The Ultimate Guide to Periodic Maintenance for Facilities Managers
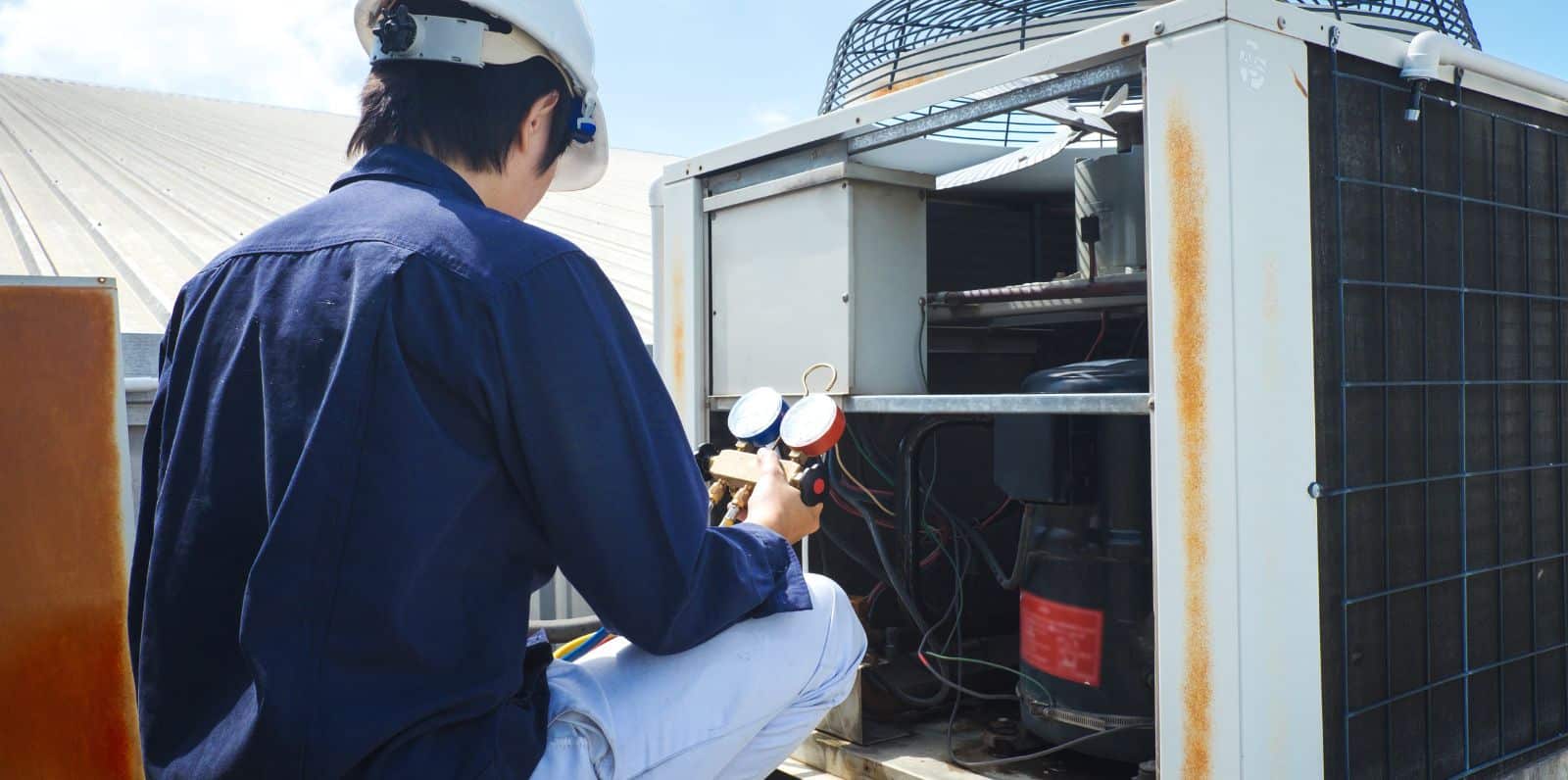
Elevate your facility’s efficiency with a comprehensive periodic maintenance program. Explore the tools, technologies, and cost-saving insights.
Keeping a facility running efficiently requires careful attention, especially when managing multiple assets that must perform at their best. Periodic maintenance plays a vital role in ensuring equipment reliability and preventing unexpected failures. For facilities managers, a well-structured maintenance program can be the key to avoiding costly disruptions and maintaining seamless operations. This guide explores the essentials of periodic maintenance, including its benefits, practical implementation, and strategies for building a cost-effective program that maximizes your facility’s performance and optimizes your maintenance budget.
What is Periodic Maintenance?
An essential tool for facilities and asset management, periodic maintenance is a proactive approach focused on performing upkeep at regular, predetermined intervals to keep equipment in good working condition. It’s similar to preventive maintenance in that periodic maintenance seeks to avoid issues before they can become problems. However, whereas preventive maintenance is often condition- or usage-based, periodic maintenance is scheduled regardless of asset conditions. Unlike reactive maintenance, which addresses problems after they occur, periodic maintenance aims to prevent unexpected failures by routinely checking and servicing assets.
Periodic maintenance is a cornerstone of effective facility management for facilities maintenance managers. It ensures equipment reliability, minimizes downtime, and controls repair costs. Maintenance managers prefer to adopt this approach for mission-critical assets in environments where uptime and operational continuity are a top priority.
The Benefits of Implementing Periodic Maintenance
Periodic maintenance offers significant advantages to facilities management, helping to extend equipment lifespan and cut down on unexpected asset failures. With this proactive approach, facilities managers can achieve better operational efficiency, safety, and cost savings. The benefits of a periodic maintenance plan include:
- Improved Asset Reliability: Consistently scheduled maintenance keeps assets operating optimally, reducing unexpected breakdowns and extending their useful life.
- Enhanced Safety and Compliance: Routine maintenance checks help minimize hazards by ensuring that equipment meets industry safety standards, reducing risks to operators and facilities.
- Optimized Resource Allocation: Facilities managers can distribute resources more deliberately by planning maintenance ahead of time, reducing the impact on daily operations and keeping costs manageable.
Developing a Periodic Maintenance Program
Creating a successful periodic maintenance program involves clear steps to ensure all assets are properly maintained. Each part of the process—from identifying which assets are critical to scheduling regular check-ups—plays a key role in keeping equipment reliable and operating effectively. These steps can help you launch an effective periodic maintenance strategy.
Identifying Critical Assets
When creating your periodic maintenance strategy, begin by identifying the assets most essential to your facility’s operations. Critical assets are those that, if they fail, would most likely cause significant unplanned downtime, safety hazards, or costly repairs. By prioritizing your most crucial assets, you can direct your resources more effectively and ensure that vital equipment will receive the attention needed to prevent disruptions. This foundational step helps focus maintenance efforts on the assets that impact overall facility performance and your organization’s budget.
Establishing Maintenance Schedules
Defining scheduled maintenance intervals is vital for any successful periodic maintenance program. Schedules should be based on each asset’s operational demands, manufacturer recommendations, and historical data on performance and repairs. High-use or high-impact equipment might require more frequent attention, while less critical assets could get by on a more flexible schedule. By tailoring maintenance intervals to each asset’s needs, facilities managers can ensure equipment reliability while managing resources effectively. Establishing regular maintenance times keeps maintenance predictable, reducing unplanned downtime and supporting uninterrupted operations.
Creating Detailed Checklists
Checklists are essential for guiding maintenance technicians through each task, making sure every asset receives thorough and consistent service. For periodic maintenance, these checklists should cover all necessary inspections, adjustments, and parts replacements according to each item’s unique requirements. Clearly outlining each procedure step by step reduces the chances that a technician will miss something and helps maintain a high standard of care across all maintenance activities.
Assigning Responsibilities
Clear role assignments ensure that everyone involved in the periodic maintenance program knows their tasks and what they’re responsible for. Whether scheduling, performing maintenance, or logging data, each team member should have a well-defined role to streamline the process. Assigning responsibilities reduces overlap and confusion while building a sense of ownership by encouraging a proactive culture among team members. This structure helps keep the program organized and ensures everyone completes their tasks on time and according to standards.
Tools and Technologies for Effective Periodic Maintenance
Advancements in technology have transformed maintenance practices, allowing facilities managers to approach periodic maintenance with powerful, data-driven tools. From software-based solutions to hardware-based instrumentation, these tools have tremendously impacted maintenance strategies across all industries, streamlining maintenance processes, reducing downtime, and helping keep equipment in top condition.
Computerized Maintenance Management Systems (CMMS)
A computerized maintenance management system (CMMS) platform is an essential software solution for managing and tracking maintenance tasks, schedules, and equipment performance. A CMMS centralizes all maintenance data, making it easier for facility managers to monitor asset health, log maintenance history, and schedule periodic maintenance at optimal intervals. These systems give managers a holistic view of all maintenance activities, enabling more informed decision-making, better task management, and more efficient resource allocation.
Internet of Things (IoT) Sensors
IoT sensors play a critical role in modern maintenance by providing real-time data on asset performance, conditions, and usage. These sensors can monitor metrics like temperature, vibration, and energy consumption, detecting subtle signs of wear or potential failures. Connected to a CMMS, IoT sensors can trigger alerts when readings meet or exceed specified thresholds, giving maintenance teams ample warning to address issues before they become full-blown problems. This proactive approach helps facilities managers minimize unplanned downtime, reduce repair costs, and extend equipment lifespan.
Artificial Intelligence (AI) and Machine Learning Applications
AI and machine learning (ML) are revolutionizing maintenance by enabling predictive analysis and intelligent automation. These technologies can analyze vast amounts of data from maintenance logs, IoT sensors, and equipment history to predict when assets might need attention. This proactive insight lets facilities managers perform predictive maintenance before potential issues arise and inform periodic maintenance scheduling. This combination can greatly reduce unplanned downtime and maximize asset reliability, making maintenance programs more efficient and cost-effective.
Periodic Maintenance vs. Other Maintenance Strategies
Understanding how periodic maintenance compares to other strategies is key to creating an effective maintenance plan. While each method has strengths, periodic maintenance ensures consistent performance and prevents unexpected issues. No single strategy fits every situation; the goal is to apply the right approach for each asset. Here, we’ll compare periodic maintenance with preventive, predictive, and reactive strategies to see how they align with facility needs.
Periodic Maintenance vs. Preventive Maintenance
Periodic maintenance uses fixed schedules, performing maintenance at predetermined intervals despite asset conditions. Preventive maintenance is condition-based or usage-driven, relying on data like wear and tear or runtime hours to determine when to perform upkeep. The best approach depends on the specific asset. Periodic maintenance is ideal for assets with predictable needs, while preventive maintenance suits those that benefit from condition-based care.
Periodic Maintenance vs. Predictive Maintenance
While periodic and predictive maintenance seem similar, periodic maintenance follows a schedule and predictive maintenance uses advanced analytics, sensor data, and machine learning to anticipate maintenance needs. While predictive maintenance minimizes unnecessary servicing, periodic maintenance offers simplicity and predictability. For facilities without access to predictive technologies, periodic maintenance remains an effective, proactive approach to ensuring equipment reliability.
Periodic Maintenance vs. Reactive Maintenance
Periodic maintenance focuses on scheduled upkeep, while reactive maintenance is performed after a failure or breakdown occurs. This can lead to higher repair costs and unplanned downtime. Reactive maintenance works well for low-value and low-impact assets. Periodic maintenance is an effective strategy for ensuring that high-value, high-impact, and safety-critical assets are regularly inspected and maintained to avoid more severe problems.
Best Practices for Periodic Maintenance in Different Facility Types
Different facility types come with their own maintenance challenges and requirements. Periodic maintenance strategies should be tailored to the needs of your specific environment to maximize asset reliability, ensure safety, and enhance operational efficiency. Here are the best practices for the most common facility types:
- Office Buildings: Prioritize HVAC systems, elevators, and fire safety equipment in office environments. Regularly check ventilation systems for air quality and energy efficiency. Maintain lighting and plumbing systems to ensure a comfortable, functional workspace for occupants.
- Healthcare Facilities: Maintain critical medical equipment, backup power systems, and climate control to support patient care. Regularly sanitize and service air filtration systems to meet strict cleanliness standards. Schedule frequent checks for emergency systems like generators and alarms.
- Educational Institutions: Ensure that HVAC systems, fire alarms, and plumbing are maintained to provide a safe learning environment. Periodically inspect playground equipment, laboratory facilities, and IT infrastructure. Coordinate maintenance schedules to minimize disruptions during school hours.
- Industrial Plants: Regularly monitor heavy machinery, conveyor systems, and safety equipment for wear and tear and schedule maintenance for high-use equipment to prevent production delays. Inspect ventilation and exhaust systems to ensure compliance with safety and environmental regulations.
Maximizing Facility Performance Through Periodic Maintenance
Periodic maintenance is an essential strategy for facilities managers looking to improve asset reliability, minimize downtime, and enhance operational efficiency. By implementing a well-structured periodic maintenance program tailored to your facility’s unique needs, you can rest assured you’ll see more consistent performance, extended equipment lifespan, and reduced costly disruptions.Ready to optimize your facility’s performance with periodic maintenance? Contact us today for a personalized consultation and discover how the ServiceChannel facilities management platform can help you implement an effective periodic maintenance program tailored to your facility’s needs.