Breakdown Maintenance: A Comprehensive Guide for Facilities Managers
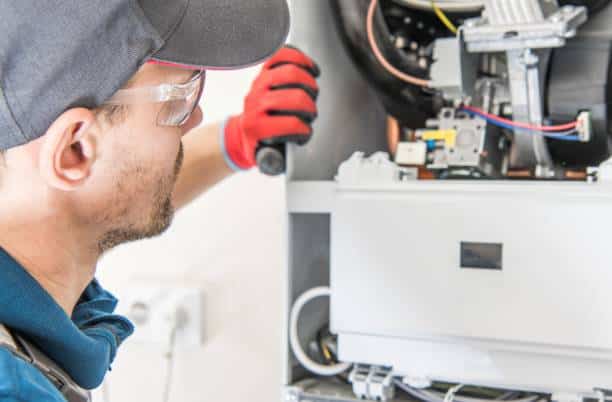
Understanding breakdown maintenance strategies, whether planned or unexpected, is crucial for keeping your operations running smoothly. This guide dives deep into the nuances of breakdown maintenance, equipping you to manage equipment failures efficiently and minimize downtime.
What is breakdown maintenance?
Breakdown maintenance refers to addressing failures after they occur rather than attempting to prevent them in advance. It’s a reactive strategy that only repairs or replaces equipment when necessary.
Breakdown maintenance helps reduce unnecessary maintenance on non-critical equipment. However, it requires a well-thought-out plan to implement efficiently. By understanding the role of breakdown maintenance, facility managers can develop strategies that balance costs, downtime, and safety.
Types of breakdown maintenance
Breakdown maintenance is typically categorized into two main types — planned and unplanned maintenance. Each serves a distinct role in facility management, depending on the criticality of equipment and your operational priorities.
Planned breakdown maintenance
Typically, non-critical assets or equipment receive planned breakdown maintenance, where failure has little to no impact on operations.
- Run-to-failure maintenance strategy: Facilities managers adopt this strategy for predictable wear-and-tear items, such as light bulbs or small appliances, to save on unnecessary preventive maintenance costs.
- When to use planned breakdown maintenance: It’s ideal for assets that are inexpensive to replace, have readily available spare parts, or do not pose safety risks if they malfunction.
Unplanned breakdown maintenance
Unplanned breakdown maintenance occurs when equipment fails unexpectedly, requiring immediate attention to restore functionality.
- Corrective maintenance: This involves repairing faulty equipment after failure and restoring it to optimal functionality.
- Reactive maintenance: Reactive maintenance addresses issues as they arise, often requiring rapid responses and emergency repairs.
- Emergency maintenance: A subset of reactive maintenance, emergency maintenance is performed when equipment malfunctions pose significant risks to safety, compliance, or production.
Advantages and disadvantages of breakdown maintenance
Breakdown maintenance offers simplicity and cost benefits for certain equipment but has some drawbacks, particularly for vital assets. Understanding both sides helps determine when this approach is appropriate.
Pros of breakdown maintenance
- Cost savings on non-critical equipment: For assets like light bulbs or inexpensive components, breakdown maintenance eliminates the costs of unnecessary preventive measures.
- Reduced maintenance staff requirements: A reactive strategy enables you to concentrate maintenance efforts only when they are actually required.
- Simplified maintenance planning: Without detailed preventive schedules, planning becomes more straightforward for non-essential assets.
Cons of breakdown maintenance
- Increased downtime potential: Unexpected equipment failures can halt operations, leading to costly downtime.
- Higher critical equipment repair costs: For key assets, reactive maintenance often involves emergency repairs that are more expensive than proactive maintenance approaches.
- Safety risks and compliance issues: Equipment failures can create hazardous conditions or lead to violations of safety regulations.
A proactive approach, such as preventive or predictive maintenance, usually works best for safety-critical equipment and assets integral to operations. Reactive maintenance practices typically suit less essential items.
Implementing an effective breakdown maintenance strategy
By following structured steps and adhering to best practices, facilities managers can maintain efficiency while reducing risks by utilizing breakdown maintenance practices.
Step-by-step guide for facilities managers
Establishing an effective breakdown maintenance strategy begins with understanding your assets and creating clear protocols to respond to equipment failures.
- Assessing equipment criticality: Evaluate which assets are vital to operations and prioritize those for preventive or predictive maintenance.
- Developing response protocols: Establish clear procedures for identifying, reporting, and addressing equipment failures to reduce reaction time.
- Training maintenance staff: Equip your team with the skills and knowledge to handle breakdowns effectively, including diagnostics and emergency repairs.
- Establishing inventory management procedures: Maintain adequate spare parts and tools to avoid repair delays, particularly for critical equipment.
Best practices and pitfalls to avoid
Properly utilizing reactive and preventive maintenance strategies is vital for long-term success. Adopting best practices can improve efficiency, and avoiding common pitfalls ensures resources are used effectively. These guidelines will help you refine your approach to breakdown maintenance over time.
- Balancing breakdown and preventive approaches: Combine reactive strategies with preventive measures to minimize unnecessary downtime while controlling costs.
- Documenting maintenance activities: Keep detailed records of all maintenance actions to identify trends and optimize future strategies.
- Continuous improvement strategies: Regularly review and refine your maintenance processes based on performance metrics and evolving operational needs.
Breakdown maintenance vs. preventive maintenance
Choosing between breakdown maintenance and preventive maintenance depends entirely on your organization’s operational goals, budget, and equipment criticality. Understanding the key differences and similarities will help create a balanced approach.
Key differences and similarities
Breakdown maintenance is a reactive approach, addressing failures after they occur. Preventive maintenance is proactive, aiming to prevent failures in the first place. Both approaches aim to keep equipment functional and safe.
- Breakdown maintenance reacts to failures, often requiring immediate action.
- Preventive maintenance schedules routine checks and repairs to avoid unexpected breakdowns.
- Both strategies contribute to operational efficiency but require careful planning to achieve the best results for your organization.
When to choose breakdown maintenance over preventive maintenance
Breakdown maintenance allows facilities managers to conserve resources and manage assets better by not conducting unnecessary preventive efforts on low-priority items.
- Breakdown maintenance is ideal for inexpensive, easily replaceable equipment.
- This approach works best for assets with predictable lifespans and readily available spare parts.
- A breakdown strategy is useful in situations where downtime is non-disruptive.
Hybrid approaches for optimal facility management
Breakdown and preventive maintenance each have distinct advantages.
- Preventive maintenance works best for high-value or safety-critical assets.
- Breakdown maintenance is a popular approach for most non-critical, low-cost equipment.
- Regular evaluations help facility management adjust the balance based on performance data and operational needs.
Role of CMMS in breakdown maintenance
A computerized maintenance management system (CMMS) can automate processes and provide real-time data. This can streamline maintenance workflows, reducing downtime.
Work order management
A CMMS centralizes work order creation, assignment, and tracking, ensuring timely responses and reducing delays. Facilities managers can prioritize tasks based on asset criticality and monitor real-time progress.
Asset tracking and history
CMMS tools provide detailed records that help identify failure patterns and inform decisions about whether to repair or replace equipment, optimizing asset performance.
Reporting and analytics
CMMS platforms generate insights on key metrics like downtime costs, response times, and repair success rates. These analytics let you measure the effectiveness of breakdown maintenance strategies and identify areas for improvement.
Analyzing breakdown maintenance data
Robust data analysis helps facilities managers pinpoint inefficiencies, reduce downtime, and optimize overall operations by tracking key metrics and identifying patterns.
Key performance indicators (KPIs) for facilities managers
Effective maintenance management relies on measurable KPIs. These metrics help facilities managers assess equipment reliability, repair efficiency, and overall performance:
- Mean time between failures (MTBF): Measures the average time between equipment breakdowns, offering insights into reliability.
- Mean time to repair (MTTR): Tracks the average time needed to fix equipment, highlighting repair efficiency.
- Overall equipment effectiveness (OEE): Evaluates equipment performance based on availability, performance, and quality metrics.
Using data to improve facility performance
Analyzing maintenance data provides actionable insights that drive continuous improvement. Such insights include:
- Identifying recurring issues and root causes: Pinpoint patterns in equipment breakdowns to implement targeted solutions and reduce repeat breakdowns.
- Optimizing maintenance schedules based on historical data: Adjust maintenance plans based on past trends to service critical assets ahead of potential issues.
Balancing breakdown maintenance with other strategies
Achieving an effective maintenance strategy often requires blending reactive and proactive approaches. By integrating breakdown maintenance with preventive and predictive methods, facilities managers can create a comprehensive plan tailored to their specific operational needs.
Create a comprehensive maintenance plan
A well-rounded maintenance plan ensures that critical assets are prioritized while lower-priority equipment receives attention as needed.
Integrate breakdown maintenance facility management
Integrating breakdown maintenance into your broader strategy requires thoughtful planning to minimize disruptions. Effectively communicate protocols to maintenance teams. Carefully allocate your resources and offer technology support to monitor performance and streamline processes.
Adapt strategies to fit your needs
No two facilities are alike, and maintenance strategies should reflect the unique needs of your operation based on facility type and equipment criticality. Effectively communicate protocols to maintenance teams and offer technology support to monitor performance and streamline processes.
Optimizing breakdown maintenance for your facility
Breakdown maintenance is essential for any facility management strategy, but its success depends on well-planned implementation. By understanding its pros and cons, integrating it with other approaches like preventive maintenance, and leveraging tools such as CMMS, you can reduce downtime, control costs, and maintain a safe work environment.
Every facility is unique, and there’s no one-size-fits-all solution. Take the time to evaluate your assets, analyze maintenance data, and refine your strategies to strike the right balance for your operation. Adopt a technology solution like ServiceChannel for a more streamlined solution to centralize data and enhance decision-making across your maintenance team.