Predictive Maintenance (PDM): A Comprehensive Guide for Facilities Managers
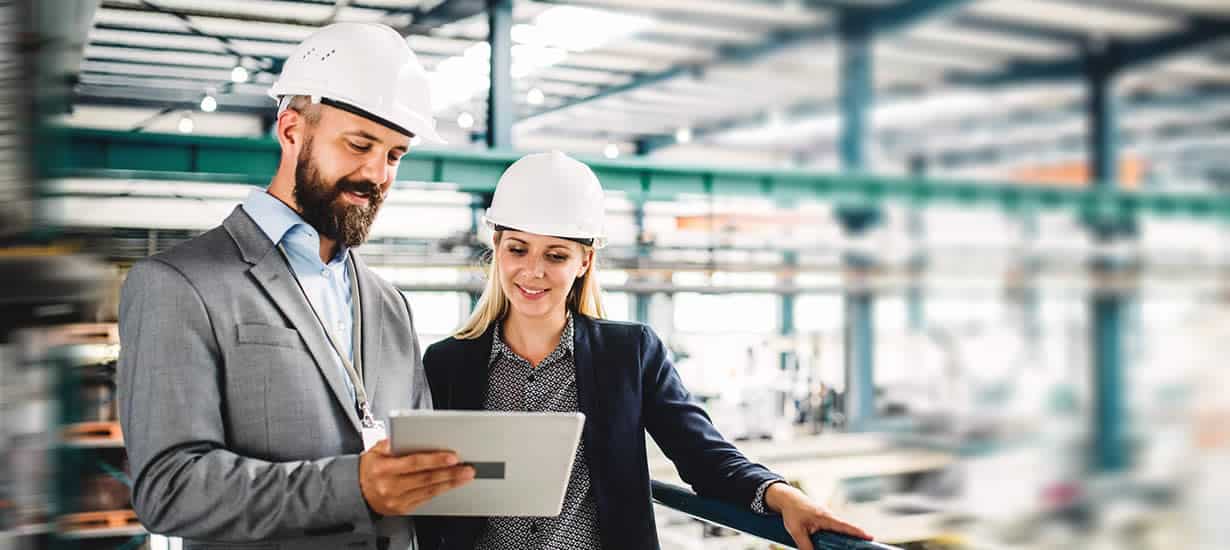
Learn how predictive maintenance is key to smart, efficient facility management and how this transformative approach can boost your operations.
Applying effective and efficient maintenance strategies is a crucial responsibility for facilities managers. A successful PDM strategy offers a proactive approach, enabling facility managers to anticipate and address potential issues before they disrupt operations. A predictive approach can enhance asset reliability, reduce unplanned downtime, and achieve cost savings.
What is Predictive Maintenance (PDM)?
Predictive maintenance is a facility and equipment upkeep strategy that uses common predictive maintenance tools, data analytics, and inspection results to anticipate current and future maintenance needs.
Why PDM Maintenance Matters for Facility Managers
Unexpected equipment failures can significantly disrupt a facility’s operations and budget. Implementing a PDM strategy empowers you to anticipate potential issues and address them proactively, minimizing disruptions and unplanned expenses.
Through data analytics and inspection results, PDM allows for timely interventions that enhance asset reliability, reduce downtime, and lead to significant cost savings. In fact, proactive maintenance, like PDM, can reduce maintenance costs by 12–18% compared to reactive maintenance strategies.
Embracing PDM helps establish a maintenance schedule that streamlines your maintenance processes and provides peace of mind, knowing that your facility is operating efficiently and effectively.
Key Differences: Predictive vs Preventive Maintenance
Maintenance strategies generally fall into three categories: preventive, predictive, and reactive. Depending on asset value, criticality, and acceptable downtime, each strategy has a valid role in maintenance planning.
Maintenance Type | Approach | Timing | Cost Efficiency | Ideal For |
PDM (Predictive) | Data-driven condition monitoring | Just before failure is predicted | High (minimal waste) | Critical, expensive assets |
PM (Preventive) | Calendar-based scheduled tasks | Fixed intervals regardless of condition | Medium (some unnecessary work) | Standard equipment with consistent wear patterns |
Reactive | Fix after failure occurs | After breakdown | Low (emergency costs, downtime) | Non-critical, easily replaceable items |
A preventative maintenance approach uses predetermined schedules and conditional thresholds to trigger maintenance activities.
Predictive maintenance anticipates potential breakdowns and triggers specific maintenance tasks to avoid failures.
Reactive maintenance triggers once an equipment failure or breakdown has occurred, making it suitable for low-value and non-critical assets.
Facility managers might wonder if PDM is truly better than preventive maintenance or if reactive fixes can suffice. As the table shows, each approach has its place, but PDM offers the optimal balance for high-value assets where unexpected downtime would be particularly costly. PDM uses real-time analytics to detect early signs of failing equipment and trigger timely maintenance, often before any malfunction becomes apparent.
PDM activities often involve safely shutting down systems, prepping tools or parts, and coordinating service providers before issues escalate.
Key Components of a PDM Maintenance System
Predictive maintenance solutions utilize a variety of mechanisms to gather and analyze the data necessary to anticipate problems. These include:
1. IoT Sensors for Data Collection
Predictive maintenance technologies rely heavily on sensors that monitor the condition of equipment and components during operation. Internet of Things (IoT) connections enable sensors to transmit data to a central server for data analysis.
2. Data Analysis and Machine Learning Algorithms
Predictive maintenance plans use advanced data analysis to compare equipment conditions and asset performance with historical equipment failure data. AI and machine learning algorithms continually improve their ability to anticipate problems and increase their accuracy over time.
3. Computerized Maintenance Management Systems (CMMS)
Facilities managers often utilize CMMS software platforms to aggregate and analyze IoT data to inform predictive and preventive maintenance activities.
Industry Applications & Standards for PDM
Automotive, Aviation, and Manufacturing
In automotive production lines, real-time condition monitoring prevents assembly line halts that can cost thousands per minute. Major manufacturers like Ford and Toyota have implemented predictive maintenance (PDM) strategies that have reduced unplanned downtime by over 30%.
Meanwhile, aviation heavily relies on advanced predictive analytics RUL (remaining useful life) models to increase aircraft safety and comply with strict FAA regulations. Aircraft engines, which cost millions to replace, benefit particularly from vibration analysis and oil testing to prevent catastrophic failures.
Manufacturing facilities using high-speed production equipment find that PDM extends machine lifecycles by 20-40% while dramatically improving product quality by ensuring equipment operates within optimal parameters.
Aligning with ISO 55000 & ISO 14224
Following ISO 55000 guidelines ensures consistent asset management practices aligned with predictive maintenance techniques and strategies. This international standard provides a framework for establishing, implementing, and improving an asset management system that complements predictive approaches.
ISO 14224 focuses on collecting and exchanging reliability and maintenance data for equipment. The ISO 14224 framework offers valuable guidance for structuring your PDM data collection methods. Aligning with these standards improves maintenance operations and can also be a compelling point when justifying PDM investments to executive leadership.
Common Predictive Maintenance Techniques for Facilities
Predictive maintenance relies on various techniques to monitor asset conditions and identify potential issues. Some methods can be performed by IoT devices to provide sensor data for predictive analytics, while others may require a service provider with specialized equipment to detect defects that could potentially impact asset integrity.
Vibration Analysis
Sensors continuously monitor vibration levels in high-speed rotating equipment like motors and pumps. These sensors feed real-time data to a central system for immediate analysis and alerts.
Power Quality Analysis
Integrated sensors monitor electricity levels and feed real-time sensor data to the central system. Power quality analysis is often part of an energy management program or used to monitor critical electrical equipment.
Infrared Thermography
Trained technicians use specialized infrared cameras to identify fatigue and microscopic cracks accumulated through wear and tear over time. Fluid leaks and potential fire hazards from overheated components are some other common issues that infrared cameras can detect.
Oil Analysis
Oil analysis typically involves collecting oil samples and sending them to a laboratory for a comprehensive analysis. Analysis can help detect a variety of issues by identifying contaminants such as wear particles or fluid intrusion. This technique requires specialized equipment and expertise, which makes off-premises services a common choice.
Ultrasonic Testing
Ultrasonic testing works by reflecting high-frequency sound waves off of a surface and translating the waves into data as they echo back into the device’s sensor. Ultrasound can detect the smallest flaw, perfect for inspecting welds and high-stress components. While some sensors offer limited ultrasonic capabilities, a trained technician with specialized ultrasonic testing equipment typically yields more thorough results.
Benefits of PDM for Facilities Managers
PDM technology provides many advantages to facilities, including reduced maintenance costs, more dependable equipment, and safer working conditions. By anticipating problems before they arise, the predictive approach offers these benefits and much more
1. Cost Savings and ROI
PDM pays for itself many times over in the long term. Catching issues before they arise substantially reduces unnecessary maintenance costs, as well as reducing equipment failures that can result in significant unplanned expenses. You’ve already invested in advanced maintenance tools, and PDM ensures you get the most value from them, culminating in significantly reduced operating expenses.
2. Improved Asset Reliability and Longevity
Predictive maintenance programs enable maintenance teams to address issues before they lead to equipment failure by continuously monitoring equipment performance and identifying wear and tear early. Catching minor problems and preventing small issues from escalating into major breakdowns extends equipment lifecycles and optimizes efficiency, ultimately increasing asset value. For best results, pair PDM with a holistic asset performance management approach that considers the entire lifecycle of your facility’s equipment.
3. Reduced Downtime and Increased Productivity
A predictive maintenance program puts the power of foresight into facility managers’ hands, enabling them to attack non-critical issues during preventive maintenance and address critical issues immediately. This proactive approach to maintenance reduces the likelihood of malfunctions and failures that lead to extended periods of unplanned production downtime, greatly improving equipment and employee productivity as a result. When an entire facility grinds to a halt, the pressure is on. PDM helps you avoid those emergencies and lets you maintain peace of mind while you maintain operations.
4. Enhanced Safety and Compliance
Through continuous monitoring, teams are alerted when malfunctions that could lead to hazardous conditions are likely to occur, and safety-critical systems, such as high-speed rotating equipment, usually automatically shut down at the first sign of a dangerous situation. These mechanisms significantly reduce the chances of unsafe events and prevent the likelihood of falling out of compliance with industry safety standards and government safety regulations. If you’re under pressure to keep systems operational while protecting your team, PDM helps you do both while protecting your facility’s reputation in the process.
Overcoming Challenges in Predictive Maintenance Implementation
While a successful predictive maintenance program can help enhance asset performance and extend their life, facilities managers can face some obstacles when trying to adopt this strategy.
1. Initial Cost and ROI Justification
A predictive maintenance plan can require a substantial initial investment in equipment and training. It may take some effort to get leadership on board. However, when weighing the long-term benefits to production and the budget, the savings in operational costs and worker safety typically far outweigh the upfront costs.
2. Data Quality and Integration Issues
Purchasing sensors and software compatible with your current maintenance management system is vital. Saving money on incompatible components may cost a company significantly as IT staff work to make new devices and existing systems work together.
3. Skill Gap and Training Requirements
The concepts are relatively easy to grasp, but predictive maintenance programs have a lot of moving parts. Various levels of staff play different roles in the processes. It takes some time and investment to build proficiency.
4. Resistance to Change
People tend to prefer the comfort of systems and practices they already know. Clear, honest communication is essential for earning buy-in from veteran personnel and receiving full cooperation throughout the transition.
Step-by-Step Implementation for Facility Managers
PDM solutions require some planning and strategic implementation. The following steps will help guide you toward rolling out a program that helps predictive maintenance work effectively for your organization. It can seem daunting to push for new technology while there are daily fires to put out. However, implementing PDM step-by-step alongside a preventive maintenance program and routine maintenance can alleviate those emergencies in the long run, letting you focus on big-picture strategies that drive real results.
1. Assessing Current Processes & Asset Prioritization
Review all maintenance SOPs and historical documentation. Perform a cost analysis that includes unplanned downtime costs, material expenses, and the cost of lost production. Identify areas for consolidation. Run projections for alternative processes that compare the potential effectiveness and cost with current maintenance practices.
Evaluate all maintenance-dependent assets and identify the highest-risk, highest-value, and safety-critical ones. PDM helps safeguard against events that could significantly impact the company budget and occupant safety. A robust CMMS integration strategy that centralizes data for easy analysis will help further drive success.
2. Selecting IoT Sensors & Integrating with CMMS/EAM
Find high-quality IoT sensors and monitoring devices that are compatible with your current CMMS/EAM system. Install the devices in critical assets and calibrate as needed. Perform startup tests to ensure they work together as expected. Real-time condition monitoring warns you before minor issues escalate.
Bring your predictive maintenance devices and controlling software together with your current CMMS or EAM system. Ensure monitoring tools directly feed into your maintenance system for real-time alerts and comprehensive reporting. Integration is vital for streamlining operations and giving your organization effective predictive maintenance capabilities. A well-thought-out PDM architecture ensures seamless data flow for real-time alerts.
3. Overcoming Challenges (Cost, Training, Change)
Educate your team on new predictive maintenance processes to ensure a smooth transition. Highlight the benefits of a predictive maintenance program, such as greater efficiency and reduced unplanned downtime. Proper training and clear communication are essential for managing this shift in practice.
As one facility manager put it, “Implementing PDM was easier than we thought. Staff took pride in using cutting-edge technology.”
Start here to find a preventative maintenance checklist to help you schedule maintenance and guide your rollout.
KPIs and ROI of Preventative Maintenance
OEE, Reliability Indices, and Mean Downtime
To improve something, you have to know where things stand, and predictive maintenance offers no shortage of metrics to work with. Key indicators such as overall equipment effectiveness (OEE), mean time between failures (MTBF), and mean downtime (MDT) help gauge performance and estimate how long assets can operate before requiring maintenance.
These KPIs create a high-level picture of equipment health and operational stability. For example, understanding your MTBF trendlines can help determine when to intervene and how to plan for optimal uptime.
Linking Data Insights to Budget Approvals
Performance metrics provide valuable information for making a case to leadership. Financial approval for PDM initiatives often hinges on clearly quantifiable returns. Fortunately, predictive maintenance produces plenty of data that ties directly to cost savings and risk reduction.
Together, KPI data points tell a compelling story: predictive maintenance is smart business. A strong ROI case should include:
- Cost of equipment replacement vs. extended lifecycle value
- Labor savings from fewer emergency callouts
- Avoided production losses through planned intervention
- Energy efficiency gains from smoother system performance
- Fewer safety incidents due to proactive detection and response
Data Analysis and Interpretation for Facilities Managers
Predictive maintenance relies on data streamed from a variety of sources. Understanding the data as it’s presented is key to taking appropriate action.
Understanding Predictive Maintenance Reports and Dashboards
Every software system is different. Familiarize yourself with the predictive analytics, dashboards, and reports that your maintenance management platform provides. Most dashboards color-code metrics to inform users when equipment is approaching its limit. Review equipment manufacturer recommendations for alert levels and automatic emergency shutdown thresholds.
Making Data-Driven Maintenance Decisions
The data analytics that predictive maintenance mechanisms provide give an abundance of information to help make informed asset and equipment choices that can improve efficiency and drive down operating costs. Sensor data can help make a variety of determinations for your facility, such as shutdown planning for repairs, replacing outdated equipment prone to failure, and consolidating maintenance efforts to tackle additional upkeep tasks during planned downtime.
When to Choose Predictive Maintenance
The benefits of a predictive maintenance plan are far-reaching. Companies typically choose predictive maintenance to help extend the lifespan of high-value equipment and ensure that critical assets perform optimally.
Industries utilizing safety-critical equipment such as chemical vats or smelting furnaces prioritize safety as much as operational efficiency. Predictive maintenance helps ensure equipment safety and adherence to compliance standards.
Embracing Predictive Maintenance for Smarter Facility Management
Predictive maintenance is a smart, proactive solution for ensuring equipment works optimally and facilities operate efficiently. Predictive mechanisms make it possible to accurately anticipate maintenance needs and provide insights into equipment patterns of behavior that can inform a wide variety of executive decisions. By forecasting issues, the strategy keeps maintenance teams ahead of the game, helping avoid unwanted surprises.If you’re ready to transform your facility maintenance strategy and learn how to perform maintenance more effectively, contact us for a personalized predictive maintenance consultation or request a free demo. Start optimizing your operations today.