What Facilities Managers Need to Know: Optimizing Supply Management
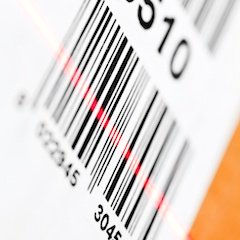
This is the next in a series of posts highlighting the 13 trends, technologies and best practices essential for facilities managers, from the ebook What You Need to Know to Succeed in Facilities Management in 2020.
Not only are parts and supplies a requisite component of any FM program but their availability and use are important when optimizing such a program. To start being smart about managing your parts and supplies, it’s important to integrate all planned maintenance services and warranty work into your FM platform. Such services are key drivers of when and where parts and supplies are needed.
Boosting FM Performance Through Asset Efficiency
Tracking parts-to-equipment usage can give insight into asset efficiency and help guide timing for planned maintenance services. Major repairs and downtime can also be avoided by automatically creating preventive maintenance work orders based on supplier recommendations.
Optimizing the supply chain across a multi-location chain can often prove challenging. With thousands of parts across hundreds of locations, local staff can end up buying parts that can jeopardize warranties at costs well outside of corporate negotiated rates.
Smart Purchasing Tied to Facilities Software
With approved purchasing options and customized online product catalogs easily available across the company, facilities managers can ensure proper parts are used and costs controlled. Such e-procurement systems will connect with both purchasing systems to track payments properly and with facilities management systems to sync purchases with asset tracking and work order management.
Barcode scanning will further integrate assets with their required parts and supplies. Tracking this way will enable deeper visibility across both the supply chain and assets’ lifecycles. Planned maintenance services will have more accurate scheduling based on parts usage and ensure warranties remain in compliance, eliminating risk factors.