Guide to Condition-Based Maintenance (CBM)
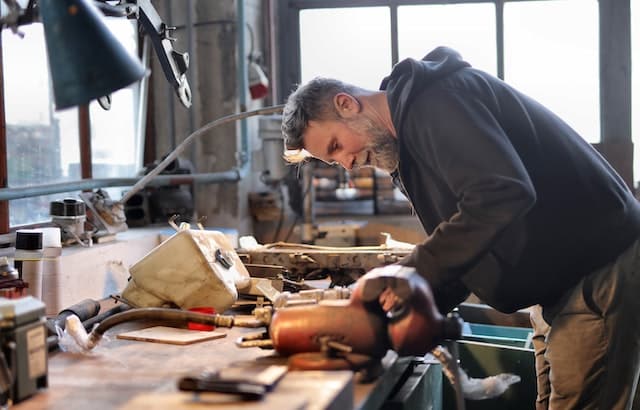
Learn how condition-based maintenance (CBM) works, how it differs from other strategies, and how to implement CBM to reduce downtime and maintenance costs.
Unplanned downtime and costly repairs can cause drastic operational disruptions. Condition-based maintenance (CBM) helps facilities managers stay ahead of the game with real-time equipment health monitoring. By using sensor data and performance trends, CBM ensures that your maintenance teams can perform their duties exactly when it’s needed — preventing failures, extending asset life, and optimizing costs.
What is Condition-Based Maintenance?
Condition-based maintenance (CBM) is a proactive maintenance strategy that relies on real-time condition monitoring to determine when equipment requires servicing. Instead of following a fixed schedule, CBM uses sensor data, visual inspections, and IoT-enabled monitoring to detect signs of wear, inefficiency, or potential failure.
This approach works for both mission-critical and non-critical assets, helping maintenance teams avoid breakdowns and extend asset lifespan without wasting time and money on unnecessary upkeep. CBM operates within defined performance thresholds. As long as an asset’s condition stays within the acceptable range, it doesn’t require any maintenance. Once data indicates a deviation beyond set limits, the system alerts the maintenance team to take action, preventing breakdowns and optimizing maintenance costs.
Condition-Based Maintenance vs. Preventive Maintenance
Condition-based maintenance (CBM) and preventive maintenance are proactive strategies designed to reduce equipment failure and extend asset lifespan. However, they take very different approaches to scheduling maintenance tasks.
Preventive maintenance follows a fixed schedule, using historical asset data to determine when to perform maintenance. For example, if an HVAC system in a commercial building has a history of requiring servicing every three months, a maintenance manager might schedule routine inspections and part replacements every 90 days, whether the equipment needs it or not.
Condition-based maintenance relies on real-time condition monitoring to identify potentially failing assets before issues arise. Instead of servicing equipment on a set schedule, CBM ensures maintenance is only performed when sensor data, visual inspections, or condition monitoring sensors indicate a potential issue.
This key difference can make CBM a more cost-effective strategy. Preventive maintenance can lead to unnecessary maintenance, replacing parts too early, or spending time on equipment that is still functioning properly. CBM helps reduce maintenance costs by focusing only on actual equipment performance, preventing unplanned downtime without overspending on premature repairs.
Condition-Based Maintenance vs. Predictive Maintenance
Condition-based maintenance (CBM) and predictive maintenance are proactive strategies designed to identify potentially failing assets before breakdowns occur. However, they differ in how they collect data and trigger maintenance actions.
Predictive maintenance relies on historical asset data, advanced diagnostics, and machine learning algorithms to forecast when a failure is likely to happen. This approach often incorporates failure modes analysis, vibration analysis, oil analysis, and electrical analysis to detect subtle performance changes over time.
Condition-based maintenance focuses on real-time equipment performance, using sensors’ data, manual inspections, and predefined operation thresholds. Instead of predicting when a failure might happen based on trends, CBM ensures maintenance is performed only when live data indicates an issue.
For example, in an industrial manufacturing plant, predictive maintenance might analyze historical vibration data to estimate when a motor is likely to fail in the next three months. In contrast, condition-based maintenance would continuously monitor vibration levels in real-time, triggering maintenance only when the readings exceed acceptable limits.
Condition-Based Maintenance Techniques
CBM relies on various condition-monitoring techniques to detect early signs of equipment failure. By continuously collecting data, you can make informed decisions about when to perform maintenance, preventing costly breakdowns and improving equipment reliability. Each strategy has advantages, and many facilities use multiple methods.
Here are the most common condition-based monitoring techniques used in CBM programs across various industries:
Oil Analysis
Oil analysis plays a crucial role in industrial equipment maintenance, particularly in rotating equipment such as pumps, compressors, and hydraulic systems. Sensors analyze oil viscosity, contamination levels, and particle intrusions, enabling personnel to identify potential asset failures before they experience significant wear. A condition-based maintenance program incorporating oil analysis can prevent lubrication-related failures and extend asset life cycles.
Infrared Thermography
Infrared scanning systems detect temperature variations in electrical and mechanical components, helping to identify overheating equipment before failures occur. This method is widely used in HVAC systems, electrical panels, and industrial motors to pinpoint hotspots, loose connections, and insulation breakdowns. Regular infrared inspections can reduce maintenance costs by catching minor issues before they lead to breakdowns.
Electrical Analysis
Electrical analysis is essential for monitoring power systems, transformers, and circuit breakers. By measuring motor current readings, voltage fluctuations, and power quality, teams can detect electrical imbalances that lead to overheating or failure. This method is commonly applied in manufacturing plants, hospitals, and data centers, where stable power is critical.
Performance Monitoring
Performance monitoring uses traditional techniques like visual inspections, modern audio assessments, and operational data tracking to measure equipment efficiency. Maintenance teams evaluate flow rates, pressure levels, and temperature fluctuations to detect anomalies in critical equipment. While this technique is cost-effective, it requires experienced maintenance technicians to interpret the results accurately.
Ultrasonic Analysis
Ultrasonic testing detects high-frequency sound waves that indicate leaks, friction issues, and failing components. This method is valuable in compressed gas systems, steam traps, and fluid pipelines, where small leaks can lead to significant waste and safety risks. Contact ultrasonic testing helps identify lubrication problems and misaligned bearings, while airborne ultrasonic methods can locate pressure or vacuum leaks.
Acoustic Monitoring
Acoustic monitoring is a specialized form of ultrasonic analysis that detects friction and mechanical wear before human hearing can pick it up. This technique is useful for detecting gas leaks, failing valves, and deteriorating bearings in petrochemical plants, food processing facilities, and heavy machinery operations.
Vibration Analysis
Vibration analysis is an effective condition-based maintenance strategy for analyzing rotating equipment such as motors, turbines, and gearboxes. Maintenance staff can pinpoint misalignments, unbalanced loads, and structural defects by measuring frequency changes, shock pulses, and harmonic distortions. A well-implemented CBM program that includes vibration analysis helps reduce maintenance costs by identifying issues before they escalate into critical failures.
Baseline Performance Standards
For condition-based maintenance to be effective, monitor assets against baseline performance standards. These standards are the predefined thresholds determining whether the equipment operates normally or shows signs of deterioration. Establishing these criteria lets you detect equipment anomalies early and get ahead of unexpected failures and costly repairs.
Key Factors in Establishing Baseline Performance Standards
To create an effective condition-based maintenance program, you need to define baseline data using the following factors:
- Historical Data: Analyze historical data to determine past failure trends, expected performance levels, and normal operating conditions.
- Manufacturer Specifications: Use OEM (Original Equipment Manufacturer) guidelines to establish acceptable performance ranges for critical assets such as motors, pumps, and HVAC systems.
- Operating Conditions: Consider environmental factors such as temperature, humidity, and load capacity. Conditions like these can affect your equipment’s performance over time.
- Sensor Readings: Implement condition monitoring sensors to collect real-time data on vibration levels, pressure changes, and electrical metrics.
- Failure Modes Analysis: To predict how assets might degrade, use failure modes and effects analysis (FMEA) to identify potential failure points.
- Industry Standards and Regulations: To ensure safety and operational efficiency, follow ISO 55000 asset management guidelines and other industry-specific compliance requirements.
Benefits of Condition-Based Maintenance
An ideal condition-based maintenance program helps you maximize the efficiency of maintenance efforts and minimizes downtime. By performing repairs only when necessary, CBM reduces costs and extends asset life — all while improving operational reliability.
Here are the key benefits of adopting CBM in facilities management and industrial maintenance programs:
- Extends Equipment Life: CBM ensures you can make repairs before failures occur, preventing excessive wear and increasing asset lifespan.
- Reduces Maintenance Costs: Maintenance teams only perform maintenance when necessary, eliminating unnecessary part replacements and labor expenses.
- Minimizes Downtime: Since you perform CBM while equipment is in use, you can strategically schedule maintenance to avoid disruptions.
- Improves Equipment Performance: Real-time condition monitoring helps keep operations running optimally, reducing inefficiencies that lead to higher energy consumption and production defects.
- Enhances Compliance and Safety: CBM supports safety regulations by identifying potential electrical, mechanical, or structural hazards before they escalate.
With data-driven insights and condition monitoring, your organization can streamline maintenance efforts, avoid unnecessary work, and focus on keeping critical assets running smoothly.
The Long-Term Impact of Condition-Based Maintenance
A well-implemented condition-based maintenance (CBM) strategy does more than just prevent equipment failures. It also helps organizations optimize their maintenance programs over time. By continuously monitoring asset conditions and adjusting maintenance strategies, CBM enables facilities managers to make data-driven decisions that improve efficiency, reduce costs, and extend the lifespan of critical equipment.
Key Long-Term Benefits of CBM
- Optimized Maintenance Strategies: Over time, CBM helps you refine maintenance schedules and resource allocation, keeping maintenance efforts focused where needed most.
- Improved Asset Reliability: By continuously monitoring performance trends, you can identify failure patterns and proactively adjust to extend asset lifespan.
- Reduced Operational Costs: With historical data and trend analysis, facilities managers can eliminate unnecessary maintenance while preventing costly emergency repairs.
- Enhanced Predictive Capabilities: As you collect more baseline data, you can integrate predictive analytics into your CBM programs, further improving equipment reliability and minimizing downtime.
- Sustainability and Energy Efficiency: CBM reduces wasteful maintenance activities and helps optimize energy consumption, leading to a more sustainable and cost-effective operation.
By adopting CBM as a long-term strategy, your organization can continuously improve maintenance efficiency, drive operational excellence, and ensure critical equipment operates at peak performance for years.
Condition-Based Maintenance Challenges
While condition-based maintenance offers significant benefits, it also presents challenges that organizations must address to implement it effectively:
- CBM requires upfront costs for sensor installation, employee training, and potential retrofits for older assets.
- Some failure modes, such as material fatigue, may not show clear indicators until a breakdown is imminent.
- Harsh conditions, like mining or extreme temperatures, can interfere with sensor accuracy and shorten equipment lifespan.
- Because CBM triggers maintenance based on real-time conditions, predicting maintenance expenses and resource allocation can be more challenging than fixed-schedule maintenance programs.
Evaluate these factors carefully when developing a CBM strategy to ensure a cost-effective and sustainable approach.
How to Implement Condition-Based Maintenance
Before adopting condition-based maintenance, make sure it aligns with your organization’s objectives, budget, and maintenance personnel’s expertise. Once confirmed, follow these key steps to implement CBM successfully:
- Decide which assets will receive this type of maintenance, starting with the highest priority assets to maximize ROI. Factor in equipment failure costs, safety concerns, the likelihood of failure, and the difficulty of detecting critical issues early.
- Determine your indicators for gauging failure, such as temperature, air quality, or noise. Also, choose the upper and lower limits for each indicator.
- Decide on the level of monitoring that makes the most sense for your operation. Evaluate factors such as budget and the skill level of your maintenance staff.
- Look into software solutions. If you use sensors, consider solutions that automatically issue a work order when maintenance is required. Also, assess platforms that integrate well with your existing systems.
Your Facilities Maintenance Partner
ServiceChannel helps facilities teams streamline maintenance with enterprise asset management (EAM) software that boosts efficiency and simplifies operations. Our collaborative services and sourcing solutions strengthen your asset management program, helping you cut costs and improve performance. Learn how ServiceChannel can help accelerate your facilities management program.