What is TCO in Facilities Management & How Can You Minimize It?
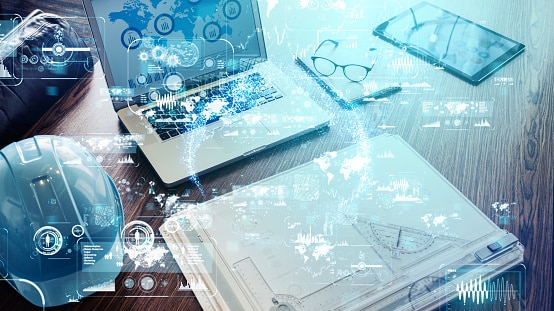
As anyone who has purchased a car knows, the upfront cost is one price; the cost of maintaining that vehicle is entirely another. This concept is a simple example of “total cost of ownership” or the total direct and indirect cost of purchasing and maintaining a system over its useful lifetime.
TCO is a well-understood concept in facilities management, especially when it comes to the maintenance and upkeep of critical equipment such as heating and cooling systems (e.g. HVAC) or business-essential ones (e.g. restaurant ovens). Keeping TCO as low as possible is the reason so many facilities managers and their businesses anguish over the dreaded “repair-or-replace” decisions when it comes to failed or failing equipment.
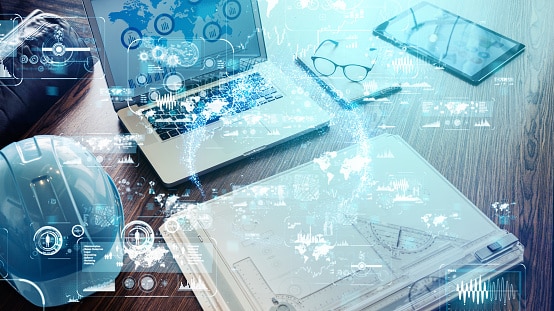
While having the ability to track costs and service history data is an absolute must, facilities managers can really make data-driven decisions when they have analytics and insights at their fingertips. Not only does analytics help the facility management team make better decisions about future equipment purchases, usage, and maintenance schedules, but this ultimately leads to being able to keep TCO in check.
For example, if the analytics reveal that a certain equipment brand is likely to fail consistently more than other brands, the business may opt to go with other options, even if the initial purchase prices are higher. In other words, with the right information and strategies at their disposal, minimizing TCO can be more science than gut for the modern FMs.
Let’s dive into some of the strategies they can use:
How to Calculate Total Cost of Ownership
There are six key areas to analyze when calculating the TCO of an asset:
- Initial Purchase Price: How much was the asset originally purchased for? Include any interest paid.
- Ongoing Operation Expenses: Installation costs, employee training to use the asset, electric utility use, insurance, regular safety or operation testing.
- Maintenance: Including repairs and regular maintenance that is required for the asset.
- Downtime: If the asset regularly doesn’t work (or work correctly), the cost of delays, production, and lost revenue should be included in TCO calculations.
- Usage Costs: Any additional costs outside of operation and maintenance that the asset requires, such as replacement parts due to wear and tear.
- Current Value: If the asset was sold, what would the resale value be?
These expenses and values are entered into a database or spreadsheet to calculate the overall cost of each asset. The current value reduces TCO, as this is money that would be gained if the asset was sold.
5 Strategies for Minimizing TCO
It’s clear to see that equipment ownership costs will add up quickly across a multi-location business. The good news is, facility management teams can take action to reduce the long-term cost of equipment ownership:
1. Asset Tracking & Preventive Maintenance
Facility managers can take advantage of specialized software solutions, like Service Automation, to keep track of assets across every business location. This includes data points like location, age, condition, warranty and service requests.
Most companies lose up to 34% of potential warranty savings from leakage and paying for repairs they don’t need. With access to warranty and repair details of all your capital equipment, facility teams can make data-backed “repair or replace” decisions based on TCO and depreciation analysis.
This information is also used to inform a preventive maintenance schedule, which extends equipment lifetime and reduces the likelihood of a costly sudden breakdown. This saves managers time and money spent on repairs and coordinating with contractors to get temporary or permanent fixes done quickly in the event of total equipment failure. Not only does consistent maintenance save costs in the long term by extending the life of your assets, but it also reduces the likelihood of having to spend a significant amount on emergency repairs.
2. Analytics
With the right CMMS platform, you will collect a lot of data on your assets — but without an analytics solution to visualize and synthesize the data, more than likely it will go unused.
With an analytics dashboard, your team can see if a specific location is spending significantly more than the average in repairs. They can identify which piece of equipment is the culprit (such as an older HVAC unit), take a look at its historical repair data, and quickly determine that a total replacement would save money and reduce TCO in the long run. Without access to these data points or a way to make sense of this information, you would continue dumping money into that HVAC unit with little return.
You can analyze other operation data as well, like energy usage. For example, say an HVAC unit was running without clean filters or without proper maintenance. This can lead to the consumption of excess energy and higher costs. However, with analytics capabilities, this would all be tracked and preventative measures could be put in place before accidentally running excess costs.
3. Contractor Relationships
Maintaining strong relationships with contractors and service partners might not be top-of-mind, but it helps decrease TCO
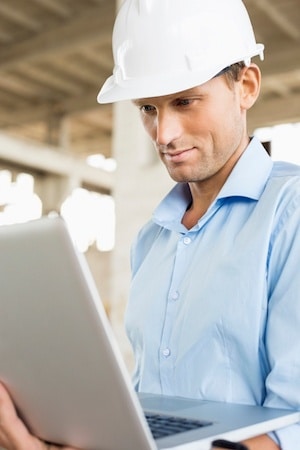
through more efficient repairs, shorter maintenance visits, and accurate service history data.
One common complaint from contractors is delayed payments. With a tool like Service Automation, your team can easily review and accept invoices and proposals, make electronic payments, and even automate the approval process. This ensures contractors get paid on time, and even cuts down on payment processing costs.
Spending time to build relationships with your contractors also facilitates more honest conversations about actual repair and maintenance costs. This prevents unnecessary fixes that are done to drive up an invoice amount. Additionally, using approved contractors that are qualified and trusted will lead to better results than if you used contractors who were found through a google search and don’t already have prior experience using your equipment.
4. Compliance
Making sure all equipment and building materials are compliant is often a thankless task for compliance officers, but it is a crucial area of facility management. Safety, installation, and material compliance can prevent future legal and repair costs due to improper installation or maintenance of building equipment.
For example, in order to mitigate the environmental impacts of refrigerant leakage, the EPA’s Clean Air Act mandates specific practices for the repair, disposal, and maintenance of refrigerated assets. Companies often struggle with traditional methods of manually tracking the work done on their assets, which increases their risks of fines that can total $27,500 per day.
ServiceChannel’s Refrigerant Tracking Manager reduces this regulatory risk by automating the scheduling of maintenance, repairs and follow-up verification based on the specific leak thresholds mandated by the EPA. In fact, ServiceChannel has already helped customers reduce overall leakage rates by up to 45% and can now further help them comply with these new regulations.
Some other areas of compliance in facility management include:
- Regularly monitoring and auditing equipment use, maintenance, and usage. For example, vertical transportation equipment.
- Ensuring ALL service providers and contractors are properly insured and experienced, including fourth parties or subcontractors.
- Better communication of all involved parties to ensure everything is compliant, from hourly staff to safety officers
Compliance rules and regulations vary wildly by industry, location, and equipment use, so it’s important to alert for any policy changes that apply specifically to each facility.
5. Automation
Automating workflows related to asset management can be a critical tool to managing hundreds and thousands of assets. Having a CMMS platform with automation can help you collect valuable data and give you the ability to set alerts and automated workflows to drive action. Especially in the case of businesses like retail or chain restaurants with facilities all over the country, without this automated element, opportunities like this will be missed simply due to oversight
You need a platform with sophisticated automation for all types of workflows – whether it is tracking key data points on service requests or generating new work orders based on a particular schedule, an all in one system is ideal for a facility team managing thousands of assets where costs can run high if not tracked properly.
Having a CMMS that can support and integrate with smart assets can give you significant benefits, allowing you to be more proactive and schedule service before the asset breaks down. Having an easy to configure scheduling tool also allows you to plan and run a scheduled maintenance program as opposed to only being reactive.
Having access to advanced asset analytics can help you plan better. Having visibility into past repair data, processing times and overall costs can help you plan for upcoming budgets as well as possibly find better suppliers that could positively impact your operations.
Final Thoughts
Managing TCO across an enterprise with many locations is certainly a challenge, but it doesn’t have to be a shot in the dark. With the right data, tools, and processes in place, businesses and facilities teams can make the best data-driven decisions to calculate and manage TCO and use money in the most efficient way.
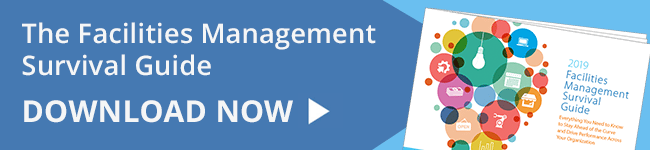