7 Essential Maintenance Metrics Every Facility Manager Should Track
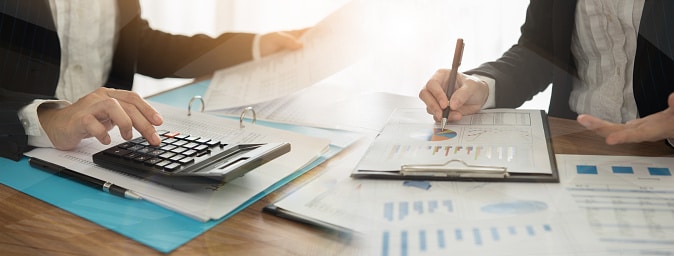
Discover the 7 essential maintenance metrics every facility manager should track to improve reliability, reduce downtime, and optimize costs.
Maintenance metrics are an essential part of facility maintenance in any enterprise. These maintenance key performance indicators (KPIs) track the reliability and efficiency of personnel, equipment, and current maintenance practices. Metrics effectively convert real-world conditions into data that the maintenance department can examine to inform numerous decisions, from replacing equipment to reevaluating budgets.
Organizations use common maintenance metrics to evaluate their success, and implementing metric tracking can help meet your facility maintenance and operations objectives. Effective computerized maintenance management software (CMMS) can dramatically save time analyzing key performance indicators and increase tracking accuracy.
Maintenance Metrics You Should Be Tracking
Mean Time Between Failure (MTBF)
Mean time between failures (MTBF) calculates the average time an asset operates before breaking down. This maintenance KPI can improve asset reliability by helping to identify underlying issues and informing schedules to conduct preventive maintenance before problems occur.
To calculate the MTBF value, divide the total operation time by the number of failures within a specified period.
For example, a pharmaceutical manufacturer wants to determine the efficiency of a bottle-capping machine. During a 3-day packaging run, the line ran for 48 operating hours. In that time, the capper broke down 9 times. To calculate the MTBF, the lead operator would write the following:
- [MTBF = 48 / 9; MTBF = 5.33]
The higher this maintenance KPI value, the more efficiently the machine operates.
Mean Time to Repair (MTTR)
The mean time to repair (MTTR) maintenance performance indicator indicates the average time it takes to repair an asset after it malfunctions. Monitoring MTTR helps companies reduce downtime by spotlighting inefficiencies in repair practices that you can improve upon.
To determine the mean time to repair value, record each instance of equipment failure and track the time it takes to restore functionality. Add the repair time for all instances and divide the total repair time value by the number of repairs to obtain the MTTR value.
For example, a utility company wants to determine the efficiency of its transformer repair procedures. During that time, maintenance teams performed a total of 3 transformer repairs. The repairs took 1.5 hours, 3 hours, and 2.5 hours, respectively, for a total repair time of 7 hours. The utility company runs the following calculation.
- [MTTR = 7 / 3; MTTR = 2.33]
Lower time-to-repair values indicate more reliable equipment and more efficient repair processes.
Preventive Maintenance Compliance (PMC)
Preventive maintenance compliance (PMC) compares the percentage of completed maintenance work orders to total scheduled work orders. This maintenance KPI is a reliable way to evaluate the effectiveness of preventive maintenance operations and explore ways to optimize practices.
To calculate the PMC value, divide the total number of maintenance activities completed on schedule by the total number of scheduled maintenance tasks and multiply the result by 100.
For instance, a university maintains HVAC units and internal systems across its buildings. Each year, the institution schedules 500 maintenance jobs. Of those 500, 358 scheduled tasks were completed on time, with 142 tasks left incomplete or finished late. They calculated the PMC using the following formula:
- [PMC = 358 / 500 x 100; PMC = 71.6]
A higher PMC value reflects more effective maintenance processes and more reliable equipment.
Overall Equipment Effectiveness (OEE)
The overall equipment effectiveness (OEE) metric reflects the percentage of scheduled productive operations. This performance indicator helps identify enhancement opportunities for maintenance and manufacturing processes. By pinpointing disruptions such as stops and slow cycles, teams can investigate the root causes of these issues and improve practices to increase asset uptime.
You obtain the OEE rating by multiplying availability, quality, and performance. ServiceChannel offers deeper insights into determining the availability, performance, and quality scores to calculate the OEE rating.
For example, a snack company wants to assess the OEE of its snack cake production line. The team has calculated their availability at 73% (0.73), performance at 85% (0.85), and quality at 75% (0.75). The formula would read as follows:
- [OEE = 0.73 x 0.85 x 0.75; OEE = 0.465]
This gives the production line a 46.5% OEE rating. A higher rating indicates greater productivity.
Planned Maintenance Percentage (PMP)
Planned maintenance percentage (PMP) is a key maintenance metric that compares the number of hours spent on maintenance jobs against the number of scheduled maintenance hours. Tracking PMP can improve a preventive maintenance strategy and reduce preventive and reactive maintenance work by helping identify failure points.
The PMP value is calculated by dividing the planned maintenance hours by the hours spent conducting maintenance multiplied by 100.
If a toy manufacturer plans for 80 hours of maintenance per month, but the maintenance team spends 130 hours in a month performing maintenance duties, the calculation would look like this:
- [PMP = 80 / 130 x 100; PMP = 61.5]
The toy manufacturer achieved a modest 61.5% PMP rating. A low PMP indicates issues with equipment or maintenance processes that need to be addressed.
Maintenance Backlog
The maintenance backlog reflects the time value of incomplete maintenance jobs, whether in-process or pending tasks. Maintenance backlogs indicate a variety of tasks, including inspections, repairs, and overdue preventive maintenance tasks. Tracking maintenance performance metrics such as the backlog enables teams to improve their maintenance strategies by examining the conditions that cause them to fall short of their maintenance goals.
Calculating the backlog involves listing all overdue maintenance jobs and adding up the total planned time to complete them.
For example, a power plant assesses the backlog from the previous quarter. The maintenance manager sees that 4 maintenance work orders remain outstanding, scheduled for 2, 3, 3, and 5 hours, respectively, for a total planned time of 13 hours. As an equation, the formula would look like this:
- [MBL = 2 + 3 + 3 + 5; MBL = 13]
A smaller backlog generally indicates higher maintenance team efficiency. Consistently reaching a backlog of 0 might indicate the crew needs more to keep them busy throughout the quarter.
Maintenance Cost as a Percentage of RAV
Maintenance cost as a percentage of replacement asset value is more of a budgeting measurement than a maintenance KPI. Companies use this metric to help determine the cost-effectiveness of maintaining a specific asset. If scheduled and unplanned maintenance costs exceed a certain threshold, management might consider replacing the asset to reduce expenses in the long term.
To calculate this metric, determine the annual maintenance cost in dollars, divide it by the cost to replace the asset, and multiply the result by 100.
For example, a fast-food franchise is considering acquiring a new ice cream maker. They calculate the maintenance cost as a percentage of RAV to determine if it will be an informed decision. The ice cream machine would cost $20,000 to replace. When adding up the parts and wages in person-hours to maintain their current one, the company is spending $8,000 per year on maintenance costs. The manager performs the following calculation:
- [MCRAV = 8,000 / 20,000 x 100; MCRAV = 40]
A cost-to-RAV of 40% is higher than the company would prefer. Even though a new ice cream machine would still require periodic upkeep, management determines that they would ultimately come out ahead if they bought one.
Conclusion
Your organization can benefit from the valuable data that these maintenance metrics provide. A CMMS platform like ServiceChannel is a powerful tool to track maintenance KPIs and provide data analysis, empowering your company to make informed decisions at every stage of its maintenance strategy. Explore the ServiceChannel solution today and discover a more efficient and effective way to implement facility maintenance.