What Does Stockout Mean?
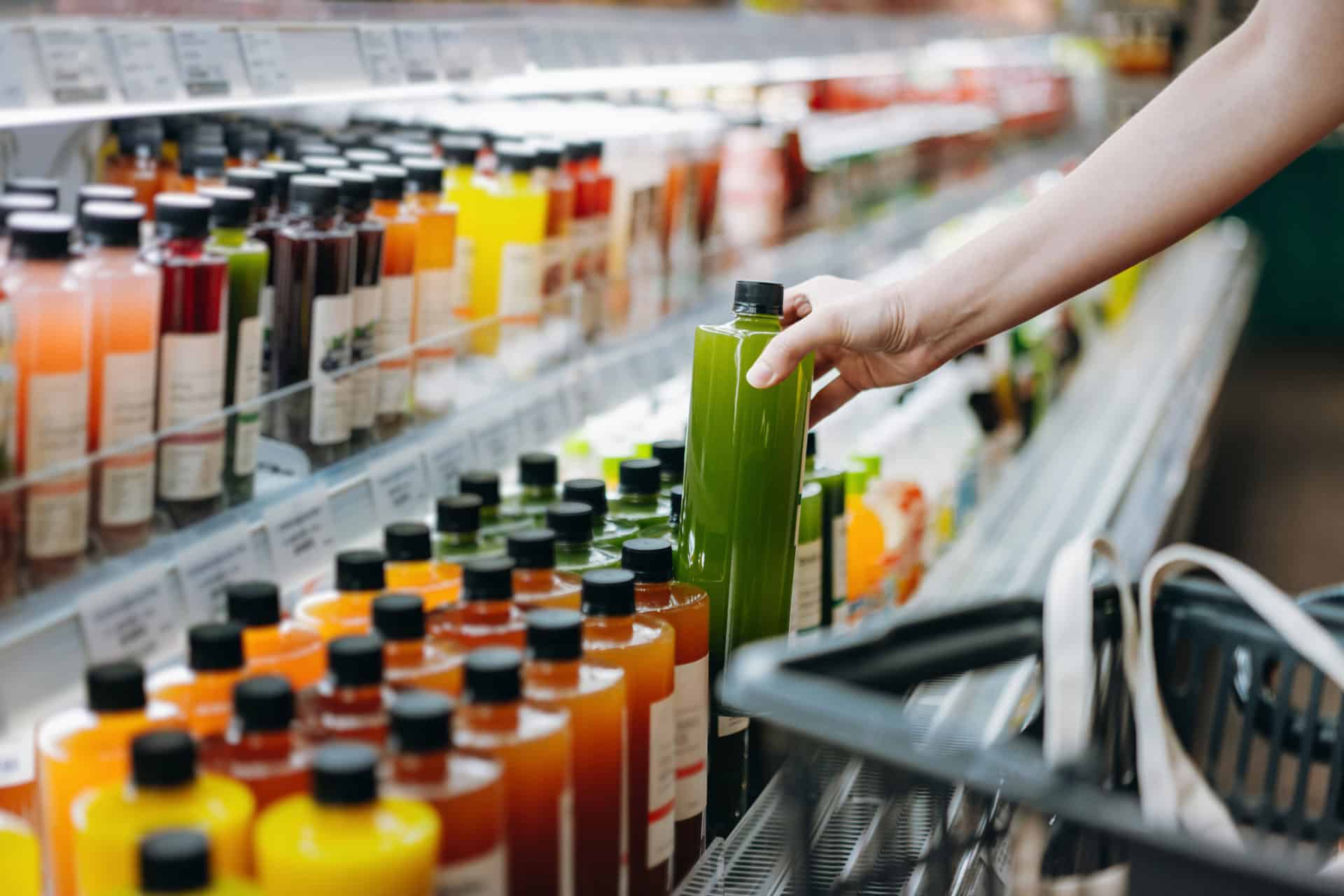
Find out what the exact definition of a stockout is, why it’s important for you to avoid them, and how you can prevent stockout situations.
A stockout occurs when a business runs out of inventory for a particular product. Stockouts can be caused by inaccurate demand forecasting, supply chain disruptions, or poor inventory management. However, no matter the cause, if frequent stockouts happen at your facility, you may face lost sales, poor customer satisfaction, and lost customer loyalty.
Effective inventory management is critical to preventing stockouts and maintaining a smooth supply chain. Inventory management software may help you consistently meet customer demand, but there are other possible causes of stockouts that may not be easy to track using your available inventory management software.
So, understanding what causes stockouts, how stockouts impact your business, and what you should do to avoid a stockout situation is just as important as installing software to help you prevent the worst case scenario.
The Importance of Preventing Stockouts in Business
Preventing stockouts is crucial to maintaining a competitive edge in the market. Stockouts can lead to lost sales and revenue, reduced customer satisfaction, and wasted resources. Stockouts may also disrupt operations as employees may need to invest time into responding to negative reviews or making adjustments to inventory systems.
How to Calculate Your Stockout Rate
A stockout rate is the percentage of customer orders that could not be fulfilled due to a lack of inventory. Your goal should always be to keep your stockout rate to as close to 0% as possible. To calculate this rate, divide the number of orders that went unfilled because you were out of stock by the total number or orders. Then, multiply the result by 100 to express it as a percentage.
Here is the formula:
Stockout Rate = Total Unfulfilled Orders/Total Orders × 100
For example, if a business had 100 orders and couldn’t fulfill 10 due to stockouts, their stockout rate would be 10% because 10/100 × 100 = 10%.
What is Safety Stock?
Safety stock is inventory that is held in reserve to help you avoid stockouts. Safety stock can also be used to mitigate the impact of stockouts by providing a buffer against unexpected demand.
How Much Safety Stock Should You Have?
How much safety stock you need depends on demand variability, lead time variability, desired service level, and forecast accuracy. If customer demand or lead times often vary based on historical sales data, then you need a higher level of safety stock for that product. Also, if customer demand forecasting has been off in the past, it’s best to default to higher safety stock levels.
You can also calculate safety stock to estimate how much you may need. Here is the general formula.
Safety Stock = Z × σₑ × L
In this formula, Z is the Z-score based on the desired service level, σₑ is the standard deviation of demand, and L is the lead time.
Causes of Stockouts
Inaccurate Demand Forecasts
Inaccurate forecasting can lead to costly stockouts, whether it was too high or too low. Forecasts that exceed actual demands may lead to too much inventory, which limits the working capital you have available for other products. On the other hand, underestimations leave shelves empty.
Discrepancies in Inventory Data
Inventory discrepancies occur when actual stock levels differ from recorded data. These discrepancies in inventory accuracy may be the result of miscounts, shrinkage, or technical errors. If the data shows that items are in stock when they aren’t actually available, your employees may delay new fulfillment orders and leave that product out of stock for longer.
Unexpected Spikes in Demand
Sudden surges in demand may occur due to new customer trends or unprecedented events. These situations can quickly deplete your inventory if you weren’t prepared for this shift in buying habits. Try your best to predict when these shifts may occur. Some spikes are easy to predict, such as holiday seasons, while others are nearly impossible to predict. The latter is part of why safety stock is so important to have.
Supply Chain Disruptions
Sometimes, the causes of stockouts are beyond a retailer’s control. If your supply chain partners face natural disasters, geopolitical events, or logistical issues, it may delay product delivery. Delayed supplier deliveries mean that you may run out of stock before you can replenish your inventory.
Poor Cash Flow Management
Ineffective cash flow management limits the funds you have available to purchase inventory. Simply put, if you don’t have enough cash on hand to buy stock, you’ll run out of stock sooner. Follow cash flow management best practices to reduce this risk.
Inventory Management Strategies That Prevent Stockouts
Regular Stock Counts
Regular stock counts help identify discrepancies between actual inventory levels and inventory data records. Being proactive about this practice gives your team time to correct any discrepancies (if found) before they impact the customer experience.
Dynamic Inventory Management
Dynamic inventory management means using real-time data to track and adjust stock levels according to fluctuating customer habits. This practice is an effective way to keep your business up-to-date with changing consumer trends so you can more easily meet demand. The best way to gain this level of real-time visibility is to implement inventory management software that integrates with your sales and supply chain systems.
Demand Segmentation
Demand segmentation is the process of categorizing products based on demand characteristics. Examples of demand characteristics include purchasing patterns, seasonality, or typical customer profiles. Segmenting products in this way allows for precise demand forecasting. Instead of applying the same tactics to all products, you can apply different strategies to different segments as needed.
Supplier Collaboration
Frequent communication with suppliers helps your business anticipate disruptions and adjust inventory orders accordingly. As a result, you can avoid stockouts by prioritizing product orders of items that your supplier may run out of or lose access to in the near future. You may also gain more time to seek alternative suppliers for certain products as needed.