Types of Preventive Maintenance and How to Choose the Right PM Program
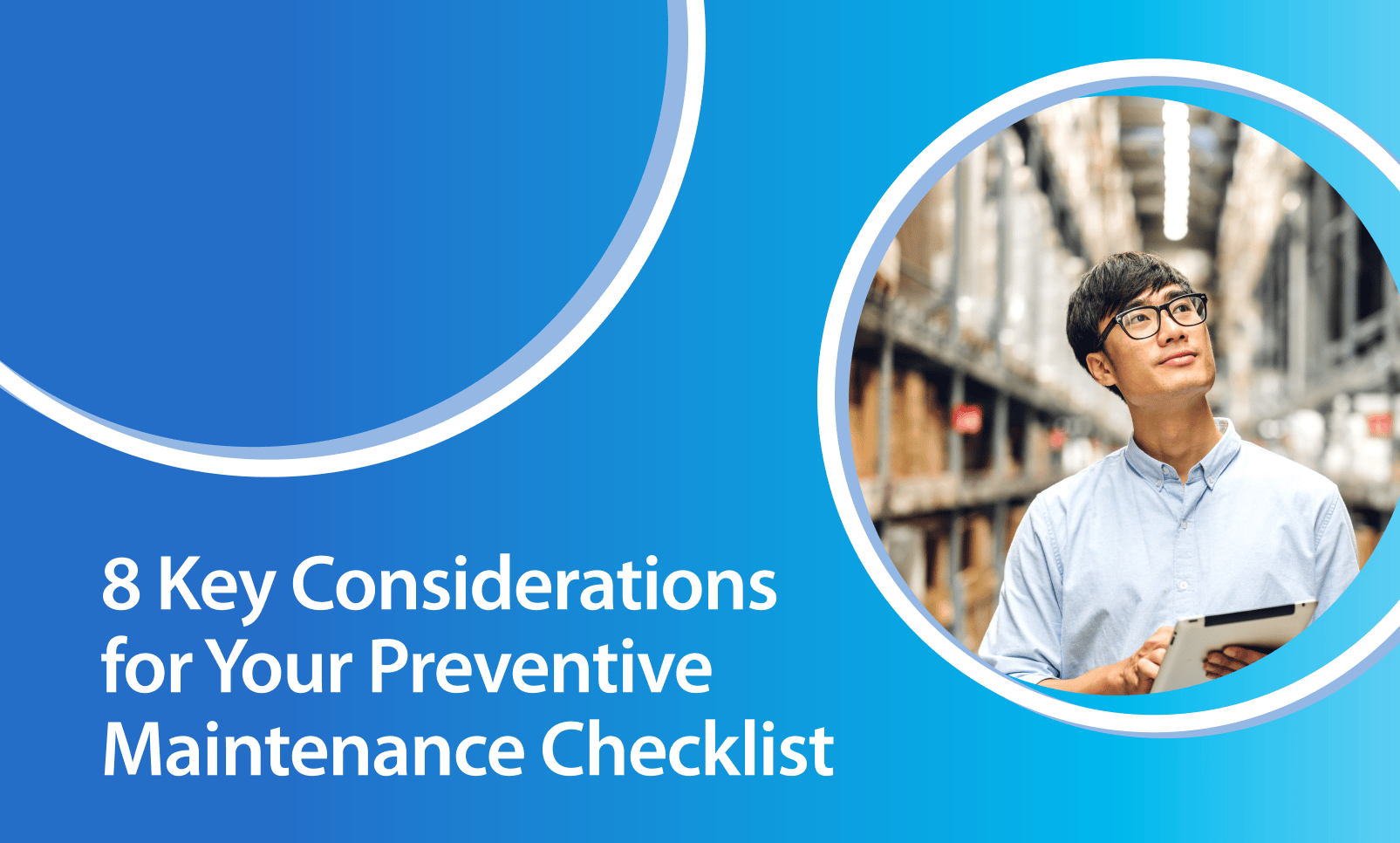
Preventive maintenance (PM) is a facility manager’s best friend—and it’s good for any company’s bottom line. Just like regular tune-ups and oil changes for your car, proactive maintenance, or preventive maintenance, goes a long way toward preventing a critical equipment failure that can leave your operations stranded on the side of the road while you wait for someone to come fix what’s wrong.
Different types of operations require different types of preventive maintenance plans—but they all require careful planning. Building the right program for your facility depends on understanding what the preventive maintenance process entails, the different types of preventive maintenance, and what to consider when implementing an effective preventative maintenance strategy.
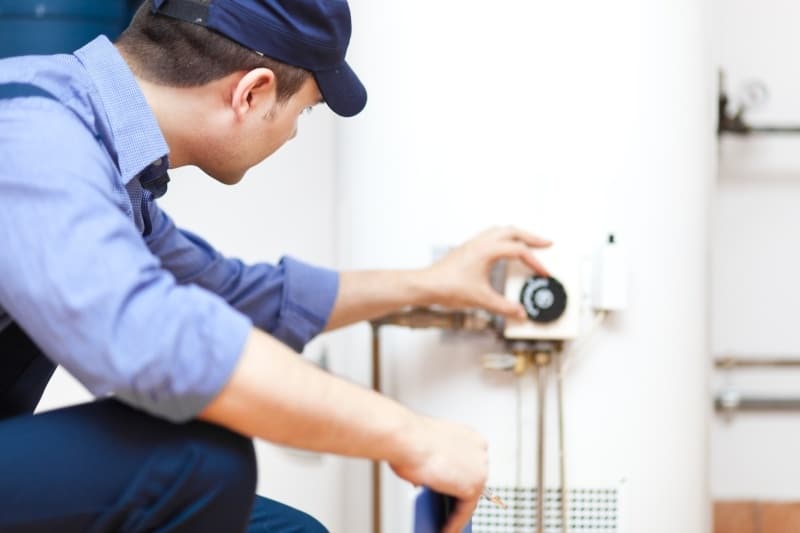
What is Preventive Maintenance?
Preventive maintenance is a method for keeping all of your assets in good working order to prevent equipment failures and unplanned downtime. It involves proactively scheduling maintenance tasks like inspecting equipment for potential issues before they become significant problems for your maintenance operations. Preventive maintenance examples include cleaning and lubricating the moving parts of equipment and replacing parts that are wearing out—before they wear out. Regular maintenance helps extend the life of your assets and reduce the costs associated with unplanned maintenance and repairing and replacing equipment.
Preventive Maintenance vs. Reactive Maintenance
The opposite of implementing a preventive maintenance schedule is performing reactive maintenance, or corrective maintenance, which is just what it sounds like—servicing your assets only in reaction to their various failure modes. Reactive maintenance costs far more in the long-term than a solid, comprehensive preventive maintenance strategy.
Advantages of Preventive Maintenance Schedules
The benefits of regular preventive maintenance vs. reactive maintenance extend beyond protecting your assets against premature failure and unplanned equipment downtime.
- Equipment that undergoes regular maintenance works better, whether it’s your HVAC system keeping customers cool, the ovens in your bakery maintaining the perfect temperature, or the coolers in your convenience store keeping beverages ice-cold.
- Equipment that’s in great condition has a higher resale value when it’s time to upgrade.
- Properly maintained equipment uses less energy and emits fewer greenhouse gasses than equipment that’s not part of a preventive maintenance strategy.
- Regular inspections help improve the safety of your equipment—and your maintenance teams.
Preventive Maintenance Examples
The tasks involved in preventive maintenance depend on the equipment. A preventive maintenance checklist for electrical systems might involve routine maintenance tasks like inspecting electrical panels and wiring, checking grounding and surge protection systems, and replacing damaged cords. A preventive maintenance task checklist for an HVAC system includes activities like lubricating moving parts, replacing filters or belts, cleaning coils, and checking for gas or refrigerant leaks. Scheduling preventive maintenance services on a regular basis helps you identify and address issues before they cause unplanned breakdowns and high corrective maintenance costs.
Types of Preventive Maintenance Strategies
The type of preventive maintenance plan that’s best for your company depends on the types of equipment you use, the criticality of your different assets, and the resources available to your maintenance team. Here are some common types of preventative maintenance schedules you can choose from.
Time based preventive maintenance (TPM)
Time based preventive maintenance involves performing routine maintenance tasks at predetermined intervals. Time based preventive maintenance schedules might be monthly, quarterly, or annually—or it could depend on the type of asset, the industry standards, the manufacturers’ recommendations, and how critical the equipment is to operations. A time based approach to preventive maintenance assumes that the equipment in question will need some type of preventive maintenance task at regular intervals, regardless of usage.
Reliability-centered maintenance (RCM)
Reliability-centered maintenance originated in the aviation industry and is widely employed in manufacturing, transportation, and energy. The key principle of RCM is that there is no one-size-fits-all maintenance plan that’s ideal for all asset types. RCM identifies the most relevant and effective maintenance strategy for an asset based on its particular needs, criticality, and failure consequences. The aim of RCM is to perform preventive maintenance in a way that maximizes the reliability and safety of equipment.
Usage-based maintenance
Usage-based preventive maintenance—also known as meter-based preventive maintenance—is a strategy of performing maintenance tasks based on the actual usage of an asset, such as hours, mileage, or cycles of operation. A usage-based preventive maintenance workflow is ideal for assets that have various usage patterns, like vehicles, conveyor systems, or pumps. It ensures the maintenance tasks are aligned with the actual use of the equipment and scheduled based on the wear and tear you’d expect at various usage points.
Condition-based maintenance (CBM)
Condition-based maintenance involves monitoring the condition of assets using sensors, data analysis, and predictive techniques. By continuously monitoring equipment performance and analyzing data, you can identify early warning signs of potential failures. CBM allows for targeted and preventative maintenance interventions, reduces unnecessary maintenance, and maximizes asset availability.
Predictive maintenance
Predictive maintenance leverages advanced analytics and machine learning algorithms to monitor equipment and predict failures. It optimizes maintenance activities and reduces unnecessary maintenance tasks by using real-time data, historical records, and predictive maintenance models to determine the best preventive maintenance schedule for a particular piece of equipment. Predictive maintenance is ideal for critical assets and can result in far fewer costly repairs.
Planned maintenance
Planned maintenance, also known as scheduled maintenance, is a proactive maintenance strategy that involves scheduling maintenance activities during planned downtime or during periods of low production demand. By coordinating preventive maintenance tasks with production schedules, you can minimize disruptions and maximize your maintenance resources. Planned maintenance is particularly beneficial for facilities with time-sensitive operations or limited downtime windows.
Elements of a Preventive Maintenance Program
A good preventive maintenance plan is based on factors like the amount and types of equipment you have, the criticality of your different asset types, and the size of your maintenance team. Regardless of the type of preventive maintenance schedule you implement, whether it’s predictive maintenance or a time-based plan, it should include these essential elements.
Asset inventory
Keeping an up-to-date inventory of all of your equipment helps you identify and prioritize assets for preventive maintenance, track their history, and ensure that no critical equipment components are overlooked.
Asset prioritization
Assigning priority levels to assets based on their criticality and impact on operations allows you to allocate resources effectively. Critical assets may require more frequent inspections and more comprehensive preventive maintenance activities than equipment that’s not as critical.
Maintenance scheduling
A well-planned maintenance schedule ensures that periodic maintenance is carried out systematically and in a timely manner. Preventive maintenance scheduling helps you avoid disruptions, streamline resource allocation, and optimize the availability of your assets.
Regular inspections
Regular inspections help you identify signs of wear, damage, or potential issues early on. These inspections can be conducted visually in person or with the help of sensors and monitoring systems, depending on the asset type, complexity, and the proactive maintenance plan you have in place.
Lubrication and cleaning
Proper lubrication and cleaning are essential preventive maintenance tasks for HVAC and other systems that help reduce friction, corrosion, and buildup of grime, which all contribute to premature equipment failure. These activities help keep your critical equipment running smoothly and efficiently to prevent unplanned downtime.
Documentation and record-keeping
Maintaining complete and accurate documentation of all preventive maintenance activities helps you track the maintenance cost and preventive maintenance benefits of each piece of equipment, identify recurring problems, and ensure compliance with warranty requirements. It also helps you track and plan your maintenance procedures and decide when and how often to schedule maintenance.
Performance measurement
Measuring the performance of assets allows facility managers to assess how effective your preventive maintenance program is. By monitoring key performance indicators (KPIs), such as equipment downtime during unplanned maintenance, mean time between equipment failures, and maintenance costs, you can identify areas for improvement and optimize your preventive maintenance strategies.
Continuous improvement
Regularly reviewing and improving your preventive maintenance plan is important for getting the most out of your proactive maintenance strategy. Analyze data, solicit feedback from your maintenance teams, and stay updated on industry best practices to continuously improve your preventive maintenance workflow and optimize your preventative maintenance program’s effectiveness.
Let’s Get Started
Ready to kickstart your maintenance program?
Tell us about your situation and we’ll help plan a preventive solution that hits your goals.
How to Decide Which Preventive Maintenance Plan is Right for Your Company
Practicing preventive maintenance is good for your bottom line—unlike reactive maintenance, which leads to costly repairs and strains the resources of your maintenance teams. Choosing the most suitable preventive maintenance program for your facility requires careful consideration of several factors, including the nature of your industry, the type of equipment and systems you’re using, and the resources available to your maintenance teams. Here are some important steps to help you make an informed decision about which preventive maintenance plan is right for you:
Assess your facility’s needs: Evaluate the criticality of each of your assets, their maintenance requirements, and any regulatory or compliance obligations that apply to your operations.
Consider the asset lifecycle: Understand the lifecycle of your assets, including their installation, operation, and decommissioning phases. Knowing this information about your equipment helps you create a preventive maintenance plan that will work best for your assets and your needs at each stage.
Evaluate equipment complexity: Complex assets may require condition monitoring, predictive maintenance techniques, or specialized expertise in a certain maintenance task. Assess the complexity of your equipment to determine the level of sophistication required in your preventive maintenance plan.
Analyze maintenance history: Review your maintenance records to identify recurring issues and patterns and determine the effectiveness of previous preventive maintenance programs (or reactive maintenance approaches.) An analysis of your maintenance history provides valuable insights for selecting the most suitable proactive maintenance plan for various types of equipment.
Seek expert advice: Consult with industry experts, equipment manufacturers, and maintenance professionals to gain insights about different advantages of preventive maintenance programs and which might be best for your facility and equipment.
Consider available resources: Determine the resources you have available when choosing a proactive maintenance plan and preventive maintenance schedule. Consider your budget, the size of your maintenance team, and the availability of your maintenance personnel. Choose a proactive maintenance program that aligns with the resources available to your facility managers.
Prioritize continuous improvement: Select a preventive maintenance program that’s flexible, adaptable, and which streamlines your maintenance processes for continuous improvement. Regularly review and refine your maintenance operation based on performance metrics and emerging best practices.
Preventive Maintenance Software for PM Program Implementation
Advanced digital maintenance solutions make quick and easy work of implementing and managing your preventive maintenance program. A computerized maintenance management system, or CMMS, is a comprehensive preventive maintenance software that tracks your assets, automates work orders, and produces reports that help you make data-driven decisions around performing periodic maintenance. Preventive maintenance software helps you streamline your PM program and ensures that every maintenance manager and maintenance technician on your team has access to critical information about HVAC and electrical systems as well as other equipment used in your operations.
Make ServiceChannel Your Preventive Maintenance Partner
Preventive maintenance helps save you money on equipment purchase and repair costs and reduce downtime. A preventive maintenance program is a far better way to manage your assets than relying on reactive maintenance. A comprehensive preventive maintenance program helps extend the lifespan of your equipment, keeps your assets operating properly and efficiently, and can ensure all essential preventive maintenance tasks are performed in a timely manner. The ServiceChannel platform offers a collaborative approach to preventive maintenance through our facilities maintenance solutions, including PM software, facilities management-as-a-service, and our premier Service Provider Marketplace. By understanding the different types of preventive maintenance work and the various program types available, you can choose the most suitable plan for your needs. ServiceChannel helps you continuously evaluate and improve your preventive maintenance program to stay ahead of emerging challenges and maximize the value of your facility investments.