8 Effective Strategies for Keeping a Log of Repairs
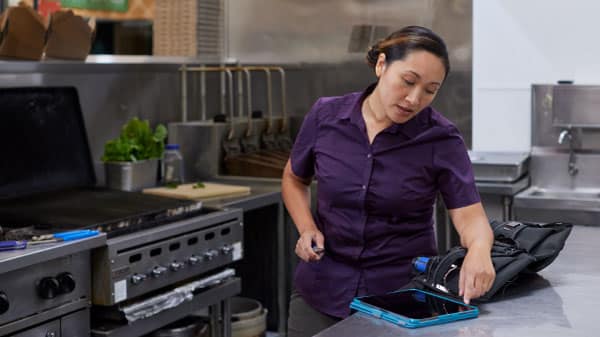
Discover effective practices for keeping a log of repairs to enhance equipment efficiency and lifespan. Learn how to keep your operations running smoothly.
Keeping a log of repairs is a key practice for efficient facilities management. Many organizations struggle with tracking maintenance activities, accessing past repair records, and standardizing documentation. Accurate repair and maintenance logs help prevent critical repair information from slipping through the cracks. Without structured record-keeping, delays and increased maintenance costs can add up. A well-organized approach helps your organization stay on track with an efficient and effective maintenance plan.
This guide outlines eight strategies to help you track, document, and analyze maintenance tasks more effectively. Whether your goal is digitizing maintenance logs, automating repair tracking, using maintenance schedule logs, or streamlining reporting, these best practices will help you build a reliable record-keeping system that enhances decision-making and improves facility performance.
1. Centralized Dashboard: Streamline Repair Tracking
Organizations often struggle with miscommunication, missed tasks, and inefficiencies in organizing work orders and maintenance activities. Without a centralized solution, tracking repair requests, scheduling maintenance, and keeping teams informed is often more difficult than it needs to be.
ServiceChannel’s unified dashboard provides a single view of all repair tasks — giving you full control over your maintenance operations and work order management. You can be confident that no repair request is overlooked, letting you focus on business-critical tasks.
Many organizations face challenges with fragmented systems, but our solution brings everything together in one place, simplifying workflows and enhancing communication between teams. Centralizing repair tracking will save time, improve resource allocation, and maintain full visibility into maintenance activities.
Explore ServiceChannel’s dashboard solutions to centralize your repair tracking today.
2. Automated Work Order Creation: Simplify Repair Logging
Manually creating work orders can be time-consuming and prone to errors, leading to delays, missing details, and workflow disruptions. Logging repairs can slow response times and impact maintenance operations without an efficient system.
With ServiceChannel, you can instantly generate a detailed work order using asset tags and QR code scanning for quick equipment identification and historical maintenance records. This ensures that you log every necessary repair without manually entering the data. This automation saves time and reduces errors, keeping records organized and up to date. If you’re looking for the fastest way to make accurate equipment maintenance logs and repairs, automated solutions like these are the answer.
Check out how automated work order creation can transform your maintenance logging.
3. Real-time Tracking: Act Fast on Open Repairs
Delaying open repair requests can lead to unnecessary challenges in work order management, such as unplanned downtime, increased repair costs, and operational disruptions. Maintenance requests can pile up quickly without a real-time tracking system, making it harder to prioritize urgent repairs and keep everything running smoothly.
ServiceChannel gives you full visibility into all open work orders in real-time, allowing you to respond faster and prevent minor issues from escalating into costly problems. By tracking repair statuses as they happen, you can minimize disruptions, keep maintenance personnel on schedule, and complete repairs efficiently. When you need to perform emergency repairs, real-time tracking lets maintenance teams quickly allocate resources, reducing downtime and preventing further damage to critical assets.
Project logs help track progress over time for larger-scale repairs or recurring issues. These records consolidate ongoing maintenance needs, maintenance activities performed, and future repair plans into one system, making it easier to manage long-term projects without losing critical repair data.
Learn more about real-time tracking and how it keeps your operations running smoothly.
4. Historical Data Logging: Access Past Repair Insights
Keeping track of past repairs helps spot recurring issues and make informed maintenance decisions. Without a reliable historical record, maintenance teams and equipment operators may struggle to identify trends, plan for future repairs, or understand an asset’s full lifecycle. This lack of visibility can lead to repeated equipment failure, inefficient maintenance schedules, and unnecessary repair costs.
ServiceChannel enhances your enterprise asset management system by automatically generating detailed equipment maintenance logs for every asset’s service history. This gives you instant access to valuable insights. Our platform functions as a digital equipment maintenance logbook, storing past service records in one place. You can also use an equipment maintenance log template to standardize data entry, ensuring consistency across your maintenance team.
With detailed maintenance records, you can identify patterns, predict future maintenance needs, and extend asset lifespans with more strategic planning. Easy access to historical information makes your maintenance strategy more proactive and cost-effective.
See how historical data logging can improve your long-term maintenance planning.
5. Customized Reporting: Analyze Trends and Make Data-Driven Decisions
Standardized reports don’t always provide the level of detail you need to justify maintenance spending or fine-tune your budget. Without customizable reporting tools, tracking repair trends, measuring maintenance performance, or making strategic, data-driven decisions is often difficult.
With ServiceChannel, you can build custom reports and modify dashboards to focus on the metrics that matter most to your organization. Whether you need to analyze repair spending, monitor response times, or assess service provider performance, our platform allows you to generate repair and maintenance reports tailored to your needs.
Key Insights You Can Track with Customized Reports
- Equipment Maintenance Logs: Monitor repair frequency and past service history easily to identify trends and inform future servicing.
- Machinery Maintenance Logs: Track wear and tear on critical assets, identifying equipment and parts that need replacing.
- Scheduled Maintenance Activities: Stay ahead of routine inspections and preventive maintenance, keeping your equipment in top condition.
- Maintenance Log Software Analytics: Evaluate compliance and data accuracy so you can remain confident in your operations practices.
- Future Maintenance Activities: Plan for upcoming repairs and budget allocations to ensure that you stay proactive.
- Workplace Safety Metrics: Identify trends in workplace incidents so that you can stay ahead of compliance and safety issues.
Start creating custom facilities management reports that provide actionable insights today.
6. Provider Management: Ensure Quality and Compliance
Managing all of your service providers can be a time-consuming challenge, often leading to inconsistent service quality, contract disputes, and potential compliance issues. A structured system lets you track provider performance and maintain accountability, easing much of the mental load and saving you time.
ServiceChannel simplifies provider management by giving you full visibility into contractor performance, contract terms, and compliance requirements. Our platform helps you track maintenance history, monitor key performance metrics, and verify that all providers meet your quality standards.
Tracking and Performance
Keeping tabs on provider performance helps you maintain service quality and identify issues before they escalate.
With ServiceChannel, you can track each provider’s response times, completion rates, and work quality. These insights help you make informed decisions and be confident that only the most reliable vendors handle your maintenance needs.
Compliance Features
Managing multiple service providers means keeping up with industry preventive maintenance compliance standards, governing regulations, and contractual obligations.
ServiceChannel helps you track provider certifications, insurance details, and service-level agreements in one place. By centralizing compliance management, you reduce the risk of non-compliance and maintain a higher standard of service across all your vendors.
Communication Tools
Clear communication between maintenance personnel and service providers is essential for avoiding delays and misunderstandings.
With built-in messaging and reporting, ServiceChannel lets you share digital logs and equipment maintenance reports between teams and contractors, keeping everyone on the same page. With instant updates and documented interactions, you can streamline coordination, reduce miscommunication, and ensure repair tasks are completed efficiently.
Optimize your provider management with ServiceChannel’s tools.
7. Mobile Access: Report Issues Instantly
Delays in reporting asset concerns can lead to incomplete logs, overlooked maintenance needs, and unexpected equipment breakdowns. Without an efficient way for on-site staff to communicate repair needs, issues can go unaddressed, creating larger problems.
With ServiceChannel’s mobile app, your team can log repair requests instantly, no matter where they are. This immediate access keeps maintenance data up to date, prevents small issues from escalating, and supports your facilities.
With integrated digital maintenance logs and cloud storage, your team can access repair records remotely, always keeping critical maintenance information at their fingertips. Whether tracking past work orders or documenting new or upcoming maintenance tasks, mobile access helps keep records accurate and accessible. You improve response times and enhance overall maintenance efficiency by enabling real-time reporting.
Empower your team with mobile access to improve maintenance log reporting.
8. Automated Workflows: Maintain and Control Your Repairs
Balancing flexibility and control in repair workflows can be challenging for maintenance managers. Without a structured system, inconsistencies and inefficiencies can get in the way of quickly completing routine maintenance activities, causing delays and unnecessary spending on repairs. Automating workflows standardizes maintenance processes while remaining adaptable to your organization’s needs.
ServiceChannel’s automated workflows simplify repair management by giving you a structured approach without imposing unnecessary oversight. These workflows keep your maintenance schedule consistent, improve efficiency, and let your teams manage repairs effectively without getting bogged down in manually writing down your log of repairs.
Workflow Customization
A one-size-fits-all approach doesn’t always work. Every organization has unique maintenance needs shaped by industry standards, government regulations, and operational requirements. For example, a lotion manufacturer relies on vats and liquid transfer systems, while a metal fabrication shop has no use for them.
ServiceChannel’s automated workflows allow you to customize approval processes, assign tasks based on priority, and tailor notifications to your needs. By adapting workflows to match your specific maintenance strategy, you improve efficiency while maintaining control over repair processes.
Automation Benefits
Manually keeping detailed equipment maintenance logs can be slow and cumbersome, often leading to errors and creating bottlenecks. Automating workflows eliminates these inefficiencies by standardizing the maintenance process, reducing administrative work, recording equipment performance, logging repairs, and enabling teams to address issues quickly.
With ServiceChannel’s automated workflows, a maintenance technician can set up predefined rules for approvals, task assignments, and follow-ups. This speeds up maintenance operations while enhancing accountability, not letting any critical task fall through the cracks.
Flexibility and Control
Finding the right balance between structured processes and adaptable workflows can be tricky. A rigid workflow can slow operations, while too much flexibility can lead to inconsistencies and missed maintenance tasks.
ServiceChannel’s automated workflows give you the best of both worlds — offering standardized processes while allowing for real-time adjustments when unexpected situations arise. This balance keeps maintenance actions efficient without sacrificing control over critical maintenance tasks.
Routine Inspections for Long-Term Reliability
Scheduling regular inspections is a fundamental part of any equipment reliability strategy. Regular check-ups help teams detect minor issues before they grow into costly repairs or unexpected failures.
With ServiceChannel’s automated workflows, you can schedule inspections, track maintenance logs, and receive alerts for timely maintenance — keeping your assets in peak condition.
Take the next step toward a streamlined preventive maintenance program with our automated workflows.
Strengthen Your Repair Logging Process
Keeping a log of repairs and maintenance is about more than generating documentation. It’s about staying efficient, reducing costs, and maintaining equipment reliability. These eight strategies provide a practical approach to improving your repair tracking and maintenance processes.
You streamline maintenance workflows and reduce administrative burden by centralizing work order management and automating processes. Real-time tracking and customized reports help you make informed decisions, while provider management, mobile access, and automated workflows improve efficiency and keep your facilities running smoothly.
Proper maintenance includes a mix of different types of maintenance, such as preventive, predictive, and emergency repairs. By maintaining logs that track these maintenance types, you can create a more proactive maintenance strategy, reduce equipment downtime, and extend the lifespan of critical assets.Take action now to optimize your repair logging process. Implement these best practices and see the difference in your maintenance practices. With ServiceChannel, you get the tools to seamlessly integrate repair logging into your maintenance strategy. Book a demo today and discover how our platform enhances your maintenance log tracking and efficiency.