3 Tips for Dealing with Facility Management Budget Cuts
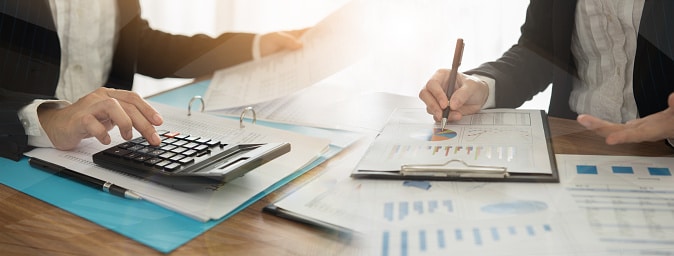
A recent Forbes survey of nearly 600 senior executives uncovered some interesting insights on the topic of digital transformation. In terms of top business priorities, the survey found that revenue growth was number one, followed closely by cost cutting. In today’s heavily automated, digitally-driven business environment, it’s no surprise that corporations are starting to scrutinize the “legacy” ways of doing things – and operating costs are usually the first to be reviewed.
Even in the best of times, managing tight budgets has been a necessity for almost all facilities managers at some point during their career. And as businesses become even more digital, the pressure to do more with less will only intensify. FM teams should not be too surprised when budget makers propose drastic changes.
That being said, the need to manage tight budgets can drive nimble facilities teams to be more resourceful, increasing creativity and accelerating the adoption of new technology. In addition, FMs who become stewards of their corporate budgets can add tremendous value for their organization long-term, improving overall efficiencies. Knowing your ‘must-haves’ and being able to prove those needs to stakeholders is a good place to start.
The following tips are designed to help facilities managers strategically cope with budget cuts – since it’s those seemingly small adjustments that will ultimately have a substantial impact on year-end outcomes.
1. Streamline Your Preventive Maintenance Program
A maintenance program that isn’t strategically thought-out well in advance of the new fiscal year is bound to cost more money than it should. A program that is heavily skewed by only ‘reactive’ work tends to be expensive because of emergency repair needs as well as the opportunity costs of downed assets. As we all know, emergency repairs (or, worse, a replacement) are never cheap. Yet some FMs may feel so much pressure to save money when budgets are tight that they are tempted to neglect preventive repairs, operating under the assumption that the asset is “functional enough for now.” Unfortunately, this approach will only lead to more expenses in the long run.
When faced with budget cuts, facilities managers should instead shift their focus towards preventive maintenance. A comprehensive strategy will consider costs for planned, corrective, and emergency maintenance, some of which will take place on a recurring basis – such as regular HVAC filter cleanings or periodic lightbulb replacement.
Planning maintenance strategically is easy to budget towards since it can be predicted with a high degree of accuracy – especially when you have software in place to track assets, historical data, and performance. A Service Automation platform, for instance, serves as a centralized hub through which FMs can track and store data on all relevant assets, schedule and approve work orders, maintain regulatory compliance, and seamlessly manage invoices and payments.
While Service Automation software requires a certain amount of up-front investment, the long-term value outweighs the cost, especially when considering the potential improvements in efficiency. The longer your assets hold up, the less money you’ll spend overall – and assets that you carefully track and maintain will hold up far past their warranties. Of course, you may be unable to keep up with yearly, quarterly, or monthly maintenance on all assets, and you may be required to reprioritize those that are most critical to your organization’s day-to-day functioning.
Maintaining HVAC and boilers should always be a top priority: On a very hot or very cold day, a breakdown of either of these systems could present a major issue. FMs are pressured to fix these problems immediately, which is always more expensive. HVAC systems and boilers should be thoroughly tested on a regular basis, with specific frequency depending upon location and usage. On the other hand, some brands might choose to defer certain non-critical or aesthetic repairs (like a new coat of paint) when budget cuts are imminent. Of course, this can be challenging, too – it will depend on the type of customer experience your brand is trying to uphold.
2. Focus on Energy Efficiency
Sustainable and energy-efficient design and equipment can have a big impact on year-over-year costs. The changes you make don’t have to involve expensive upgrades – small changes, such as installing LED light bulbs, can be very meaningful. While it might be another project to manage, it’s likely to be worth your while: Incandescent bulbs consume more than six times as much electricity as LED bulbs. It only takes a quick calculation to figure out your potential savings after the switch.
Depending on how your facility is used and when it is occupied, you can implement a more efficient lighting system that operates under an “economize mode” during off-hours, whenever the property is minimally occupied. While perimeters, entrances, and main drives should always be well-lit at nighttime, other parts of your buildings may not need it. When possible (or if there’s any wiggle room leftover in your budget), set up strategic zones, motion sensors, and timers to maximize lighting efficiency 24/7.
Of course, lighting isn’t the only facilities energy hog: In a restaurant environment, roughly 30% of electrical consumption is used by refrigerators – and in many cases, refrigerators are set to far lower temperatures than necessary. Cut costs by making sure refrigerators are consistently set between 37- 40 degrees F and freezers between 0 – 5 degrees F. If possible, implement smart sensors that track temperature fluctuations over time and ensure refrigerators are functioning properly: For every degree difference in temperature, you’ll add an additional 1.5% to your energy bill. If you don’t have the budget to invest in sensor technology, some quick manual checks can catch issues before they grow larger and lead to lost product.
While budget cuts make it difficult to spend money on brand new, energy-efficient windows or roofing, there are plenty of practical ways to reduce energy expenditure without swapping out the assets and equipment you already have. Even adjusting thermostat set points to align with occupant schedules and seasonal fluctuations can dramatically cut costs and free up resources for other areas of your FM program. Plus, creative fixes and adjustments will only make your program (and your efforts) more valuable to key stakeholders in your organization.
3. Set the Right Business Requirements for Dispatching Service Providers
When faced with budget cuts, it’s tempting to throw in the towel and look for the provider with the lowest rates, or outsource the responsibility altogether. This, however, can become a costly mistake – especially when utilizing an outsourcing model, which can be fraught with massive hidden costs.
Dispatching technicians who are either inexperienced, have a poor reputation, or are ill-supplied with the parts, knowledge, and resources you need will be a poor choice in the long run. Providers with the lowest rates don’t necessarily cost you less – they might take longer to complete the repair, meaning your business will suffer a longer stint of downtime. Plus, lower-cost providers may have inexperienced technicians, meaning it’s far more likely that the equipment will experience another breakdown only a week or two later. When this happens, you’ll end up paying for repeat services – or even an entire replacement of the asset. Two to three visits by an inexperienced, inexpensive laborer will far surpass the cost of one visit by a seasoned professional.
To avoid this, FMs need to create detailed business requirements for their providers to only dispatch skilled, experienced technicians to your site. These requirements might involve specific mandatory licenses, distance from work order location, membership within certain professional organizations, and years of experience in the field. With a machine learning-enabled work order automation platform, you can put in place controls to ensure you are only billed for the rates that you have agreed to – while also ensuring your decision to approve the work leverages insights based on historical data.
In addition, organizations that employ Service Automation technology will be better able to communicate repair and maintenance timelines to their locations with optimized request workflows. When everyone is on the same page about the scope of a project, the potential costs, and likelihood of overtime, locations can more easily choose the right priorities for service requests – thereby saving you from paying overtime charges. Plus, with troubleshooting scripts built in to the platform, a significant number of service calls can be avoided from the get-go.
Final Thoughts
One of the most obvious outcomes of digital transformation has been the increase in budget scrutiny toward legacy operations. FM teams who fail to track expenses early enough – or who fail to make adjustments to maintenance programs and overall strategy throughout the course of the year – are likely to succumb to budgetary failure.
To avoid this, a platform with sophisticated real-time reporting and business intelligence to track assets and maintenance costs is incredibly important. For most FMs, a traditional pen-to-paper or even just an Excel-based method won’t suffice. After all, there’s no shortage of data available – and smart FMs know how to leverage it strategically in order to improve core decision-making processes.
Of course, there are plenty of little things that can be done to reduce costs and work within ever-tightening budgets. Anything from turning off vending machine lights at night to checking refrigerator temperatures, changing out filters, or optimizing when to switch on or off your HVAC systems will have an impact. These actions, along with a strategic preventive maintenance plan based on data-driven insights, will ensure your program succeeds even under the most difficult of circumstances.