Preventive Maintenance vs Predictive Maintenance
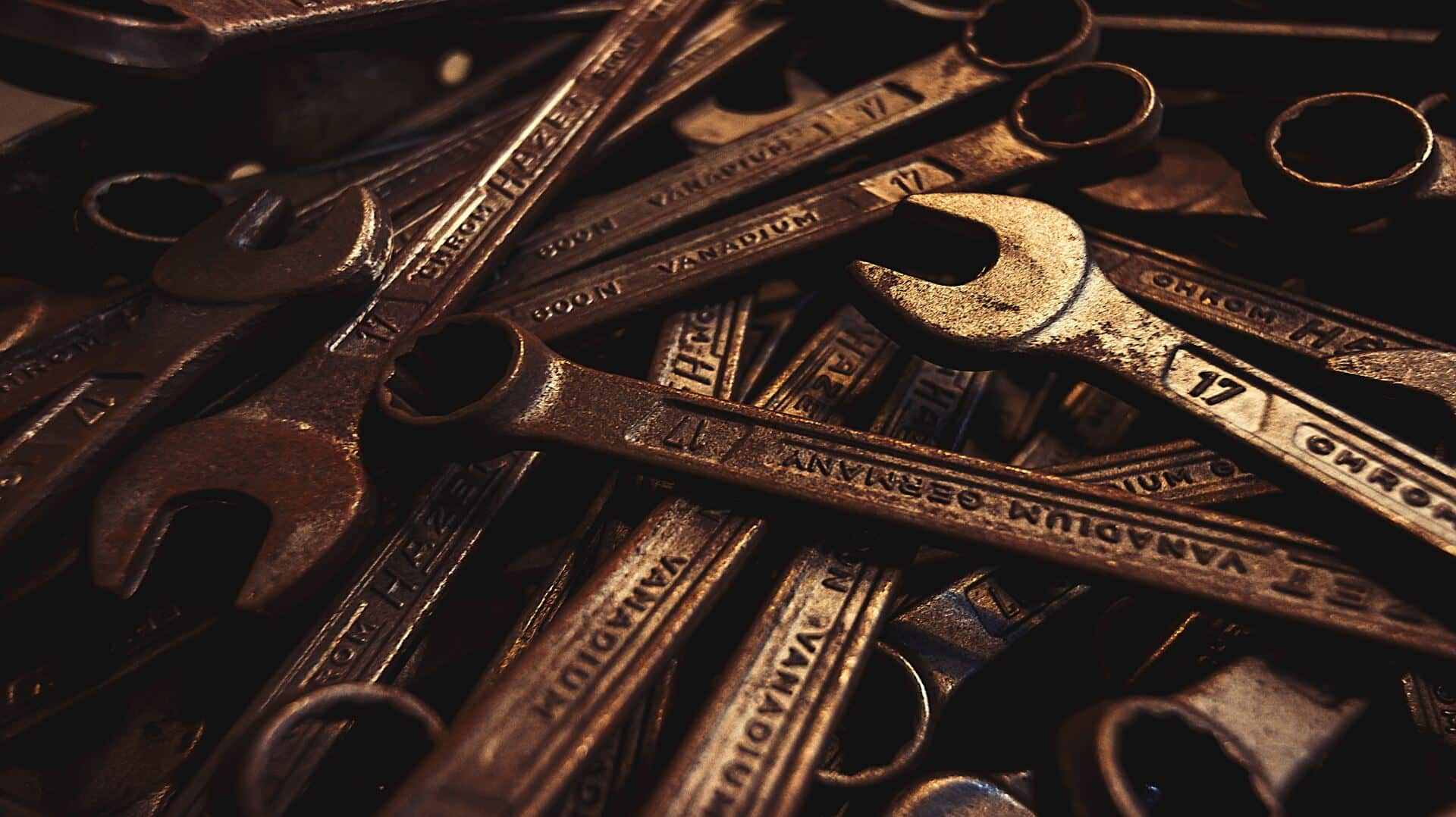
Preventive and predictive maintenance are both considered proactive maintenance strategies. They fit this definition because they both aim to keep equipment and systems operating smoothly through regular maintenance rather than fixing the equipment only when it breaks down.
Preventive and predictive maintenance can save your organization time and money because they are proactive. Extending the life of the equipment and avoiding lost productivity due to machine downtime helps to increase your overall profit margins.
Longer-lasting equipment decreases the amount of money you’ll need to spend on replacements, and less downtime leads to optimal work-hour usage.
What is Preventive Maintenance?
Preventive maintenance is a maintenance strategy that involves performing regular maintenance tasks at regular intervals based on a predefined set of criteria. For example, you might schedule maintenance weekly, monthly, semiannually, or annually, or plan for every 500, 1,000, or 5,000 hours of usage.
This proactive approach contrasts with reactive maintenance, which involves waiting until equipment failures occur before performing maintenance tasks.
Examples of Preventive Maintenance
Preventive maintenance is like getting the oil changed in your car at regular intervals to avoid engine problems. However, in the context of facility management, some prime examples of preventative maintenance include:
- A restaurant checks its stoves and refrigerators periodically to ensure they are operating properly
- A grocer cleans meat slicers regularly
- A manufacturer cleans large equipment parts on a regular schedule
- A manufacturer lubricates equipment after a certain amount of usage
- An accounting firm checks its electrical system every three months to ensure it still functions optimally and complies with code standards
When to Use Preventive Maintenance
A preventive maintenance plan is best when you need to keep equipment running smoothly without interrupting operations. You schedule when maintenance occurs so you can decide when it is most feasible to take assets offline.
You can also use preventive maintenance software to streamline this process. It automates the creation of work orders and the scheduling of technicians according to your established timelines.
Benefits of Preventive Maintenance
There are numerous benefits to preventive maintenance strategies. Here is a sample list of three.
Increasing Asset Reliability
Performing preventive maintenance decreases the risk of unexpected equipment failure and extends each asset’s useful life. As a result, your facility gets more consistent performance out of every asset for longer.
Predictable Machine Downtime
Unlike unexpected equipment downtime, planned downtime does not cause sudden halts in production. The predictability of scheduled maintenance downtime helps managers plan operations around preventive maintenance work periods.
Improved Safety Standards
Preventive maintenance can identify wear and tear or defects that might pose risks. Catching these issues early reduces the likelihood of accidents and promotes a safer work environment.
Limitations of Preventive Maintenance
Although the preventive maintenance approach offers significant benefits, it has limitations.
Increased Time and Labor
Preventive maintenance demands that staff regularly inspect, repair, and maintain equipment, even if it appears to be functioning well. Therefore, there will be more working hours spent on maintenance. These additional hours might be perceived as less productive than other business activities.
Resource Allocation Challenges
Preventive maintenance requires regular investment in tools, personnel, and time. Balancing these requirements with other operational needs can be difficult, especially for organizations with limited resources.
Possibility of Unnecessary Maintenance
When a maintenance schedule is based more on a routine timeline than the actual condition of the equipment, there’s a risk of performing unnecessary maintenance on equipment that doesn’t need it. The result could be unnecessary wear from too-frequent servicing.
What is Predictive Maintenance?
Predictive maintenance uses analytics to monitor equipment and detect potential malfunctions before failure occurs. It does this by tracking specific measurements that are associated with common causes of equipment failure and historical data. Measurements might include temperature, performance parameters, abnormal vibrations, or noise levels.
Predictive maintenance leverages advanced data analysis tools and data collection techniques, such as the Internet of Things (IoT), artificial intelligence (AI), cloud computing, or a combination thereof, to achieve this analysis.
Examples of Predictive Maintenance
Many industries effectively use predictive maintenance to avoid downtime. Here are some examples:
- A restaurant uses a refrigeration sensor to evaluate vibrations or temperature and alert staff to a potential problem before it occurs
- A manufacturer uses Al to gather information on an industrial machine’s performance and note when performance falls slightly out of the normal range so that you can schedule maintenance
- A building manager uses predictive maintenance technology in the HVAC system to track humidity and moisture within the building for abnormalities that demonstrate a need for maintenance
When to Use Predictive Maintenance?
Use a predictive maintenance strategy when strategically allocating your maintenance resources. This approach helps you see which assets need the most attention and when. These insights give you a clearer understanding of how to schedule your maintenance teams and how you can optimize labor and material costs.
A predictive maintenance program requires a significant investment. However, it can help you avoid making repairs before you need to. A McKinsey report predicts that predictive maintenance could save companies $630 billion on unnecessary maintenance by 2025.
If you want to use predictive maintenance on equipment that has not failed, you can create failure models using FEMA analysis. You can also recall potential repair data from a computerized maintenance management system (CMMS).
Advantages of Predictive Maintenance
Facility managers can reap numerous benefits by using the predictive maintenance strategy. Here are a few examples.
Increased Operational Efficiency
By predicting when a machine might fail, predictive maintenance allows for repairs to be done without significantly disrupting production. It may reduce both planned and unplanned downtime by catching issues early, so less extensive maintenance work is needed.
Optimized Maintenance Scheduling
Predictive maintenance allows for the optimization of maintenance schedules. Instead of following a set routine, maintenance activities are performed based on the actual condition of the equipment. This leads to more efficient use of maintenance resources and strategic servicing. Strategic servicing helps facilities avoid both under and over-maintenance while saving maintenance costs.
Reduced Environmental Impact
Predictive maintenance focuses on ensuring that equipment only undergoes maintenance when it’s necessary. As a result, it minimizes waste and energy consumption related to maintenance work. This approach also helps prevent incidents that could lead to environmental harm, such as leaks or emissions caused by equipment failure or inefficient asset performance.
Challenges of Predictive Maintenance
Like other maintenance practices, a predictive maintenance program has challenges. Here are a few to watch out for.
High Initial Investment
Implementing a predictive maintenance program requires a significant initial investment. Implementation includes costs for sensors, data analytics tools, and training personnel to interpret the data. This upfront cost is a major barrier to adopting predictive maintenance for many organizations, particularly smaller ones.
Complexity of Data Analysis
Predictive maintenance management relies heavily on data analysis, which can be complex and require specialized skills. Yet, accurately interpreting this data is crucial to predicting potential machine failure effectively. This complexity means that organizations must either train existing staff or hire new personnel with the necessary expertise.
Dependence on Technology
The condition monitoring techniques of predictive maintenance are heavily dependent on technology. Any failure or inaccuracy in the technology can lead to incorrect predictions, unexpected downtime, or unnecessary maintenance. Additionally, keeping up with technological advancements to maintain an effective predictive maintenance system can be both challenging and costly.
Preventive Maintenance vs. Predictive Maintenance: A Comparative Analysis
Triggers
Predetermined schedules or usage metrics are what initiate preventive maintenance. In contrast, machine data that assesses each asset’s condition serves as the trigger for predictive maintenance. One exception to this difference is the condition-based maintenance strategy (CBM). Like predictive maintenance, CBM is based on the asset’s condition, not on time or usage.
Scheduling
Preventive maintenance tasks occur on schedule, regardless of the condition of the equipment. Predictive maintenance occurs only when analytics advise it. Because machines typically must be down for maintenance, using predictive maintenance on critical equipment to which you can attach sensors will keep the device operating longer.
Cost-Effectiveness
Companies can implement preventive maintenance quickly and affordably by using preventive maintenance software to automate the project. Predictive maintenance requires more training, time, and money to implement. However, the potential cost savings of predictive maintenance are more significant in the long term.
Resources
Predictive maintenance requires a smaller team because machines are only serviced when analytics indicate otherwise. However, the team will require considerable technical skills. By comparison, a preventive maintenance program needs a larger maintenance team, but technicians don’t need as many technical skills beyond standard machine repair knowledge.
Choosing the Right Maintenance Strategy
The choice between preventive and predictive maintenance depends on several factors. These factors include:
- Your organization’s goals
- Types of assets
- Budgetary constraints
- Other maintenance strategies used
Predictive maintenance provides the most data but is comparatively more expensive to implement. It works best for companies with complex machines that are critical to the company’s operations. Although preventive maintenance often creates more planned downtime, it is inexpensive to implement. For this reason, it may be the best choice for most smaller companies.
The following list showcases what else to consider when deciding between a predictive or preventive maintenance program.
Equipment Criticality
If your facility has highly critical assets that could cause significant health and safety risks upon failure, it may be best to choose predictive maintenance. Preventive maintenance strategies may be simpler to implement, but time- or usage-based scheduling still has a (albeit smaller) failure risk.
Predictive or condition-based maintenance is the best choice if failure is out of the question for any asset, such as a piece of medical equipment.
Technological Infrastructure
Your organization’s technological infrastructure may impact your decision between preventive and predictive maintenance. Predictive maintenance is more feasible if your infrastructure can support condition monitoring equipment.
However, preventive maintenance is often a more realistic choice for organizations with more basic tech systems. It doesn’t require highly sophisticated technology to perform maintenance effectively.
Downtime Costs
Reduced downtime is the primary objective of all proactive maintenance strategies. However, unexpected downtime is a bigger risk when you choose time- or usage-based preventative maintenance strategies instead of a predictive or condition-based approach.
If downtime is associated with exceptionally high maintenance costs at your facility, predictive maintenance strategies may be the more cost-effective choice despite the higher initial investment.
Ease of Monitoring
The ease with which you can monitor the condition of your assets plays a crucial role in choosing a maintenance strategy. Preventive maintenance often requires less sophisticated monitoring systems, as it is based on regular checks rather than continuous monitoring.
Implementing preventive maintenance programs may be more feasible if your company cannot constantly track asset conditions.
The key to starting a proactive maintenance program is finding the right partner. ServiceChannel can provide both preventive and predictive maintenance solutions for your company. We can also help you decide which tools and services best meet your needs.
Learn more about the ServiceChannel platform and how we can help you get ahead and stay ahead with your maintenance strategy. Request a demo today.