What Ben Franklin Can Teach Us About Proactive Facility and Equipment Management
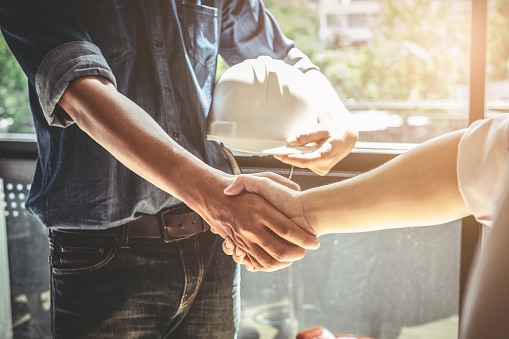
Ben Franklin is attributed with the maxim “an ounce of prevention is worth a pound of cure”. As also the inventor of the eponymous “Franklin Stove,” Ben would have also known that routine maintenance on a piece of equipment like this would prevent a lot of problems down the line. But this is easier said than done for modern facilities managers and their contractors who are responsible for the upkeep of dozens of important equipment and assets that can mean the difference between a business staying open or shuttering for the day (or worse).
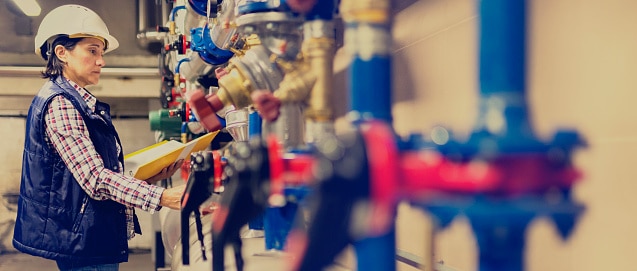
From a pure cost perspective, proactive maintenance is a no-brainer. Emergency repairs demand premium pricing and without the proper strategy in place, just about every facility or equipment issue may be treated as an emergency. So, in this post, we are going to explain the strategies FMs can implement to integrate just the right amount of proactive measures and reactive maintenance to maximize efficiency and reduce costs of operation.
It Starts with Proactive Equipment Maintenance
Professionally maintaining your equipment on a regular basis will help things run smoothly, extend its working life, and avoid costly repairs and replacements. However, moving forward with your preventive maintenance plan can be challenging simply because of the amount of equipment that needs to be tended to, especially across multiple locations.
Identifying preventive work that needs to be done and strategically prioritizing that list is step one. Though costly issues are bound to arise, the goal is to reduce the number of immediate repairs and/or total replacements needed.
Visibility plays a vital role in this plan, which means you need access to key information about your equipment, like work and maintenance history and warranties. This will help to guide your preventive maintenance efforts and ensure the right equipment is serviced at the right time.
Take central air conditioning units for example. They are relied upon heavily during the summer, but there is ample opportunity for you to prevent summertime breakdowns— that will cost you in both repair dollars and in poor customer experiences— if you focus on regular servicing during the winter months.
Filling in the Gaps with Reactive Maintenance
Reactive maintenance is required when a piece of equipment is failing, and its problems won’t be solved on a scheduled and incremental basis. The challenge of planning for reactive maintenance is that it might push you over your budget or limit your ability to stay on track with your proactive maintenance plan.
According to a Schneider Electric report, 55% of the building owners and operators in the United States rely on reactive maintenance programs, the most expensive kind, to care for their equipment. There are instances of reactive maintenance being the only option, like when human-error stops a piece of equipment from working properly or a weather event puts functionality at risk.
Reactive methods are necessary, and they help you fill in the gaps that preventative measures might not account for – but, becoming too comfortable and just rolling with the punches can lead you down a slippery slope.
Reducing costs and balancing our proactive and reactive maintenance efforts go hand-in-hand. Relying on reactive measures is costly and time-consuming. On top of that, the last-minute or rushed repairs might not be as reliable as what you might get when you are proactive and operating according to a plan. If you focus on taking the necessary preventative measures ahead of time, reactive maintenance will be less of a burden.
Finding a Balance and Reducing Costs
Emphasizing planned maintenance as much as possible across locations is a cost-saving measure, but there is a level of balance that comes into play too. Analyzing your asset data and pulling historical insights helps you understand past proactive and reactive maintenance costs. This will allow you to allocate spend between the two more strategically in the future.
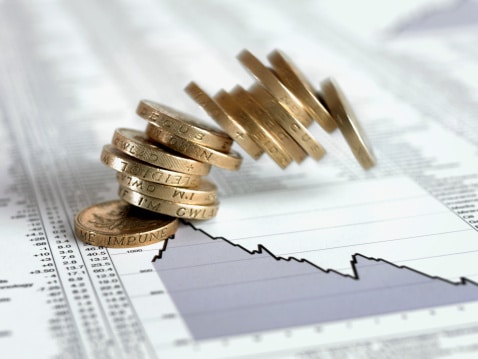
Any contractor that is expected to maintain equipment on a regular basis should also be working with as much data as possible, so that they’re aware of asset histories and can perform the work that will lessen the chances of equipment breaking down in the future.
Taking preventive measures ultimately limits the risk of equipment failure in your facility. In addition, the cost of repairs and revenue loss from equipment-related productivity issues can prove to be a notable roadblock. It’s something that you should be working to avoid through historical data analysis as well as strategic planning and budgeting.
Final Thoughts
Finding equilibrium between proactive and reactive maintenance for your equipment will help balance your budget and limit downtime. Crunching the numbers, analyzing your equipment, and developing a holistic view of the facility is how you put yourself in the best situation possible. These initiatives will be beneficial in both the short and long term, keeping your team of contractors on the same page while painting a clearer picture of what your facility needs to maximize efficiency without wasting money.
Or, as Ben Franklin might have said, “a penny saved is a penny earned.”