How To Reduce Downtime In Facilities
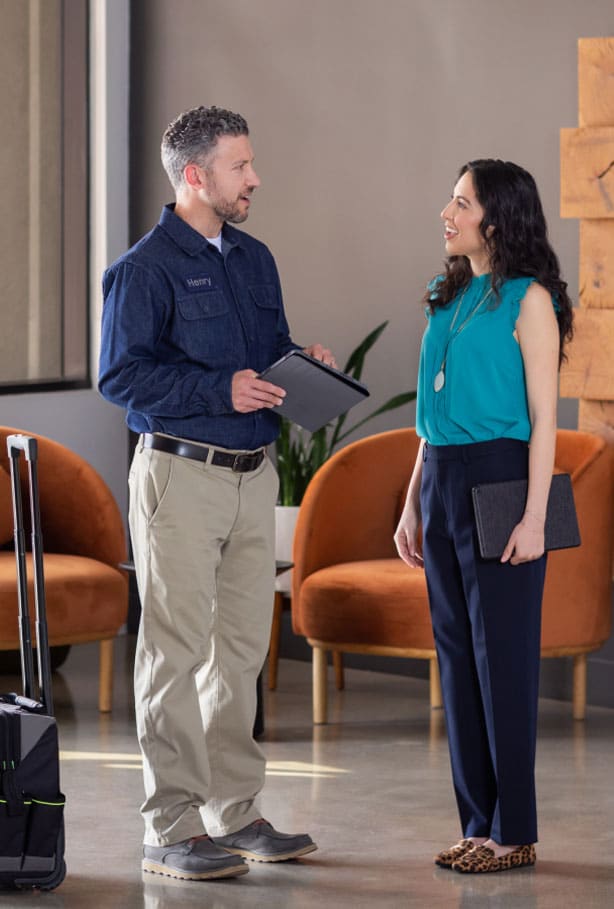
Discover how to reduce facility downtime with strategies, technology, and preventive planning. Learn to prevent errors, failures, and optimize maintenance.
Nothing impacts productivity quite as dramatically as a work stoppage or facility shutdown. These downtimes can be planned or unplanned, but the results are the same. Production comes to a halt. Whatever the reason for the downtime, the goal is always to minimize the length of the work stoppage. Here, you’ll learn some common reasons for production interruptions, ways to reduce the length of a stoppage and reduce machine downtime, and the benefits of preventive maintenance in minimizing unplanned downtime.
Importance of Reducing Downtime in Facilities
Whether it’s scheduled or unplanned downtime, any interruption in production costs a company money. Downtime also directly impacts a facility’s efficiency, a critical key performance indicator (KPI) across manufacturers in most industries. When costs rise and efficiency declines, this can significantly affect a company’s overall success.
Reasons for Downtime
Facilities can experience downtime for several reasons, planned or unplanned. Planned downtime is a scheduled shutdown of specific equipment or a facility for reasons such as planned maintenance or inspections. Planned shutdowns are often necessary to ensure equipment longevity, improve safety measures, or install new assets.
Unplanned downtime occurs when production is forced to shut down for unforeseen reasons, such as equipment failure or a workplace accident. It’s often difficult to predict how long an unplanned shutdown will last, depending on many variables. Whatever the reason for downtime, the objective remains to complete all necessary tasks as quickly as possible to maximize efficiency and minimize revenue loss.
Human Errors
While proper training and experience can minimize the risk, human error is inevitable. Employee mistakes, such as operational errors or workplace accidents, often lead to unplanned downtime for a facility.
Poor Maintenance
It’s not uncommon for facilities management to postpone scheduled equipment maintenance, preventive maintenance, or predictive maintenance in favor of continuing a line run. Deferring maintenance for too long can often lead to greater problems in the future, such as equipment breakage or reduced efficiency.
Equipment Failure
Equipment deteriorates over time, and extended usage can accelerate asset degradation. This often leads to unexpected critical equipment or machinery breakdowns, which, in turn, leads to unscheduled downtime. When replacement spare parts aren’t readily available, it can cause an extended production stoppage.
Security Incidents
Breaches can occur in an organization, often with nefarious intent. A facility may need to shut down its manufacturing process to investigate the source of the intrusion and remediate any developments that might arise from such a situation.
Excessive Changeovers
In a manufacturing plant, downtime events from production line changeovers add up over time. Excessive line changes frequently turn over consumable resources, increasing costs and decreasing overall production capacity.
Strategies to Reduce Downtime
Downtime is sometimes unavoidable. While shutdowns are an inherent part of doing business, an organization can employ a number of strategies to minimize the number and extent of facility and machine downtime.
Set Up a Preventive Maintenance Plan
Schedule regular inspections, repairs, and maintenance tasks. Exercising preventive maintenance on equipment and systems ensures machinery runs more efficiently and reduces the likelihood of an unexpected breakdown. When maintenance managers, employees, and operators are involved in continuous improvement initiatives, it helps provide a sense of ownership for the assets involved, and they are better taken care of, reducing unplanned downtime.
Perform Constant Risk Audits
Regularly scheduled site risk audits significantly help reduce unplanned downtime. Auditors inspect the facility, equipment, and operations to locate and identify potential points of failure, vulnerabilities, and safety hazards that could contribute to an unplanned work stoppage.
Be Proactive With Maintenance, Not Reactive
Be sure to respond to maintenance issues before equipment fails. Take a planned approach to regular maintenance by implementing a proactive maintenance strategy. Create a preventative maintenance schedule and a roadmap for response actions when a potential breakdown seems likely.
Prioritize Root Cause Analysis
Root cause analysis (RCA) refers to a collection of varying tools and techniques aimed at identifying issues that underlie system failures. Locating and addressing issues causing repeated shutdowns ensures continuous improvement and enables organizations to confidently resume operations and significantly reduce downtime.
Perform DMAIC Analysis
DMAIC means to define, measure, analyze, improve, and control. It refers to a five-stage method of improving processes and solving complex problems. A robust maintenance management software system will incorporate DMAIC or similar steps in their operation, helping organizations to minimize downtime in manufacturing, and optimize production.
Conduct a Facility Downtime Assessment
When downtime occurs, perform a facility-wide assessment to evaluate all assets. Downtime assessments enable the company to locate and identify vulnerabilities and assess the overall impact of a full production loss or stoppage. Such assessments can help prevent overspending and reduce downtime in the future by optimizing current maintenance and production practices.
Create a Maintenance Schedule
A well-structured preventive maintenance schedule enables organizations to see equipment effectiveness and arrange planned downtime strategically. Performing scheduled maintenance helps the company keep equipment in optimal running order and allows staff to identify obsolete equipment or assets approaching the end of their lifecycle.
Role of Technology to Reduce Facilities Downtime
Facilities can improve their operations by implementing updated or enhanced technology. Technological advancements improve all aspects of manufacturing. As devices grow smaller and more powerful, organizations can optimize available space, reduce downtime in manufacturing, increase productivity, and lower costs. Modern tech can also help decrease accidents, track downtime, and reduce cycle and lead times.
Computerized Maintenance Management Systems (CMMS)
A computerized maintenance management system (CMMS) software solution provides real-time data on equipment. With the ability to automate work orders, track equipment performance, and monitor asset statuses, a CMMS enables quicker repair response times and provides predictive maintenance recommendations to reduce downtime.
Augmented Reality (AR)
Augmented reality (AR) enables remote viewing of assets, keeping more staff from the factory floor and minimizing the necessity for experts to travel to a facility site to inspect and calibrate equipment during planned downtime. Advanced hands-free remote collaboration among operating personnel reduces the need to address machinery up close and in person.
Internet of Things (IoT)
The Internet of Things (IoT) enables equipment to be connected centrally to a hub via sensors that accurately diagnose equipment problems as they arise. The central system can monitor statuses and run real-time data analytics on connected devices, enabling it to predict eventual decreases in performance that might call for equipment downtime.
Cloud Computing
Cloud computing provides a secure and reliable platform for storing data off-site. Redundancies in cloud systems, along with off-site backup and storage capabilities, ensure that an onsite system failure doesn’t corrupt data and provides a means to restore data to a facility’s internal systems, reducing overall downtime and ensuring continuity.
Proactive Planning to Reduce Downtime with ServiceChannel
There’s little debate. Proactive planning and preventive maintenance are critical to reducing facility downtime. Effective scheduling strategies and work order management go a long way in keeping everything running smoothly.
Many industries today rely on dependable and efficient software solutions to help ensure production continuity and minimize work stoppages during a downtime event. Bring your organization into the future, secure your future productivity, and reduce the cost of downtime in your facilities with the help of the ServiceChannel platform.
Contact us to request a demo today.