What is Reliability Centered Maintenance?
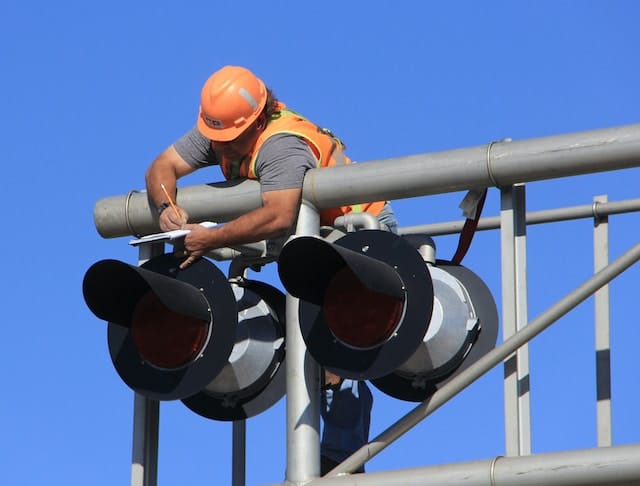
Learn what reliability centered maintenance (RCM) is, the principles of reliability centered maintenance, and the phases of implementation.
Reliability centered maintenance (RCM) starts with top management optimizing their maintenance programs with the best solutions for asset management. There is no one size fits all solution, so creating a complete framework that pays attention to the different styles of maintenance to increase productivity, efficiency, and effectiveness is needed. This could be preventive maintenance, predictive maintenance, or reactive maintenance.
Where is Reliability Centered Maintenance Used?
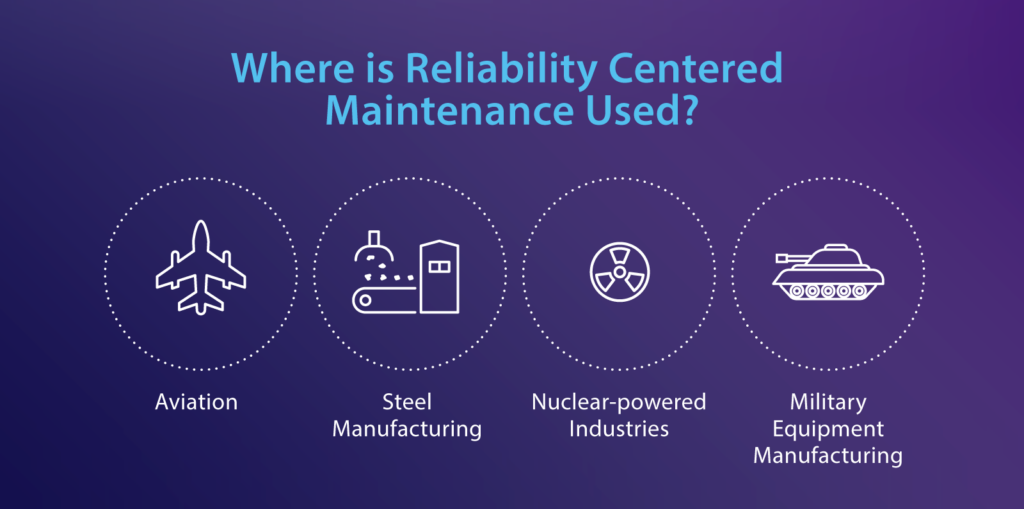
Reliability centered maintenance helps industries focus on analyzing why equipment fails. It captures the types of technology and equipment being used, its design, and any inefficiencies present using time-directed maintenance tasks, failure-finding tasks, and condition-directed tasks. The goal is to have a high-level maintenance strategy to follow. These industries use RCM on a regular basis:
- Aviation
- Steel manufacturing
- Nuclear-powered industries
- Military equipment manufacturing
Reliability Centered Maintenance Principles
The heart of reliability centered maintenance is the less time spent on maintenance activities, the better. This means carefully weighing the risks and costs with the benefits of the maintenance activities. To help facilitate this careful balance there are four main reliability maintenance principles, they are:
- Preserving system functions.
- Identifying failure modes that can affect system functions.
- Prioritizing identified failure modes according to risk and cost projections.
- Selecting the most effective tasks to control failure modes.
Using these principles builds towards the goal of RCM: reducing the life cycle costs of your assets. This means evaluating every cost related to those assets, including the initial, installation, support, operational, and maintenance costs while the asset is in use. Once the asset is taken out of use, the failure, environmental, uninstallation and disposal costs must also be realized and included. When done correctly, it is one of the most profitable maintenance models in use.
Implementing a Reliability Centered Maintenance Program
In order to correctly implement a reliability centered maintenance program there are three phases with multiple steps within each phase that must be closely followed.
Phase 1: Decision
When beginning to implement RCM, the first phase defines the justification and planning of the program based on need, whether the company is ready, and specific outcomes. The steps for completion include:
- Choosing the Equipment: Choosing the right equipment for your strategy is key. This means analyzing the equipment critical to your operations, giving consideration to the legal, safety, and economic impacts the asset may have.
- Identifying the Functions: Having the right data that describes the equipment, it’s tasks, and how it performs helps in understanding how each piece of equipment fits into the larger operational system.
Phase 2: Analysis
In this phase, the study conducted for reliability centered maintenance is designed to provide a high-quality output. These steps include:
- Identifying Functional Failures: This is when the asset or system does not meet performance standards. There are different types of failures beyond complete failure, including poor performance, overperformance, or unintended or unnecessary functions taking place.
- Identifying and Evaluating the Effects of Failures: You must document the observations of failures and any potential impacts these failures could have on production or safety.
- Identifying Failure Modes and Effects: Assessing and identifying possible failures and impacts that could disrupt the overall process can be realized using the Failure Mode and Effects Analysis (FMEA). This approach helps understand any effects that could happen through point of failure, failure analysis, and risk assessment. Using a Computerized Maintenance Management System (CMMS) alongside support solutions can help create the best program.
Phase 3: Action
The final phase, maintenance tasks are selected to minimize or remove any interruptions in production. This is done by using maintenance tasks that improve equipment functionality. There are different types, including corrective maintenance, preventive maintenance, predictive maintenance, prescriptive maintenance, and proactive maintenance.
Once the RCM process begins, you can assess and refine those tasks that need improvement to enhance your maintenance strategy.
Advantages of Reliability Centered Maintenance
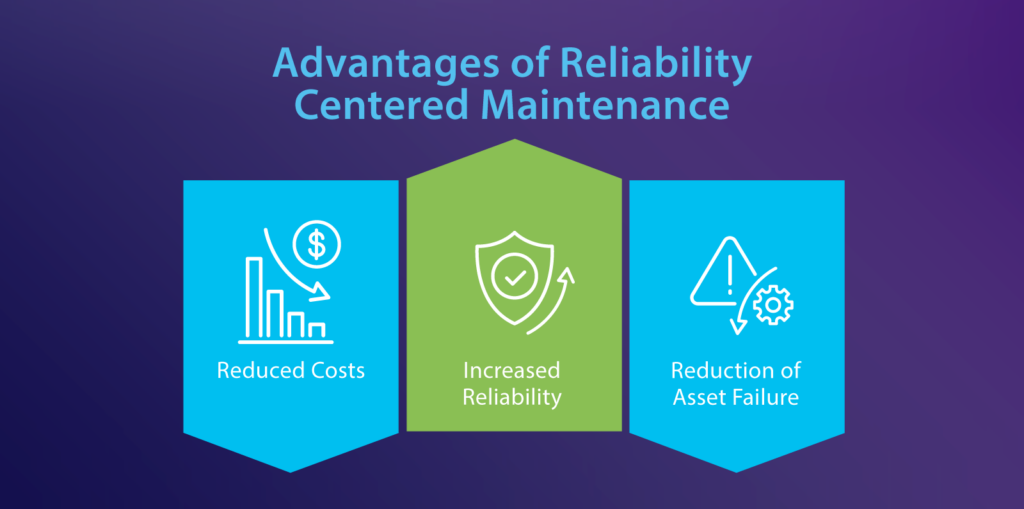
RCM provides a sound framework for maintenance planning and activities that help in coordination, allocation of resources, and a reduction in disruptive production processes. Advantages of RCM implementation are realized as your organization focuses on effective maintenance planning through a well-thought-out RCM program. They include:
- Reduced Costs: When the focus is on critical equipment and their failure modes, maintenance activities are optimized. This lowers maintenance costs while maintaining effectiveness in the resources being used.
- Increased reliability: RCM works proactively by identifying and addressing any potential failures. This helps heighten safety while increasing reliability, efficiency, and productivity.
- Reduction of asset failure: With each asset being properly monitored and maintained, the lifespan is increased while the likelihood and risk of asset failure are minimal. This also prevents premature replacement of assets because of increased efficiency in operational maintenance tasks.
Disadvantages of Reliability Centered Maintenance
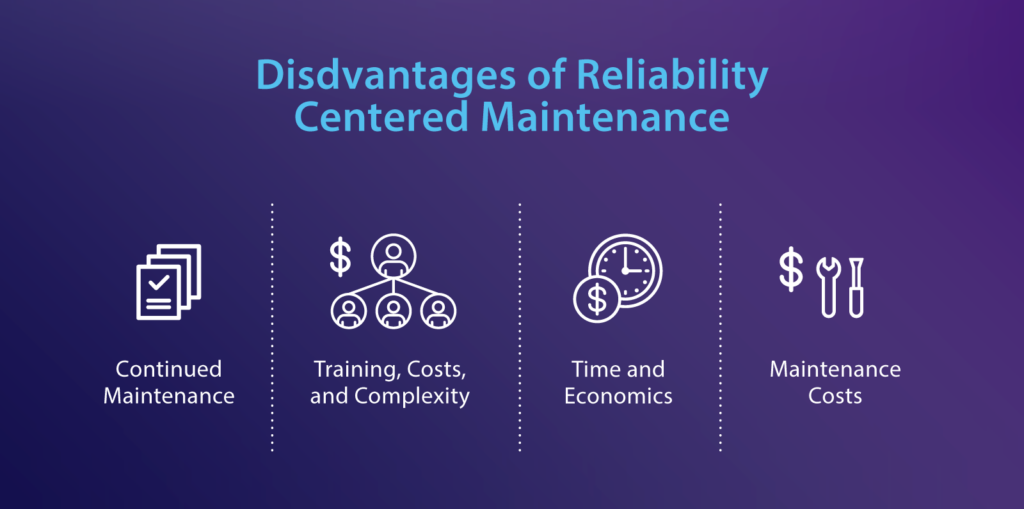
There are a few things that can go wrong in RCM, even with a program designed to increase efficiency in maintenance tasks. In fact, research implies that only 5% of organizations implement RCM programs with the right systems. Here are a few disadvantages:
Implementing RCM is usually more expensive than other maintenance processes, taking more time to discover and assign priorities. This could pose a problem, especially when using multiple maintenance styles at the same time. Other factors include:
- Continued maintenance: Maintenance never stops with RCM. There must be ongoing and regular maintenance tasks in place.
- Training, Costs, and Complexity: Developing and implementing an RCM program is detailed, complex, and costly, especially when considering the amount of training in design and implementation necessary to be successful.
- Time and Economics: Wasting manpower and resources on unnecessary tasks, more analysis required, and the economic impact of implementation.
- Maintenance costs: RCM is a proven process but does not consider the additional expenses, costs, and maintenance. Companies often fail to replace assets past their lifespan in a timely manner.
Your Trusted Maintenance Partner
If you’re looking to fulfill your KPIs and have a strong RCM process in place, ServiceChannel is a great solution to optimizing your maintenance program. We help evaluate what your organization needs and how to choose the best course of direction for maintenance regulations. Learn more about how the ServiceChannel platform can help streamline your maintenance operations here.