Reactive Maintenance: A Comprehensive Guide for Facilities Managers
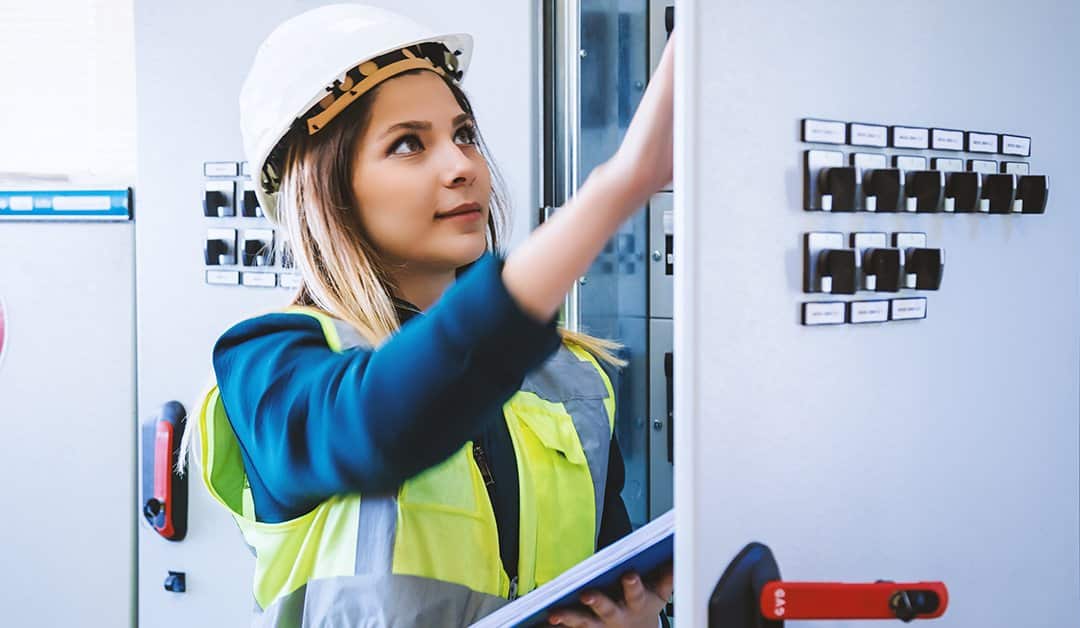
Reactive maintenance is the direct opposite of proactive maintenance. Instead of performing routine maintenance tasks to prevent failures, reactive maintenance means that your maintenance teams wait until failure occurs to perform work.
Such equipment failures may be unplanned; however, a purely reactive approach may also involve adopting the run-to-failure maintenance strategy. That means that the equipment is intentionally used until it breaks down.
The disadvantages of reactive maintenance may seem obvious. However, many advantages also exist. This maintenance strategy is not necessarily bad; it simply needs to be managed correctly.
What is Reactive Maintenance?
Reactive maintenance (also commonly known as corrective maintenance) involves repairing or replacing equipment only once it has malfunctioned or broken down. While it is unwise to rely solely on reactive maintenance vs. preventive maintenance, your facility should also have a solid reactive maintenance approach so that you can efficiently perform emergency repairs as needed.
When is Reactive Maintenance Appropriate?
Reactive maintenance is appropriate when the cost of proactive maintenance outweighs repair costs or when some unplanned downtime is acceptable. Given that criteria, it makes the most sense to apply reactive maintenance to assets that are non-critical, inexpensive, or rarely fail.
How to Identify Non-Critical Assets
Evaluate both financial and operational factors to determine which assets are non-critical. Consider the total cost of ownership, including the initial and repair costs. Also, assess how potential downtime would affect productivity or if there are potential safety risks.
A good example of an asset that could go either way is a light bulb. In most cases, light bulbs are inexpensive to replace, and a burned-out light has little impact on safety or operating conditions. Therefore, reactive maintenance is sufficient.
However, there are situations when a burned-out light bulb could create a significant safety risk, or you may use specialty lighting that is expensive to replace. In those cases, lighting would instead need a preventive maintenance approach.
Types of Reactive Maintenance
Depending on the level of urgency and the condition of the equipment, several types of reactive maintenance strategies are available. The type of reactive maintenance you use may vary per asset. Here are the 3 most common categories.
Run-to-Failure Maintenance
Run-to-failure maintenance involves allowing equipment to operate until it breaks down. Repairs or replacements are made only after equipment malfunctions. This approach is typically used alongside predictive maintenance to pinpoint when failure is about to occur.
Unplanned Maintenance
Unplanned maintenance happens when unexpected equipment issues arise that were not previously scheduled. These issues may not be an equipment failure. They may simply cause the asset to underperform or be signs of future equipment failures if not immediately addressed.
Breakdown Maintenance
Breakdown maintenance is similar to unplanned maintenance, but it differs slightly. This type of reactive maintenance only happens after equipment failures. However, it may or may not be an emergency maintenance situation.
Emergency Maintenance
Emergency maintenance is the most urgent form of reactive maintenance. It is performed when critical equipment experiences a failure that threatens safety, production, major operational functions, or property damage. Such maintenance tasks must be performed immediately upon detection.
The Impact of Reactive Maintenance on Facility Performance
Energy Efficiency
Relying too much on reactive maintenance negatively impacts energy efficiency. When equipment is allowed to run until failure, it typically consumes more energy than it would have had it gone through routine inspections. So, consider the energy consumption of your assets before you adopt a reactive maintenance plan for them.
Occupant Satisfaction
Reactive maintenance can quickly address issues that directly impact occupants. When critical systems fail, immediate repairs restore comfort and functionality. Therefore, timely repair requirements should be the bare minimum of your reactive maintenance strategy.
Regulatory Compliance
Delaying maintenance until failure increases the risk of non-compliance with regulatory standards. Avoiding planned maintenance for critical assets can lead to safety hazards. Be very careful about which strategies you choose for which assets.
Tips on Implementing an Effective Reactive Maintenance Strategy
Sort Non-Critical Assets by Priority
Some non-critical assets have more of an impact than others. For example, a malfunctioning HVAC system in a data center could lead to hardware overheating without causing significant delays in overall operations. Such assets should be prioritized over assets with a lower impact.
Develop a Clear Response Protocol
Establish specific procedures for reactive maintenance activities. Ensure your team knows the steps to take when equipment fails, including troubleshooting guidelines, escalation paths, and documentation processes.
Leverage Data for Continuous Improvement
Collect and analyze data on the reactive maintenance performed. This information helps identify patterns in equipment failures. Recognizing such patterns helps you refine maintenance schedules or switch to a preventive approach for certain assets.
Tools and Technologies for Reactive Maintenance Strategies
Decision Matrices and Cost-Benefit Analysis Templates
Decision matrices and cost-benefit analysis templates help determine when reactive maintenance is the most cost-effective approach. Repair costs, equipment downtime, and the importance of each asset are all considered to help managers make informed decisions.
IoT Sensors
IoT sensors are monitoring tools that provide real-time data on equipment performance. Machine sensors detect anomalies early, which helps your maintenance team address potential issues before they escalate into critical failures.
CMMS Software
CMMS software is incredibly helpful for organizing your reactive maintenance tasks. It helps schedule major repairs, monitor equipment history, and prioritize urgent issues. It also makes it easier for your maintenance teams to see when and where work is needed.
Mobile Apps
Mobile apps allow technicians to receive real-time alerts, access work orders, and communicate effectively while on the go. These apps improve response times and ensure maintenance teams can resolve issues efficiently.
How to Transition from Reactive to Preventive Maintenance
Assess Your Current Maintenance Program
Before transitioning, it’s important to evaluate your existing maintenance and asset management practices. Look at how often your team responds to unplanned repairs, the procedures they follow, and whether they have the tools and training to implement preventive maintenance. Identifying these areas will help you prioritize improvements.
Develop a Phased Approach
A phased approach allows for a smoother transition from reactive to preventive maintenance. Start by implementing preventive measures on critical equipment while maintaining reactive strategies for lower-priority assets. Gradually expanding your proactive maintenance plan will help your team adapt more easily.
Plan for Potential Implementation Challenges
Proactively plan for the challenges you may face during the transition. Addressing these issues in advance helps make the process run smoother. Preparation involves securing resources, organizing training, and managing any pushback from your team.
Here are some examples of challenges you can solve.
- Prioritize essential investments and phase in new tools gradually if your budget is limited
- Schedule focused training sessions if your team lacks expertise in preventive maintenance
- Clearly explain the long-term benefits to overcome resistance to changing practices
- Start by upgrading critical systems first if your equipment or software needs an update
Balance Reactive and Preventive Maintenance with ServiceChannel
The best approach for most facilities is to balance regular preventive maintenance with reactive maintenance activities. This combined strategy helps extend asset lifespans by catching issues early without overcommitting resources to unnecessary repairs.
Achieve this perfect balance with ServiceChannel. Our platform offers real-time data and predictive insights that allow you to detect where repairs are needed. With our tools, you can pinpoint exactly when preventative maintenance work is ideal and when emergency maintenance work is required.