Cooling Tower Maintenance Checklist
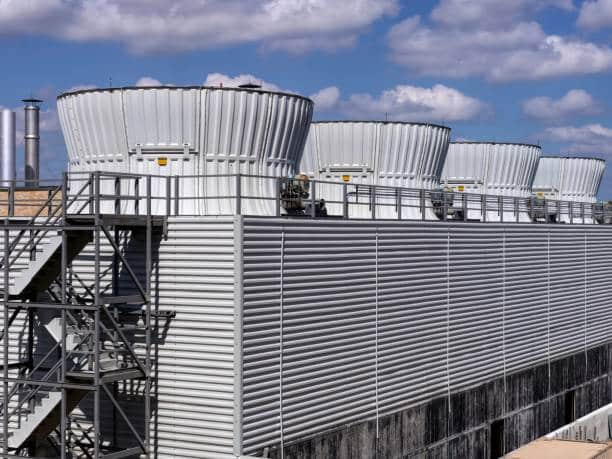
Explore our cooling tower maintenance checklist for expert tips and practices. Extend your equipment’s lifespan and ensure optimal performance.
Cooling towers are an essential piece of HVAC equipment for large commercial buildings. Preventative maintenance is crucial for keeping a cooling tower system running at peak efficiency and avoiding costly repairs. We will cover this critical piece of HVAC maintenance and guide you through creating an effective cooling tower maintenance checklist to ensure the proper operation of your cooling tower systems.
ServiceChannel offers helpful advice on different types of preventive maintenance for facilities and assets.
Understanding Cooling Tower Systems
Cooling towers help to reduce the temperature of an indoor environment by drawing any heat from condensation water and expelling the heat outside. The tower then recirculates the cooled water into chillers to cool a facility’s interior.
Cooling tower maintenance is critical for all kinds of industries. Even hospitality facilities incorporate HVAC cooling towers into their hotel maintenance routines. Facilities typically use one of the following types of cooling towers in their HVAC systems:
Counterflow
A counterflow cooling tower system works by spraying pressurized water from above onto incoming air traveling upwards from below. The air absorbs heat and discharges it into the outdoor air while the water flows downward into a chiller to cool the interior air.
Crossflow
A crossflow cooling tower system uses gravity flow to drop water vertically from above while air moves horizontally across the water. Fan blades force the warm air into the outdoor air while the cooled water feeds into the chiller.
Open Loop Cooling Tower
In an open loop cooling tower system, water passes through a filter medium and falls into a chamber below, through which air flows. The water makes direct contact with the air, which draws heat from the water and exits through a top vent, while the cooled water recirculates back into the chiller.
Closed Loop Cooling Tower
A closed-loop cooling tower system keeps the air and water separate as the water passes through the filter medium and air flows around it to draw out the heat.
Troubleshooting Cooling Tower Issues
Cooling towers come with their own unique set of issues to look out for. Poor heat transfer, reduced efficiency, water leaks, and microbial contamination are a few common issues you may encounter. Here are some tips to help keep your cooling tower running efficiently and effectively.
Creating a Cooling Tower Maintenance Checklist
Establish cooling tower upkeep protocols and create a maintenance checklist to lay out detailed steps. These steps will help you create a cooling tower maintenance checklist that suits your facility’s needs.
1. Understand Cooling Tower Type
Identify and itemize the types of cooling towers your company utilizes. Tailor a preventative maintenance checklist to fit each type of cooling tower your organization uses.
2. Collect Manufacturer’s Guidelines
Review the manufacturer’s recommendations for cooling tower maintenance on their specific equipment. Individual tower maintenance needs may vary between different models of cooling towers.
3. Cleaning Cooling Tower
Regardless of the type of cooling tower a facility employs, cleaning is an essential maintenance task. Remove debris buildup, algae, and scale accumulation from the tower’s fill material, cold water basin, drift eliminators, and other interior cooling tower components.
4. Water Quality Inspection
Routinely examine, test, and treat the water as part of cooling tower maintenance. Regular tower water treatments help prevent scale, corrosion, and biological contaminants from accumulating in the cooling system.
5. Fan Maintenance
Every cooling tower maintenance checklist should include fan inspections and upkeep. Ensure fan blades, motors, belts, and bearings are properly lubricated.
6. Check Drift Eliminator
Drift eliminators help prevent water from discharging into the outdoors with the air. Check for damaged or clogged eliminators, which can obstruct water flow and reduce cooling tower efficiency.
7. Test Control Systems
Ensure proper operation of control systems, sensors, and valves. Repair or replace any damaged or worn components.
8. Inspect the Tower Structure
Examine the internal and external structural components for signs of damage or wear. Gaps in the body of a cooling tower can allow the introduction of debris and biological contaminants.
9. Sample for Legionella
Legionella is a harmful bacteria that thrives on water droplets and can be introduced into a building’s environment through HVAC systems. Regularly sample cooling tower water and test for Legionella.
10. Keep Detailed Records
Diligently record all cooling tower maintenance activities. Track dates, personnel, and completed tasks. Maintenance records include inspections, test results, repairs, and water treatment adjustments.
Establish a Regular Maintenance Schedule
A regular cooling tower maintenance schedule ensures consistent upkeep and optimal equipment performance. These steps will help guide you through setting up a plan for proper cooling tower maintenance, as well as other critical facility assets.
1. Create an Inventory of Assets
Itemize and catalog all essential facility assets and equipment. A cooling tower inspection checklist will often include attached utilities and connected pipes.
2. Prioritize Criticality & Usage
Assess the impact of each asset and establish a hierarchy of importance. Equipment that’s essential to operations and safety should take the highest priority. Many industries rely on the environmental control of HVAC, and cooling tower maintenance will be high on their priority lists.
3. Identify Maintenance Triggers
Determine which situations and asset conditions trigger preventative vs. reactive maintenance. Reduced efficiency, odd sounds, and strange smells are some occurrences that commonly trigger cooling tower maintenance.
4. Develop an Asset Schedule
Design a preventative maintenance schedule and task list tailored to each of your assets. While cooling tower maintenance tasks may vary between types of cooling towers, they all benefit from weekly, monthly, and annual routine maintenance.
5. Use PM Software
Facility management and preventative maintenance (PM) software can streamline many high-level maintenance tasks. A robust preventive maintenance platform such as ServiceChannel can tremendously help with routine cooling tower maintenance scheduling and history tracking. A PM platform also provides condition monitoring and powerful analytics, which can examine data and recommend predictive maintenance tasks before issues present themselves.
Benefits of Preventive Maintenance for Cooling Towers
Monitoring and inspecting all cooling tower components, from the fan blades to drift eliminators, ensures you’ll have ample warning of any impending cooling tower problems. Routine cooling tower maintenance safeguards against breakdowns and optimizes energy consumption. Organizations with conscientious preventative maintenance programs tend to enjoy longer equipment life spans and greater operational efficiency, which leads to noticeable cost savings for the company.
Ensure Longevity with Cooling Tower Maintenance
Heating and cooling are staple technologies in facility management and maintenance, and innovations emerge daily. Look at ServiceChannel’s take on sustainable thermoelectric cooling to glimpse the future of HVAC and refrigeration.
ServiceChannel is a top-notch facility maintenance and management software solution that empowers organizations to monitor and maintain their assets more easily. Follow the checklist above to help ensure your cooling towers run efficiently and reliably, and explore the ServiceChannel software platform to take on many of your maintenance tracking and scheduling tasks.