A Comprehensive Guide to RCM Maintenance for Facility Managers
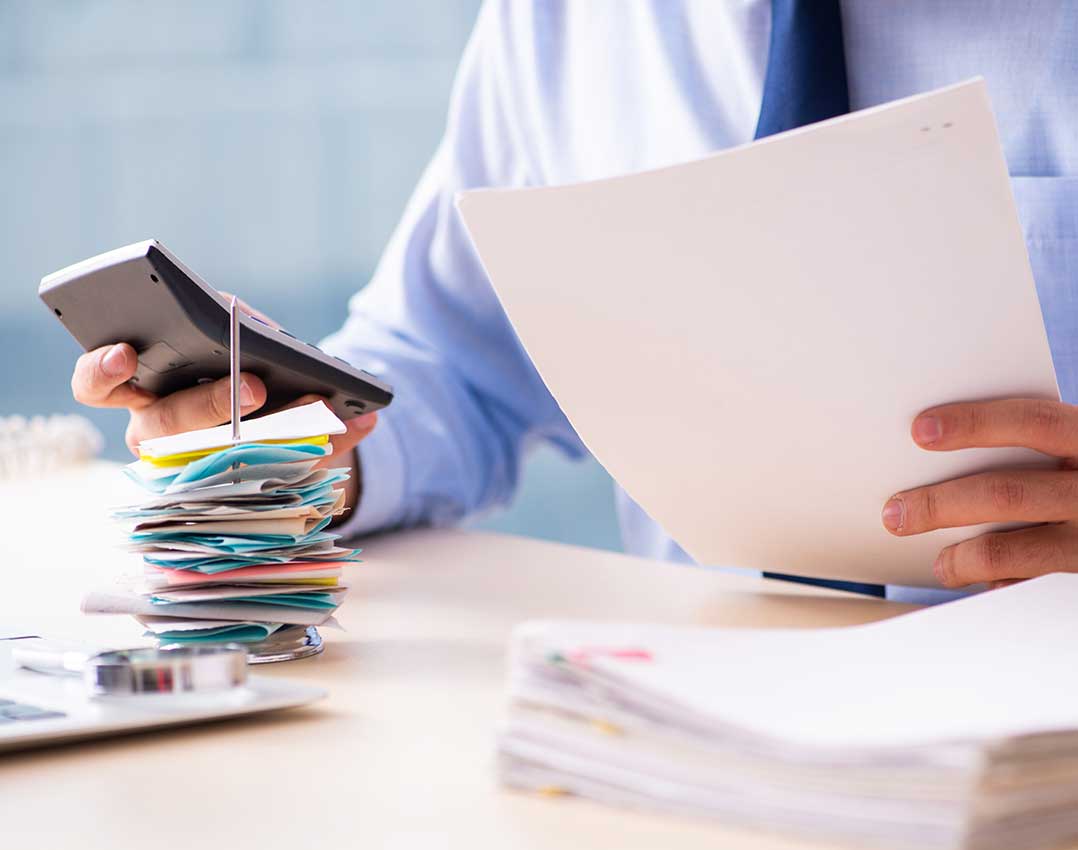
See how you can optimize your facility’s assets, reduce downtime, cut costs, and ensure efficient operations with RCM maintenance.
Facility managers are under constant pressure to keep operations running without disruption. Aging equipment, tight budgets, and growing expectations from leadership often make it more difficult to keep up.
Following a strictly time-based or corrective maintenance approach often wastes time and money and is more prone to missing the signs of potential system failure. Reliability-centered maintenance (RCM) offers a better approach. Its focus is prioritizing maintenance tasks based on asset functionality and risk.
The RCM process examines what each asset does, how it can fail, what causes those failures, and the potential failure consequences. This process helps you decide which type of maintenance makes sense for each situation, whether preventive, predictive, or run-to-failure. As a result, you can choose the most cost-effective, efficient, and safe maintenance strategies for each asset instead of using one maintenance program for all equipment.
If RCM sounds like an effective method for organizing your maintenance team and the tasks that they will perform, bookmark this page. We will explore the core principles of RCM, why they matter, and key steps to help you implement a reliability-centered maintenance program at your facility.
What Are the Principles of Reliability-Centered Maintenance (RCM)?
RCM is based on 9 key principles. These principles are intended to guide organizations to make more informed decisions about maintenance by focusing on actual asset behavior rather than assumptions.
Here is what those 9 principles are.
- You must accept some amount of asset failure because they are sometimes caused by uncontrollable events. In such cases, it’s more practical to accept that possibility and plan mitigation efforts rather than attempting to prevent it entirely.
- Do not assume that every asset failure is age-related. Research by Nowlan and Heap (focused on the aviation industry) found that 70% to 90% of equipment failures have no connection to age. Therefore, a strictly time-based maintenance program may be unreliable.
- The importance of equipment failures varies depending on the consequences. If an asset’s failure could affect safety, the environment, or production, comparatively more maintenance resources should be allocated for that asset.
- Failures may be the result of complex interactions. Do not assume that fixing singular parts will always be enough to prevent failures.
- Always check for hidden failures. Hidden failures are failures in systems that don’t run regularly, such as backup systems. Remember to check these systems for failures regularly so that they can perform effectively when needed.
- Identical assets may not suit the same maintenance strategies. Differences in the present operating context, usage patterns, and environments can lead to varying failure modes. Maintenance strategies should be tailored to each asset’s specific context.
- Preventive maintenance alone will not guarantee equipment reliability. Design quality, installation practices, and operational procedures also play a role.
- Effective maintenance programs focus on tasks that provide value. Reducing unnecessary or ineffective maintenance activities as much as possible will help you improve overall efficiency.
- Maintenance tasks should never be treated as “one-and-done.” Regularly review the results of your maintenance tasks and collect feedback to allow for continuous improvement.
The Benefits of Adopting an RCM Program
Less Unplanned Downtime
One of the key objectives of facilities maintenance management is always reduced downtime. By analyzing asset functions and their likely failure modes using the RCM process, maintenance tasks can be scheduled based on risk.
As a result, your facility will experience fewer unexpected downtime incidents, which will lead to improved equipment reliability that necessitates costly reactive maintenance.
Using the right data will quickly reduce future maintenance calls. For example, Sam’s Club reached their goal of 100% uptime by simply using the right data-driven insights.
Fewer Unnecessary Maintenance Tasks
RCM helps organizations allocate resources effectively by focusing on critical assets. You reduce the risk of over-servicing any piece of equipment. You will also free up your maintenance team so that they are more able to react quickly if it is needed.
Lower Maintenance Costs
Streamlining maintenance efforts means lower labor and materials costs. Focusing on specific assets at specific points on your maintenance schedule is an effective way to lower your maintenance budget and save time without compromising the integrity of your equipment.
Make Maintenance Costs Easier to Justify
RCM uses measurable data to support maintenance decisions. That means that you’ll be better equipped to justify your decisions while evaluating maintenance investments. You can present the financial impact of RCM with clear numbers that show reduced maintenance costs, fewer repairs, and longer asset performance.
Focus on how the program helps use existing resources more effectively rather than adding new expenses. Also, address concerns from leadership by explaining that RCM reduces reactive work and supports long-term stability.
You can also present the ROI of your reliability-centered maintenance program. The formula is as follows:
RCM ROI Formula
Total Expected Savings includes benefits from reduced reactive maintenance and extended asset life.
Total RCM Costs includes setup, training, tools, and ongoing management.
To use this formula, start by adding up all the expected savings your RCM program will bring, such as savings from less reactive maintenance and longer asset lifespans. Then, identify all RCM costs, including setup, training, tools, and ongoing management. Subtract the RCM costs from the total savings, then divide that number by the RCM costs. Multiply the result by 100 to get the ROI percentage.
A positive number means that your reliability-centered maintenance program will likely deliver more value than it costs.
Better Risk Management
Implementing an RCM program can also help with navigating risk management challenges. By evaluating the severity and likelihood of different failure modes, maintenance efforts are directed toward areas with the highest risk. This targeted approach mitigates potential hazards and supports safer operational environments.
Extended Asset Life
RCM allows for timely interventions that prevent minor issues from escalating. Proactive tasks are for more than simply reducing your risk of unexpected downtime. Scheduled maintenance tasks that keep assets running at your performance standards will also reduce wear and tear. Each asset will last longer, and your facility will save on repair and replacement costs.
Streamlined Maintenance Planning
Reliability-centered maintenance gives maintenance management clear guidelines on the appropriate maintenance tasks for each asset and when they must be performed. As a result, managers can schedule preventive maintenance activities in ways that better preserve system functions.
What Are The 7 Questions of RCM?
The 7 questions of RCM present a structured framework that helps facilities develop effective reliability-centered maintenance strategies. Each question builds on the last to help identify how assets are used, where they are vulnerable, and what actions will reduce the risk.
The questions are as follows:
1. What are the functions and performance standards of the asset?
Define what each asset is expected to do and the level of performance it must meet. This assessment sets the baseline for identifying when performance drops below acceptable levels.
2. In what ways can it fail?
Identify failure modes that would prevent the asset from performing to acceptable levels. Identifying these failure modes helps your team understand which potential issues could disrupt operations.
3. What causes each functional failure?
List the reasons why each failure might happen, including wear, errors, or environmental conditions. Knowing these reasons helps you plan targeted maintenance activities that prevent failures based on context.
4. What happens when each failure occurs?
Assess the potential impact of each potential failure, including safety, environmental, operational, or financial consequences. Understanding the possible consequences of equipment failures is integral to prioritizing maintenance tasks based on risk.
5. In what way does each failure matter?
Evaluate how serious the consequences of each potential failure could be. Not all failure modes should be treated with equal weight. Place a higher priority on assets with critical failure modes, such as those that would risk human safety or property damage.
6. What can be done to predict or prevent each failure?
Determine which proactive maintenance tasks, such as inspections or condition monitoring, are best to detect or prevent failures before they occur. Implement these tasks wherever possible.
7. What should be done if a suitable proactive task cannot be found?
If there is no way to predict or prevent certain failures (or if there is no way to feasibly implement certain preventive measures), consider what you should do next. Lacking the ability or resources to prevent a failure doesn’t mean that the incident will never happen.
Possible next steps could include redesigning the asset, accepting the risk of failure, or implementing a planned reactive maintenance process. Exploring preventive vs. reactive strategies may be your best approach in this scenario.
Core Steps to Implement Reliability-Centered Maintenance (RCM)
1. Set Clear Goals
Specify what you want your RCM program to achieve. For example, your goal may be to reduce the number of emergency calls and energy waste caused by your HVAC system. Having clear goals makes it more likely that you will get leadership buy-in.
2. Use The 7 Questions to Set Priorities
Ask yourself the 7 RCM questions to create an effective maintenance strategy. Define each asset’s function, identify how it can fail, and determine the likely causes. From there, you can set maintenance planning goals based on key priorities and a proactive maintenance approach.
3. Build a Maintenance Team For Your RCM Program
Decide whether to form a dedicated RCM-focused maintenance team or train members of your current maintenance and operations staff. If internal skill gaps or training budgets are a concern, start with focused training for key personnel. Small investments in skills development can lead to long-term savings as a result of reduced downtime.
4. Plan Your Key Maintenance Activities
Assign targeted maintenance tasks for each critical failure mode. Select only those that are practical, cost-effective, and proven to prevent or detect issues. Keep your task list strategically focused on the results each task offers. Remove as much unnecessary maintenance work as possible.
5. Consistently Evaluate Your RCM Process
A well-developed guide to maintenance procedures should include ongoing data analysis, regular adjustments, and a commitment to continuous improvement. Still, it’s understandable to worry about how you’ll find time for these tasks while also keeping up with routine maintenance schedules.
To solve this challenge, adopt a computerized maintenance management system (CMMS) or analytics platform. These systems help your team schedule tasks, monitor asset performance, and stay organized without additional administrative work.
Enable Reliability-Centered Maintenance With ServiceChannel
A reliability-centered maintenance program helps you reduce reactive work, focus on high-impact tasks, and use your resources more effectively. The steps above give you a strong starting point, but your next step is to find the right tools to help you drive a successful implementation.
ServiceChannel helps you apply reliability-centered maintenance (RCM) with clarity and control, whether you’re launching a pilot project or improving your current operations.
Schedule a quick call or short planning session to discuss adopting an effective maintenance program today.