The Ultimate Plumbing Maintenance Guide for Facilities Managers
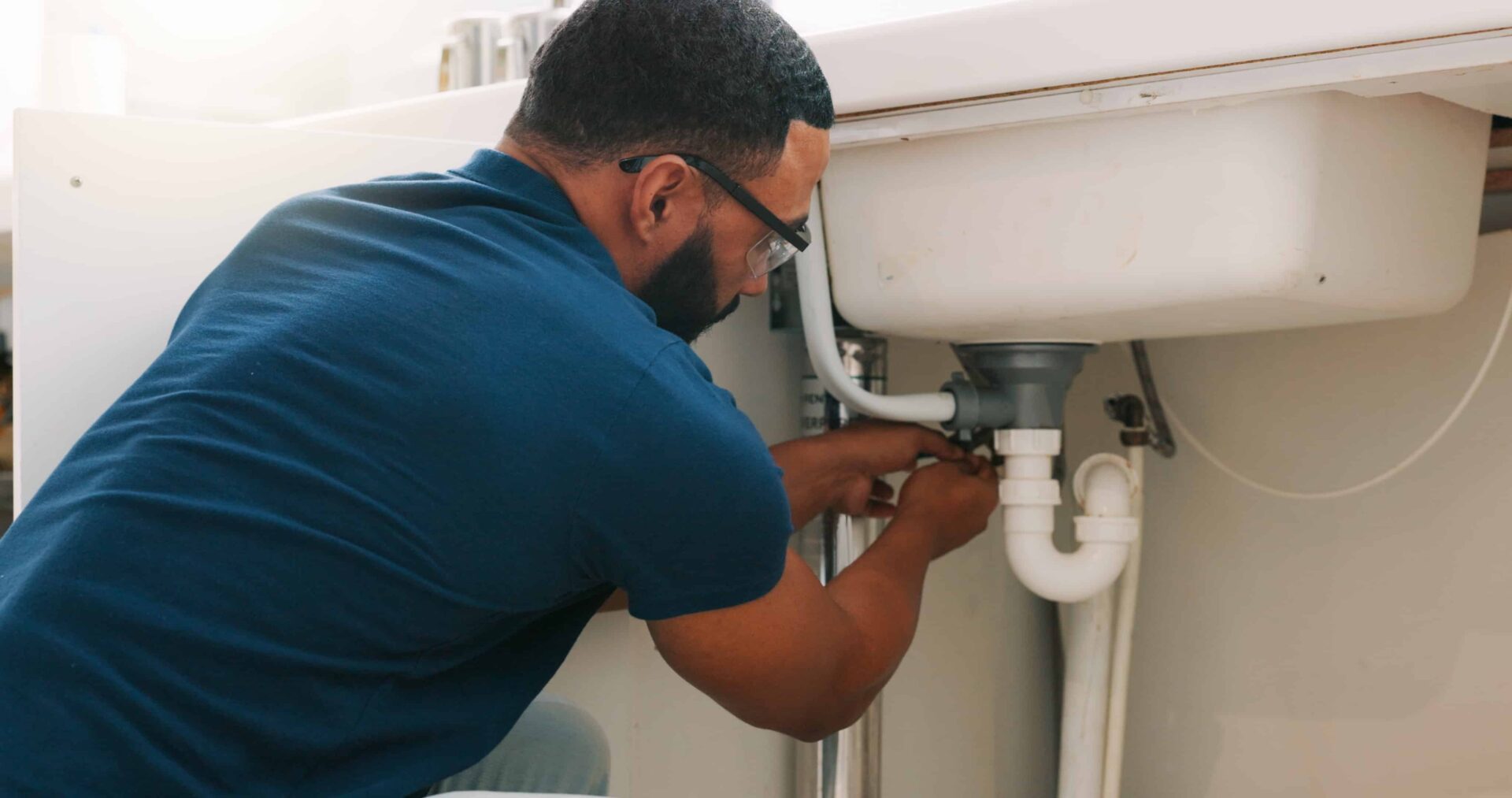
Read our daily, weekly, monthly, and annual plumbing maintenance checklist for optimal performance, efficiency, and facility organization.
Proactive plumbing maintenance in commercial facilities can lower repair costs and prevent water damage. Regular inspections keep plumbing systems working efficiently, so an efficient plumbing system is less at risk of emergency repairs and damage that may have occurred before the issue is caught.
Additionally, regular plumbing maintenance supports a healthy environment by preventing mold growth and ensuring a clean water supply. Depending on your facility, that may be critical. Healthcare and food service facilities are prime examples of facilities where such prevention is crucial. In these cases, more frequent plumbing maintenance may be required.
Plumbing Maintenance Checklist
Daily Tasks
Check your plumbing system daily for leaks, unusual noises, and odors. If these are present, they may indicate plumbing issues. For example, gurgling sounds from drains or toilets suggest a possible venting issue or clogged pipes.
Banging noises may also indicate something referred to as a water hammer. This term refers to a shock wave that travels through pipes when water flow suddenly stops. The shock wave may bang against wall studs or floor joists, damaging drain connections and fittings.
It’s also important to ensure proper drainage in sink drains, toilets, shower drains, and floor drains every day. Slow drains must not be ignored. Although water is running down these drains, it’s important to address the potential blockages before slow drains become clogged drains.
Clogged drains can cause a huge mess in your facility. Water backups can pool on the floor, posing a slipping hazard or risk to any nearby electrical equipment.
Weekly Tasks
Schedule a time every week to test the water pressure and temperature. Ensure that hot water runs hot and cold water runs cold wherever it’s expected. Use a pressure gauge tool to check the water pressure.
Outdoor faucets or hose bibbs are typically where you’ll get the most accurate measurement. Before you test the water pressure, ensure you turn off all appliances that use water in your building.
Normal water pressure should be between 40 and 60 pounds per square inch (psi). If your water pressure is too high, it can cause excess stress on your pipes, which wears them down more quickly. Conversely, if your water pressure is too low, it may indicate a leaking pipe or blockage.
Cleaning faucet aerators and shower heads is another important weekly plumbing maintenance task. Over time, calcium buildup and other minerals from the water can clog the small holes on your aerator or shower head and restrict water flow.
You can dissolve mineral buildup by soaking the aerators and shower heads in simple white vinegar and wiping it away with a soft brush.
Monthly Tasks
Inspect pipes for corrosion and leaks at least monthly. Regular plumbing inspections are vital to keeping your plumbing system working properly. Also, check the water heater temperature and pressure relief valves during this time.
To check a valve, gently lift the lever part way up. You should hear water flow and see some water and vapor exit through the discharge tube. If not, the valve may be faulty. When checking any plumbing valves, make sure you know where the main water shutoff valve is located, just in case of a leak you can’t control.
Test sump pumps if you have them, especially before the rainy season. Proactive sump pump maintenance helps prevent water damage and mold or mildew growth in your sump pit during heavy rainfall.
Annual Tasks
Conduct a comprehensive plumbing inspection at least once a year. Service water heaters, sump pumps, and backflow preventers during these annual inspections. This ensures all plumbing appliances are functioning properly and meet plumbing codes.
Update your plumbing map and maintenance logs after each plumbing inspection. It’s easy to assume that your building’s plumbing system will stay the same, but this isn’t the case. An updated map will show these changes if a new construction project affects your plumbing system.
Maintenance logs help track what was done during the last regular maintenance check. Having these logs helps you uphold your preventative maintenance plan.
The ROI of a Preventative Plumbing Maintenance Schedule
Waiting until a problem occurs can lead to higher costs. Emergencies often happen at inconvenient times, leading to higher labor rates for immediate service. By comparison, regular plumbing inspections, cleaning, and plumbing system maintenance prevent problems before they happen. These costs are predictable and often lower because you avoid emergency rates and major damage.
For example, inspecting pipes can identify blockages or weaknesses before they lead to major pipe bursts. That lets you avoid costly repairs and water damage.
Calculating the ROI involves comparing the costs saved by preventing problems with the costs of the preventive maintenance program.
Sum up the costs of all preventive maintenance activities over a year. Then, estimate the costs of major repairs, replacements, and damage cleanup that would likely occur without regular maintenance.
Subtract the total preventive maintenance costs from the estimated reactive maintenance costs. This is the amount saved by preventing major repairs and damage.
Finally, divide the savings by the preventive maintenance costs and multiply by 100 to get a percentage.
Here is the formula:
ROI (%) = (Estimated Savings/Preventive Maintenance Costs) x 100
Common Commercial Plumbing Issues and Prevention
Pipe Corrosion
Pipe corrosion usually happens due to the water’s chemical composition, the plumbing system’s age, or the water’s oxygen levels. Corrosion can lead to leaks, water damage, and water contamination.
Using materials like copper or plastic for piping can resist corrosion better than others. Treatments such as protective coatings also help extend the pipes’ lifespan. Applying corrosion inhibitors inside pipes during preventative maintenance is helpful. These chemicals form a protective layer on the pipe’s interior to slow down the corrosion process.
Leaks
Leaks usually occur at joints, corroded sections, or due to high water pressure. They can cause significant water waste and damage to a building’s structure.
Acoustic sensors and thermal imaging cameras can detect hidden leaks by identifying sound frequencies or temperature differences caused by escaping water. Use these tools and a visual inspection during routine maintenance.
Clogs and Blockages
Avoid pouring grease, oil, and non-biodegradable materials down drains to prevent clogs. Regularly educate building users on what not to dispose of in toilets and sinks. You can use a store-bought drain opener or baking soda and vinegar mixture to clear smaller clogs. For massive clogs, hydrojetting uses high-pressure water to clear blockages.
Low Water Pressure
Installing pressure-regulating valves can help maintain a consistent water pressure level throughout the plumbing system. These valves prevent issues related to both low and high water pressure. Proper design and installation of pipe layouts are also needed to ensure adequate flow. It’s crucial to size pipes correctly according to the building’s water demand.
Running Toilets and Faucets
Regular maintenance of toilet flappers and fill valves can prevent running toilets, which saves water and helps you save money on utility bills. Check the toilet flapper for signs of wear or damage. A deteriorating flapper is a common cause of running toilets and should be replaced if it doesn’t seal properly.
Examine the fill valve for leaks and proper operation. If the fill valve is malfunctioning, it may need adjustment or replacement to ensure it stops filling at the correct water level.
It is also recommended that you use hands-free sensor faucets in your facility. This type of faucet reduces water waste by ensuring the water runs only when needed. It also minimizes the spread of germs in commercial settings.
Water-Saving Plumbing Upgrades
To save even more water, consider these upgrades to your plumbing systems.
- Low-flow appliances: These are designed to use less water while performing the same tasks. They help save water by reducing the amount of water used in everyday activities.
- Greywater recycling systems: These systems collect water from sink drains, showers, dishwasher discharge, and washing machines for reuse in irrigation and toilet flushing. Therefore, less fresh water is needed.
- Smart leak detectors and water meters: These devices monitor water use in real time and detect leaking pipes or unusual water consumption. They prevent water waste and lead to more informed water use.
- Rainwater harvesting for irrigation: Collecting rainwater from roofs and storing it for watering gardens and landscaping helps lower water bills and reduce reliance on municipal water supplies for irrigation.
Facility Plumbing Mapping
A plumbing map outlines the location of pipes, sewer lines, valves, meters, and other key components of a facility’s or home’s plumbing system. One of the main reasons to create such a map is to ensure quick and easy access to these components during maintenance, repairs, or emergencies.
Labeling and tagging pipes clearly identify what each pipe, valve, and meter is for, which is helpful during troubleshooting processes. For instance, if a specific water line must be shut off quickly to prevent water damage during a leak, accurately labeled valves allow immediate identification and action.
To simplify plumbing mapping, you can use digital mapping tools. Digital maps can be easily updated to reflect any changes or additions.
Once your initial map is complete, verify the information’s accuracy with a professional plumber or your maintenance staff. Make sure everyone on your team knows where the map is kept and how to read it. Quick access to this map can help mitigate damage.
Plumbing Maintenance Documentation
Maintenance documentation is needed for all forms of maintenance. Without it, your maintenance staff has less visibility into what has been done or why. Related maintenance logs, such as plumbing maintenance and sewer line maintenance, may be connected simply because your plumbing system is directly linked to your sewer system.
Keeping up-to-date records of all inspections and tests also demonstrates adherence to codes. If violations are ever found, document any corrective actions taken in response to inspection findings.
Every work order should have a clear, concise description of the issue, including details about the location and the specific plumbing asset affected. These details ensure technicians understand the scope of the task. Include a section for technician feedback in service logs. This information can provide valuable insights for future maintenance work and potential improvements.
CMMS tools make it easier to maintain this log. Such tools allow you to keep a comprehensive history of each asset in one centralized location. You can also use the reporting and analytics features of CMMS software to identify trends, forecast maintenance needs, and optimize resource allocation.
Staff and Occupant Training
Keeping plumbing systems in good shape isn’t just your maintenance staff’s job. Everyone who uses your facility should have some level of education about how they can protect your plumbing.
Provide Water Conservation Tips
Promoting water conservation helps reduce costs, reduce wear on your plumbing, and promote sustainability. Here are some practical tips that can help conserve water:
- Fix leaks in any plumbing fixtures promptly.
- Recommend using a broom instead of water hoses to clean driveways and sidewalks.
- Encourage turning off the tap when it is not in use.
- Encourage only using dishwashers when there is a full load.
Be Clear About What Not to Flush or Pour Into Drains
Inform everyone in your facility about what cannot be flushed or poured down drains. Misuse can affect drain water quality or lead to clogs. Clear signage above sinks and toilets can serve as effective reminders. Obvious alternative garbage disposal units must also be placed nearby.
Make It Simple to Report Plumbing Problems
Teaching occupants to recognize early signs of a plumbing problem can prevent small issues from becoming major disruptions. Encourage everyone to report leaks, odd noises, or slow drainage as soon as they notice them, and make it easy to do so. Setting up a dedicated hotline, email address, or online reporting tool is one of the most straightforward ways to do that.
Plumbing Maintenance Tools and Technology
The right tools can make every plumbing inspection a bit easier. Here are some you can use.
- Video pipe inspection cameras: These cameras let you see inside pipes without cutting into walls.
- Smart pump control system: This system adjusts a pump’s speed based on inputs from a flow sensor to control pressure automatically.
- Automatic leak shutoff valves: These valves detect leaks and shut off the water supply to prevent damage. They check for pressure or water on the floor to determine if there is a leak.
- Water quality testing equipment: This equipment can ensure drinking water is safe and measure the water’s pH level to prevent corrosion or scaling.
Plumbing Problems Troubleshooting Guide
How to Diagnose Low Water Pressure
- Check for closed valves or leaks
- Inspect pipes for clogs or corrosion
- Inspect the pressure regulator
- Seasonal factors may be at play in areas prone to drought or where water usage restrictions are in place
How to Unclog a Drain or Toilet
- Use a plunger
- Try a plumber’s snake
- Consider chemical cleaners
- Regularly flush drains with hot water to prevent buildup
How to Check Water Heater or Pilot Light Issues
- Inspect your water heating system annually as part of routine maintenance
- Look for signs of rust or water pooling around the water heater
- Check the thermocouple, cold water inlet pipe, and hot water exit pipe
- Inspect the pilot orifice to ensure it isn’t clogged
What to Check For if There is a Sewer Odor
- Ensure all drains have water in their traps
- Check the vents for any blockages
- Verify that there isn’t an issue with your main sewer line or your septic system
When to Call a Licensed Plumber
- When issues persist despite troubleshooting
- For installations or repairs that require specialized knowledge
- When fixing the issue without assistance could pose a safety risk
Simplify Plumbing Maintenance With ServiceChannel
If your facility requires more frequent plumbing maintenance, keeping track of everything that needs to be done can be harder. However, the right software can make it simple to track all plumbing work.
ServiceChannel’s preventive maintenance software lets you track every past and upcoming plumbing inspection. Our tool also makes it clear what each inspection needs to cover. This level of transparency gives your team direction and helps keep them accountable.