How to Overcome 7 Asset Management Challenges

For facilities managers who are often also responsible for the repair and maintenance of major assets, not having a modern asset tagging/management system only compounds the complexity of their day-to-day operations. Frankly, with all the headaches that FMs face even when things are going relatively smoothly, they need this added complexity like they need a site-wide power outage.
Key benefits of this integrated method include being able to make repair or replace decisions more quickly, as well as being able to use historic and real-time asset management data to improve operations continually.
Of course, moving to this integrated model assumes that a business is using modern asset tagging technologies in the first place. Selecting and implementing digital asset tagging is therefore the first and most important step of an overall effective asset management system.
Unfortunately, there are still many companies who are still managing their assets manually, including using outdated asset tracking methods such as pen-and-paper inventory trackers or paper labels – if assets are even being tracked at all! Let’s dive into the top seven challenges that FMs are likely to face.
Financial Impact of Asset Management Challenges
The financial implications of inadequate asset management software can be staggering. From unexpected breakdowns and premature replacements to inefficient maintenance schedules, the costs can rapidly escalate, draining your operational budget and hindering growth.
Missed warranty opportunities, inaccurate depreciation calculations, and lost productivity due to equipment downtime further strain your financial resources. These challenges can impact your bottom line, erode your competitive edge, and impede your organization’s overall success.
1. Little to No Visibility of Inventory
Without visibility, there is no sure way of determining the inventory of assets in a given location(s). With no previous record of assets and information, there is also no way to track important data such as an asset’s serial or model number for future support and service uses. This becomes even more problematic when smaller assets – like small appliances and tools – are moved among locations as they are routinely for various reasons. In short, there’s no way to be making smart asset-related decisions without knowing what you already have in place and where everything is.
2. Losing Potential Warranty Savings
If a business is not accurately tracking its assets at all, then it is highly likely that it is not tracking these assets’ warranty status or availability. This could cost the business real money in the form paying for unnecessary repairs. ServiceChannel research reveals that companies are losing up to 35% of potential warranty savings from paying for repair on under warranty equipment.
3.Lack of Information Sharing with No Asset Tagging
Asset tagging is essentially a data management strategy. Without modern asset tagging in place, it is difficult if not impossible to create a dynamic data profile of the key assets even at a basic level such as with repair and cost histories. This makes the FM and other users highly dependent on others such as contractors for repair and maintenance decisions, with no good way to hold these vendors accountable.
4. Repair or Replace Decisions Not Backed by Data
Determining whether an asset should be replaced or repaired is a common decision for FMs. Making the wrong decision can cost the business plenty either in paying too much or incurring the cost of equipment downtime. Without the right levels of data to analyze and to guide the FMs, these repair-or-replace decisions can end up being no better than a coin flip.
5. Asset Servicing Errors
Without having a method to easily and confidently identify a particular asset, there’s no way to be sure that the on-site staff is choosing the correct piece of equipment when creating a work order (e.g. which stove, HVAC unit or refrigerator unit). In the case of emergency or on-demand services, time is of the essence and costs can accelerate with the wrong decisions when the service provider is not certain which asset to fix or maintain when on-site. Even planned maintenance can be wasted or assets can be put at risk if routine services are performed on the incorrect asset.
6. Time Spent Managing Assets
The biggest problem with any operational complexity is the time required just to maintain the status quo. This is certainly the case for FMs who are trying to manage critical assets without good asset tagging tools. Ultimately, with all the responsibilities that an FM has, the time investment in managing assets manually may be the greatest cost.
7. Strategic Decision Making Without Clean Data
Spending on capital assets and equipment are a big portion of every budget with real business impact to a company’s bottom line. Major decisions such as investing in new capital equipment require comprehensive, accurate and clean asset data across a location portfolio to ensure that the business is acting intelligently and strategically. From new location build outs to future capital planning, it is critical for a business to know the asset inventory, its service history, and the cost-per-asset over its lifecycle. And there’s no way to do that without an accurate way to capture, maintain and track equipment company-wide.
Overcome Asset Management Challenges with Technology Today
The complexities of asset management tools can be mitigated with the right technology. In today’s digital landscape, a wealth of innovative solutions exists to streamline asset tracking, optimize maintenance operations, and unlock valuable data-driven insights.
Imagine a centralized system that provides real-time visibility into asset locations, conditions, and maintenance histories, empowering you to proactively schedule repairs, predict failures, and extend asset lifecycles. By leveraging the power of technology, you can transform asset lifecycle management from a reactive burden into a strategic advantage, driving efficiency, cost savings, and long-term growth for your organization.
Ready to learn more about asset management technology? Request a demo today!
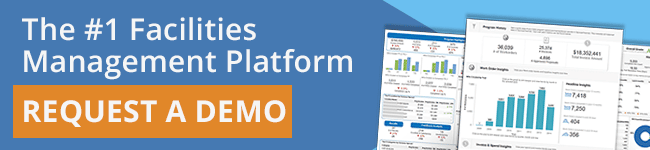