8 “Must Have” Work Order Management Software Features
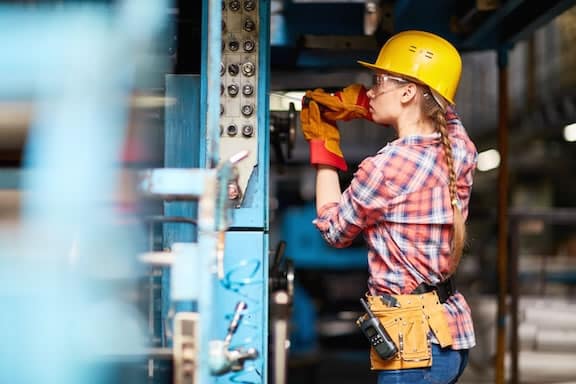
What is Work Order Management Software?
Work order management software streamlines and optimizes the entire work order lifecycle. It’s a centralized platform where work requests are initiated, tracked, assigned, executed, and closed out – all in a paperless environment. This software empowers facility managers and maintenance teams to ditch manual processes, spreadsheets, and sticky notes. Instead, it provides a structured, efficient, and transparent way to handle everything from routine maintenance tasks to emergency repairs.Essential Work Order Software Features
While work order management software offers a wide range of features, not all are created equal. Choosing the right solution for your facility requires an understanding of the essential features that truly make a difference. These features not only streamline your workflow but empower your team to work smarter. Work order management software allows FMs to plan maintenance and be proactive across locations, increase efficiency, and reduce spend. This kind of software can be fairly broad, so to weed through the numerous options out there for platform providers, ensure you focus on features that optimize work order processes. In this post, we’ll take a look at five features that FMs must have in order to improve their work order management.1. Contractor Selection Tools
Contractors that are experienced, in compliance, and professional are necessary for timely and high-quality service completion. Work order management software can include an easily searchable contractor directory that provides contractor names, specialties, compliance statuses, rates, certifications, and insurance (types and amounts) to help you find the best possible service providers in the shortest amount of time. The ability to find the right person for the right job not only increases efficiency, but also helps to establish strong relationships with contractors.
2. Automated Scheduling Capabilities
Work order management software needs to include automated scheduling to ensure that equipment is kept in operational order, that you are not wasting time duplicating service requests, and that you can successfully implement preventive maintenance programs. These programs reduce the cost of lost productivity, minimize the frequency of expensive repairs, keep assets in optimal working condition, and support brand uptime.
This software should also allow you to authorize not-to-exceed (NTE) levels to keep spend in check and set pricing controls for contractors.
3. Ability to Monitor Work
Monitoring contractor performance is an essential feature in that it ensures repair and maintenance is being performed properly, efficiently, and cost-effectively. The right software allows FMs to view contractor performance across key metrics during all phases of the life cycle, though objective, quantitative-based contractor scorecards or report cards. FM software can also monitor contractor on-site arrival and departure via mobile GPS check-in and check-out apps, capture photographs and videos of worked-on assets, and provide alerts if contractors are lagging.
Ideally, work order management software should also integrate with contractor software so that service providers can generate service requests while onsite for pre-approved types of work. This takes the role of scheduling and approving minor repair and maintenance off of the FMs hands.
4. Payment Processing
Software should track invoices throughout the entire work order life cycle— from order creation to invoice submission, approval, and payment. With visibility into every step of the invoice process, FMs can monitor spend and efficiency.
Additionally, this software should integrate with your established financial technology so that the accounts payable department can approve and pay invoices virtually. This saves on administrative and processing costs, enables quick contractor payments, reduces human error, and keeps the facilities management and accounting departments in sync with one another.
5. Analytics & Business Intelligence
Analytics are another important as they deliver impactful predictive views based on past financial and operational data. Look for software that presents data in easy-to-use dashboards that can be specified by trade, category, location, and contractor.
With facilities-focused analytics and business intelligence, you can find answers to business-critical questions quickly and make data-backed decisions (e.g. asset repair/replace) about how to save money and improve efficiency.
6. User Friendly Interface
In the fast-paced world of facility management, time is of the essence. A user-friendly interface in your work order management software is non-negotiable. It should be intuitive, easy to navigate, and require minimal training for your team. Look for features like drag-and-drop functionality, customizable dashboards, and clear visual cues that guide users through the work order process.
Remember, the easier it is for your team to use the software, the faster they can respond to issues and keep your facility running smoothly.
7. Seamless Integrations
Your work order management software shouldn’t exist in a silo. It should seamlessly integrate with other systems you use, such as your asset management platform, accounting software, or building automation system. This integration allows for a smooth flow of data between systems, eliminating the need for manual data entry and reducing the risk of errors. Imagine having your work orders automatically trigger purchase orders for required parts or updating your asset records with maintenance history – all without lifting a finger.
8. Inventory & Tracking Controls
Keeping tabs on your inventory is crucial for efficient work order management. Imagine running out of a critical part in the middle of a repair, causing unnecessary delays and frustration. Work order management software with robust inventory tracking and control features helps you avoid such scenarios. It allows you to track inventory levels, set reorder points, and generate purchase orders automatically when stock runs low. This ensures that you always have the right parts on hand when you need them, keeping your maintenance operations running smoothly.