What Is Deferred Maintenance?
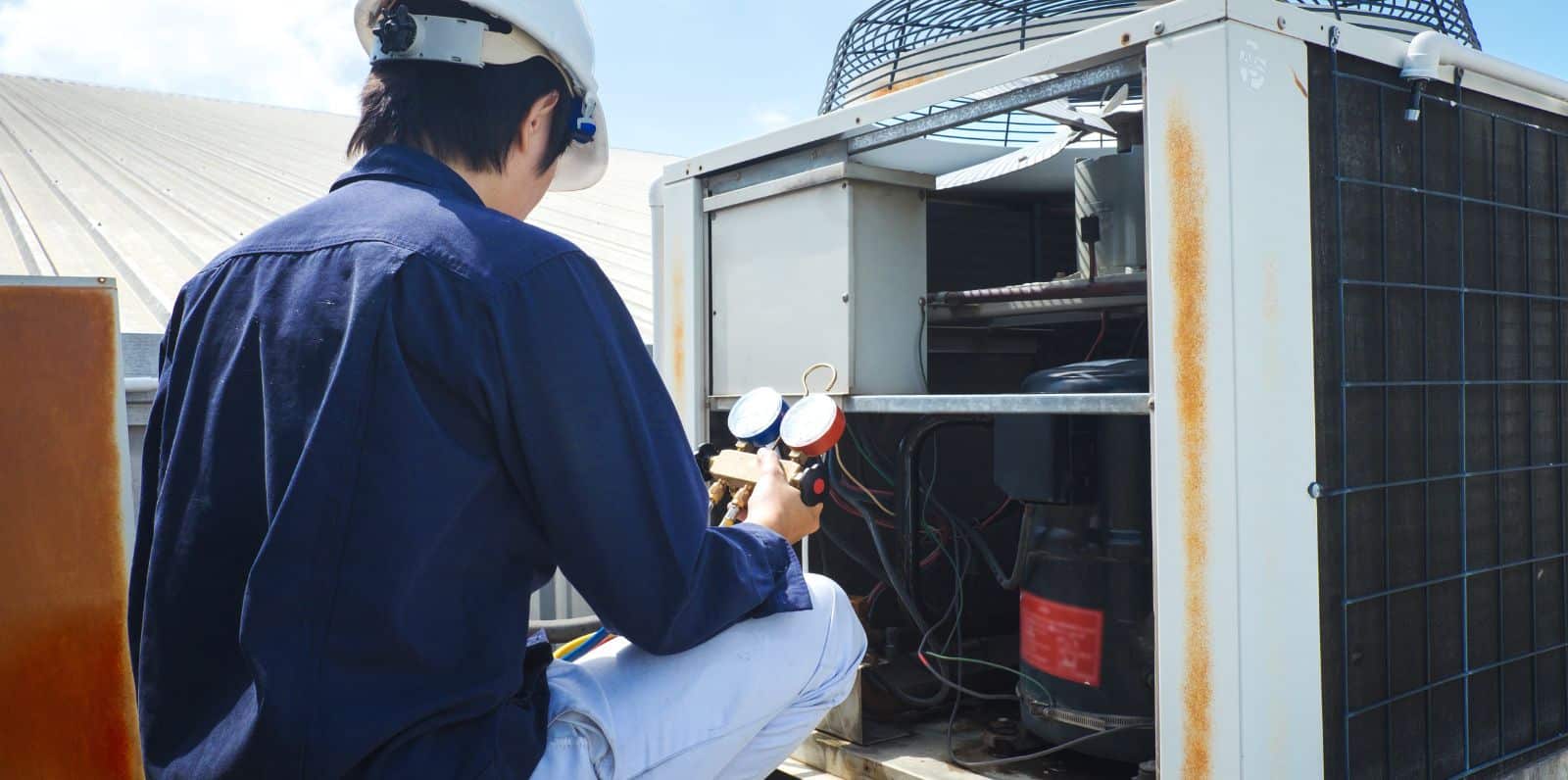
Learn about deferred maintenance, including what it is, how it affects your facility, and what you can do to overcome your maintenance backlog.
Occasionally, your facility may decide that delaying maintenance is the best option, even if repairs are needed. This decision is usually made to save future costs, allocate resources elsewhere, or prioritize other work.
This practice is called deferred maintenance, and the tasks you delay are part of your deferred maintenance backlog. While there is nothing inherently wrong with deferred repairs in general, you need to be careful not to delay critical tasks.
Understanding Deferred Maintenance
One reason to be careful with deferred maintenance is that minor maintenance issues can escalate if ignored for too long. Plus, assets that need repair may develop more issues later if the current problem isn’t resolved, leading to higher costs. This is why you must address deferred maintenance in the same way you would address any other routine maintenance strategy.
Why Is Deferred Maintenance Important?
It is important to identify which repairs require immediate attention and which can be delayed. A maintenance audit helps prioritize critical repairs and pushes lower-priority tasks further down the schedule or into deferred maintenance. Factors like maintenance costs, limited resource access, or unavailable parts often influence maintenance management’s decisions.
Examples of Deferred Maintenance
Deferred maintenance happens across different types of assets and facilities. In commercial buildings, typical examples include postponing cosmetic upkeep like painting offices, delaying landscaping, or skipping scheduled pressure washing.
Delaying inspections is also a form of deferred maintenance. For example, if a critical piece of equipment shows signs of failing, the maintenance team may need to inspect it right away, which can push back other scheduled inspections.
The reasons and frequency of deferred maintenance can also vary by industry. In public education, deferred maintenance often results from limited budgets. Schools and colleges may not receive enough funding from the local government or federal government to implement all needed repairs or upgrades. Lower-priority tasks are deferred to ensure that public assets affecting health and safety are always properly maintained.
Interestingly, deferred maintenance is prevalent in the government and public sector. The Government Accountability Office (GAO) reports that billions of dollars in needed repairs have been postponed due to tight budgets. Rising material and labor costs have caused further delays.
Common Reasons for Deferred Maintenance
Deferred maintenance can’t always be avoided. However, overdoing it can cause a wide range of problems. Facilities that overuse deferred maintenance have higher maintenance costs because their equipment doesn’t run efficiently.
Some common causes of deferred maintenance include:
- Company policies: The policies in place may be run-to-failure based, which means the assets and equipment run until they break down.
- Lack of information: If the maintenance strategy is unorganized or the facility does not have one, maintenance managers cannot use facilities management metrics (FM) to make educated decisions on the budget needed to run the department successfully.
- Lack of trained staff: Certain assets and equipment may require specialized training and knowledge that the current team lacks. When large assets break down, there may not be enough people to complete the repairs.
- Lack of parts: Depending on the asset or equipment, there may be a backlog of certain parts needed to repair the assets and equipment.
Deferred Maintenance Workflow
A deferred maintenance workflow indicates the expected scheduling of maintenance tasks and when they’re due. Using steps like these, the facility manager determines whether to schedule these tasks for completion or place them in a backlog:
- Look at preventive and reactive maintenance tasks and capital renewals.
- Determine if there are enough resources and time to complete the tasks.
- The maintenance tasks are scheduled if there are enough resources and time.
- The tasks are added to the maintenance backlog if there aren’t enough resources or bandwidth.
Long-Term Consequences of Deferred Maintenance
Deferred maintenance affects your entire facility. Understanding these impacts highlights why timely upkeep matters. Here are some common deferred maintenance issues:
- Increased backlog: Putting off repairs and upkeep today can grow your backlog and push back other critical maintenance.
- Decreased efficiency: Poorly maintained internal systems can lead to higher overhead costs, such as utility bills. Equipment not kept in good repair can experience intermittent breakdowns and loss of productivity.
- Increased safety hazards: Deferred maintenance on facility assets can increase the likelihood of stray components causing injury. Other hazards to be aware of include the potential for explosions and the build-up of carbon monoxide or other harmful gases.
- Compliance issues: Inspections revealing unmaintained assets may result in action from a regulatory agency. Depending on the severity of the problem, discovery of out-of-compliance equipment or assets could result in a warning, fines, or operational shutdowns.
- Decreased asset value: Better-maintained assets are consequently valued higher. Asset value can impact financial statements, which may subsequently affect business loans.
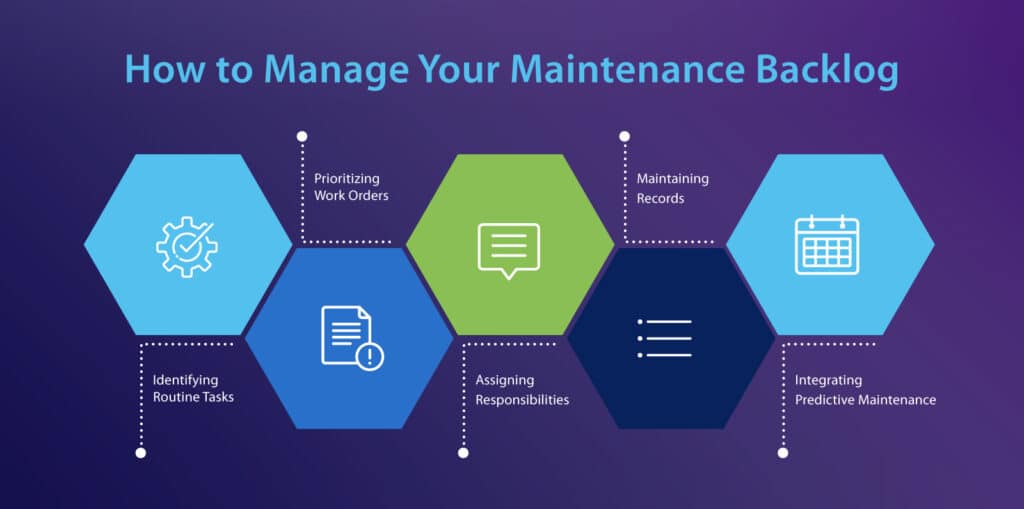
How to Manage Your Maintenance Backlog
Managing your maintenance backlog helps reduce delays, cut costs, and improve repair efficiency. Follow these steps to better maintain control over your backlog:
1. Identify Routine Tasks
Schedule recurring inspections to catch early signs of wear or failure. Test alert systems like smoke and carbon monoxide detectors regularly to protect safety and avoid costly downtime. Schedule regular maintenance and repairs so that anyone can cover for others when needed.
2. Prioritize Work Orders
Assign a work order for every task and sort them by urgency. First, focus on maintenance issues that need immediate attention. Such issues include anything that poses safety risks or could cause property damage. Close each completed task to keep your list current. Doing so helps make your backlog more manageable.
3. Assign Responsibilities
Make sure that everyone on your team understands their role. Hold regular meetings to review the backlog, update priorities, and adjust your strategy based on current risks or operational needs. Also, these meetings should be used to evaluate which work requests should be prioritized. Prioritize high-impact systems and delay lower-priority tasks so you can save costs and allocate more resources to higher-priority work.
4. Maintain Records
Use work order management software to track all tasks, inspections, and repairs. This practice saves time and prevents repeated work in the long run. Try breaking each report into 30, 60, and 90-day timelines to make it easier to reassign or reprioritize tasks as needed.
5. Integrate Predictive Maintenance
Adding predictive maintenance to your asset management process helps you stay ahead of equipment issues and avoid unplanned downtime. This strategy uses analytics to anticipate failures and schedule proactive repairs. Knowing when assets are at risk of failure soon is an easy way to ensure they are adequately maintained before failure occurs.
How to Decrease Your Deferred Maintenance Needs
1. Log All Maintenance Activities
Tracking all upkeep tasks is vital in effective maintenance scheduling. All preventive maintenance tasks and activities should be logged to see where problems most often occur. Data gathered through activity logging helps build a proactive, predictive model.
2. Develop a Preventive Maintenance Program
Routine maintenance reduces the risk of unexpected breakdowns. Therefore, there is less chance that an unexpected task will cause the need to defer other services.
3. Utilize a CMMS
A computerized maintenance management system (CMMS) tracks all maintenance tasks, scheduling, and deferred maintenance orders. A CMMS empowers facilities teams to make better budgeting and inventory decisions through analysis and visualizations.
4. Budget for Maintenance Projects
Set aside 2–4% of your total budget for maintenance projects. Factor in labor, materials, and admin costs as part of your overall maintenance costs. If you use production equipment, consider planning separate maintenance budgets for equipment and facility upkeep.
5. Manage Risks
Despite your best efforts, you do need to accept that periodic breakdowns will happen. You must also plan for risk mitigation efforts during these breakdowns. Effective risk management assesses what has the highest risk and greatest financial impact if a breakdown occurs. Once you have determined your risks, prepare all needed tools and materials ahead of time so that your maintenance teams can act quickly if a high-risk system breaks down.
The Role of Technology
Computerized Maintenance Management Systems (CMMS)
CMMS solutions can track all of your assets and equipment. A CMMS can often track certain metrics, such as pressure levels or torque, to inform users if equipment operates outside of acceptable parameters. These alerts allow you to act quickly before lasting damage occurs.
Building Automation Systems (BAS)
Building automation systems control certain functions to reduce the burden of manual monitoring tasks. Like a CMMS, a BAS observes the condition of integrated assets and provides alerts to pinpoint problems and risk factors.
Internet of Things (IoT)
The Internet of Things (IoT) integrates physical objects, allowing them to communicate across an internal network and the Internet. For example, a thermostat must no longer be hardwired to an HVAC unit. Wireless communication can direct a furnace or air conditioning unit to activate to maintain an optimal environment. This system helps reduce your backlog by keeping maintenance data current and alerting staff to problems before they escalate.
Use Cases
Different industries will need to address deferred maintenance differently for various reasons. Here is a quick overview of where these differences may occur:
Residential Buildings
Property managers overseeing residential buildings often delay cosmetic fixes and focus on repairs that may affect residents’ health or safety. For instance, a blocked sewer line can cause backups that could lead to water damage or health risks. Such issues always matter more than surface-level upgrades that are purely aesthetic.
Commercial Buildings
In shared commercial buildings, property owners are responsible for maintaining all infrastructure that multiple tenants share. Failing to keep these assets in good condition can lead to safety and legal risks. If tenants have equipment that only supports their business, they would manage maintenance and repairs independently. Therefore, deferred maintenance decisions largely depend on who is responsible for the asset.
Industrial Facilities
Industrial facilities depend on complex systems that usually involve heavy machinery. The challenge is that each piece of equipment will have its own maintenance needs. That means that decisions are typically made on an asset-by-asset basis instead of at the facility level.
Education
Schools, colleges, and universities often operate within strict budgets, making it necessary to prioritize maintenance that directly affects safety, accessibility, and learning environments. For example, fixing a leaking roof or repairing faulty HVAC systems will typically take precedence over cosmetic improvements like repainting hallways. Deferred maintenance in education settings often reflects a focus on maintaining functional, safe spaces for students and staff.
Government
Government facilities, ranging from administrative offices to public infrastructure, must balance public service delivery with fiscal responsibility. Essential repairs that impact safety, compliance, or critical operations — such as fixing broken elevators in municipal buildings or repairing bridges — are prioritized. Less critical upgrades are more likely to be deferred, especially when budgets are tight and funding must stretch across multiple public services.
In each case, decisions to defer maintenance should only happen when safety is not compromised and there’s a clear plan to minimize risk. Delaying needed repairs can lead to serious accidents, so following a strict preventive maintenance schedule is best.
Your Trusted Maintenance Partner
Replace deferring and postponing maintenance issues with a proactive solution. Maintenance management software is the definitive tool for improving your company’s approach to maintenance scheduling and record keeping and, ideally, keeping operating costs down.As your maintenance management solution, ServiceChannel can help your organization develop a proper maintenance strategy that works effectively, efficiently, and productively.
Explore our platform today for more information.