The Different Types of Work Orders That Facility Managers Need to Know
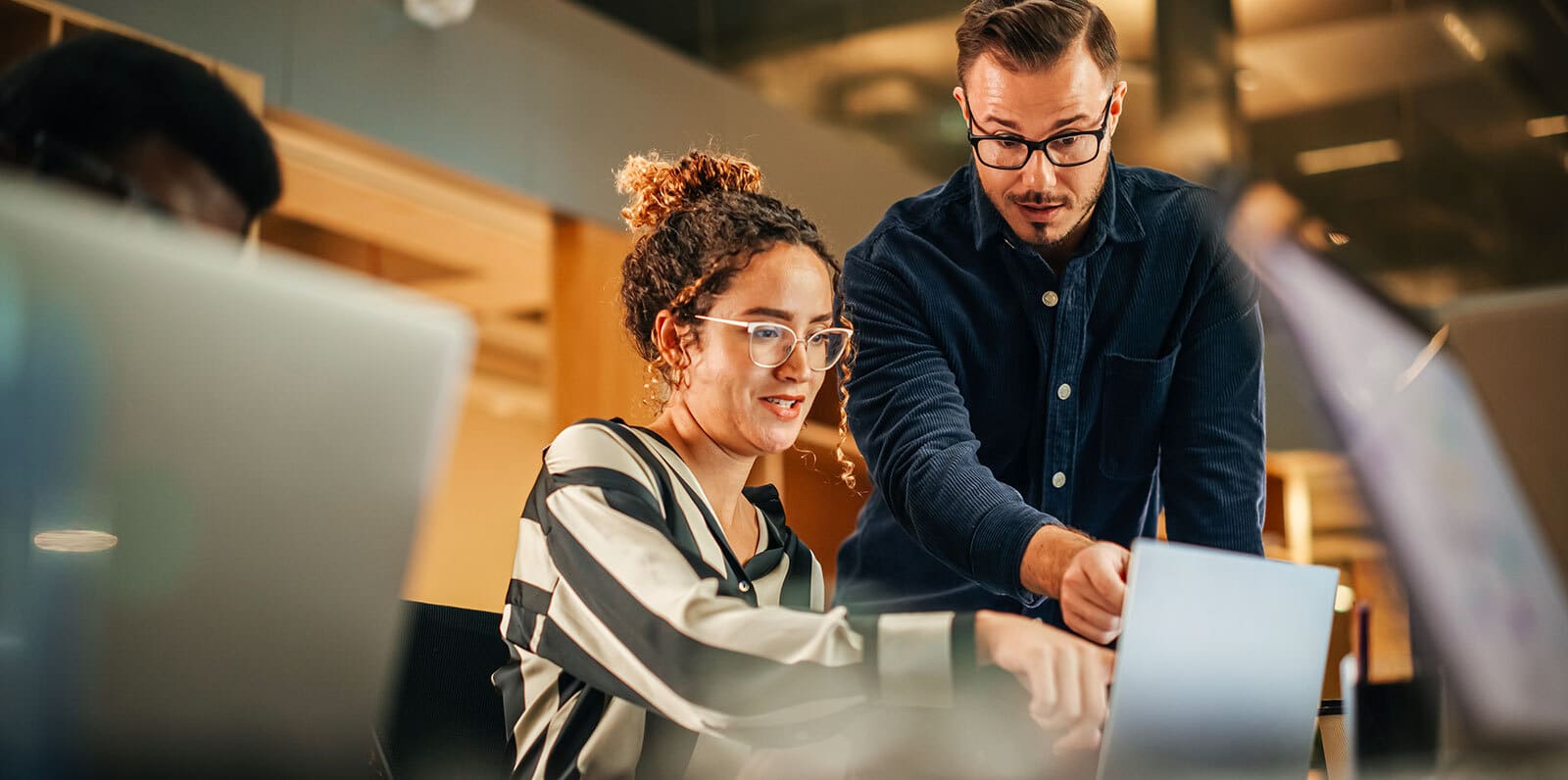
Explore different types of work orders in facility management and how preventive, corrective, and emergency orders impact efficiency and asset performance.
Managing maintenance across multiple sites is challenging. These sites often require separate protocols, and routine inspections may compete with emergency repairs for attention. As a result, many maintenance managers must perform a lot of manual data entry to make sure all work gets done.
However, an efficient work order management process can reduce the pain of this situation and facilitate proactive maintenance. When you create a work order, you help maintenance teams respond faster, managers plan better, and all staff work more efficiently with less equipment downtime.
What Are Work Orders?
Work orders give facility managers a clear way to organize maintenance tasks. Each work order outlines what type of maintenance work needs to be done, who will do it, and when it should happen. They may be submitted for preventive maintenance tasks or emergency repairs. In either case, clear work orders will give your maintenance team clear direction and hold them accountable.
ServiceChannel’s work order management software makes this process much easier. Our software centralizes task submission, assignment, and tracking, so you can keep everyone in your maintenance department on the same page, even across multiple locations.
The Importance of Work Order Management
Work order management is important because it keeps maintenance processes organized and on schedule. It also reduces confusion because all the details about the required maintenance work will be listed on the work order. Maintenance management can also schedule resources and allocate them more effectively with a clear understanding of where labor and materials are most needed.
A computerized maintenance management system (CMMS) helps your facility achieve these goals. The CMMS overview is a software tool that organizes work orders, tracks assets, schedules maintenance tasks, and keeps equipment and maintenance records.
Using CMMS software gives your team real-time visibility into maintenance activities. With this level of visibility, you can streamline maintenance operations and reduce the risk of repeat work.
Types of Work Orders
Preventive Maintenance Work Orders
Preventive maintenance work orders are scheduled tasks that help reduce the chance of equipment failures through routine inspections. If a potential issue is found during an inspection, maintenance work is performed to prevent it from escalating. This type of preventive maintenance work helps extend asset lifespans and prevent equipment failures.
Such issues usually include wear, needed adjustments, and cleaning. Preventive maintenance work does not usually focus on noticeable breaks, although any maintenance team should correct these issues if found during an inspection.
Corrective Maintenance Work Orders
A corrective maintenance work order is submitted if a malfunction is detected or if an asset is underperforming. However, corrective maintenance work orders would not be used in situations where said malfunction or performance issue could cause immediate safety or property damage concerns. Examples include replacing worn parts or fixing minor leaks.
Emergency Maintenance Work Orders
Emergency maintenance work orders are created in response to sudden equipment failures or if the failure could risk safety, property, or operational efficiency. These situations require urgent attention to restore functionality or to prevent damage.
With ServiceChannel, you can expedite any emergency maintenance request. Our work order management system includes automated emergency dispatching. When an emergency work order is created, our system immediately assigns it to a top-ranked provider. That means shorter wait times and less need for manual follow-ups.
Exploring Predictive vs. Prescriptive Maintenance
Predictive maintenance uses sensors, historical records, and real-time analytics to forecast when equipment is likely to fail. Prescriptive maintenance goes a step further by using AI to recommend specific actions based on this data. As more organizations adopt connected systems and smarter tools, predictive and prescriptive maintenance are both increasingly popular maintenance strategies.
Facilities that use these strategies often see a noticeable decrease in the time it takes to complete service requests. For instance, Cole Haan saw a 36% decrease in full-resolution time for open work orders thanks to the valuable insights they gained using real-time data.
Challenges in Work Order Management
Managing Multiple Facilities
Coordinating work orders is more difficult if you must coordinate across multiple locations. You can simplify coordination by standardizing maintenance processes so that teams follow the same standardized operating procedures regardless of location. Using a centralized platform will also help keep all locations in line with your organization’s maintenance strategy.
Tracking Asset Performance
Without real-time visibility into each asset’s condition, it’s too easy to miss a critical period when a work request should have been submitted. That’s why you should use a data-driven asset management strategy. Use real-time sensors to monitor asset performance and assess each asset’s maintenance history. Identifying performance trends helps you make more informed repair or replacement decisions.
Coordinating With Vendors
Vendors may complete maintenance tasks late, fail to update a task’s status, or deliver inconsistent services. However, you can reduce the risk of these issues by setting up a clear SLA and a shared portal where vendors can track assignments, upload documents, and stay aligned with expectations.
Keeping Maintenance Records Consistent
Missing records make it difficult to prove maintenance was done. As a result, your maintenance team may repeat repair tasks, or you may face challenges during audits. Store all notes, photos, and status updates in a single digital location. Use templates and required fields to make sure each record includes enough detail to be useful.
How to Optimize Work Order Processes
Prioritize Work Orders
Treating every work request equally leads to backlogs and delayed repairs. Instead, prioritize service requests for essential equipment or any particular asset that could cause safety risks. There is no reason to focus on chipped paint on your office building if a major electrical equipment failure occurs.
Standardize The Work Order Intake Process
People may submit work order requests without all the necessary details. You can reduce the instances of that by using a standardized submission form. Clearly include areas where the submitter can add all the details that your maintenance technicians need to complete the work request in a timely manner.
Use Clear Status Milestones
Maintenance technicians may delay work if they are unsure of what steps to take next. That’s why it may be helpful for your maintenance managers to provide status milestones. These milestones may include submitted, assigned, in progress, and completed. Most digital work order management systems allow you to set the work order status.
Use Automation
Manual task execution is time-consuming and can be error-prone. Automate work order creation by using tools that pull data directly from service requests or sensors. Automation will also reduce the risk of missing details on submission forms.
ServiceChannel’s platform can automate work order creation, streamline vendor communication, and monitor task status. Our tool supports performance tracking and provides real-time updates, so you always know where maintenance work is needed most.
Optimize Your Work Order Management Process With ServiceChannel
No matter your strategy, handling maintenance tasks will quickly become cumbersome without an effective work order management system. Understanding the various types of work orders and how you can optimize work request intake will make effectively managing your maintenance tasks much easier.
Enhance your existing processes by adding ServiceChannel’s digital platform to your maintenance operations.
Our work order management software will drastically increase the number of maintenance tasks you can complete without compromising the quality of the service.