3 Cost Containment Strategies for Facilities Managers
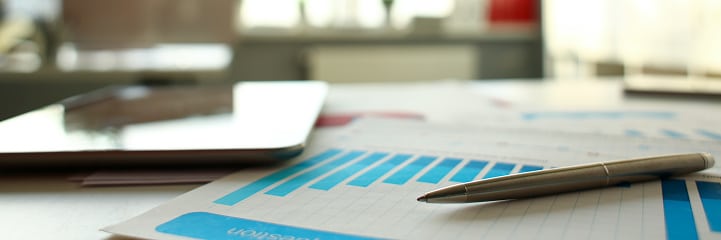
As any first-year finance major student can tell you, businesses can use two big levers to maximize profit: increasing revenues and containing costs. Cost containment is especially crucial in the modern corporate world. However, when many businesses implement cost containment strategies, they tend to focus on the most obvious expenses. These might include marketing initiatives, employee benefits, or annual contracts with third-party vendors.
However, many businesses fail to tackle latent costs — hidden operational expenses, such as facilities management (FM) programs. FM encompasses more than repair and maintenance practices; it also includes energy expenditures, space utilization, and asset management. Keeping one or more physical spaces operating optimally can be expensive — and often, FM expenses aren’t properly tracked.
A facilities management software platform can help businesses implement more robust cost-containment measures by analyzing overhead costs associated with facility upkeep. This opens the door for considerable savings. When compounded year by year, facilities management cost-containment strategies can help you build a significant profit in just a few fiscal cycles. Let’s explore the concept of cost containment and key strategies that can enhance your organization’s FM program.
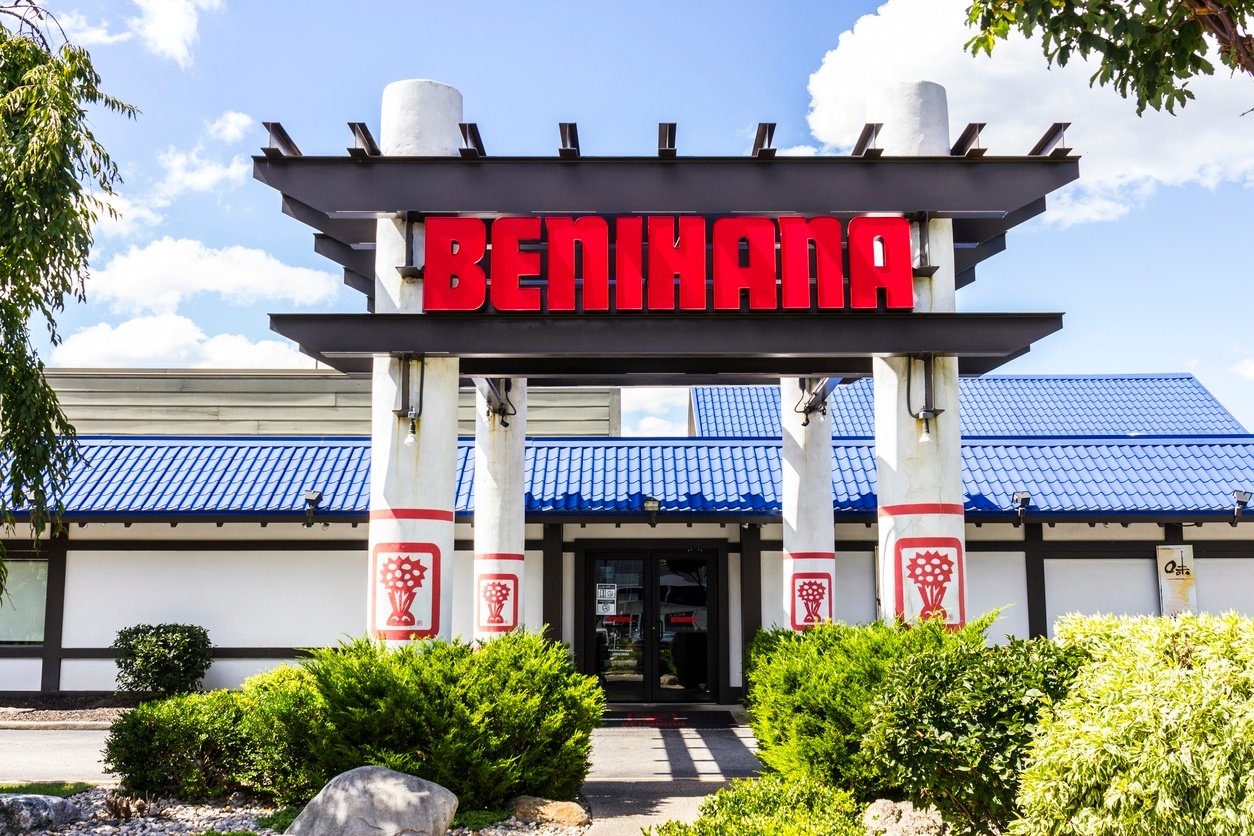
What is Cost Containment?
Cost containment is the practice of controlling expenses by reducing or limiting spending to stay within specific budgetary limits. This enables businesses to improve profitability without long-term damage to the company. For instance, your business might choose to clean existing HVAC filters rather than replace them every year. This would be a classic example of cost containment. There are numerous other cost containment opportunities within facilities management, but they are easy to overlook because the overhead might seem small compared to other recurring expenses.
While cost containment strategies were formerly put into place primarily for profit above impact on operations, modern businesses look at cost containment to improve overall business efficiencies. The current marketplace demands that reducing costs should never compromise business operations. The best cost-containment practices improve operational efficiency, increase marginal savings, and complement the customer experience.
Cost Containment Strategies Within Facility Management
These simple strategies can help you decide if your business could benefit from improved FM cost containment:
Implement Price Controls & Contractor Benchmarking
Many organizations bill for repair and maintenance work hourly. This enables them to negotiate low hourly rate caps with service providers, creating an illusion of savings. However, these rate caps often make high-quality service providers inaccessible, leaving organizations with inexperienced contractors and inconsistent quality. Hourly rates are lower up front, but a business ends up paying more to cover the additional hours for less experienced providers to finish the job.
Implementing quality and price controls based on set benchmarks for a particular type of service can help ensure effective cost containment. When charged hourly, tracking contractor time and the quality of service delivered is vital. Comprehensive facilities management software simplifies this process. For example, service automation carries out contractor benchmarking automatically, tracking hourly rates, technician experience, time to completion, and performance metrics. The resulting contractor scorecard makes it simpler to hire the right service providers for future maintenance needs.
Businesses may also choose to utilize a not-to-exceed (NTE) work order billing strategy. This places cost-to-completion caps on every job. With a fixed dollar value assigned to each task, your organization can more easily contain work order costs — motivating providers to manage their time more efficiently. A service automation platform helps control NTE thresholds by analyzing historical data on trade, service, and region to ensure that work orders are not inadvertently overbilled.
Automate MRO Inventory Tracking
To keep facilities running properly, many businesses stock an inventory of maintenance, repair, and operations (MRO) parts. Rush-ordering a replacement part for an emergency repair is much more expensive than purchasing essential parts ahead of time. For this cost containment strategy to be most effective, facilities managers need to control their MRO inventory completely. This involves tracking purchase orders, documenting all incoming and outgoing inventory, and ensuring proper parts storage.
Technology plays a key role in MRO inventory management. Databases to track spare parts, costs, warranty information, and other key details keep you from overspending or understocking. Inventory management software dramatically reduces miscalculations, purchase duplicates, or the purchase of parts that void warranties much more reliably than when using pen and paper to track MRO inventory.
Facilities managers can automate inventory tracking and align purchase orders with preventive maintenance schedules using the right FM technology. For example, the Supply Manager suite consolidates information on the diverse suppliers that a business relies on and enables strategic sourcing with increased transparency across the FM program. Businesses also gain access to the best available prices, enjoy a longer equipment lifecycle, and maintain spending limits to meet the demands of cost-containment initiatives.
Increase Energy Efficiency
In a commercial setting, saving money in the winter isn’t as simple as lowering the thermostat a few degrees. Customers aren’t likely to stay in a store long if they’re shivering in the winter or sweltering during the summer. Emerging technology has made it easier for businesses to reduce energy use and cut costs without taking away from the customer experience. In fact, from a cost containment standpoint, increasing energy efficiency presents a valuable opportunity to reduce spending while improving operations.
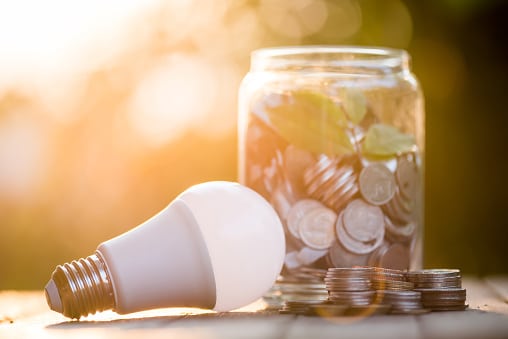
To thoroughly evaluate opportunities for energy efficiency, consider both energy supply costs and energy demand-reduction strategies. The ability to reduce supply costs depends largely on regional market regulations, the organization’s ability to invest in new energy procurement processes, and the reliability of the energy source. Demand-reduction strategies are perhaps more valuable in terms of cost containment, especially when simple adjustments — such as replacing older light bulbs with energy-efficient fixtures — can be implemented quickly with an obvious ROI.
Energy costs are unpredictable, but businesses can track usage using a robust digital FM solution with analytics capabilities. Tracking energy expenditure often reveals where they can improve asset performance — or whether to replace an older asset with a new, energy-efficient model.
Data-Driven Decision Making
For most modern businesses, leveraging data has become essential for effective facilities management. Data-driven decision-making enhances transparency and reduces bias by relying on measurable, fact-based metrics rather than intuition or anecdotal evidence. This approach enables facilities managers to make well-informed choices that improve cost-effectiveness and help address the challenge of rising costs in facilities operations.
A robust facilities management platform can give you access to real-time data on key performance indicators (KPIs), such as contractor response time, equipment downtime, and energy consumption. These insights tie cost containment strategies directly to facilities management, where managers can identify inefficiencies contributing to rising costs and evaluate opportunities to enhance competitive pricing with service providers. By embracing technological advances, such as automated dashboards and benchmarking tools, businesses can streamline operations and prioritize high-impact areas for improvement.
Facilities management software also lets you leverage historical data to benchmark contractor performance, helping to ensure that service providers complete work efficiently and within budget. Additionally, predictive analytics tools help you anticipate maintenance needs, letting you intervene proactively and preventing costly emergency repairs.
Data transparency promotes collaboration across departments, giving stakeholders access to dashboards for monitoring progress and sharing insights. A data-driven approach reduces dependence on subjective decision-making, allowing your teams to implement cost-containment strategies more confidently. This approach helps businesses anticipate the cost curve of operations, aligning operational goals with long-term business objectives. This transforms facilities management from a reactive process into a proactive strategy.
Preventive Maintenance
Preventive maintenance is one of the most effective cost-containment strategies in business and facilities management. By identifying and addressing potential issues before they escalate, businesses can avoid costly emergency repairs, minimize equipment downtime, and extend the lifespan of critical assets. This proactive approach ensures smooth operations and contributes to a more effective cost-containment process — potentially leading to significant savings for your company.
How Preventive Maintenance Works
Preventive maintenance involves scheduling regular inspections, maintenance tasks, and replacements based on usage data, manufacturer guidelines, and environmental conditions. By utilizing information from your facilities management data systems, your teams can identify patterns and predict when maintenance is due, enabling timely interventions and avoiding unnecessary costs. For example:
- HVAC Systems: Regular filter changes and coil cleanings prevent performance degradation, reducing costs by avoiding expensive breakdowns.
- Lighting: Replacing bulbs and inspecting fixtures on a schedule reduces the likelihood of sudden outages, ensuring more inviting customer-facing spaces.
- Plumbing: Periodic inspections of pipes and fixtures prevent leaks that could lead to water damage, costly repairs, and higher utility bills.
Cost-Containment Benefits of Preventive Maintenance
- Cost Savings: Preventative maintenance lowers repair costs by catching problems early. This reduces the likelihood of major equipment failures and ensures assets last longer.
- Improved operational efficiency: With fewer unplanned interruptions, businesses can maintain consistent productivity, delivering a better customer experience while controlling costs.
- Enhanced Safety: Regular maintenance reduces the risk of accidents caused by faulty equipment that can lead to significant costs for a company.
- Data-driven decision-making: Facilities managers can use analytics to refine maintenance schedules, prioritize high-risk assets, and allocate resources effectively — reducing the impact on your budget.
Integrating preventive maintenance into your cost containment strategy creates a foundation for long-term operational success. With tools like ServiceChannel’s Preventive Maintenance software, your organization can streamline operations, enhance maintenance processes, and ensure you’re one step ahead of potential issues.
Final Thoughts
Whatever your business’s objectives, unnecessary expenses are inevitable. Putting cost-containment strategies into place will help reduce needless overhead, streamline operations, and increase efficiencies across the board. When approaching cost containment within your facilities management program, start by differentiating positive and negative costs. Positive costs bring new business in, whereas negative costs are those your business is seemingly “stuck with.” Make a greater effort to contain the negative costs, such as equipment and parts purchases, asset maintenance, and energy consumption.
Your ultimate goal should be meeting and exceeding customer expectations while keeping costs within carefully defined limits, tracking spending, and constantly looking for opportunities to improve.
Let’s Get Started
Ready to take your FM program to the next level?
Learn how our facilities management software can help you streamline operations and reduce costs.