7 Asset Lifecycle Management Best Practices
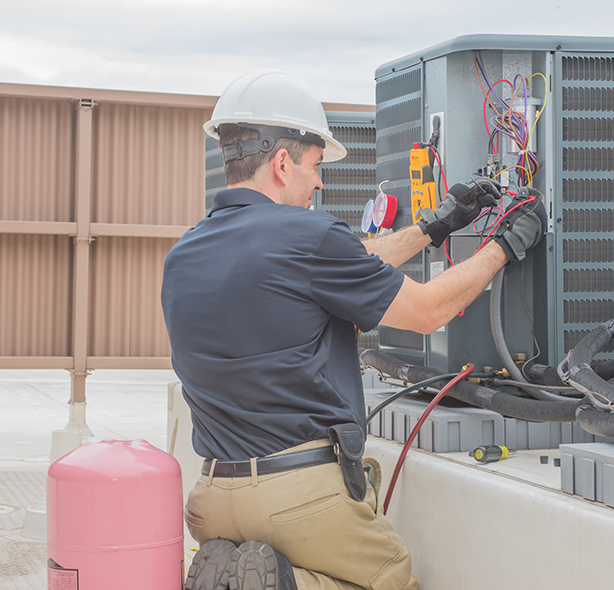
Discover the 7 Best Practices for Asset Lifecycle Management. Learn how to optimize performance, reduce costs, and improve resource allocation for your business.
Companies from many industries depend on an array of physical assets and equipment to keep their operations running smoothly. Whatever services or goods a company provides, optimum asset performance is a key component that helps increase productivity and reduce costs.
Best practices for asset lifecycle management enable a company to reduce waste, minimize unplanned downtime, and maintain customer satisfaction. A business can extend asset usability by implementing a maintenance strategy that incorporates an asset lifecycle plan.
What is Asset Lifecycle Management?
Asset lifecycle management (ALM) uses software systems to gather information and apply real-time analytics to track information technology (IT) and physical assets throughout their lifespan. Enterprise asset management systems monitor and analyze several data points to build mathematical models that anticipate future occurrences and recommend maintenance schedules.
Automated integrations and monitoring enable a maintenance team to take an informed, data-driven approach. Personnel can better prepare for preventive maintenance and repair needs before they arise.
Asset Lifecycle Stages
Asset lifecycle management (ALM) can improve asset performance, keeping your organization running at maximum operational efficiency. ALM follows five main stages of asset lifecycle management. These phases of an asset lifecycle are broken down into acquisition and planning, utilization, maintenance, and disposal.
Acquisition and Planning
During the first planning stage of an asset life cycle, the operations team typically identifies the need for a particular piece of equipment and aligns with management to obtain purchase approval. The purchasing department works with vendors to locate and secure the requisitioned new asset.
Installation and Commissioning
Proper installation ensures smooth equipment activation and reduces the need for emergency maintenance in the future. Equipment vendors often come to the site to assist maintenance technicians with the installation or install it themselves to ensure everything is done properly.
Operation and Maintenance
Asset monitoring and maintenance help ensure optimum asset performance. Scheduling preventive maintenance activities and monitoring assets, often according to vendor specifications, helps extend an asset’s lifespan significantly. Inspecting, lubricating, and replacing worn parts before they fail reduces unplanned downtime considerably.
Upgrades and Modifications
Continuous improvement maintains asset usability and relevance. Many vendor add-ons can expand the capabilities of existing assets and equipment. Engineering teams can often assess equipment and recommend in-house modifications that may reduce wear or improve asset functionality.
Decommissioning and Disposal
The final stage of the asset lifecycle takes some planning. You may need to seek out a replacement before going ahead with dismantling the asset. When an asset is decommissioned, all systems and utilities are disconnected. A disposal crew then disassembles and removes the asset. Depending on what’s being taken out, a company may need an environmental consultant to ensure clean asset disposal.
Best Practices for Asset Lifecycle Management
Asset longevity is a key objective of asset lifecycle management (ALM). The longer an asset’s lifespan, the more value a company gets for their investment. An asset management lifecycle plan uses best practices to guide organizations in maximizing each asset’s usability and long life, aligning with their asset management strategy.
I. Utilizing asset management software
An enterprise asset management (EAM) software solution centralizes tracking, asset data gathering, and analysis. A reliable IT asset management solution will process asset information, data breaches, maintenance histories, and downtime incidents. It will empower staff to make informed decisions regarding maintenance scheduling and purchases for spare parts and other items necessary for upkeep.
II. Integrating preventive maintenance
Preventive maintenance as part of an asset lifecycle management plan reduces the risk of equipment breakdowns, costing time and money. Preventative maintenance extends asset lifespan and improves operational reliability. Taking the time to perform maintenance tasks proactively ensures smooth asset operation and avoids unplanned downtime.
III. Reducing emergency repairs
A timely maintenance schedule minimizes costly emergency repairs. Companies that rely on reactive maintenance tend to experience more unexpected breakdowns and critical asset failures, costing time and money.
IV. Specifying asset roles in operations
Clearly define the role of each asset and how each asset is to be used. Specify necessary qualifications for operating and acceptable running parameters. Study user manuals and vendor reference resources to understand each asset’s capabilities and follow vendor guidelines when using critical assets.
V. Implementing asset tracking systems
Keeping tabs on all assets, large and small, is critical to avoid loss and waste. Smaller assets may benefit from RFID or barcodes for organization and storage. GPS tracking helps locate lost or stolen assets. Serial numbers simplify digital asset identification for software and databases.
VI. Reducing downtime and extending asset life
Proactively address issues before they arise. You’ll reduce maintenance costs and increase profitability through optimum production. With diligent asset planning and a robust software solution, your organization can significantly increase your assets’ lifespan.
VII. Budgeting for asset maintenance
Budget financial resources to ensure proper care of equipment and assets. Whatever funds your company puts toward equipment maintenance and repairs, return the investment through an extended asset lifecycle, increased productivity, and reduced downtime.
Benefits of Asset Lifecycle Management
Companies face several asset management challenges. Depreciating asset value and maintenance costs impact the financial side of asset ownership, while equipment age and wear can affect productivity. Asset lifecycle management provides numerous benefits to help overcome challenges and optimize the value for cost.
Cost-effective solution
Collecting and analyzing productivity and maintenance data enables companies to develop informed, data-driven repair and maintenance strategies. Identifying cost-effective maintenance solutions can reduce the total cost of ownership (TCO) of assets and equipment by reducing reactive maintenance and improving asset performance.
Optimize asset utilization
Optimal utilization ensures effective and efficient asset use. Operating equipment within manufacture-specified parameters minimizes wear and tear throughout an asset’s life cycle. Experienced, knowledgeable, and well-trained operators understand asset limits and know when an asset is operating at its maximum level.
Improve asset performance
Dependable and productive equipment simplifies managing assets, reduces costs, and increases profitability. Including upgrades and modifications in asset management processes can provide numerous benefits. Engineers can often expand equipment performance and broaden parameters for greater productivity. Vendor upgrades can also enhance the effectiveness of equipment.
Reactive to proactive maintenance
Moving the maintenance stage from reactive to proactive maintenance simplifies all other asset management processes. Reactive maintenance often involves unexpected breakdowns, resulting in longer downtimes while the maintenance team awaits parts delivery. By keeping critical components on hand and creating a preventative maintenance schedule, your company can minimize unplanned repairs and the resulting downtime.
Resource allocation
Implement strategic resource allocation measures into your asset life cycle management plan. Prioritize asset significance and allocate supplies, equipment, labor, and time to address critical asset requirements. Having what you need when you need it helps the maintenance team stick to their preventative maintenance schedule, ensuring that assets are optimally maintained and extending the useful life cycle of all assets.
Effective Asset Performance with ServiceChannel
Software integration can help guide an asset management plan by informing personnel of current asset needs and preparing your maintenance team for future requirements. Empower your team to move forward with the help of a robust enterprise asset management solution (EAM). Contact ServiceChannel today and see how we can meet your organization’s needs.