A Guide to Corrective Maintenance
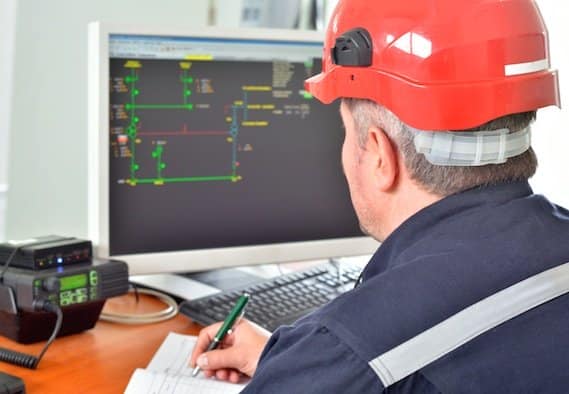
Corrective maintenance can be a significant part of an overall reliability strategy when implemented properly. Learn more in this comprehensive guide.
A comprehensive maintenance program is a key component to the smooth operation of a commercial or industrial enterprise. Thorough asset and equipment upkeep reduces the likelihood of breakdowns and ensures longer asset lifespans. Corrective maintenance is one of several strategies that organizations include in their maintenance plans to keep their facilities running at optimal levels.
This guide dives into the corrective maintenance process and how including this strategy in an organization’s maintenance program can help facility managers optimize maintenance practices and keep maintenance costs low.
What is Corrective Maintenance?
Also often referred to as reactive maintenance, corrective maintenance is the practice of addressing equipment and asset problems as they occur. There is planned corrective maintenance, unplanned corrective maintenance, emergency maintenance, and breakdown maintenance—to name a few examples.
In commercial and industrial enterprises, corrective maintenance differs from preventive maintenance in that a preventive strategy seeks to perform necessary upkeep tasks and conduct inspections before any issues arise.
The predictive maintenance strategy takes it a step further, using data analysis to anticipate future equipment issues and maintenance needs. A robust maintenance program incorporates all of these strategies. Each one contributes to a maintenance plan that minimizes issues and promotes optimal facility operations.
Applying predictive and preventative maintenance strategies to all assets would be cost-prohibitive and impractical. A corrective maintenance strategy works well for assets that have minimal impact on a production line.
Best Practices for Optimizing Corrective Maintenance
Applying these corrective maintenance best practices to your company’s maintenance processes can help maximize the effectiveness of your overall maintenance plan.
Promptly Address Issues
Prepare for emergency repair situations and respond swiftly to equipment failures. Optimize resource planning to minimize unplanned downtime. Monitor the condition and effectiveness of equipment as it runs to help anticipate corrective maintenance needs.
Troubleshooting
When a breakdown occurs, and the root of the failure isn’t readily apparent, practice these troubleshooting techniques, which have consistently proven invaluable to maintenance teams.
- Identify the issue.
- Examine and test components that could be causing the issue.
- Determine the defective element at the root of the issue.
- Create and implement a plan of action.
- Test the solution and analyze the results.
- Document the process to inform future maintenance tasks.
Preventing Recurring Issues
When assets repeatedly experience an equipment breakdown, the unnecessary costs can start to add up. Include actions such as those mentioned above in a preventive maintenance plan to reduce overall maintenance expenses and minimize the cost of downtime and resources.
Gathering Data
Tracking maintenance activities and analyzing collected data helps improve maintenance plans and increases corrective maintenance efficiency.
Corrective Maintenance Tips for Facilities Managers
Keep these useful practices in mind to conduct corrective maintenance tasks quicker and more effectively.
Train Staff
Provide training and continuing education opportunities for maintenance personnel to ensure that they remain up-to-date on the latest and most effective techniques for repairing and maintaining equipment.
Document Tasks
Thoroughly record maintenance activities. Keep track of the issue being corrected, steps to correct the issue, personnel who conducted corrective maintenance, and the time it took to complete. Other information, such as the timespan since the last breakdown and the parts needed to complete the task, are also helpful data points to track for recordkeeping and data analysis.
Leveraging Corrective Maintenance Data to Improve Preventive Plans
Corrective maintenance strategies are a great tool for enhancing existing preventive maintenance tasks. Adding these procedures to corrective maintenance practices can improve a preventive maintenance plan.
Data Analysis
Corrective maintenance data can provide numerous insights. Thorough analysis can track how often assets break down, average repair costs, estimated preventive maintenance costs, and many other data points to streamline maintenance policies and procedures.
Identify Patterns
Corrective maintenance tasks often offer first-hand experience with several assets and pieces of equipment. Maintenance team equipment interactions can provide invaluable information that helps identify patterns and trends in equipment failures.
Dynamically Update Maintenance Practices
Constant improvement shaves significant time off of maintenance activities and frequently produces more effective outcomes. Adjust maintenance practices to align with findings as you gather new information while performing corrective maintenance duties.
Combine Maintenance Strategies
Many assets benefit from utilizing multiple strategies where it makes sense. For example, a regular preventive maintenance task on a vacuum cleaner would include regularly emptying the dirt receptacle. Corrective maintenance includes such tasks as changing the belt if it breaks.
Balancing Corrective and Preventive Maintenance for Optimal Results
A corrective maintenance strategy works well for many situations, but it’s rarely the only approach to any given piece of equipment or asset. A balanced approach combines the best elements of corrective and preventive upkeep practices.
Pros of Relying on Corrective Maintenance
When applied to appropriate assets, a corrective maintenance strategy has benefits. Here are a few of the more impactful advantages of corrective maintenance practices.
Reduced Downtime
There are generally longer stretches of time between corrective maintenance tasks than between preventive maintenance duties. Preventive maintenance often involves more frequent periods of downtime that disrupt or delay production until all tasks are complete.
Less Planning is Required
Corrective maintenance is usually utilized on non-critical assets, which frees up planning time and resources for the upkeep of more important equipment.
Short-Term Cost Reduction
Corrective maintenance typically only requires resources and personnel at the time of need, reducing short-term maintenance costs. Keeping critical parts and materials on hand can further reduce immediate costs.
Cons of Relying on Corrective Maintenance
Waiting until issues present themselves before addressing them carries a certain amount of risk. Because of these uncertainties, a corrective maintenance strategy should be applied to non-critical assets and equipment.
Shortened Asset Lifespan
Damage to one machine component during operation can cause undue stress to other parts within the asset. This cascading effect can bring maintenance teams back to the same piece of equipment multiple times to remedy various issues. Repeated bouts of equipment failure have the potential to result in shorter asset life cycles from the continued stress.
Unpredictability
Without the benefits of planning and routine inspections, you can never be sure when an asset will encounter issues that call for corrective maintenance action. When an issue occurs, maintenance teams often need to spend more time diagnosing a problem than they would with the familiarity of a routine inspection.
Taking a Balanced Approach
Effectively blending corrective and preventive maintenance approaches can facilitate a smoother-running operation. Routine maintenance and inspections of critical assets ensure a more effective production line and optimize the maintenance budget.
Corrective Maintenance Factors to Consider
Strategies should be implemented for each asset individually, based on an item’s specific maintenance needs. When determining whether to apply a corrective strategy, a preventive strategy, or a combination strategy, consider these factors.
Impact of Failure
Consider the effect an equipment failure will have if a breakdown occurs. Consider a preventive and predictive maintenance strategy for assets that could produce a safety or health hazard and equipment that could significantly delay operations if they fail.
Replacement Cost
Calculate an asset’s expected annual upkeep and weigh that against the cost to replace it. The RAV calculation includes downtime, dismantling, transportation, and installation costs. A corrective maintenance strategy might work best for a non-critical asset if the preventive budget exceeds 2% to 5% of the RAV.
Optimizing Your Approach to Corrective Maintenance
Corrective maintenance is only effective if an organization strategically applies it to a comprehensive maintenance plan. Consider these useful tips to help maximize the effectiveness of your corrective maintenance processes.
- Training is essential. Make sure maintenance personnel understand the assets they’re working with and know how to effectively address issues they might encounter.
- Having a backup inventory of spare parts and materials on hand greatly reduces the time it takes to address common issues.
- Continuously improve by implementing practices that work and eliminating the ones that don’t.
Examples of Corrective Maintenance
Even with the most thorough preventive maintenance plans, industries are littered with examples of corrective maintenance measures that must be employed. Corrective maintenance is often the most effective approach to addressing issues.
Box-taping machines are a prime example of an asset used across numerous manufacturing facilities that would see little if any, benefit from a preventive maintenance plan. Box tapers tend to be reliable machines that usually only require a regular feed of new tape to keep going. When they break down, they’re relatively simple and inexpensive to replace, and a worker can easily perform the task while awaiting repairs or a replacement box taper.
Other assets that frequently enter a corrective maintenance plan include power hand tools, portable instrumentation, and industry furnishings such as work tables and seats. These items typically cost more to maintain over time than to repair or replace as needed, and they tend to have minimal impact on facility operations.
The Role of CMMS in Corrective Maintenance Management
A computerized maintenance management system (CMMS) is an effective tool for managing a maintenance program and maximizing the effectiveness of corrective maintenance activities. A CMMS enables facilities managers to schedule and track maintenance duties, assign roles, and gather data for more effective future maintenance planning. The measures an effective CMMS provides can significantly reduce maintenance costs by helping to streamline upkeep processes.
Apply these best practices to maximize the effectiveness of a CMMS solution.
- Track asset conditions and maintenance activities in real time.
- Get the entire organization involved and train essential personnel to administer and operate the software proficiently.
- Utilize dashboard features to get at-a-glance information on the status of assets and the effectiveness of maintenance.
- Take advantage of mobile capabilities to minimize travel time to a central console for data tracking.
Conclusion and Next Steps
In summary, businesses can make the most of their maintenance budgets by implementing an effective corrective maintenance strategy. Corrective maintenance is ideal for maintaining low-impact assets and reducing upkeep expenses by eliminating unnecessary routine tasks.
A powerful facilities management platform like ServiceChannel further streamlines maintenance activities by providing a toolset that offloads data analysis and tracking, freeing up facilities managers for more crucial tasks. Look into the ServiceChannel software solution today and learn how your organization can get the most out of its comprehensive maintenance plan.