Common Causes of Equipment Failure
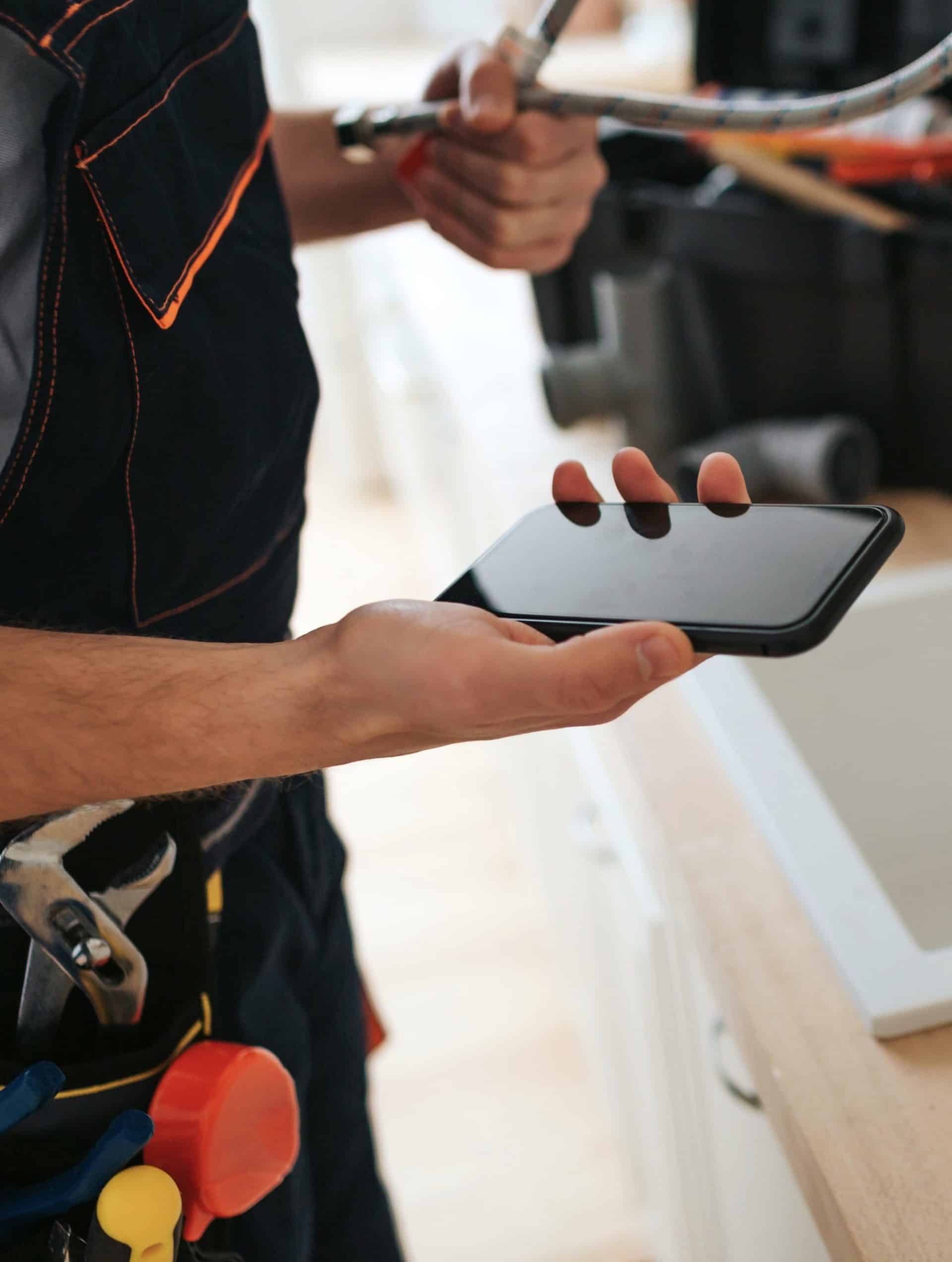
Explore the most common causes of equipment failure, best practices to avoid breakdowns, and partnering with ServiceChannel for equipment management.
Equipment failures are inconvenient. They can bring your productivity to a halt and may have health and safety implications. Additionally, frequent machine failures can expedite an asset’s natural breakdown and significantly reduce its useful life. As a result, you spend more money and get less use out of your equipment.
For these reasons, it’s important to know the warning signs of impending equipment failures, what causes them, and how to prevent them.
Understanding Equipment Failure
Equipment failure refers to the breakdown or malfunction of any asset in your regular operations. Such failures may lead to costly downtime and negatively affect production. As a result, you may face delivery delays that impact client satisfaction.
Preventing equipment failures ensures smoother operations and higher profitability. That’s because less machine failure means more productive staff and maximum operational efficiency.
What is Preventive Maintenance?
Preventive maintenance involves regular maintenance operations that occur to prevent equipment breakdowns. There are various types of preventive maintenance, such as time-based, usage-based, and predictive maintenance. This proactive approach aims to identify issues before they lead to equipment failure.
The difference between this type of proactive vs. reactive maintenance strategy is based on whether or not asset failure occurs before equipment maintenance takes place. Preventive maintenance occurs based on defined maintenance schedules regardless of whether or not equipment failure occurs. Reactive maintenance only occurs after machine failure.
Human Errors That May Cause Equipment Failure
1. Improper Operations
An operator error may dislodge a critical equipment component, leading to equipment failure. Improper usage may also refer to poor storage conditions, incorrect equipment operating procedures, or neglect of safety procedures.
2. Lack of Proper Training
Incorrect operations aren’t usually a sign that your operator is neglectful. It’s more likely they were unaware they were improperly using your asset. Therefore, adequate operator training is a vital part of preventing machinery failure.
With adequate training, proper operation is more likely, which can prevent equipment downtime. Machine operator training and basic troubleshooting may also be a requirement for certain assets.
3. Overloading Equipment
Overloading equipment means subjecting it to loads or stresses beyond its designed capacity. Such equipment usage can lead to component breaks that may cause complete failure of the machine. For this reason, it’s critical to ensure that machine operators know exactly how much each asset can handle.
4. Over-Maintenance
Excessive maintenance can be just as harmful as a lack of maintenance. When equipment is serviced too frequently or with unnecessary tasks, it causes wear and tear that can lead to equipment failure rather than preventing it.
5. Inadequate Lubrication
Lubrication is essential for machinery with moving parts. Inadequate lubrication can cause friction and heat, leading to wear and tear and equipment failure. Lubrication must be part of your preventative maintenance strategy to avoid this situation.
Equipment Conditions That May Cause Equipment Failure
1. Outdated Technology
Older equipment may become obsolete and more prone to intermittent failure. When equipment becomes obsolete, it’s more difficult to find replacement parts for it, which makes it harder to maintain. Additionally, older equipment is much less energy-efficient, so it will likely inflate your utility bills.
2. System Malfunctions
System malfunctions result from internal failures within equipment, such as electrical or mechanical faults, software bugs, or control system problems. There’s a chance that malfunctions result from human error and improper operation, but this is not always the case.
3. Natural Wear and Tear
Aging equipment naturally wears down over time, especially with frequent usage. Natural wear and tear is one of the most common causes of equipment failure because it will inevitably happen to every asset. However, you can extend your assets’ lifespans with proper equipment maintenance and operating procedures.
4. Overheating
Overheating is often caused by prolonged operation or poor ventilation. It can lead to thermal stress, damaged components, and failure. Maintenance managers and equipment operators can easily prevent unplanned downtime caused by this issue in their daily work simply by gauging the asset’s temperature.
5. Wiring and Connection Problems
Issues with electrical wiring, connections, and equipment components can cause electrical faults that lead to failure. Aging equipment is especially prone to such issues due to its natural wear and tear. Therefore, double-checking older equipment for these problems is vital to your proactive maintenance strategy.
External Factors That May Cause Equipment Failure
1. Contamination and Corrosion
Contamination involves foreign substances entering equipment, while corrosion results from chemical reactions. Both risks can decrease equipment reliability and potentially lead to breakdowns. Often, the severity of the issue varies based on the substances or chemicals involved.
2. Environmental Stress
Harsh environmental conditions, such as extreme temperatures, humidity, or exposure to the elements, can wear down equipment and contribute to failure. Therefore, it’s essential to highlight proper storage conditions in your preventive maintenance plan.
3. Air Quality and Pollution
Poor air quality can introduce particulate matter and chemical pollutants that degrade equipment and impact reliability. As such, your maintenance technicians must observe the infrastructure surrounding your asset, not just the asset itself.
4. Chemical Spills and Leaks
Accidental chemical spills or leaks can damage equipment by corroding or contaminating its components. Sometimes, seemingly harmless substances, like water, can cause equally significant damage to the equipment. Spills and leaks are especially a risk for any electrical equipment.
5. Pests and Wildlife
Pests and wildlife can interfere with equipment and create blockages that lead to operational issues and failure. Ensure you have taken the proper precautions to prevent animals from entering or tampering with your equipment. If you store your equipment outdoors, try covering it with tarps for protection.
Best Practices to Avoid Equipment Failure
1. Monitor Equipment Condition
Monitoring equipment condition involves regularly assessing the state of your machinery and systems. Follow a specific planned maintenance guide to ensure that your maintenance professionals are monitoring your equipment accordingly.
2. Leverage Condition-Based Maintenance (CBM)
Condition-based maintenance (CBM) can help optimize maintenance efforts by performing tasks only when necessary. It’s also a great strategy to help you avoid performing too much maintenance. Compare preventive vs. predictive maintenance plans to determine the best way for your facility to gauge equipment maintenance needs.
3. Avoid Unnecessary Maintenance Tasks
By avoiding unnecessary maintenance, you reduce the likelihood of introducing errors or causing additional wear. Set a strategic maintenance schedule and use maintenance management software that outlines your maintenance history to gain insights into when you last serviced equipment to prevent redundant tasks.
4. Upgrade Outdated Equipment
Upgrading outdated equipment to newer, more advanced models can enhance performance, reduce the risk of breakdowns, and often offer energy-efficient and cost-saving benefits. At a certain point, a particular asset may cost more to maintain than buying a new one. This situation is a clear sign that it’s time for an upgrade.
5. Implement Preventive Maintenance Strategies
Implementing a proper preventive maintenance plan will significantly reduce emergency maintenance and equipment breakdowns. With preventive maintenance, you can address potential issues before they lead to machine failures or higher repair costs.
Partner with ServiceChannel for Resilient Equipment Management
You will always need a healthy amount of equipment maintenance to keep your assets working at their intended performance. However, you can reduce equipment maintenance costs with the right strategy.
ServiceChannel’s maintenance management software can be an integral part of that strategy. Our tool allows for flexible scheduling so you can avoid over-maintenance while keeping your preventative strategy in place. We also integrate with internet-connected sensors to identify impending trouble before it escalates.
Contact us for a free demo to see more.