How To Reduce Emergency Maintenance
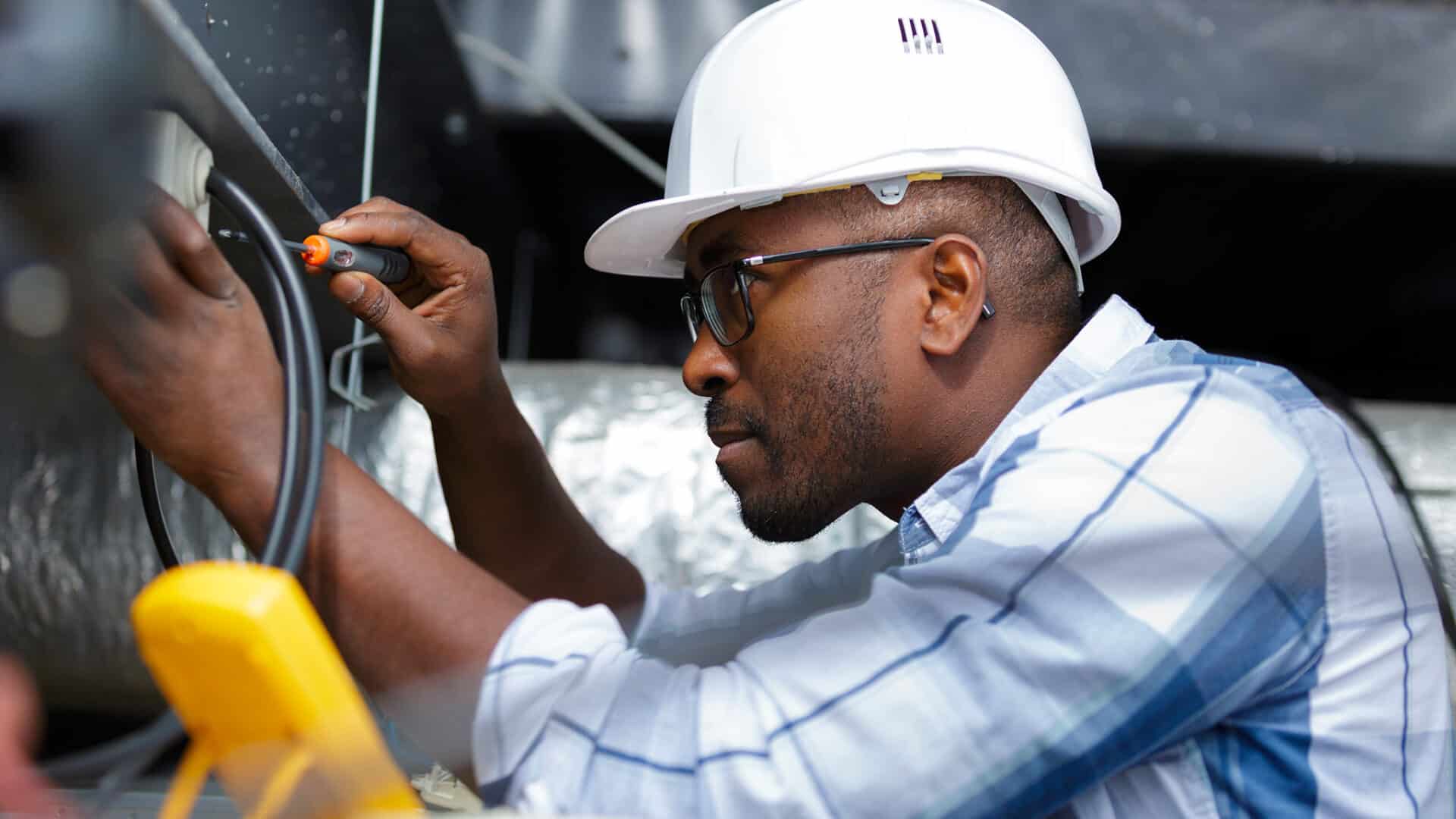
Learn how to reduce emergency maintenance risks with proactive strategies, including root cause analysis, preventive maintenance, and asset management.
No facility manager enjoys dealing with an emergency maintenance situation. When an emergency maintenance request appears, it may be a sign that safety or property value is at risk. It also leads to increased labor costs, re-scheduling, equipment downtime, and possibly overtime pay and lost revenue.
Fortunately, maintenance emergencies are usually preventable. Routine maintenance and proper asset use can prevent most urgent and emergency maintenance scenarios.
What is Emergency Maintenance?
Emergency maintenance is a form of reactive maintenance that must occur immediately due to the breakdown’s risk to human safety or property damage. Emergency breakdowns usually happen without warning. In most cases, the breakdown is caused by unexpected damage or misuse rather than expected deterioration.
Types of Emergency Maintenance
Equipment Breakdowns
Equipment breakdown refers to the unexpected malfunction of any crucial piece of equipment. This breakdown may result from an accident, misuse, natural incident, or insufficient equipment maintenance. Reactive maintenance to correct the malfunction is an emergency if that asset is required to uphold safety, maintain structural integrity, or perform core business operations.
Infrastructure Failures
Infrastructure failures refer to any emergency maintenance situation that involves your building’s infrastructure. Examples include a natural gas leak, air conditioning unit breakdown, clogged plumbing, or pipe burst. Such cases are not considered emergencies unless they risk serious property damage or building occupant safety.
Safety Hazards
Any mechanical failure that presents health and safety risks is an emergency maintenance situation. If the possible consequences are high, even potential failures may warrant an emergency maintenance request. An example of such a situation would be a suspected gas leak.
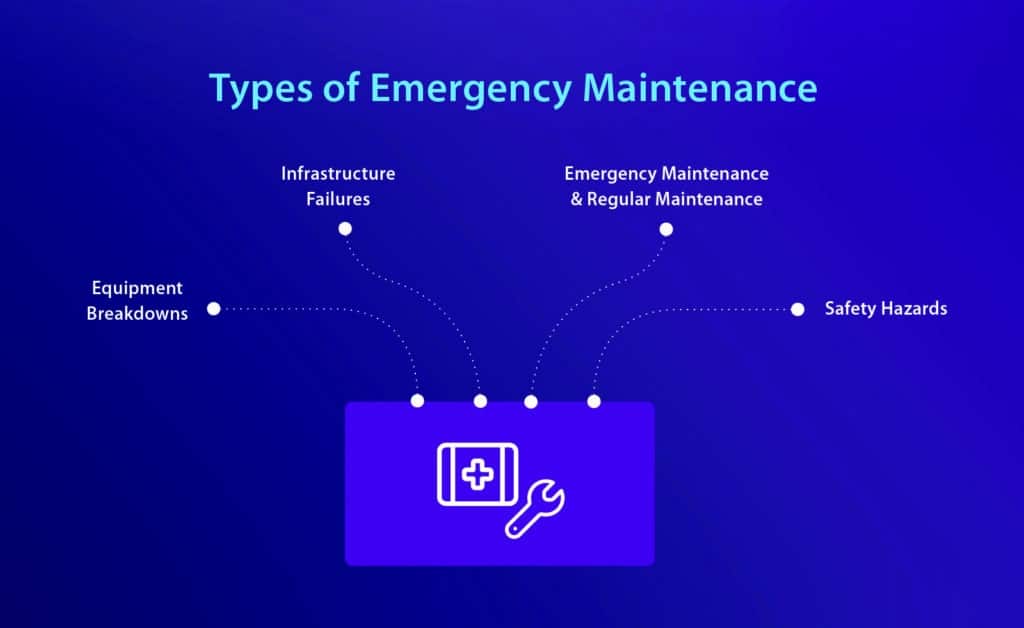
Emergency Maintenance vs. Regular Maintenance
Emergency maintenance and regular maintenance are two distinct approaches to managing and servicing assets and equipment within a facility. Regular maintenance is a form of non-emergency maintenance performed on a scheduled basis via your facility’s preventive maintenance program.
On the other hand, reacting to any issue that requires immediate attention is considered emergency maintenance. Urgent maintenance requests that do not directly threaten health and safety or property may not be regarded as emergencies.
How To Prevent and React To Emergency Maintenance Situations
Root Cause Analysis
By understanding the root causes of issues that lead to emergency maintenance, facility managers and maintenance teams can take targeted actions to prevent the same problems from occurring. Performing a root cause analysis allows you to revisit and adjust your maintenance strategies.
Common root causes of a maintenance emergency include:
- Lack of preventive maintenance
- Aging equipment
- Inadequate training
- Need for better preventive maintenance scheduling
- Accidents
- Natural events, such as fires, floods, or major snowfall
- Misuse by an employee or building occupant who is not a member of the maintenance team
Conduct a Maintenance Audit
A maintenance audit involves a comprehensive assessment of a facility’s maintenance practices, procedures, and records to identify areas of improvement. While performing an audit after your team encounters emergency maintenance issues is useful, proactively performing audits on a regular basis can prevent these issues from arising.
Plan for Possible Emergencies
Planning for possible emergencies involves creating contingency plans and response strategies to address emergency situations that may arise. You can prioritize your reactive and emergency maintenance workflow based on the urgency of the asset. Also, highlight protocols to uphold the safety of your maintenance team as they perform their work. For example, ensure they wear protective equipment when necessary.
Outline Emergency Maintenance Procedures
Emergency maintenance procedures provide clear instructions for maintenance teams on how to handle emergency situations, without safety risk and ensuring a structured and coordinated response. These procedures will expedite the time needed to complete emergency maintenance requests and maintain effective maintenance strategies.
Implement Preventive Maintenance
Implementing preventive maintenance is possibly the best way to reduce emergency maintenance issues. Preventive maintenance involves regularly scheduled maintenance tasks, inspections, and repairs to prevent equipment failures or problems before they occur. Taking this precaution will significantly reduce lingering issues that could lead to future emergencies.
Schedule Regular Maintenance Checks
Regular maintenance checks involve setting up recurring inspections and maintenance routines for all of your facility’s assets. You may perform checks on a time-based schedule or use predictive maintenance techniques to optimize your maintenance resources. In either case, checks should be regular and consistent.
Train Employees on Emergency Procedures
Employee training on emergency procedures involves educating staff on how to respond to maintenance emergencies safely and efficiently. This practice is crucial for workplace safety and will help you get your assets back in working order sooner.

Alternative Best Practices for Emergency Maintenance
The above maintenance strategies will work for your emergency maintenance program. However, every business is unique, and so are their emergencies. Here are some alternative emergency maintenance strategies effective practices that may help your facility.
Conducting Asset Management
Asset management involves systematically tracking, maintaining, and organizing your physical assets, including equipment, machinery, and infrastructure. Keeping a close eye on your assets will help you detect emergencies sooner and prevent some from happening. For instance, asset tracking may reveal that a particular asset is being stored at an improper temperature.
Replacement vs. Repair Strategies
Careful analysis of replacement vs. repair options allows facility managers to allocate resources efficiently. Opting for replacements when necessary can reduce the frequency of emergency maintenance caused by unreliable or outdated equipment. This analysis comes with the benefit of additional cost savings.
Creating a Maintenance Culture
When employees at all levels of an organization embrace a maintenance-focused culture, they are more likely to take care of equipment. As a result, they are less likely to misuse assets and more likely to report potential issues before they escalate into an emergency maintenance request.
Developing an Emergency Response Plan
An emergency response plan is a documented strategy that outlines how your team should react and manage emergency situations, including maintenance emergencies. This plan prevents knee-jerk reactions that could do more harm than good. It’s also a way to expedite emergency reactive maintenance when required.
Establishing Maintenance KPIs
You can gain valuable insights into an asset’s performance by setting and monitoring key performance indicators (KPIs). For example, you might use temperature as a KPI if overheating indicates incoming failure. These insights will help you identify improvement areas and make data-driven decisions. As a result, any future emergency maintenance issue will be handled with better care based on lessons learned.
The Importance of Reducing Emergency Maintenance
Emergencies can halt your operations, compromise health and safety, remove your maintenance team from normal business hours and scheduled work, and damage your equipment. Even with correct emergency maintenance team procedures, these risks remain. That’s why it’s crucial to prevent emergencies as much as possible, which is one of the benefits of preventive maintenance.
Preventive maintenance software tools make it much easier to keep your program on track and prevent a maintenance emergency. Such a tool may allow you to automate your schedules, ensuring more maintenance gets done precisely when needed.
Achieving Proactive Maintenance with ServiceChannel
When maintenance schedules fail, equipment suffers, and so does your facility. Avoid your next maintenance emergency by scheduling your preventive maintenance using ServiceChannel. Our software allows flexible scheduling so you can adjust your plans whenever there’s additional maintenance required.
The ServiceChannel app also allows virtual site audits, so you can be sure that every location upholds your predictive maintenance culture.
Book your free demo to see what ServiceChannel has to offer.