Proactive Maintenance: A Comprehensive Guide for Facilities Managers
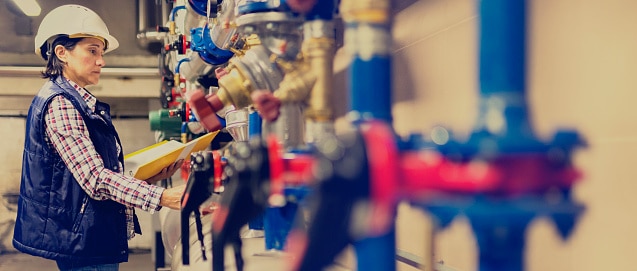
If you’re a facility manager, you’re always looking for ways to improve efficiency and extend the lifespan of your assets. Proactive maintenance offers a powerful approach to managing facility assets. Let’s explore how proactive maintenance can help you build a robust maintenance plan to enhance the efficiency of your operations.
What is Proactive Maintenance?
Proactive maintenance uses inspections, schedules, and predictive strategies to address issues before they grow into larger problems. By proactively maintaining assets, you reduce the cumulative wear and tear that can accelerate their deterioration, resulting in extended life cycles.
In contrast, reactive maintenance waits until an asset is experiencing visible issues or has fully failed before addressing the problem. While this strategy works fine for low-value assets, reactive maintenance can diminish an asset’s life cycle more quickly than applying a proactive method.
Understanding Proactive Maintenance Strategies
Proactive maintenance encompasses a range of strategies that enable facility managers to stay ahead of equipment failures and unplanned downtime. These approaches are designed to optimize maintenance efforts and ensure assets are functioning at their best. By understanding the types of proactive strategies, you can determine the best approach for your facility’s needs.
Preventive Maintenance
Preventive maintenance is like a routine checkup for your facility’s equipment. By scheduling maintenance tasks at regular intervals or performing upkeep based on equipment usage, you can help prevent unexpected breakdowns.
Benefits of Preventive Maintenance for Facility Managers:
- Cost-effective: Preventive maintenance reduces costly emergency repairs and extends the lifespan of equipment, making it a cost-effective approach over time.
- Increased equipment reliability: Addressing wear and tear early allows preventive maintenance to keep equipment operating smoothly and reduce unexpected downtime.
- Improved safety: Regular maintenance ensures that safety-critical equipment is functioning properly, minimizing risks to workers and the facility.
Limitations of Preventive Maintenance for Facility Managers:
- Resource-intensive: Preventive maintenance can require more initial labor and resources because it involves servicing based on schedules rather than conditions.
- Potential for over-maintenance: Some assets may receive maintenance before it’s necessary, often leading to unnecessary costs or downtime.
- Challenging to optimize: Without the right data, it can be challenging to determine the ideal maintenance frequency, leading to either too much or too little upkeep.
Predictive Maintenance
Predictive maintenance uses analytics and condition monitoring to anticipate equipment failures and address issues before they escalate. This method reduces downtime and helps you allocate resources more effectively, ensuring maintenance is performed only when needed.
Benefits of Predictive Maintenance for Facility Managers:
- Reduced downtime: By predicting equipment failures before they happen, predictive maintenance minimizes unplanned downtime.
- Cost efficiency: Maintenance is performed only when necessary, helping to avoid maintenance costs due to unnecessary work.
- Extended asset life: Predictive maintenance helps extend equipment lifespan by catching issues early and preventing sustained wear and tear.
Limitations of Predictive Maintenance for Facility Managers:
- Data dependency: Predictive maintenance requires accurate performance data. Without the right sensors and monitoring systems, it can be difficult to implement this strategy effectively.
- Upfront costs: The technology required for predictive maintenance often comes with significant initial costs.
- Skill gaps: Implementing predictive maintenance may require specialized skills not readily available in every facility maintenance team.
Condition-Based Maintenance
Condition-based maintenance focuses on performance and status tracking. Maintenance tasks trigger when assets meet specific conditions, such as changes in vibration or pressure. This allows you to act quickly when equipment shows signs of problems.
Benefits of Condition-Based Maintenance for Facility Managers:
- Optimized maintenance efforts: This approach reduces unnecessary upkeep and saves time by only performing needed maintenance.
- Improved equipment reliability: Real-time monitoring lets you address potential issues before they become problems, enhancing asset reliability.
- Cost savings: Fewer unnecessary repairs and less downtime contribute to lower upkeep costs, allowing more effective maintenance budget allocation.
Limitations Condition-Based Maintenance for Facility Managers:
- Initial expense: Condition-monitoring sensors and systems for real-time tracking can be costly.
- Complexity: This strategy typically involves system integration and often requires additional staff training.
- Data overload: Large volumes of performance data can become challenging to manage without proper filtering and analysis.
Implementing Proactive Maintenance in Facilities Management
Setting up proactive maintenance strategies takes planning and resources. By laying out a solid implementation plan, you can avoid many challenges that might slow your progress. These steps can help guide you through your proactive maintenance implementation plan.
Conducting Facility Condition Assessments
Understanding your facility’s current state is essential. A thorough evaluation provides a baseline of assets, equipment, and systems, helping to focus maintenance efforts on areas where they are needed most.
Key Components of a Thorough Assessment:
- Asset inventory: Document all critical equipment and systems and record their current condition.
- Inspection and testing: Examine the functionality of each asset and identify areas that may require immediate attention.
- Data collection: Gather historical maintenance data to comprehensively understand equipment reliability and future maintenance needs.
With a clear understanding of the facility’s condition, you can then develop a proactive maintenance plan that prioritizes the most critical assets and ensures the effective use of your maintenance budget.
Developing a Proactive Maintenance Plan
Creating an effective proactive maintenance plan is key to staying ahead of equipment failures and keeping operations running smoothly. A solid plan will help you set clear maintenance goals, create efficient workflows, and allocate resources effectively. This increases asset reliability and ensures that your facility remains operational with minimal disruptions.
1. Set Maintenance Goals and Priorities
Start by determining your facility’s specific maintenance goals. Identify which assets are most important for your operations and establish priorities for upkeep. This helps determine where to put your resources.
2. Create Maintenance Schedules and Workflows
Establish maintenance timetables that fit your operational demands. You can set up workflows that specify how to assign, track, and complete maintenance tasks using automated tools like a computerized maintenance management system (CMMS) to streamline processes.
3. Allocate Resources
Allocating resources properly means knowing where to invest in preventive measures, such as routine inspections, and when to focus on critical repairs. Providing your team with the right tools, staff, and budget lets them effectively implement the plan and maintain asset reliability without overspending or overlooking critical tasks.
Leveraging Technology for Proactive Maintenance
Technology plays a vital role in just about any modern proactive maintenance strategy. It enables facility managers to monitor equipment in real-time and accurately predict maintenance needs. By incorporating modern tools, you can enhance efficiency and prevent equipment failure before it happens.
Computerized Maintenance Management Systems (CMMS)
A CMMS serves as the backbone of modern maintenance operations, automating workflows, tracking assets, and organizing maintenance tasks. These platforms provide a centralized hub to streamline maintenance processes, offering an array of features such as:
CMMS Features and Benefits:
- Automated scheduling: CMMS platforms can automatically generate maintenance schedules based on usage or time intervals, ensuring critical tasks are never overlooked.
- Centralized data: Easily access detailed maintenance histories, asset performance data, and service records from one location, making it easier to track trends and monitor equipment reliability.
- Work order management: Simplify work order processes by letting managers assign tasks, track progress, and monitor maintenance performance.
- Resource allocation: Gain insights into labor and inventory needs to ensure that the right resources are available when maintenance is required.
Selecting the Right CMMS
The ideal CMMS system should align with your facility’s needs, scale with your operations, and work with your existing systems. Focus on user-friendly interfaces, customizable features, and the ability to handle multiple assets across various locations. Researching user experiences can really tip the scales one way or the other. Once selected, a thorough implementation plan—including staff training and data migration—ensures a smooth transition and sets the stage for long-term success.
Internet of Things (IoT) and Sensors
IoT sends real-time data to a centralized system for aggregation and analysis by embedding sensors into critical assets. IoT sensors can monitor various systems, from HVAC and lighting to security and energy management. This helps optimize building performance, reduce energy waste, and improve the overall efficiency of critical systems.
IoT integrates seamlessly with many existing maintenance and asset management systems, enabling real-time asset monitoring and improving decision-making. The continuous stream of information IoT and sensors provide enables facility managers to detect issues before they escalate and schedule maintenance activities based on actual asset conditions rather than time intervals.
Data Analytics and Artificial Intelligence (AI)
Undoubtedly, AI is making a tremendous impact on all aspects of the industry, including maintenance planning. Through machine learning tools and advanced analytics, maintenance management systems can sift through historical conditions and performance data to anticipate potential equipment failures.
Regulatory Compliance and Proactive Maintenance
Compliance isn’t just a legal obligation; it’s a key factor in ensuring worker safety and the longevity of assets. Proactive maintenance efforts are vital in helping facility managers meet regulatory requirements and maintain safety standards. By staying ahead of potential problems, you can avoid fines and reduce workplace hazards, ensuring that your facility meets every standard and regulation.
Meeting Building Codes and Standards
Proactive maintenance supports compliance by allowing facility managers to identify and address potential issues that can become costly violations. Keeping detailed maintenance records is also vital for organizing and preparing for audits. With a proactive maintenance program and thorough record-keeping, you can confidently protect your facility from regulatory issues.
Safety and Risk Management
Regular inspections and upkeep prevent accidents caused by malfunctioning machinery, protecting both staff and assets. Staying ahead of equipment failures also means fewer emergency repairs and fewer disruptions, creating a more stable and safe working environment. Addressing potential risks early can create a safer environment that complies with occupational health and safety regulations.
Energy Efficiency and Sustainability
Proactive energy efficiency and sustainability maintenance boost operational efficiency and enhance energy performance while reducing environmental impact and waste. Through careful planning, you can adopt environmentally friendly techniques that contribute to cost savings and improved resource efficiency, making your facility more sustainable in the long run.
Optimizing Building Systems Performance
Proactive maintenance can significantly improve the performance of building systems like HVAC, lighting, and other energy-intensive equipment. Regular upkeep ensures these systems operate efficiently, reducing energy consumption and extending their lifespan. By identifying inefficiencies early, you can make adjustments that conserve energy, reduce costs, and minimize the facility’s overall environmental impact.
Sustainable Maintenance Practices
You can minimize your environmental footprint and maintain efficiency by using environmentally friendly products, reducing waste, and implementing recycling programs. Sustainable practices, such as water conservation and energy-efficient repair methods, contribute to long-term cost savings and a more responsible use of resources. This supports both your facility’s and the environment’s sustainability goals.
Measuring and Improving Proactive Maintenance Effectiveness
Tracking the progress and effectiveness of your proactive maintenance practices is vital. Analyzing key metrics allows you to find areas for improvement and reinforce already working measures. By measuring key criteria and periodically adjusting practices, you can foster an environment of continual improvement and drive your organization toward greater excellence.
Key Performance Indicators (KPIs)
KPIs let you evaluate the success of your proactive maintenance strategies by tracking vital metrics such as equipment downtime, maintenance response times, and time to repair. Tracking these metrics over time helps gauge the effectiveness of your efforts, identify underperforming areas, and take corrective action. By reviewing performance metrics regularly, you can adjust your maintenance plans to address new challenges, optimize workflows, and enhance resource allocation, helping to continuously improve maintenance strategies.
Conclusion: The Future of Proactive Maintenance in Facilities Management
Proactive maintenance is more than just a way to keep your equipment running smoothly—it’s a forward-thinking strategy that can transform facility management. By anticipating issues, you can reduce downtime, extend the lifespan of assets, and cut maintenance costs. Emerging technologies such as AI, IoT, and data analytics make proactive solutions more accessible and effective, empowering organizations to optimize their operations.
As maintenance strategies evolve, facility managers who adopt proactive approaches will be better equipped to handle new challenges and keep up with or stay ahead of their competition. Assess your current maintenance practices and consider integrating proactive methods to boost efficiency, reduce costs, and ensure a sustainable future for your facility.