8 CMMS KPIs Facilities Managers Should Be Tracking
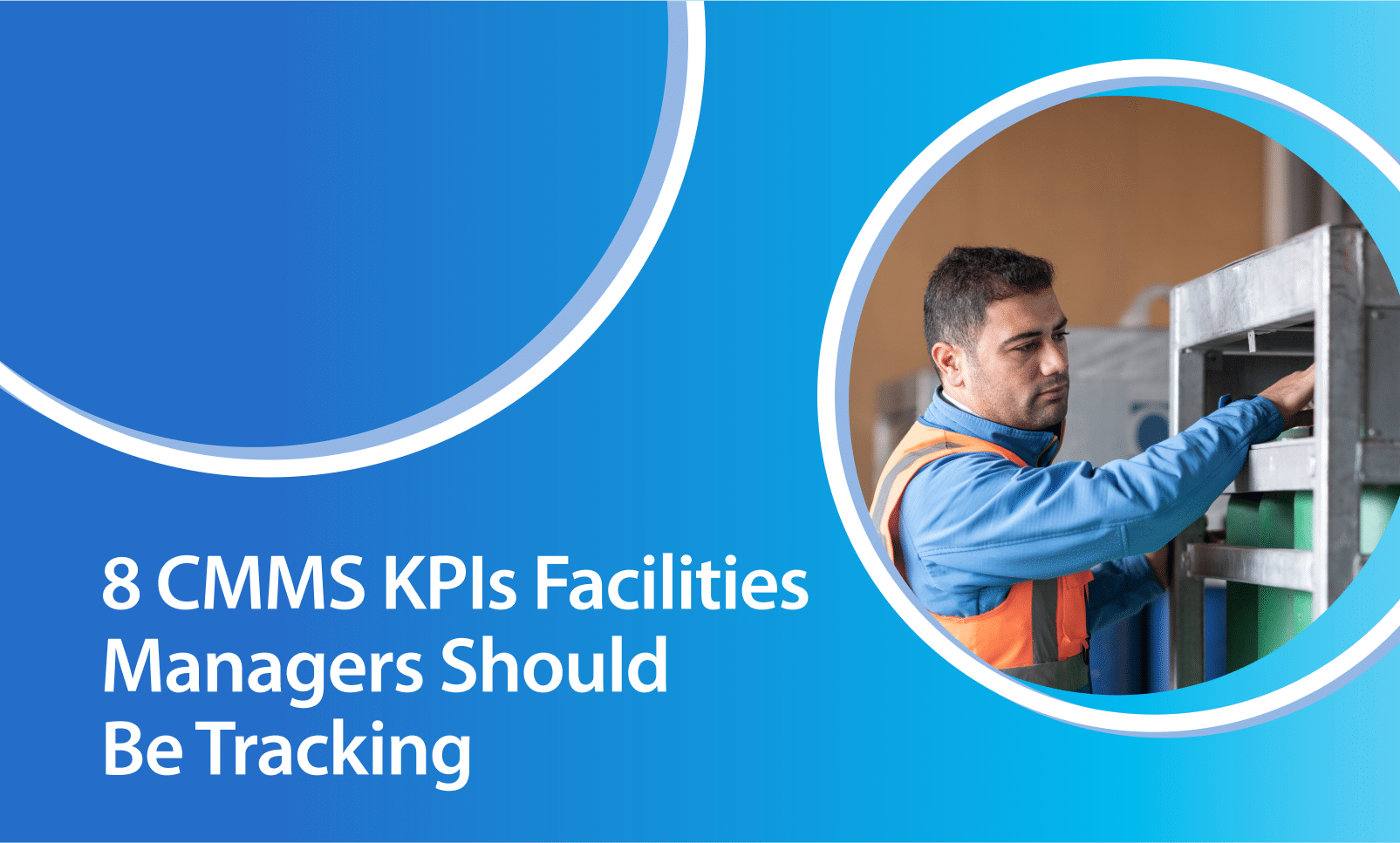
According to a study by Hassan Awan, Z. Razaq, and M. Ishaq Bhatti, Key Performance Indicators (KPIs) are a great way of improving your organization’s performance. It helps in goal setting, improves efficiency, and helps an organization stay on course with the budget.
CMMS software is handy when paired with key performance indicators because they ensure that you’re tracking the right maintenance metrics that show you where your facilities program needs to improve. Otherwise, you risk massive downtimes and costly repairs.
This piece will dive into computerized maintenance management system KPIs, which ones you should be monitoring, and how ServiceChannel can help you take back control of your facilities program.
Let’s dive in.
How KPIs Impact Facilities Maintenance
Using key performance indicators in facility maintenance gives concrete data on how a facility performs. The data triggers important conversations and actions surrounding maintenance planning. Consequently, organizations and facility managers set maintenance targets and meet them with concise, data-driven planning.
Using these metrics in facility maintenance helps organizations stay closer to their maintenance budget, have better safety compliance, improve employee morale, and suffer fewer downtimes.
On the flip side, not using maintenance KPIs makes tracking and analyzing a facility’s maintenance performance harder. Thus, you run at a higher risk of running costlier reactive maintenance programs, increased downtimes, and poor safety compliance.
8 CMMS KPIs To Track
Having a maintenance KPI to track doesn’t necessarily translate into better facility maintenance. You need to track the right maintenance metrics for the best results. Here are eight you should not leave out of your list.
Mean Time Between Failures (MTBF)
The mean time between failures represents the average time between one piece of equipment failing in some capacity or breaking down until the next machine failure. This metric is measured in hours using the formula:
MTBF = Total uptime/number of breakdowns
This maintenance KPI aids in identifying problematic assets. A maintenance manager can thus quantify the reliability of an asset and predict its future performance, which further helps in enterprise asset management.
With this maintenance metric, you can also optimize preventive maintenance schedules and organize preventive maintenance tasks such as oiling, calibration, and greasing before the piece of equipment fails unexpectedly.
Planned Maintenance Percentage (PMP)
Planned maintenance percentage is the percentage of hours spent on planned maintenance activities versus unplanned. This metric is calculated by dividing the labor hours for scheduled maintenance into the total maintenance hours during a given maintenance period.
Ideally, 90% of maintenance should be planned. However, a ratio of 80% planned maintenance to 20% unplanned maintenance is still considered okay for this KPI.
Overall Equipment Effectiveness (OEE)
Overall equipment effectiveness (OEE) contains three components: availability, performance, and quality.
Availability checks that the system is functioning when needed. Performance measures the system’s throughput divided by its maximum throughput. Quality measures the number of good units divided by the total number of units produced.
Therefore, OEE monitors the efficiency of a manufacturing process and shows you areas for improvement. This KPI is measured using the formula:
OEE = availability x performance x quality
Maintenance Cost Variance
Maintenance cost variance measures the difference between the budgeted cost allocated to a project and the actual maintenance cost. This KPI helps you track the quality of your budget and help you effectively plan for future maintenance budgets.
Maintenance cost variance is measured using the formula:
Maintenance cost variance = expected cost of maintenance – actual cost of maintenance
Often, this number is negative, indicating that the actual cost of maintenance superseded the budgeted cost. Ideally, your budget should be balanced, meaning the maintenance cost variance should be positive with extra funds available for padding the budget.
Wrench Time
Wrench time measures how long maintenance personnel spends holding an actual maintenance tool in their hand doing maintenance work.
Wrench time only measures the time taken to do the actual maintenance work. It does not include the time spent picking tools, traveling, taking breaks, or looking at the work order.
Wrench time thus gives the most accurate measure of how much time is spent on manual maintenance tasks.
Mean Time to Repair (MTTR)
Mean time to repair measures the time from which a machine fails to when it’s brought back online. This CMMS KPI helps with equipment diagnosis, planning, scheduling, and the actual work necessary to fix the equipment.
Ideally, you should aim for a lower MTTR number.
Work Order Backlog
Work order backlog indicates the time needed to execute a preventive, reactive, or predictive work order. It represents the maintenance delays in the system arising from a build-up of pending and planned activities per technician. It doesn’t matter if they’re already in progress.
Work order backlog is calculated by dividing the sum of man-hours for planned, pending, and completed work orders by the total available man-hours. The bigger the backlog, the higher the risk of breakdowns and downtimes.
Completed Work Orders
Completed work orders is a CMMS KPI that measures the number of work orders completed in time. This KPI is further used to calculate preventive maintenance compliance (PMC). Completed work orders are typically measured daily, and this information is readily available in most CMMS systems.
Get More Out of Your CMMS
Maintenance KPIs are the way to go in order to run an efficient, effective, and scalable facility maintenance program. The eight maintenance KPIs listed above will help you reduce downtimes, improve your budget, and track the throughput of each maintenance technician.
Even with the eight provided maintenance KPIs, you can do more optimization. Contact ServiceChannel to get expert help on how you can optimize these maintenance KPIs and explore a few others that may be great for your facility.