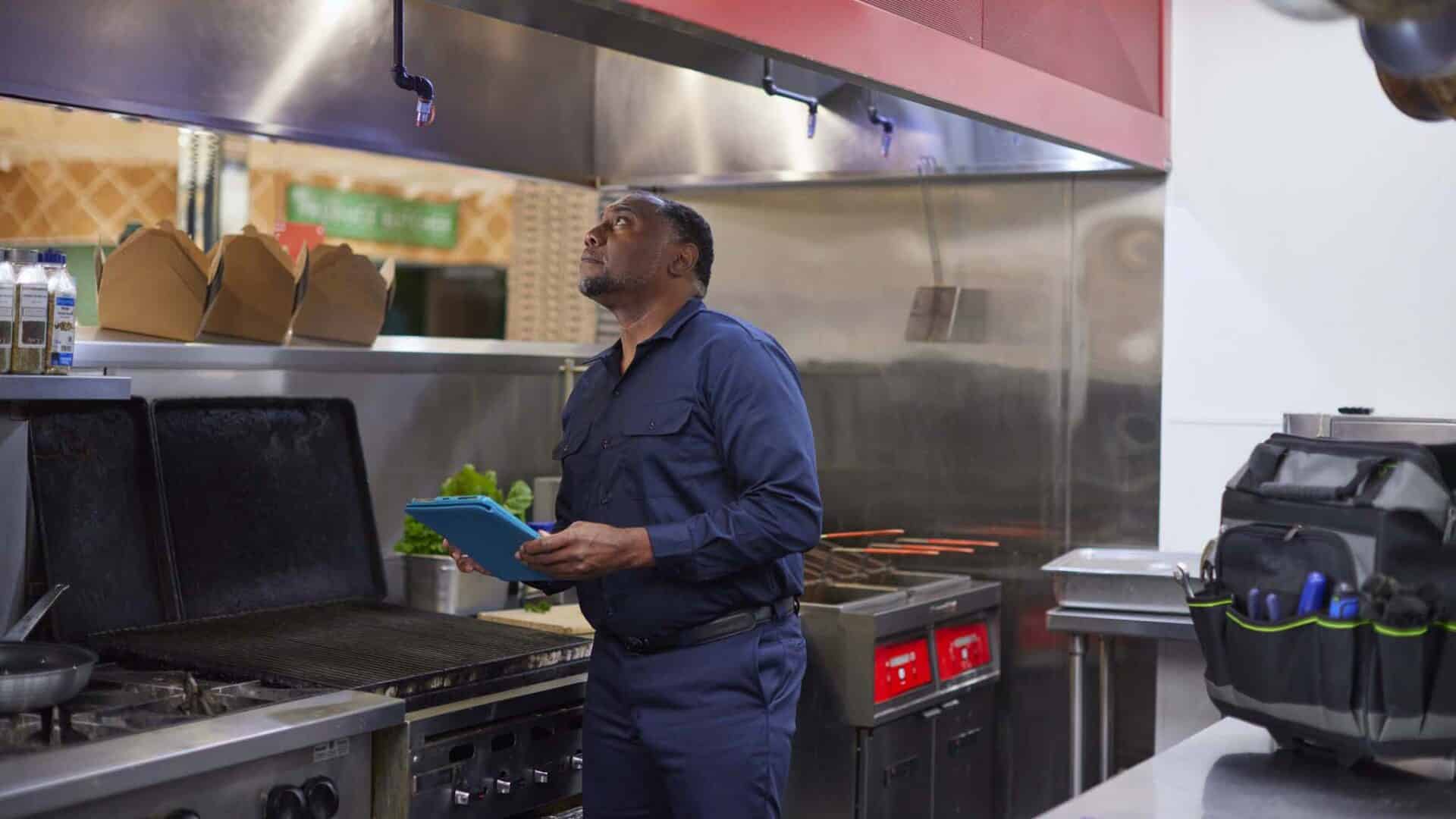
Learn about Equipment Downtime, its causes, impact, prevention, and best practices when implementing it. Discover how ServiceChannel helps manage downtime.
Equipment downtime refers to any expected or unexpected downtime that impedes a piece of equipment’s ability to perform its intended task. Planned downtime typically occurs alongside routine maintenance and doesn’t impede productivity. On the other hand, unplanned downtime events usually cause lost productivity and lost revenue.
It’s important to include planned downtime in your overall maintenance strategy. Doing so ensures that your preventive maintenance tasks cause minimal interruptions to your team’s work. For instance, scheduling maintenance downtime events outside working hours.
Integrating preventive maintenance software into your workflow is an effective way to ensure accurate implementation. However, you will still need a good understanding of equipment downtime to maximize your software’s capabilities.
Understanding Equipment Downtime
For most facilities, the goal is always to reduce equipment downtime. Maintenance managers who strategically schedule planned downtime must also do what they can to minimize downtime hours so workers can use the asset again as soon as possible. Both goals require an understanding of equipment downtime causes and effects.
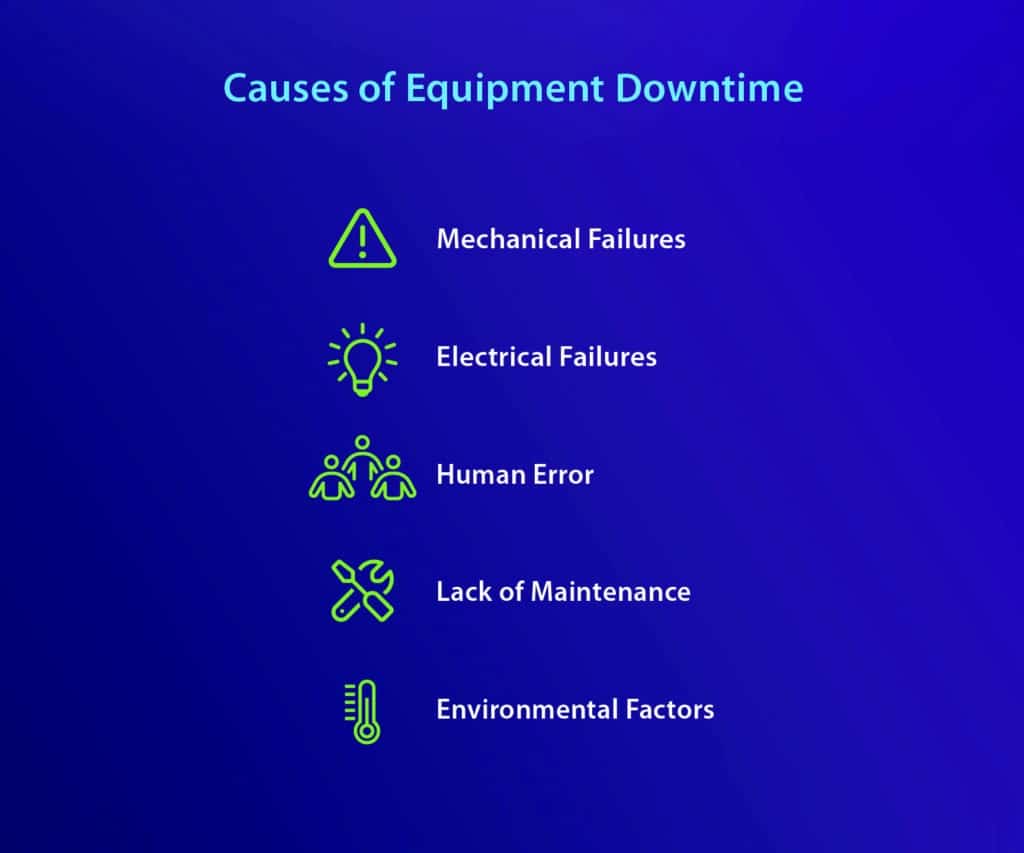
Causes of Equipment Downtime
Machine downtime could be caused by almost anything. So, to reduce downtime, you need to thoroughly analyze what is most likely to cause unscheduled downtime at your facility.
Factors such as your industry, occupant density, and location may affect your results. For example, what is more likely to cause downtime in a rural healthcare facility differs from an urban manufacturing plant. Regardless, there are a few common causes that apply to most facilities.
- Mechanical failures: Often stem from wear and tear or the breakdown of specific components such as gears and bearings and can lead to unplanned asset downtime.
- Electrical failures: Usually occur due to issues like circuit overloads, short circuits, or the failure of electrical components like switches, fuses, and wiring, leading to unexpected equipment downtime.
- Human error: Misuse, accidents, misinterpretation of instructions, or failure to follow standard operating procedures can all cause unplanned equipment downtime.
- Lack of maintenance: Without regularly scheduled equipment maintenance, the gradual breakdown of equipment will occur much faster, leading to more unexpected downtime.
- Environmental factors: Temperature, humidity, and other external conditions can accelerate material degradation. Additionally, natural events such as floods, storms, and fires can cause rapid equipment failures and unplanned downtime.
Impact of Equipment Downtime
Unplanned or poorly planned maintenance downtime can negatively affect your facility, team, and potentially your customers, depending on the equipment failure, leading to the following impacts:
Increased Repair Costs
How much downtime you experience will inevitably increase your reactive maintenance costs. While this statement is true regardless of whether or not the downtime was planned, unplanned downtime will significantly drive up costs. The reason for this difference is that mainly experiencing planned downtime allows for better budget management that keeps costs under control.
Reduced Productivity
Unexpected failures can happen anytime, whereas scheduled maintenance downtime is strategically planned to occur during off hours. As such, an unexpected breakdown during a busy workday will drastically reduce productivity. For instance, workers cannot complete a manufacturing process if their production line equipment is out of order.
Reputational Damage
Customer-facing assets that consistently fail unexpectedly will give your facility a bad reputation. No one wants to eat at a restaurant with frequent refrigeration issues or shop at a store that constantly has a broken POS machine, for example.
Negative Customer Experiences
Even if the asset is not customer-facing, lost production means lost revenue. Workers who can’t perform their jobs due to malfunctioning equipment also cannot deliver to customers in a timely fashion. Some asset failures may also trickle down your entire production line, affecting multiple deliverables in multiple areas.
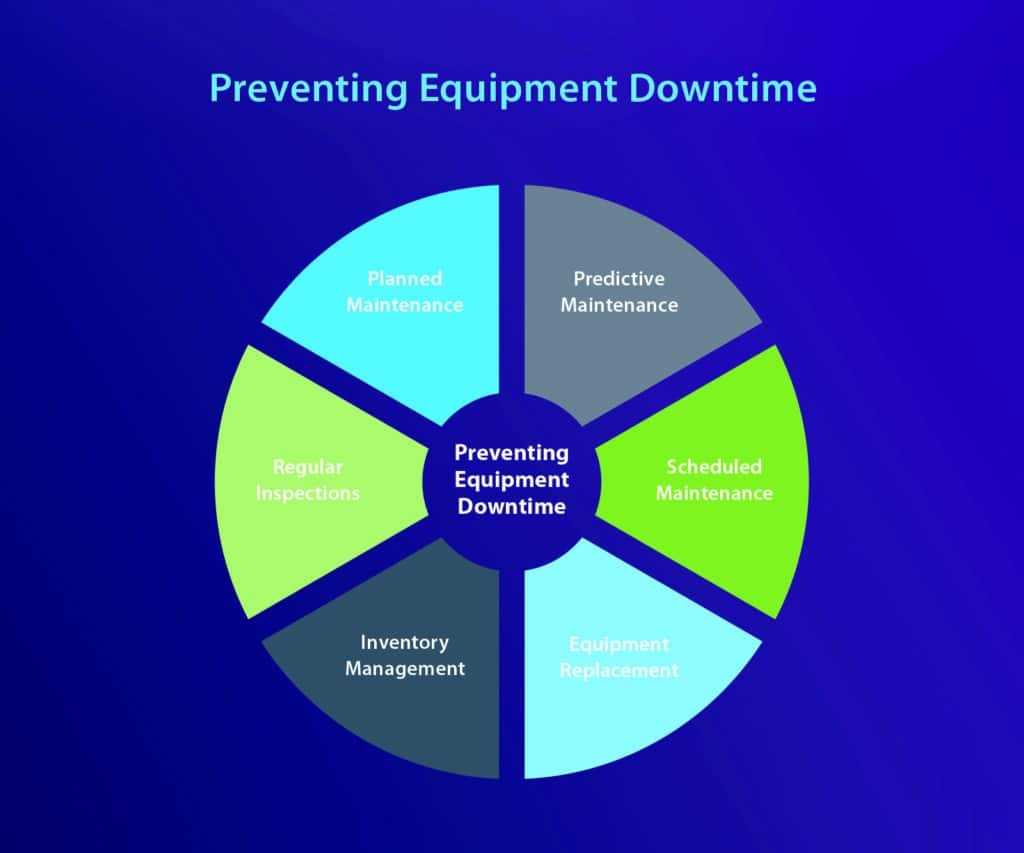
Preventing Equipment Downtime
Preventing equipment downtime is critical to maintaining the operational efficiency and reliability of equipment and machinery. While you’ll never eliminate downtime, you can calculate equipment downtime to reduce it to a reasonable level with minimal impact on your operations. Here are some preventive maintenance tips to help you reduce your downtime hours.
Planned Maintenance
Planned maintenance is assigning routine maintenance tasks to technicians on a regular schedule. The goal of planned maintenance is to prevent future equipment failures. It could be on a recurring schedule or a one-time basis, depending on the nature of the maintenance task. This practice helps you streamline maintenance operations and catch potential issues before they cause downtime.
Predictive Maintenance
Predictive maintenance relies on data and technology to anticipate when equipment might fail. It uses condition monitoring, sensors, and data analysis to predict maintenance needs. You can use this system to efficiently allocate resources to the assets that need it most when they need it most.
Regular Inspections
Regular inspections involve systematically assessing equipment’s condition looking for signs of wear, damage, or potential issues. Whether or not you have a planned preventive maintenance schedule, regular inspections are crucial for your critical assets. Performing them will drastically reduce machine downtime and can have a dramatic positive effect on equipment efficiency.
Scheduled Maintenance
Scheduled maintenance involves planning maintenance activities well in advance, often based on manufacturers’ recommendations or industry best practices. You may also plan based on seasonal conditions, such as preparing outdoor equipment for the winter. Following a maintenance schedule, regardless of the asset’s current condition, will reduce the downtime cost and increase the asset’s value upon depreciation.
Inventory Management
Inventory management is the practice of maintaining an adequate stock of spare parts and components needed for equipment maintenance and repairs. Of course, you can only perform the required tasks if you have the tools. However, it’s important not to overstock either, as doing so can waste money and space. Electronically tracking parts and inventory is an easy way to gain transparency into your stock levels.
Equipment Replacement
Equipment replacement involves retiring old or obsolete equipment and replacing it with newer models. The general best practice is to determine replacement time by comparing the cost of replacement to the cost of maintenance or repair. If keeping the asset in working condition costs more than replacing it, replace it.
Best Practices for Managing Equipment Downtime
Track Downtime
Record all instances of unplanned machine downtime and calculate how much they cost, including intangibles. Tracking downtime provides valuable insights into an asset’s performance. Accurately tracking the cost of downtime can also give you an idea of how severe typical failures may be.
Compare both factors to gain a more accurate picture of equipment performance. If a particular asset experiences frequent or unusually costly downtime, that may warrant investigation. If you track equipment downtime this way, it may reveal that the asset is no longer functional or has not been adequately maintained.
Perform a Risk Audit
Determine and record downtime reasons after every incident. This information helps you predict when and how future equipment failures may occur. You can also use this downtime data to tailor your maintenance plan to your facility’s specific needs. As a result, you can reap more preventive maintenance benefits.
Preventive Maintenance Plan
A good preventative maintenance plan will both reduce costs and increase efficiency. Proactively order spare parts and perform regular maintenance during intentionally planned downtime. These proactive measures will help reduce downtime and the actual time it takes to perform future corrective maintenance tasks if needed.
Prioritize Critical Equipment
Identify critical equipment by pinpointing which assets significantly impact production, service delivery, property integrity, or health and safety. Consider the possible consequences that may occur if any system fails. Once determined, critical equipment must always take priority during both proactive and reactive maintenance tasks.
Root Cause Analysis
When failures occur, conduct a thorough root cause analysis to determine the underlying reasons. Tracking equipment downtime causes is part of your audit process. However, performing a root cause analysis at this time may reveal that the reason is not what was determined at first glance.
For instance, you might first assume that a conveyor belt stopped working because of an electrical issue, but a root cause analysis could reveal that a jammed roller was the problem.
Managing Equipment Downtime With ServiceChannel
Manual tracking is tedious, but many use the process as a critical aspect of reducing downtime. Automated tracking and a planned maintenance guide will simplify asset management and help you maximize equipment utilization.
If you’re looking for a user-friendly and efficient way to do that, consider ServiceChannel’s platform. Our software is designed to reduce downtime by giving you real-time data-driven insights into equipment performance and your asset management practices.
Advance your production process by enhancing your equipment management. Book a free demo today.