How to Enhance Maintenance with Criticality Analysis
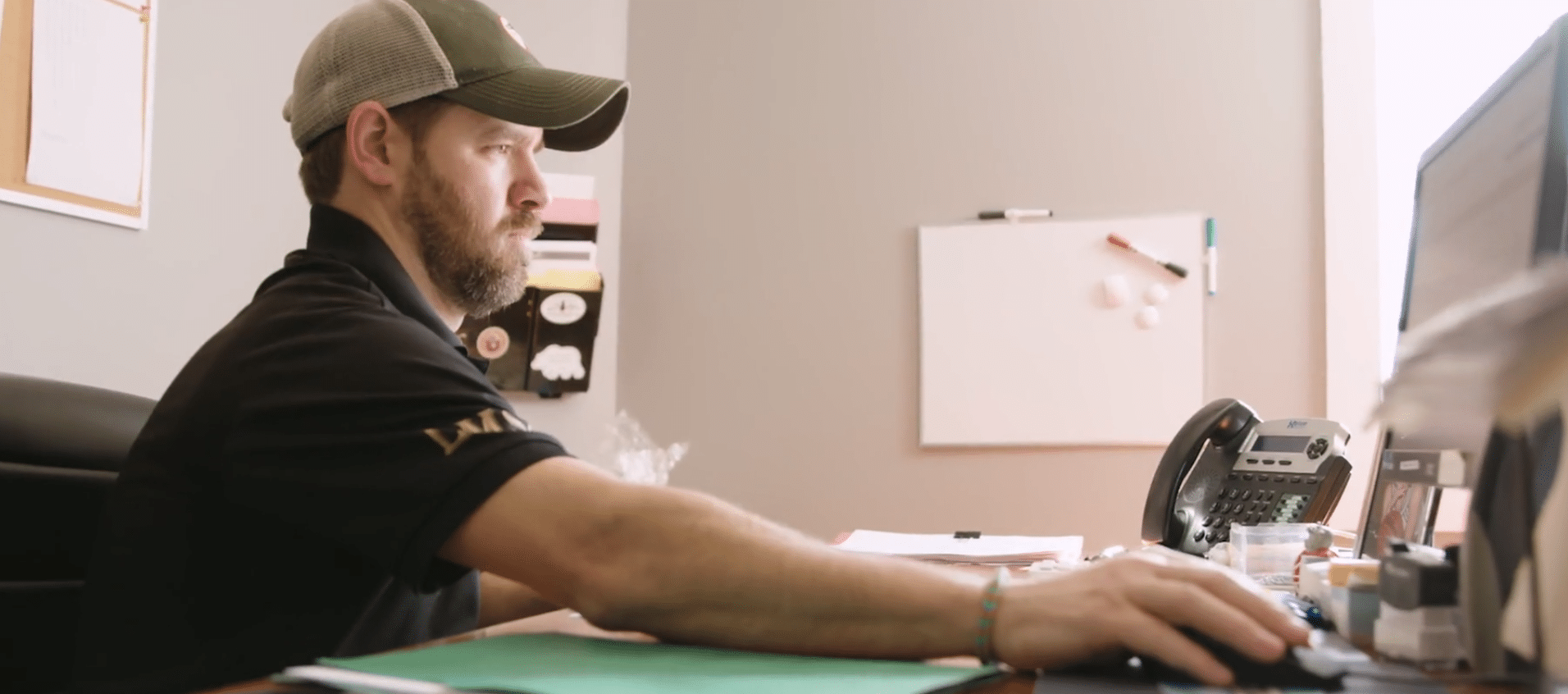
Optimize your maintenance strategy with criticality analysis. Prioritize assets effectively for safety, efficiency, and cost savings in facilities management.
Facilities managers often find themselves in a balancing act — keeping essential systems operational, preventing unexpected failures, and adhering to budget constraints. With a continuous influx of maintenance requests, it’s easy to slip into reactive maintenance cycles, where urgent breakdowns take precedence over proactive planning. This frequently results in higher repair costs, unplanned downtime, and increased pressure on maintenance teams.
Criticality analysis helps prevent these issues by providing a structured approach for facilities managers to prioritize maintenance efforts. By evaluating the importance of each asset, they can focus on what matters most.
Why Preventive Maintenance Isn’t Enough
Even the most effective preventive maintenance programs may fall short. Scheduled maintenance ensures regular servicing, but not all assets require the same level of attention. Some may need frequent checks to prevent failures, while others can operate safely with minimal intervention. A structured ranking system ensures your maintenance teams spend time and resources efficiently.
This guide will walk you through how to implement criticality analysis, from evaluating asset importance to optimizing resource allocation and enhancing risk management strategies. By the end, you’ll have the tools to improve asset reliability, reduce downtime, and make informed maintenance decisions.
Understanding Criticality Analysis and Its Benefits
Effective facilities management software that includes criticality analysis gives you a structured way to evaluate each asset’s importance to your operations, helping you make data-driven maintenance decisions. When equipment fails unexpectedly, it can disrupt operations, increase costs, and put safety at risk. Many facilities managers struggle with inadequate methods to gauge the real impact of asset failures — leading to reactive maintenance approaches that cost more in the long run.
By implementing criticality assessment, your organization can:
- Reduce maintenance costs by focusing efforts on high-risk assets while minimizing unnecessary maintenance on low-risk ones.
- Enhance asset reliability by identifying failure modes early and proactively addressing potential risks.
- Minimize downtime by prioritizing maintenance tasks that prevent major operational disruptions.
For example, consider a facility where a small pump unexpectedly fails. While the pump itself seems insignificant, its failure causes a bottleneck in production, delaying an entire manufacturing line. If a criticality assessment had been performed, the pump’s indirect impact would have been identified, allowing for proactive maintenance before disruption occurred.
Similarly, identifying critical equipment early can prevent costly repairs. A power distribution panel that suddenly fails might cause widespread outages, leading to lost productivity and unexpected emergency repair costs. Criticality analysis ensures that assets like these receive proper attention before failures escalate into costly crises.
Criticality analysis provides a comprehensive understanding of asset risks, allowing your maintenance team to allocate resources strategically and improve overall operational efficiency.
Performing a Step-by-Step Criticality Assessment
Understanding the benefits of criticality analysis enables you to apply the process. A structured assessment helps you determine which assets are essential to operations, allowing you to prioritize maintenance resources effectively.
By identifying high-priority assets, your team can streamline inspections, reduce unnecessary maintenance, and focus on preventing failures where they matter most. This approach minimizes downtime while also optimizing the value of labor and material costs, making maintenance operations more strategic and efficient.
These steps will help you better identify critical assets, assess risk, and assign criticality scores while following industry standards like ISO 55000 and EN 16646 best practices.
Step 1: Asset Identification and Data Collection
Begin by compiling a complete list of all assets within your facility. This includes:
- Mission-critical equipment that directly impacts production or service delivery.
- Support systems like HVAC, electrical, and plumbing infrastructure.
- Ancillary assets that may not be essential but still require upkeep.
Once identified, gather accurate data on each asset, including:
- Operational Role: What function does the asset serve?
- Failure History: How often has it failed, and what were the consequences?
- Maintenance Records: What preventive or corrective actions have been taken?
- Current Condition: Use inspections, predictive maintenance, and sensor data to assess real-time performance.
Why Data Collection Matters
With this data, you can begin conducting criticality analysis, ensuring that your maintenance strategy aligns with operational needs. The accuracy and depth of data collected directly impact the effectiveness of criticality analysis. Real-time condition monitoring provides up-to-date information that enables teams to make proactive decisions instead of relying on historical assumptions. By integrating predictive maintenance tools and IoT sensors, facilities managers can identify performance trends, detect early warning signs of failure, and plan maintenance more precisely.
For example, a real-time vibration sensor on a manufacturing motor can detect irregularities before a failure occurs, allowing for targeted repairs rather than reactive maintenance. Without these insights, the motor might appear to be in normal working condition based entirely on past performance and the operator’s observations.
Using real-time and historical data, your organization can more confidently prioritize maintenance tasks, reduce unexpected failures, and optimize resource allocation, ensuring a cost-effective and operationally sound maintenance strategy.
Step 2: Define Criticality Criteria and Scoring System
Not all assets contribute equally to operations, so defining criticality criteria that reflect their impact is essential. A scoring system helps standardize assessments across your organization.
Common criticality factors include:
- Safety risks: Could failure result in injury or regulatory non-compliance?
- Operational impact: Would downtime disrupt production or essential services?
- Financial consequences: What are the repair or replacement costs?
- Failure likelihood: How often does this type of asset fail?
By establishing a structured equipment criticality analysis process, your team can focus maintenance efforts where they are most needed, preventing unnecessary servicing on low-priority assets.
Defining Criticality Example
A high-pressure boiler in a manufacturing facility might receive a high criticality rating due to safety concerns and high replacement costs. Meanwhile, an office printer would be considered low criticality since its failure has minimal operational impact.
Step 3: Risk Assessment – Probability and Impact
Once you’ve defined criticality criteria, conduct a risk assessment to evaluate failure probability and impact severity. This will help you prioritize which assets require immediate attention.
Risk Assessment Methods:
- Failure Modes and Effects Analysis (FMEA): Identifies potential failure modes and their consequences.
- Risk Matrix: Categorizes assets based on likelihood vs. impact (e.g., high, medium, low).
- Reliability Centered Maintenance (RCM): Evaluates optimal maintenance strategies based on failure risks.
Also, consider how system components interact with one another. Some assets may have low individual criticality but are essential to a larger system. A minor failure in one component could cause cascading issues in mission-critical equipment.
Example of the Importance of Considering Impact
A cooling fan in a data center might seem a low priority, but if it malfunctions, it could overheat critical networking servers, leading to widespread downtime. By incorporating equipment criticality assessment in your risk evaluation, your team can better predict how failures will impact operations.
Step 4: Calculate the Asset’s Criticality Score
With risk data in place, assign each asset a criticality rating. Many organizations prioritize maintenance tasks using a numerical rating system (e.g., 1-10) or weighted scoring models.
Criticality Score Calculation Example:
A backup generator supporting emergency hospital operations might score 9/10 due to high operational importance and severe consequences of failure.
Meanwhile, a forklift in a warehouse might score 4/10 — important but with redundancy options in place.
By following these steps, your maintenance team can:
- Prioritize maintenance tasks based on criticality scores.
- Optimize resource allocation to focus on high-impact assets.
- Improve asset reliability with data-driven maintenance strategies.
Implement criticality analysis today and optimize your asset management. Consider ServiceChannel for all your facilities maintenance needs.
Using The Criticality Matrix and Applying Your Results
Once you understand how criticality analysis prioritizes maintenance, applying those insights is the next step. A criticality matrix provides a structured way to categorize assets based on their risk of failure and operational impact. By mapping assets into high, medium, or low criticality tiers, your organization can streamline maintenance planning, allocate resources efficiently, and reduce costly downtime.
A well-structured asset criticality assessment enables maintenance teams to direct their efforts toward assets with the greatest operational impact. By ranking assets according to business importance and assigning risk probability, organizations can avoid wasting resources on low-priority maintenance while ensuring that high-risk equipment remains operational. This approach enhances efficiency and strengthens decision-making, allowing facilities managers to allocate labor and materials strategically.
How to Use a Criticality Matrix
A criticality matrix ranks assets using two key factors:
- Likelihood of Failure: How often an asset is expected to fail based on historical data and condition monitoring.
- Consequence of Failure: The impact of failure on operations, safety, and costs.
By plotting these factors on a matrix, you can classify assets into three levels:
- High Criticality: Assets that pose significant safety risks, cause major disruptions, or lead to high financial losses if they fail. These require frequent monitoring and preventive maintenance.
- Medium Criticality: Assets with moderate operational importance can be managed with scheduled inspections and condition-based maintenance.
- Low Criticality: Assets with minimal operational impact, where maintenance can be deferred or performed reactively.
Do’s and Don’ts of Criticality-Based Maintenance Prioritization
A criticality matrix is only effective when applied correctly. Keep these best practices in mind:
Do’s:
- Prioritize preventive maintenance for high-criticality assets to avoid unplanned failures.
- Use data visualization to communicate asset risk levels clearly to stakeholders.
- Integrate criticality insights into your CMMS software for automated scheduling and tracking.
Don’ts:
- Don’t ignore low-criticality assets entirely. Schedule periodic checks to prevent gradual failures.
- Don’t base decisions solely on criticality scores. Consider factors like compliance, redundancy, and repair costs.
- Don’t treat this as a one-time process. Update your analysis regularly as asset conditions and business needs evolve.
Applying Criticality Analysis to Maintenance Planning
Facilities managers can optimize maintenance schedules and resource allocation using a criticality matrix. Consider these examples:
A large manufacturing plant uses criticality analysis to identify that a key conveyor system is at high risk due to past failures disrupting production. The team schedules predictive maintenance and real-time condition monitoring to prevent unexpected shutdowns.
A corporate office assesses its HVAC system and determines that while it’s crucial for employee comfort, a failure wouldn’t halt operations. The team moves to scheduled maintenance every six months instead of every three.
Including criticality analysis can improve operational efficiency, reduce unnecessary maintenance costs, and keep your most critical equipment operational.
Enhance Your Operations with Criticality Analysis Through ServiceChannel
Implementing criticality analysis transforms the way your organization manages facilities maintenance. By systematically evaluating asset importance, prioritizing high-impact equipment, and optimizing resource allocation, you can reduce downtime, control costs, and improve overall operational efficiency.
When your maintenance team identifies the most essential equipment, they can make informed decisions that prevent expensive failures and prolong asset lifespan. Instead of depending on reactive maintenance, you adopt a proactive strategy that ensures business continuity and operational stability.
With a structured criticality assessment, your team will feel:
- Confident in making data-driven maintenance decisions.
- Empowered to allocate resources effectively.
- Assured that high-priority assets receive the attention they need.
- Informed about potential risks and their impact on operations.
- Prepared to communicate critical asset insights to stakeholders.
ServiceChannel easily integrates a systematic criticality analysis approach into your maintenance strategy. Our enterprise asset management solutions provide the tools to analyze asset importance, streamline workflows, and automate maintenance planning. You can ensure long-term asset performance and cost savings by mitigating operational risks and improving maintenance efficiency.
Let’s Get Started
Start prioritizing your maintenance tasks based on accurate asset rankings.
Request a demo of ServiceChannel today!