Cost-Benefit Analysis of Maintenance
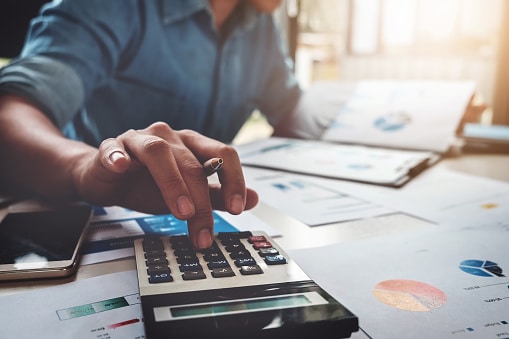
Explore our in-depth preventive maintenance cost calculation guide, cost-benefit analysis frameworks, and mitigation strategies for cost-effective operations.
Cost-benefit analysis is an important part of any business operation. Preventive and reactive maintenance are two critical business elements to consider when breaking down overall cost vs. benefit for the entire organization.
ServiceChannel offers excellent guidance on preventive maintenance for deeper insights into planning and performing maintenance tasks. Also, look at the benefits of preventive maintenance to further understand the importance of establishing and executing an effective maintenance schedule.
What is Cost-Benefit Analysis (CBA) in Maintenance?
CBA is the process of analyzing the risk vs. the reward of undertaking certain actions. In preventive maintenance, CBA examines the cost of preventive maintenance and weighs it against potential losses.
Breakdowns of critical assets could ultimately cost a company more than the sustained cost of preventive maintenance. It is prudent to employ proactive strategies for these assets.
Performing continual upkeep on some assets might cost more in the long run than performing emergency repairs or reactive maintenance as issues arise.
Preventive Maintenance Cost Calculation
There’s no denying the importance of preventive maintenance in reducing the need for costly emergency repairs. It’s also important to look at the direct and indirect costs that each asset will have associated with its upkeep. A strategic approach can reduce total maintenance costs overall and minimize equipment downtime. Whatever types of preventive maintenance your organization employs, any effective maintenance strategy should consider these expenses. The preventive maintenance cost calculation is:
Total Preventive Maintenance Cost=Direct Costs + Indirect Costs
1. Direct Costs
In reactive maintenance and preventive maintenance, direct costs are expenses that can be directly tied to performing maintenance tasks. Proactive maintenance strategies can significantly offset many maintenance expenditures. Direct maintenance costs include these factors.
- Labor costs: Repair costs include the per-hour wages of all personnel performing tasks multiplied by the time it takes to complete a task.
- Material costs: The itemized cost value of consumable and single-use items needed to complete a maintenance task.
- Equipment costs: This can be an estimated cost-of-wear for existing equipment or the cost of new tools and instruments needed to conduct maintenance.
- Contractor costs: The invoice total for third parties involved in conducting maintenance.
2. Indirect Costs
Calculating indirect maintenance costs such as those outlined below and attributing them directly to common preventive maintenance tasks is more challenging than determining direct maintenance costs.
- Downtime costs: Wages and overhead still pile up, with no deliverables being produced to offset these costs.
- Opportunity costs: Determine whether planning preventive maintenance vs. reactive maintenance will impact other possible future gains, either positively or negatively.
- Overhead costs: Utility and energy costs are a factor in all business expenses, including maintenance schedules.
- Environmental and safety costs: Many expenses are involved in keeping maintenance in compliance with environmental and safety regulations.
Cost-Benefit Analysis Framework
A cost-benefit analysis (CBA) framework is a systematic approach for calculating the financial impact of a company’s objectives. Applying these CBA framework elements to preventive and reactive maintenance can significantly reduce overall maintenance costs.
1. Identify Cost Drivers
Define specific objectives and determine their cost drivers. Cost drivers are the particular causes of expenses within a business action. For example, in a preventative maintenance strategy, direct and indirect cost drivers would include the wages of the maintenance workers, material and equipment expenses, and overhead costs of implementing the plan.
2. Quantify Costs and Benefits
Most objectives will have several moving parts, each with its own expense and benefit, including preventive maintenance goals. Analyze cost output and the advantages of your preventive maintenance practices and goals, then assign a realistic monetary value to each element.
3. Determine a Time Frame
A preventive maintenance objective with immediate benefits might cost you more in the long run. Define the timeframe of a cost-benefit analysis. Calculate the costs for the short term and the long term. Consider the long-term cost impact on your organization and determine whether the risk-to-reward ratio ultimately benefits your company.
4. Calculate the Net Present Value (NPV)
It only requires the simplest calculation to determine the NPV for your preventive maintenance strategy. Sum up the present value of preventive maintenance benefits and subtract the present value of preventive maintenance costs. The result is the net present value (NPV). A positive NPV indicates a favorable outcome.
Strategies for Mitigating Preventive Maintenance Costs
Expenses for preventive maintenance can rack up quickly. Reducing maintenance costs significantly tips the preventive maintenance cost-benefit ratio in your favor. Implementing these strategies can help your organization reduce maintenance costs while improving maintenance efficiency and reducing unplanned production downtime.
1. Analyze Historical Maintenance Data
Historical data is invaluable for preventive maintenance management. Specific patterns arise that help predict when and how assets might break down. This information enables maintenance managers to avoid issues and set an effective preventive maintenance schedule. A computerized maintenance management system (CMMS) is an excellent tool for helping companies collect and analyze valuable maintenance data and generate predictive maintenance strategies.
2. Risk-Based Prioritization
Assess risks based on the importance of assets. Calculate the direct and indirect costs involved if unexpected issues might lead to unplanned downtime or a safety risk to personnel. Prioritize preventive maintenance for assets that are most critical to operation, equipment that can pose a safety risk if not operating properly, and high-value assets with a higher likelihood of experiencing equipment downtime due to failure. A robust predictive maintenance software solution is an effective tool for assessing risks and constructing a successful maintenance plan.
3. Assess Equipment Health in Real-Time
Put condition-based monitoring systems in place to assess equipment health in real time. A powerful maintenance management software solution can monitor equipment’s condition and operational efficiency up to the moment and anticipate imminent issues based on historical maintenance data.
4. Optimize Maintenance Schedules
Structure your preventive maintenance plan to ensure maintenance occurs at the most cost-effective time for the company. It works best for many organizations during non-operational hours and between expected production runs.
5. Apply RCM Principles
Observe these five pillars of reliability-centered maintenance (RCM) and weave them into your maintenance plan.
- Identify failure points.
- Focus on maintaining function.
- Identify failure modes.
- Develop a routine maintenance strategy for each asset.
Tips for Conducting a Cost-Benefit Analysis
To make informed decisions on determining a maintenance budget and implementing a preventive maintenance plan, a company should first conduct a robust cost-benefit analysis (CBA). Here are some tips to help guide you through performing an effective CBA.
1. Assess the Cost of Inaction
Calculate the cost of taking no preventive maintenance action. Place a monetary value on expenditures and losses your organization may incur during an unexpected breakdown. Use these results as a baseline for comparison.
2. Quantify Costs and Benefits
Identify all costs and benefits and quantify them in monetary terms to enable a direct comparison between the two.
3. Include Opportunity Costs
Quantify potential opportunity costs, representing the benefits lost when deciding on an option.
4. Discount Future Cash Flows
Apply a discount rate to account for the monetary value of time expenditures.
5. Perform Sensitivity Analysis
Conduct a sensitivity analysis to assess the impact of variations on key assumptions. This helps calculate how the total cost will change based on different inputs, like how often preventive maintenance inspections will affect the likelihood of an asset’s equipment breaking down, by making assumptions about how that asset compares to others and looking for any differences.
Smart Investments, Bigger Returns with ServiceChannel
There’s no better modern-day tool for analyzing data for predictive maintenance, tracking maintenance tasks, and structuring an effective preventative maintenance plan than ServiceChannel’s powerful facilities maintenance management software. Sign onto the ServiceChannel platform today to discover how we can help you with your preventive maintenance cost calculation guide, cost-benefit analysis frameworks, and mitigation strategies for cost-effective operations and customer satisfaction.