Why Every Facility Needs a Comprehensive Safety Audit Checklist
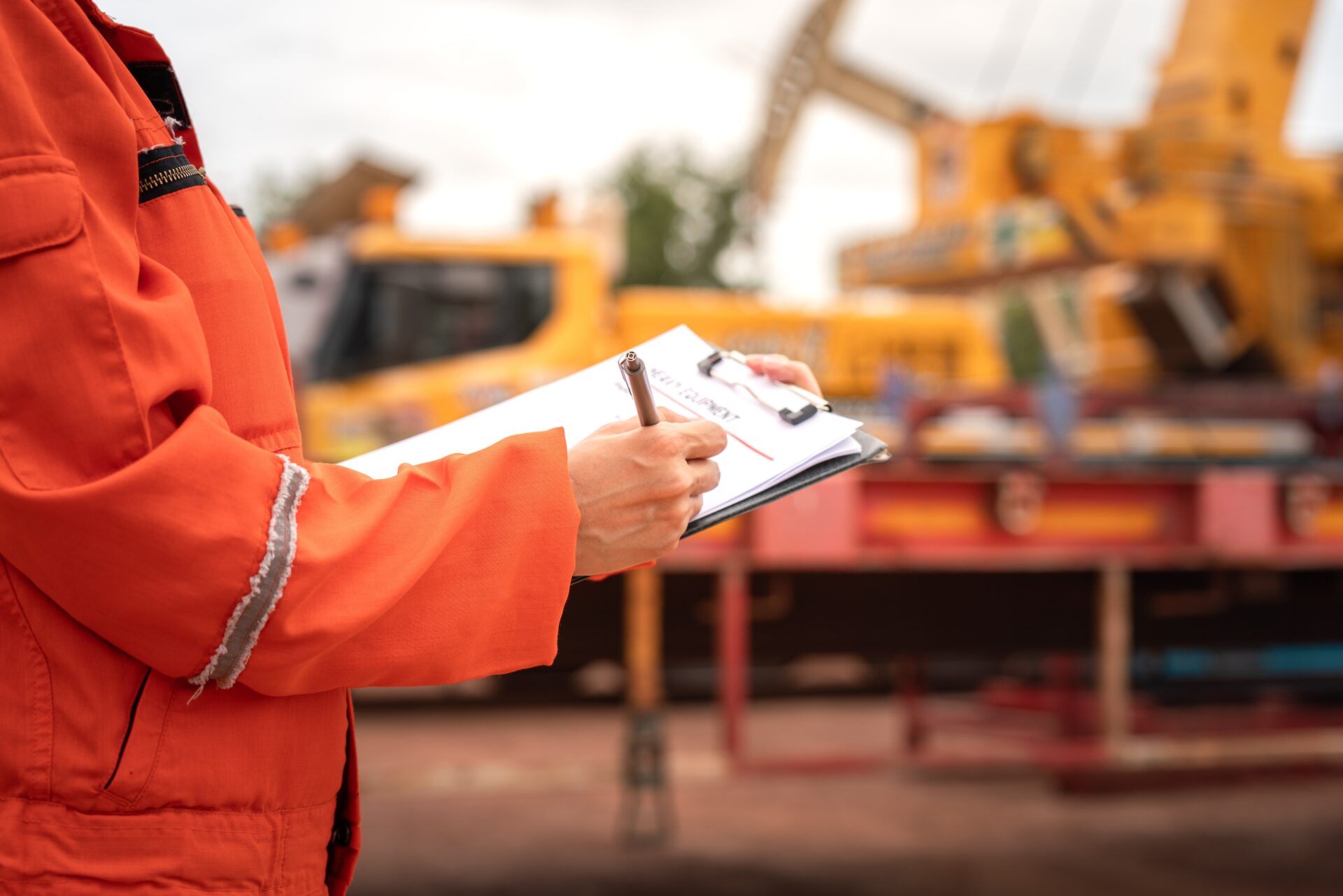
Facility managers rely on a safety audit checklist for regular audits, ensuring proactive hazard identification and incident prevention. Download today.
Most sectors have industry safety standards that they are legally obligated to follow. While the required safety procedures may vary, the need to consistently meet regulations stays the same. For this reason, every facility can benefit from a thorough safety audit checklist that keeps the team on track.
Legal regulations will also vary depending on your facility’s region. However, regular safety audits are important for more than just legal reasons. Regular audits will help you uphold your facility’s safety policies and keep your staff safe at work.
The Importance of Regular Safety Audits
The biggest reason why safety audits matter is that they help your facility proactively identify potential hazards while ensuring compliance with OSHA standards. By reducing safety risks, workplace accidents also become less likely. As a result, you’ll keep your employees safe and avoid potential compensation costs.
Regular health and safety audits also help improve safety management systems and support a safety-conscious culture. A safety inspection may reveal previously unknown workplace safety hazards and areas where you need employees to be trained more.
Download the PDF
Key Elements of Effective Safety Audit Checklists
Although we are providing a general safety audit template available for download in this article, you need to realize that you must customize your safety audit checklist to fit your specific industry and region’s regulations.
For example, healthcare facilities have specific protocols for handling and disposing of medical waste that differ significantly from waste management practices in other industries.
However, the safety management system in most industries will include the following safety procedures.
Safety Equipment Every Industry Needs on Their Safety Audit Checklist
Personal Protective Equipment (PPE)
Personal protective equipment (PPE) ensures workers have the necessary protection against various hazards. Alternatively, it may protect clientele from pathogens that could spread to them from your staff. If your facility requires PPE use, ensure none of it is damaged and that the correct sizes are available for all workers.
Tools and Machinery
Inspecting tools and machinery is crucial for preventing safety issues. Facilities must ensure all equipment is in good condition and that employees know how to use it safely. Look out for signs of wear, improper setup, or lack of maintenance.
Electrical
Facilities must ensure all wiring and electrical equipment are up to code and in safe working condition to prevent shocks and fires. Check for exposed wires, faulty equipment, and overloaded circuits. It’s also important to perform preventive electrical equipment maintenance to reduce potential risks.
Fire
Following the National Fire Protection Association (NFPA)‘s standards is essential for safety in case of a fire emergency. Facilities must have working fire extinguishers, alarms, and sprinkler systems that meet NFPA guidelines. You also need to regularly check these systems for functionality and compliance with the latest NFPA standards.
Heavy Loading
Heavy loading areas require special attention to prevent collapses and injuries. Facilities must ensure all shelving and storage units are stable and not overloaded. To reduce the risk of shelving collapses, check for proper labeling and secure storage methods.
Hazardous Substance Storage
Proper chemical storage of hazardous substances prevents accidents and health issues. Facilities must have suitable containment systems and labels for all hazardous materials. Watch for leaks and improper labeling, and limit access to areas where hazardous materials are stored.
Working From Height
Working from high places increases the risk of serious injuries. Ensure all scaffolding and ladders are stable and in good condition. Check for secure guardrails, proper fall protection gear, proper functioning elevating devices, and safe access points to uphold a safe work environment.
Best Practices for the Safety Auditing Process
Involve Cross-Functional Team and Get Employee Input
To make the safety audit process effective, involve team members from different departments. The reason why that helps is because varied perspectives and expertise make it easier to identify potential health and safety risks.
One department may not have the same insights into the work process as another department. Getting cross-functional input helps you cover all work processes.
Getting input from your front-line staff will also help you identify opportunities for continuous improvement. Staff who work on your job site every day will have practical insights to improve workplace health and safety that may go beyond compliance issues and safety audit templates.
Conduct Audits Regularly on a Set Schedule
Holding safety audits on a predictable schedule ensures that safety remains a continuous priority. Regular audits help identify and mitigate risks before they escalate into serious incidents.
This systematic approach keeps safety standards up to date and demonstrates your organization’s commitment to maintaining a safe working environment. It also helps you spot any new compliance gaps that may have emerged after regulations have been updated.
Use a Consistent Checklist and Document All Findings
Employ a standardized safety checklist for every audit to maintain consistency. Document every finding after every health and safety audit, including minor issues. These records are invaluable for tracking progress, understanding patterns, and planning future occupational safety initiatives.
Prioritize Hazards by Risk Level for Corrective Actions
After identifying potential hazards during an audit, it’s important to sort them based on the severity of the risk they pose. Tackling the most dangerous risks first enhances occupational health and safety. This approach is also a wise strategy for allocating costs and resources while improving safety systems.
Verify Completion of Action Items and Preventative Measures
Once corrective requirements are identified and prioritized, regularly check their progress. Ensure that each action item is completed effectively. This step helps prevent hazards from recurring and keeps employees aware of your organization’s health and safety measures.
Analyzing Audit Results to Prioritize Safety Investments
Identify the Highest Risk Areas and the Most Impactful Solutions
Analyzing the results of safety audits helps identify the areas that pose the highest risk to employees. Focusing on these areas and implementing the most effective solutions can significantly enhance workplace safety in a cost and resource-efficient manner. This focused approach allows for targeted investments in safety measures that yield the highest impact on employee well-being.
Align Spending With Your Overall Risk Management Strategy
Ensure that all safety investments align with your business’s broader risk management strategy. This alignment ensures that resources are used where they can have the most impact and keeps you on track toward your larger goals. Doing so will also help you create a unified approach to minimizing risks across your entire organization.
Make Data-Driven Decisions to Optimize Your Safety Budget and ROI
Use data from safety audits to make informed decisions about where to allocate your health and safety budget. This data-driven approach optimizes spending and maximizes the effectiveness of your health and safety programs. You can also easily customize your safety strategies to target high-risk areas and achieve the best outcomes for your investment.
Communicate Audit Insights to Leadership to Support Your Safety Culture
Sharing insights from safety audits with organizational leadership is an essential part of fostering a strong workplace safety culture. This communication ensures that leaders are aware of safety challenges and the measures needed to address them. As a result, your team is more likely to receive an adequate budget to address and maintain workplace safety standards.
Choose ServiceChannel to Help Streamline Your Next Safety Audit
A good way to ensure that your safety audit checklist is put to use is to incorporate it into your overall preventive maintenance strategy. It can be as simple as adding safety practices to your routine maintenance checklist, or you may add safety inspections to your maintenance tracking system.
Either way, you can use ServiceChannel’s software to help improve your facility’s overall safety. Our tool can promote your safety program, communicate with external safety officers, and track whether your staff is following all required workplace safety regulations.