10 Effective Ways to Utilize Spares Inventory Management Software for Multi-Location Facilities
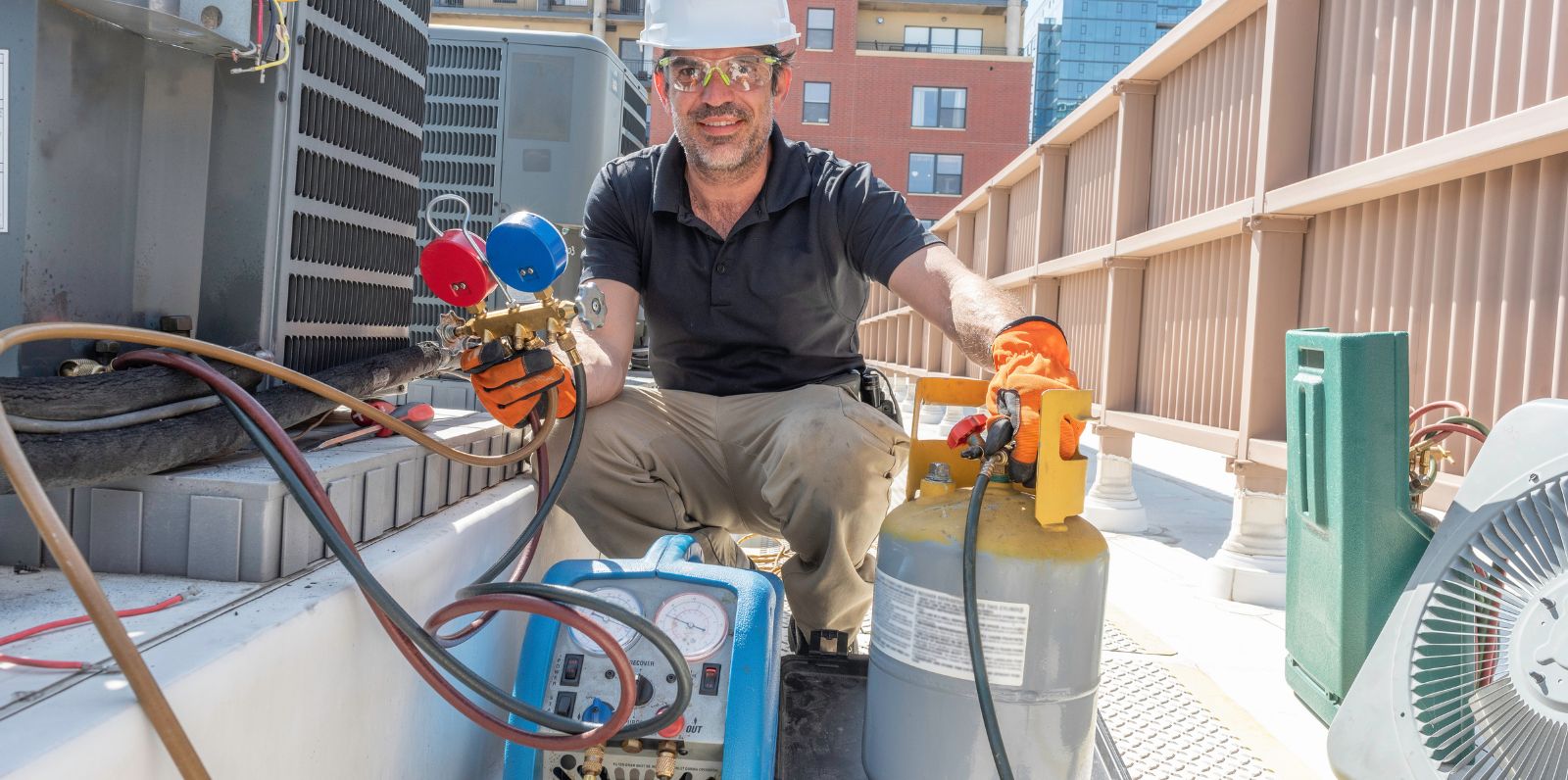
Manage parts smarter across sites. Discover how spare parts inventory software reduces downtime, cuts costs, and brings clarity to your maintenance strategy.
When managing facility operations across multiple locations, inventory issues can quickly get out of hand. Missing parts at the wrong time can derail repair timelines, drive up costs, and leave teams scrambling. Spares inventory management software helps avoid these pitfalls.
The right system centralizes data, streamlines procurement, and keeps parts moving on time. Whatever your operation’s size, spares inventory management software brings visibility and control to your spare parts strategy.
Let’s examine 10 practical ways your team can use spare parts management software to improve efficiency, enhance cost tracking, and speed up repairs across facilities.
1. Centralize Your Spare Parts Data
When inventory data lives in disconnected spreadsheets or siloed systems, it’s easy to lose track of what you have, where it is, or whether it’s been used. A central hub eliminates guesswork, whether you’re tracking spare parts across multiple facilities, storage centers, or vehicles. With all your inventory data in one place, it’s easier to maintain accuracy, reduce duplicate orders, and see exactly what’s available at a glance.
Facilities management solutions like ServiceChannel provide a single dashboard for managing inventory across locations, whether on a service vehicle or sitting in a back room at a remote site. Without centralized visibility, teams often over-order, misplace parts, or assume supplies are available when they aren’t. Visibility like this gives you control over repair processes and reduces unplanned downtime.
A unified platform lets you see what’s in stock, what’s in transit, and what needs reordering in real time.
2. Embrace Real-Time Tracking for Faster Repairs
When a critical system goes down, every minute counts. Real-time tracking helps technicians find the nearest available part quickly. There are no panicked phone calls or digging through shelves. With a spare parts inventory management solution, your techs can check part availability and location instantly, whether they’re on-site or en route.
An app builder for service and inventory management, like the ServiceChannel Provider mobile app, lets your team scan, search, and locate nearby parts in seconds. The results are faster fixes, fewer delays, and better alignment with your preventive and reactive maintenance strategies.
This helps speed up repairs and prevents parts from sitting unused in one location while urgently needed in another.
3. Use Bulk Buying for Procurement Efficiency
When you’re managing supplies across multiple locations, it’s tempting to order parts on an as-needed basis. But that can lead to inconsistent stock levels, rushed deliveries, and inflated emergency costs.
A smarter move is to use spare parts inventory software to track usage patterns and consolidate purchasing. Buying parts in bulk across all locations helps lock in better pricing, reduces redundant orders, and prevents last-minute scrambles when something breaks. You can also take advantage of vendor discounts, negotiate better terms, and plan procurement cycles that align with your seasonal maintenance needs.
Take a look at where the savings add up. ServiceChannel makes it easy to pull insightful FM reports that highlight high-use inventory items and flag opportunities for more cost-effective procurement.
4. Integrate Inventory Management with Work Order Systems
Repairs tend to hit more snags when inventory and work order systems operate separately. Perhaps the part isn’t where it should be, or no one knows if it’s in stock at all. Syncing your parts inventory system with your work order management system bridges that gap and helps keep repairs going smoothly.
Work order management systems also simplify tracking usage history, so you can tie part consumption to specific repair trends, assets, or technician requests. With everything connected, technicians can confirm part availability while creating a work order, and managers can avoid delays caused by out-of-stock components. It’s a simple step that leads to faster fixes, clearer communication, and more efficient maintenance workflows across all your teams, wherever they are.
5. Automate Low-Stock Alerts for Preventive Maintenance
One of the simplest ways to avoid repair delays is to know your supplies are running low before they run out. With a powerful spare parts management solution, you can set automated low-stock alerts that notify your team when it’s time to reorder. You can also configure low-stock alerts by location, helping you tailor restocking workflows for high-traffic sites or isolated service areas.
This kind of automation helps prevent stockouts, avoids delays, and keeps your preventive maintenance plans on schedule. Combined with strong asset management practices, automated alerts give your maintenance team the tools they need to stay ahead of parts demand and avoid conducting a search.
6. Adopt Mobile Accessibility for On-the-Go Technicians
When technicians are out in the field, every extra step back to a laptop or office slows them down. Time is precious, especially when teams are running on a tight schedule between locations. Mobile-friendly spare parts management software gives teams instant access to parts information, wherever the job takes them.
With a computerized maintenance management system (CMMS) that supports mobile access, your team can search part availability, update supply counts, and even scan barcodes using their phone or tablet. Reducing their need for steps out in the field saves time while also keeping inventory records accurate and up-to-date.
Giving your technicians mobile access reduces bottlenecks, shortens repair windows, and makes it easier to keep jobs moving, particularly when you’re managing maintenance work across several sites.
7. Streamline Data with Barcode Scanning
Manual inventory updates can be slow, prone to human error, and too easy to forget. Barcode scanning reduces those mistakes by letting your team scan items in or out as they use, stock, or move them. It will also help control costs associated with fixing inventory management errors.
When paired with a spare parts management system, barcode scanning tools make it easier to maintain accurate records and keep supply information up to date. Inventory accuracy like this is essential when planning repairs, tracking usage, or managing the full lifecycle of your equipment.
Barcode scanning also ties directly into better asset lifecycle management. With every scan, you’re doing more than just tracking parts. You’re building a reliable history of how your inventory supports equipment performance and long-term value.
8. Combine Inventory and Preventive Maintenance Scheduling
When preventive maintenance is scheduled without checking part availability, even the best-laid plans can fall short. Delays happen, repairs are postponed, and technicians lose valuable time waiting for critical supplies. That’s why coordinating inventory management and preventive maintenance scheduling makes all the difference.
Spare parts management systems that integrate with your maintenance scheduling tools help ensure that you have the necessary components before work begins. This synchronization between inventory planning and preventative maintenance keeps downtime low and improves operational efficiency.
Preventative maintenance works best when the parts you need are already on hand. With a facility management platform like ServiceChannel, your team can combine real-time maintenance data with supply availability to create smarter, better-timed maintenance schedules. This leads to faster repairs, fewer missed appointments, and a more reliable maintenance rhythm across locations.
Coordinating these workflows gives your team a clearer picture of what needs to be done, what’s in stock, and when it all needs to happen.
9. Gather Data Insights to Show ROI
A solid reporting system shows you more than just what’s in stock. It also shows how your inventory strategy impacts costs, efficiency, and long-term value. Spare parts management software with built-in analytics helps you track usage trends, flag cost-saving opportunities, and demonstrate real returns on your tech investment.
If you need to justify the cost of inventory tools, reporting dashboards can highlight measurable gains to show company officers. Reports can provide verifiable ROI information such as:
- Reduced downtime across sites
- Improved inventory accuracy
- Fewer emergency part orders
- Cost savings from better procurement strategies
With clearer visibility into what’s working, you can adjust purchasing strategies, identify underused stock, and build a more cost-effective maintenance operation that supports your team, your budget, and your long-term goals without sacrificing quality.
10. Scale Seamlessly Across Multiple Locations
Managing inventory across one facility presents enough challenges. If you spread that across five, ten, or fifty sites, the complexity multiplies quickly. Standardized inventory processes help overcome those challenges and reduce the effort across the board.
With a consistent spare parts management system in place, your team doesn’t have to reinvent the wheel for every location. Instead, you can build workflows and scale them with confidence, knowing each site follows the same playbook.
Here’s what the consistency of standardized processes can bring:
- Clear expectations on how to track and restock inventory
- Consistent data formats across locations
- Faster onboarding for new techs or managers
- Fewer surprises during audits or reporting cycles
- More predictable costs and usage patterns
Standardization is the key to growing your operation without introducing chaos. It provides structure while still allowing flexibility where it counts.
Take Control of Your Spare Parts Inventory
Using spare parts management software like ServiceChannel gives your team more than just better tracking. It helps reduce downtime, streamline workflows, and build a resilient operation with well-stocked facilities and fewer surprises.
With automatically updated inventory counts, accurate supplier data, and usage history at your fingertips, you’re equipped to make smarter, data-driven decisions that benefit your entire operation.
The benefits of a unified system become even clearer as you scale.
From faster repairs to lower inventory costs, every improvement adds up. Request a demo today to see how ServiceChannel supports multi-location synergy and start building a more connected, efficient inventory strategy.