What Is MRO, and Why Does It Matter?
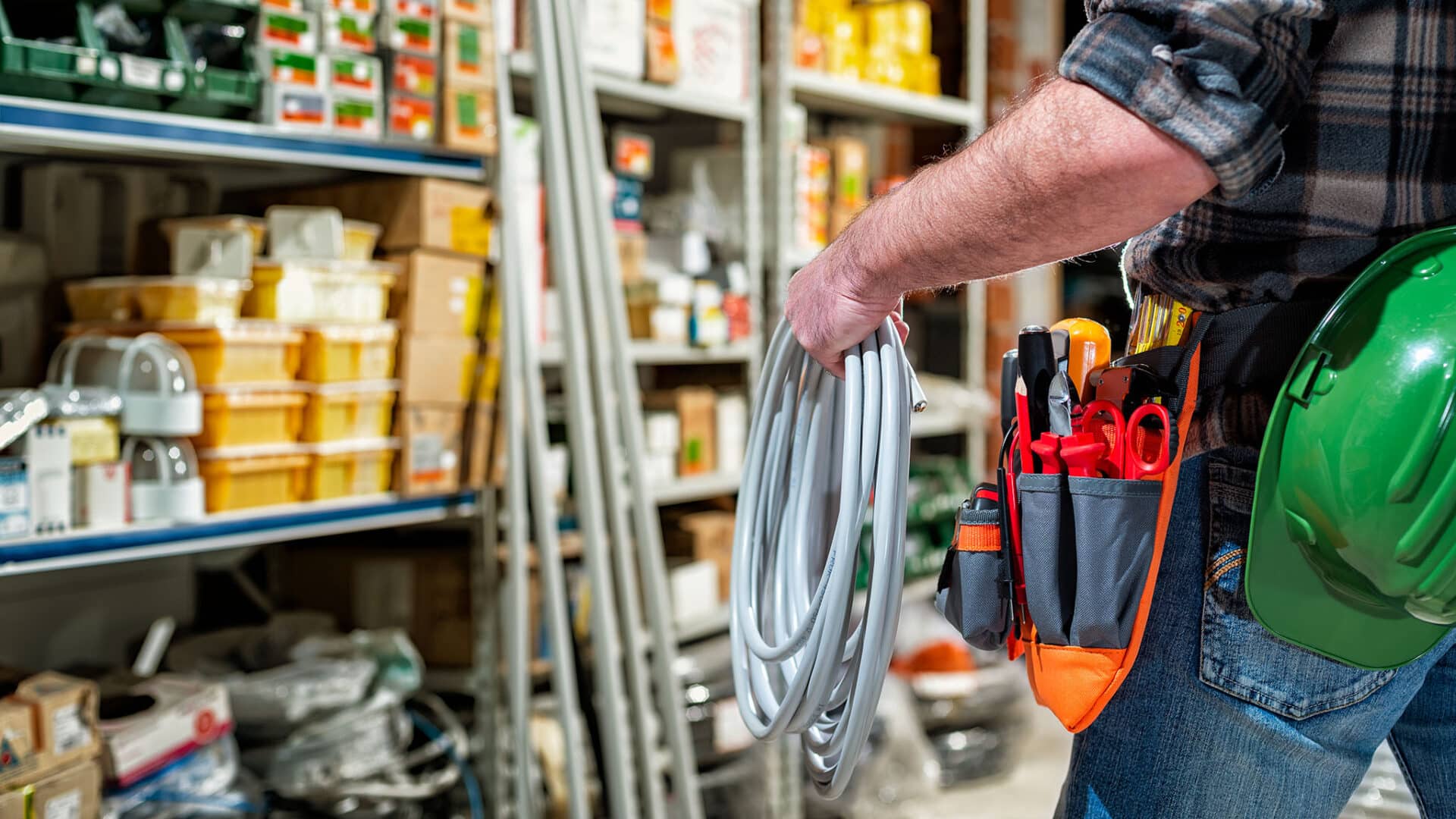
Learn what MRO means, why it matters for facility operations, and how to optimize your strategy with smarter tools, processes, and cost-saving tips.
Key Takeaways:
- MRO stands for Maintenance, Repair, and Operations — the backbone of effective facility management.
- MRO includes supplies, services, and processes that keep equipment and infrastructure running.
- Proper MRO strategy reduces downtime, extends asset life, and controls maintenance costs.
- CMMS software and predictive tools enhance MRO visibility and efficiency.
Efficient facility operations depend on more than just reactive fixes and scheduled maintenance. Maintenance, repair, and operations (MRO) plays a vital role in keeping assets running smoothly and reducing unscheduled downtime. As more organizations prioritize equipment reliability and operational efficiency, MRO strategies are becoming central to facility management across industries like retail, healthcare, manufacturing, and commercial services.
The term MRO stands for maintenance, repair, and operations. It is an umbrella term for the tools, services, and activities used to keep facilities and equipment running effectively. Unlike raw materials and other major components that go into finished products, MRO items support operational processes behind the scenes. MRO supplies can include anything from hand tools and personal protective equipment (PPE) to spare parts, cleaning staples, and office supplies.
In most facilities, MRO activities are essential for extending asset life cycles and maintaining clean and safe working environments. Whether replacing worn bearings on production equipment or restocking janitorial supplies, MRO processes ensure that everything runs smoothly day to day.
A solid MRO inventory strategy is vital for supporting production line efficiency, improving equipment uptime, and reducing MRO expenses. It also provides a foundation for more advanced maintenance approaches, such as predictive maintenance strategies and vendor-managed inventory programs.
MRO Products and Processes
MRO focuses on a wide range of activities that fall into three main categories: maintenance, repair, and operations. Each plays a unique role in supporting your facility’s physical equipment and infrastructure.
- Maintenance includes planned and unplanned upkeep actions for facilities and equipment. These tasks help identify potential issues early and extend the lifespan of assets.
- Repair involves restoring equipment after a failure. This includes minor fixes using hand tools and major corrective maintenance that may require replacement parts or outside service providers.
- Operations refers to the maintenance supplies and systems that keep things running day to day. This means everything from cleaning products and safety equipment to office supplies and pest control materials.
When managing maintenance tasks, it’s important to understand the differences between strategies:
- Preventive maintenance is scheduled in advance to avoid equipment failures.
- Corrective maintenance happens after a fault is detected and needs immediate resolution.
- Predictive maintenance strategies use data from sensors and performance logs to forecast and prevent breakdowns before they occur.
Together, these MRO processes help reduce downtime, lower MRO costs, and maintain smooth production processes. Facilities that use inventory management software and track key performance indicators (KPIs) are better positioned to streamline MRO operations, reduce costs, and gain a competitive edge.
The Role of MRO in Facility Management
A well-executed MRO strategy significantly contributes to effective facility management. From infrastructure repair and maintenance to inventory control and vendor coordination, MRO touches every corner of your operational ecosystem.
Modern facilities rely on computerized maintenance management systems (CMMS) to streamline MRO processes and reduce manual workload. By centralizing data and scheduling, CMMS software makes it easier to track maintenance activities, monitor asset performance, and flag issues before they become costly failures.
An integrated MRO plan also strengthens asset management. With the right tools, facility teams can keep critical systems in top shape, avoid unplanned downtime, and extend the life of essential equipment.
The result is fewer disruptions, greater visibility, and significant cost savings over time. Combined with preventive maintenance practices, a smart MRO strategy helps teams stay proactive instead of reactive.
To learn more about how CMMS fits into this picture, check out our full breakdown of what CMMS software does and how it supports smarter, faster maintenance operations.
MRO vs. Other Maintenance Strategies
While MRO encompasses a wide range of support activities, it’s often confused with specific maintenance strategies like preventive, predictive, and corrective maintenance. Understanding how these approaches fit into a comprehensive MRO strategy can help facility teams optimize both uptime and cost efficiency.
- Preventive maintenance involves scheduled inspections and routine upkeep to reduce the risk of unexpected failures. It’s a proactive way to keep equipment in top shape and avoid disruptions.
- Predictive maintenance takes things a step further, using real-time data and performance analytics to forecast potential issues. Facilities that invest in this approach often see longer asset lifespans and reduced repair costs.
- Corrective maintenance, by contrast, happens after an issue arises or something breaks. While it’s a viable strategy for many low-cost, low-impact items, relying on corrective fixes for more essential assets can increase MRO expenses, contribute to extended equipment downtime, and lead to potential safety and health risks.
Each of these strategies falls under the broader umbrella of maintenance, repair, and operations, but each serves a distinct purpose. The key is knowing when and how to apply them. Blocking all three within a centralized MRO framework leads to the best outcomes for most organizations.
Our preventive vs. reactive maintenance guide provides a more in-depth comparison of these approaches.
MRO Inventory Management and Optimization Tips
Optimizing your MRO strategy starts with the fundamentals: visibility, consistency, and proactive planning. Here are a few essential steps that can help streamline your approach:
- Standardize your MRO inventory management practices. Develop consistent naming conventions, categorize items clearly, and regularly audit inventory levels to reduce confusion and prevent overstocking or shortages.
- Implement a preventive maintenance schedule to reduce unplanned downtime. This ensures equipment issues are caught early, before they lead to larger failures.
- Track key performance indicators (KPIs) tied to maintenance performance, such as repair turnaround times, cost per work order, and equipment uptime. Use this data to spot trends and guide improvements.
- Improve vendor coordination. Programs like vendor-managed inventory (VMI) can help automate restocking and offload routine procurement tasks, freeing your team to focus on higher-impact activities. Strong vendor relationships also support long-term planning and help minimize risk management issues that lead to equipment failures and compliance gaps.
- Adopt inventory management software or a CMMS to centralize records, automate scheduling, and gain real-time insight into asset performance and parts usage.
By following these steps, you improve operational consistency and drive improvement across your maintenance workflow. For details on software that supports this process, visit our facilities management tools overview.
Challenges in MRO and How to Overcome Them
Managing MRO can be complex, especially for teams juggling multiple facilities, vendors, and priorities. Without the right systems in place, even basic tasks can spiral into costly inefficiencies. Here are some common MRO management challenges to look out for and how to address them:
- Data Management Issues: Paper-based systems or disconnected tools can make it difficult to access accurate maintenance records quickly. Moving to digital platforms improves visibility and streamlines reporting.
- Poor Resource Allocation: Teams often spend excessive amounts of time searching for parts, duplicating work, or reacting to last-minute breakdowns. Implementing preventive maintenance and organizing inventory can improve workflow and reduce wasted effort.
- Unscheduled Downtime: Relying on corrective maintenance as a default increases the risk of equipment failures. A proactive approach, powered by predictive maintenance tools, helps prevent problems before they escalate.
- Limited Visibility Across Locations: Without centralized data, it’s hard to prioritize repairs, forecast inventory needs, or evaluate vendor performance. A CMMS platform brings all that into one view.
Overcoming these hurdles takes commitment, but the payoff is worth it, including lower MRO costs, better team performance, and a stronger foundation for continuous improvement.
The Future of MRO Software and Automation
As technology evolves, so does the way organizations manage maintenance, repair, and operations. Industry experts are increasingly turning to advanced MRO software to automate routine tasks, forecast failures, and improve decision-making.
Tools powered by AI and machine learning are helping teams identify maintenance risks before they cause downtime. IoT sensors now feed real-time data into centralized systems, allowing for smarter planning and faster response times. Digital twins have also been a transformative addition to the tech environment, virtual models of physical assets that mirror real-world performance and wear.
These innovations make it easier to optimize repair schedules and address minor issues before they escalate into serious problems, reducing expenses over time. As automation becomes increasingly accessible, data-driven strategies and intelligent systems will define the future of MRO, helping teams operate with greater precision.
Make MRO Work Smarter for You
A strong MRO plan is one of the most effective ways to reduce downtime, extend the useful life of equipment, and improve operational performance across facilities. From managing day-to-day maintenance to preparing for long-term growth, aligning maintenance, repair, and operations processes can lead to measurable improvements across cost, performance, and reliability.
Integrated digital tools like CMMS platforms and vendor-management software make it easier to stay ahead of issues, track MRO supplier performance, and ensure your team has the right tools and materials at the right time. With better visibility and more control, you can reduce MRO expenses, streamline workflows, and keep your operations running smoothly.
Request a demo to learn how to take control of your maintenance operations and see how ServiceChannel can help you build a smarter, more efficient MRO strategy.
MRO supports asset longevity, minimizes downtime, and ensures smooth day-to-day operations.
CMMS software centralizes MRO tasks, automates scheduling, and provides real-time visibility into asset performance and inventory.