Chiller Maintenance Checklist
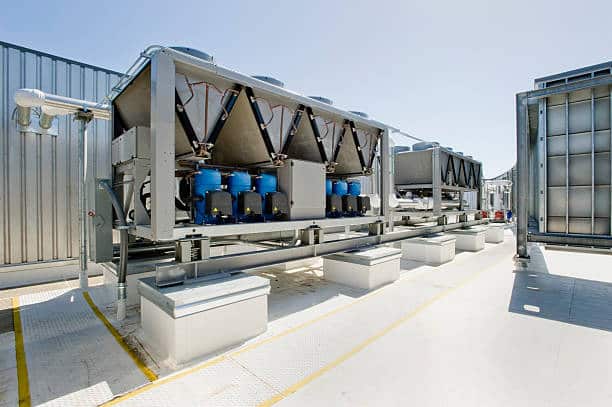
Utilize our chiller maintenance checklist. Learn the importance of regular upkeep, best practices, risks, and the benefits of preventive maintenance.
Regular maintenance tasks are important for all types of equipment. Although chillers are generally self-reliant, following the right preventive maintenance checklist for their needs will ensure consistent, optimal operation. After all, no machine can be fully self-reliant without human help.
If your facility uses industrial chillers, our chillers maintenance checklist will be helpful. Here is what to know about preventive chiller maintenance to keep yours running at peak performance.
How Chillers Work
Many industrial processes require chillers. That’s because chillers help keep sensitive equipment at the right temperature, ensuring maximum efficiency and preventing overheating. Maintaining consistent operating temperatures contributes to the longevity and reliability of all equipment.
Chillers remove unwanted heat from process water or air via a vapor-compression or absorption refrigeration cycle. The heat then transfers to the air outside. Then, the chilled water or air cools down the target area.
The key components of most chillers are the evaporator, compressor unit, condenser, compressor oil and filter, and expansion valve. The evaporator takes in the heat from the water or air. Then, the compressor increases the temperature and pressure of the refrigerant vapor. Finally, the condenser fans release the absorbed heat outside. The expansion valve regulates the flow of refrigerant from the condenser coils to the evaporator.
Types of Chillers
Air-Cooled
Air-cooled chillers rely on fans instead of process water for heat transfer. Air-cooled chillers are suitable for facilities where water availability is limited. They are also typically smaller, making them ideal for space limitations. However, air-cooled chiller systems are less efficient in a hot or humid climate.
Water-Cooled
Water-cooled chillers use water to absorb heat from the refrigerant and are typically more efficient than air-cooled chillers. Water-cooled chillers are usually preferable in large industrial settings for their efficiency and ability to maintain performance despite hot or humid environmental conditions.
Evaporative Condensed Chillers
Evaporative condensed chillers use the cooling effect of water evaporation to lower the temperature of the refrigerant. This type of chiller is particularly effective in hot, dry climates where the evaporation process can significantly reduce the temperature of the cooling medium.
They are also more energy-efficient, which makes them ideal for facilities looking into sustainable refrigeration options.
Absorption Chillers
Absorption chillers use heat to generate a cooling effect, setting them apart from chillers that rely on mechanical compression. This type of chiller typically runs on natural gas, steam, or hot water. They are highly efficient but come with higher upfront costs.
Risks of Neglecting Chiller Maintenance
Like all other assets, regular maintenance ensures chiller efficiency. An unreliable cooling system puts all the assets that need temperature control at risk. For this reason, it’s critical to prevent unexpected downtime. Chiller downtime can lead to a domino effect across other equipment.
Poorly performing chillers will also consume more energy than they should. This additional energy consumption will increase costs and lead to additional wear on your chiller.
Creating a Chiller Maintenance Checklist
1. Gather Manufacturer’s Guidelines
Collect maintenance guidelines and recommendations from the chiller’s manufacturer for specific maintenance needs. Tailor your chiller maintenance checklist to these recommendations.
2. Cleaning Condenser and Evaporator Coils
Removing dirt, debris, and scale buildup optimizes heat transfer efficiency. Make sure you train all maintenance personnel to clean your industrial chiller without causing damage to its components.
3. Lubricate Moving Parts
Applying lubrication to bearings, motors, fans, and other moving components reduces friction and wear. Poor lubrication also increases the risk of substandard output.
4. Check Refrigerant Levels
If necessary, testing refrigerant levels and topping them up ensures optimal chiller performance. Make sure any refrigerant you use follows any required CARB refrigeration standards.
5. Inspect Electrical Components
Test electrical connections, controls, sensors, and safety devices for proper operation. Proper operation ensures chiller system efficiency and prevents workplace accidents.
6. Test Water Quality
If your system uses chilled water, monitor water quality parameters and chemical treatment levels in all water inlets. Doing so prevents scale, corrosion, and microbiological growth.
7. Calibrate Temperature
Check setpoints and calibrate temperature and pressure controls as needed for optimal efficiency. Adjust controls based on the season, like you do with your HVAC maintenance checklist. The summer months will likely need more cooling than the winter.
8. Inspect Insulation and Seals
Check insulation integrity and seals to prevent heat loss and air leakage. It’s also important to check the chiller’s refrigerant container to avoid refrigerant leaks.
9. Perform Vibration Analysis
Performing vibration analysis on motors, compressors, and other rotating equipment helps detect potential issues early. Excessive vibration could indicate a misalignment between the motor and the compressor or other components, among other problems. Inspect motors to verify whether that’s the issue if you detect excess vibration.
10. Test Safety Systems
Test safety interlocks, alarms, and emergency shutdown procedures to ensure compliance with safety regulations. If you find issues, do not let staff operate the chiller until you resolve them.
Preventive Maintenance Best Practices
Keep Detailed Logs
Maintain a detailed and reliable maintenance log that includes all necessary information, like flow rates, operating temperatures, pressures, and fluid levels. This log will ensure consistency in maintenance tasks and simplify chiller machine maintenance for all technicians.
Remote Monitoring Systems
Implement remote monitoring systems to support daily logs on machinery. These systems can automate insight reports and provide real-time diagnostics on your industrial chiller system. Checking on this system can be part of your overall industrial chiller maintenance checklist.
Chiller Safety Controls
Understand and maintain chiller safety controls to protect the cooling system and your employees from harm. These controls include capacity controls, refrigerant flow controls, and other safety measures.
Benefits of Preventive Maintenance for Chillers
Regular maintenance can decrease your potential chiller maintenance costs. While that may sound counterintuitive, it’s because industrial chillers are less expensive to maintain when they’re well-cared for. An industrial chiller that exhibits efficient operation won’t wear down as quickly.
Following the correct industrial chiller maintenance checklist also ensures proper heat transfer when needed. If your heat exchanger breaks unexpectedly, it could lead to problems for all assets that require cooling and additional equipment downtime.
An inefficient chiller condenser coil will also increase the amount of energy that your HVAC system uses. Your industrial chiller will have to work harder to increase thermal resistance. By contrast, efficient chiller operation saves on your utility bills and promotes sustainability.
Manage Chiller Maintenance Processes with ServiceChannel
Chiller maintenance is a beneficial addition to a hotel maintenance checklist or any other facility’s maintenance checklist if equipment needs cooling. ServiceChannel provides preventive maintenance software that helps you keep your maintenance program organized. With our tool, you can more easily prevent substandard output for all of your assets across the heating and cooling seasons.