Comparing Proactive Maintenance vs Reactive Maintenance: Moving into the Future
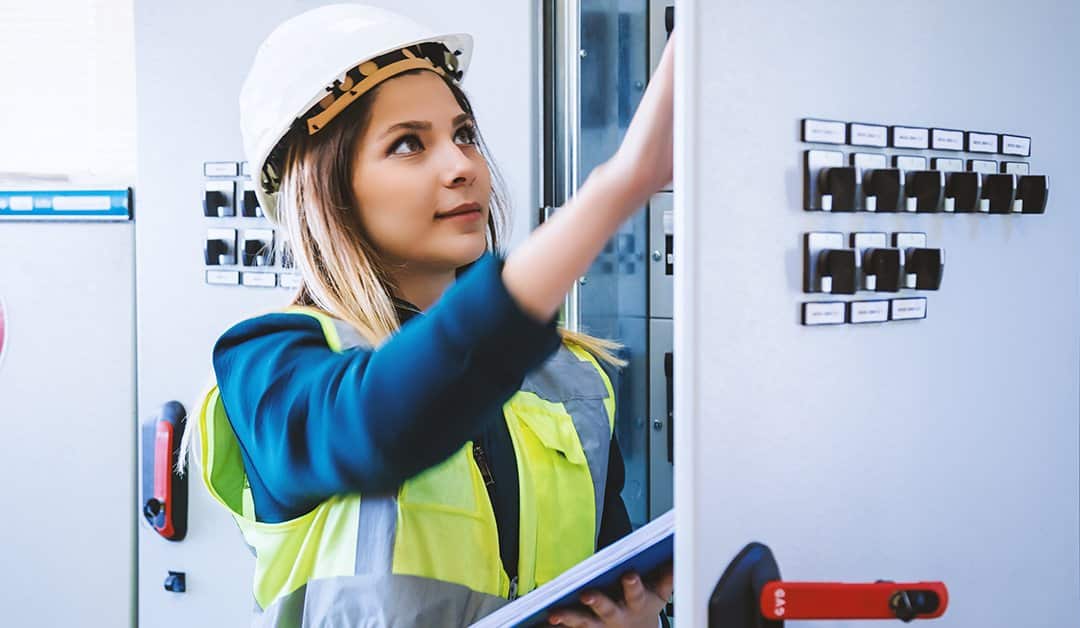
Reactive maintenance has typically been the standard for maintenance procedures in facilities management. A piece of equipment breaks or has a downtime, then a vendor is called to repair the asset and the cycle continues. This kind of maintenance doesn’t use data, so it is not possible to know when to anticipate these downtimes and is not sustainable for long-term operations. The future of facilities management is data-backed, proactive maintenance. So what’s the difference and how do we move from reactive to proactive?
What is Reactive Maintenance?
Reactive maintenance occurs when there is an equipment failure causing a lag in production. This means work on the equipment only takes place after a breakdown. The approach in reactive maintenance is crisis-based and creates a delay in maintenance and service calls. While it seems as if money is being saved by taking this approach, it is usually the most costly in the end.
Reactive maintenance creates downtime and an increase in costs because parts are purchased for “right now” instead of sourcing the parts at the lowest cost. It is also people-dependent and results in deficiencies when executing responsibilities. This is only ideal for equipment that is low priority, but using this method for operational equipment can disrupt the entire supply chain is not a good solution.
For example, these situations occur using a reactive maintenance approach:
- HVAC in a shopping mall breaks down. HVAC systems usually give some indication of wear and tear or when they are about to break down. A technician will have to come to figure out what happened, offer solutions, repair, and in some cases make recommendations for a new unit, which can be costly. This can also cause the mall to be at an uncomfortable temperature resulting in loss of business until the unit is repaired.
- At a fitness facility, the elliptical machine or treadmill may stop working or start malfunctioning. If the problem cannot be rectified by simple recommendations, the equipment will be out of service until a technician can come to repair the equipment resulting in a poor customer experience.
Reactive maintenance has more downsides than upsides, including unexpected downtime of equipment and people, the budget is always fluctuating, equipment that is not maintained has a shorter life span, the energy expended on problematic machinery is heightened, and employees usually work overtime, increasing costs. To get away from these types of situations, utilizing a proactive maintenance approach is encouraged.
What is Proactive Maintenance?
Proactive maintenance is planned maintenance that enhances the lifespan of assets, equipment, and your company infrastructure. This type of maintenance includes cleaning, repairs, replacements, adjustments, and lubrication. In essence, proactive maintenance addresses the small problems before they become larger ones. By taking this approach, overall costs are lessened when things are organized.
When a reactive maintenance approach is used, breakdowns occur at any time, employees are idle waiting for machinery to be repaired, and critical equipment is not well taken care of. In contrast, these are examples of what happens using a proactive maintenance approach:
- Having a plan to routinely check your HVAC system: Routine inspections will help identify issues before they become a problem. The last thing you want is for the unit to break down in the middle of winter or summer, which could have an impact on the bottom line.
- Never lose an essential asset to downtime: What equipment do you use on an ongoing basis? Anything used on a recurring basis that contributes to the ordinary operation of the business is considered essential and should not be able to be compromised. They should be on a fixed schedule for checking and preventative maintenance.
Proactive maintenance is known to save more money annually because issues that may have occurred from aging equipment are not a factor. Additionally, safety hazards are lessened, equipment lasts longer, productivity is increased, less energy is used, and insurance premiums are lowered.
How Shifting Your Approach Will Impact Your Facility
Most facilities programs spend about 60% of their time on reactive maintenance vs 40% on proactive. Proactive maintenance should become the dominant practice in your program; top performing facilities strive for a ratio closer to 75% proactive vs 25% reactive maintenance. Routine maintenance schedules that further asset lifecycles and utilize resources effectively will have a transformative impact on your team’s productivity and your company’s operational excellence.
A facilities management team that lives by reactive maintenance is constantly needing to put out fires, always responding to issues, rather than foreseeing and preventing them. Your team likely feels like they can’t get ahead.. Reactive maintenance tends to feature battles against rising costs, having inaccurate repair and maintenance records due to multiple people handling breakdowns, and an overall feeling of constant disruption.
With proactive maintenance, you can make data-backed decisions and find issues that could cause a disruption in production to address it before something occurs. Your team can look ahead, feel in control, and make the best repair or replacement decision for your facility based on costs, seasonality, and availability. You have more choices in how much you pay for parts, who will do the maintenance work, and when it is done. This allows your entire facilities program to operate at a much higher level, with more value for the money you spend.
Moving Into the Future
Huge brands like Sam’s Club have embraced proactive maintenance, moving away from a reactive maintenance model. This is a sign of a mature facilities management program, where a head of facilities recognizes the advantages of investing in software that tracks and analyzes data that can give insight on quality control and equipment life cycles. They recognize the benefits to their organization from a sustainability perspective as well, as proactive strategies extending your asset lifespans and enables compliance. .
How is your facility operating today? Do you have a healthy enough balance, where proactive maintenance outweighs your reactive maintenance? ServiceChannel has helped many of the biggest brands across retail, restaurant, grocery, convenience stores, among other industries, step into the future of facilities and gain a competitive edge. Check out our leading cloud platform, or contact our team for more information on how we will help you get there today!