Hot Water Heater Preventative Maintenance Checklist
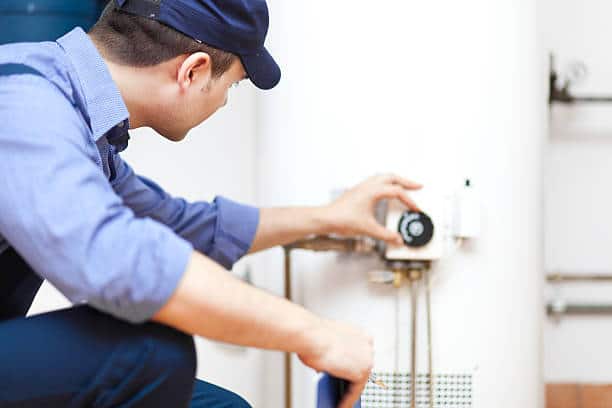
Discover our guide to Hot Water Heater Preventative Maintenance! From components to common issues, maintenance tasks, and how to integrate preventative practices.
A hot water heater is an essential component in homes and businesses. Regular water heater maintenance is as vital as HVAC maintenance in commercial facilities. Just as an HVAC maintenance checklist is important for keeping your heating and air conditioning operating at peak performance and energy efficiency, a hot water heater maintenance checklist will help ensure efficient water heating and extend the appliance’s life. This water heater preventative maintenance checklist guide will provide sound advice on navigating the steps of proper water heater preventive maintenance.
Preventative Maintenance on Hot Water Heaters
If you perform routine maintenance, a water heater’s lifespan can last 10 to 12 years, and a tankless water heater can function for up to 20 years. Preventive maintenance helps ensure a long life for your water heater.
Key Components
In homes, water heaters heat water for a variety of uses, such as bathing, cleaning, and cooking. Facilities also rely on hot water for many tasks. Regular water heater maintenance keeps all of the vital parts working correctly and reduces the risk of the appliance breaking down.
- Water heater tank. The tank stores the water that is to be heated.
- Burner: Gas water heaters use a burner to heat the water at the bottom of the tank before it mixes with the rest of the tank’s water
- Heating elements. Electric water heaters use a heating element at the top and bottom of the tank to heat all the water more uniformly.
- Thermostat. Thermostats monitor the water temperature and adjust the burner or heating elements to ensure the water maintains a consistent temperature.
- Dip tube. The dip tube is a pipe that directs water to the bottom of the tank to be heated before it mixes with the rest of the water in the tank.
- Anode rod. An anode rod attracts the oxygen in the water from the interior of the tank. This corrodes the anode rod and slows tank corrosion to extend the life of your water heater.
- Pressure relief valve. The temperature and pressure (T&P) relief valve opens automatically to relieve the tank when the temperature exceeds 210 degrees Fahrenheit or pressure exceeds 150 pounds per square inch (psi).
- Drain valve: This valve lets users empty the tank to perform water heater maintenance.
Common Issues
Whether you have an electric water heater or a gas water heater, scheduling regular water heater maintenance helps prevent a number of common issues that can dramatically impact a facility’s productivity.
- Water leaks. Leaking water can do all kinds of damage to the exposed area if not addressed quickly.
- No hot water. Many facilities rely on water to maintain a specific temperature for production purposes.
- Foul odor. This could indicate excessive corrosion that might make the water unusable for production.
- Limescale buildup. Excessive mineral deposits in the tank can reduce the lifespan of a water heater.
- Low water pressure. Slower-moving water often means slower production.
- Overheating. As many production facilities rely on water to stay at a certain temperature, it may ruin the final product if the water is too hot.
Annual Maintenance Tasks
Preventive maintenance tasks are typically broken down into frequency schedules. Water heater maintenance requires yearly, monthly, and daily tasks to keep the appliance in ideal working order. There are nine steps to the annual maintenance schedule.
Before performing any maintenance task, turn off the water heater and gas or electricity leading to the appliance.
1. Drain and Flush the Tank
Place a bucket beneath the discharge pipe and open the drain valve to empty the tank. Flush the tank with the valve open to remove sediment buildup and minimize tank corrosion.
2. Test the Pressure Relief Valve
Flip open the T&P relief valve for about five seconds and discharge it into a bucket to make sure it operates properly.
3. Replace the Anode Rod
Perform regular inspections of the anode rod. If the rod displays excessive corrosive buildup, replace it to prevent rust and corrosion of the tank.
4. Test the Thermostat and Valves
Use a multimeter to ensure electrical continuity in the thermostat. Gas heaters have one thermostat. An electric heater will have two — one for each heating element.
5. Clean the Burner Assembly
Pull out the burner assembly and brush off any debris. Rinse the burner with warm water and check the burner for signs of deterioration.
6. Examine the Flue and Venting System
Inspect the flue pipe, air intake, and vents for signs of corrosion and remove any blockage you encounter.
7. Tighten Electrical Connections
Verify that all electrical connections are secure and tighten any that appear loose. Check the wiring to the water heater for signs of wear or damage.
8. Verify Insulation and Wrap
An insulation wrap or insulation blanket prevents a water heater from losing heat. Ensure the tank is adequately wrapped while providing access to the control switch and burner panel.
9. Run a Short Test Cycle
Conduct one last quick test to verify that all water heater components perform as expected.
Monthly Maintenance Tasks
Performing monthly maintenance helps keep your water heater running at optimum efficiency and keeps energy costs down. You can also break down monthly water heater upkeep into seven steps to ensure your heater is working correctly.
1. Visual Inspection
Examine the area around the water heater for signs of water leaks. Also, look at the flue, air intake, and vents to determine any visible signs of corrosion or blockage.
2. Inspect for Leaks
Check the exterior of the water heater, especially the pipes, for any wet spots that might indicate a leak.
3. Check the Pressure Relief Valve
Open the relief valve and empty it into a bucket for a few seconds to verify it’s in good working condition.
4. Flush a Pint of Water
Place a bucket beneath the water heater discharge pipe and open the drain valve to let the water drain out a pint. This reveals if any sediment buildup has occurred and flushes out a good portion of it.
5. Check for Noises or Venting Issues
While the water heater is running, listen for popping, rumbling, or any other unexpected sounds that might indicate issues such as sediment buildup in the tank.
6. Inspect the Burner Compartment
If you have a gas heater, open the burner compartment panel and look into the chamber to verify a steady blue flame. Use a flashlight to inspect for signs of dirt or debris.
7. Inspect Insulation
Examine the water heater tank’s insulation wrap to ensure no damage or gaps. If needed, repair the insulation or replace it with a new wrap to prevent heat loss.
Daily Maintenance Tasks
Facility maintenance teams often give all water heaters a thorough once-over during their daily preventive maintenance inspections. They perform the following five tasks to ensure production teams receive the hot water they need:
1. Visual Inspection
Examine the area around the water heater and pipes for signs of water leaks. Also, check for unusual odors.
2. Monitor the Water Temperature
Sticking a cooking thermometer in a container of freshly discharged hot water works perfectly for verifying the water’s temperature is where it should be. Water used for cleaning or bathing shouldn’t exceed 120 degrees Fahrenheit.
3. Check the Pilot Light
If your water heater uses a pilot light, visually check the burner chamber to ensure it’s burning steadily with a blue flame.
4. Inspect Vents and Flue
Visually examine the water heater air intake, the flue, and vents for debris, dirt, and blockage to maximize your water heater’s efficiency.
5. Keep the Area Clear
Be sure to keep the area around the water heater free from loose items and debris, which can be a safety hazard for other facility personnel.
Let’s Get Started
Ready to kickstart your maintenance program?
Tell us about your situation and we’ll help plan a preventive solution that hits your goals.
When to Seek Professional Maintenance
Some basic knowledge helps perform rudimentary inspections, as the average person isn’t qualified to conduct professional inspections or repair water heaters. These are some common scenarios where you should call a professional.
- Persistent water leaks
- No hot water
- Unusual sounds coming from the water heater
- The pilot light won’t stay lit
- Foul odors near the water heater
- Gas smells around the heater
- Excessive accumulation of sediment
- Signs of corrosive elements
Integrating Preventative Maintenance Practices
By incorporating these four basic water heater maintenance tips into your routine, you can be sure to conduct timely and effective maintenance on all of your facility’s assets.
1. Create a Maintenance Schedule
Break down tasks into annual, quarterly, monthly, weekly, and daily. Ensure all critical tasks are part of this breakdown to avoid overlooking any vital steps.
2. Document Maintenance Tasks
Keep a maintenance log of all maintenance activities. Include the name of the maintenance personnel, dates of maintenance tasks, observations, issues encountered, and actions taken to address issues.
3. Set Task Reminders
Digital calendars, time-keeping applications, and alerts on maintenance department computers enable you to stay consistent with your preventive maintenance routine.
4. Use Preventative Maintenance Software
A facility maintenance software solution like ServiceChannel helps schedule, monitor, and sustain records of all your business’s maintenance tasks. The benefits of preventive maintenance on all equipment, including water heater maintenance, include extending the life of your appliance to its maximum potential.
Heat It Right with ServiceChannel
ServiceChannel is the ideal software solution for all of your facility management needs, from keeping up your water heaters to maintaining accurate records. Request a demo with ServiceChannel today and start your business on the path to effective and efficient facility maintenance.
For further guidance on proactive asset and appliance upkeep, ServiceChannel offers insights into what preventive maintenance is and why it matters for all of your facility assets, as well as a look into the different types of preventive maintenance.